Параметры оптимизации систем технического обслуживания и текущего ремонта автомобилей
Параметры загрузки и производительности характеризуют работоспособность системы и ее эффективность с точки зрения использования производственных мощностей. Однако более полное использование производственных мощностей еще не является единственной целью функционирования системы ТО и ТР автомобилей. Система должна обеспечить требуемый уровень работоспособности подвижного состава при минимальных затратах или максимальных прибылях. Следовательно, для оценки работы системы ТО и ТР автомобилей наиболее важную роль играют экономические параметры.
Одним из параметров, характеризующих экономическую эффективность работы системы, являются затраты (С) на ее функционирование. Затраты системы и ее производительность взаимосвязаны. Сокращение затрат на функционирование системы ТО и ТР означает уменьшение ее мощности, а следовательно, пропускной способности отдельных подсистем и, как следствие, увеличение простоя подвижного состава в системе, что, как правило, будет связано с сокращением объема перевозок и потерей доходов. В то же время стремление к обеспечению высокого коэффициента готовности подвижного состава может привести к чрезмерному увеличению затрат на систему ТО и ТР.
Для отдельной подсистемы является характерным то, что с увеличением ее мощности сокращается простой автомобилей в данной подсистеме, т.е. увеличение затрат подсистемы сопровож-
4 Macven
лается сокращением потерь от простоя подвижного состава. Поэтому в качестве показателя эффективности для отдельной (/-и) подсистемы представляется целесообразным использовать величину суммарных потерь от простоя подвижного состава по причине недостаточной пропускной способности и затрат на функционирование данной подсистемы. Условие оптимизации j-й подсистемы по данному критерию может быть записано в следующем виде:
Рис. 6.4. График изменения удельных прибылей предприятия в зависимости от производственных мощностей системы ТО и ТР автомобилей:
— удельные прибыли предприятия; — численность технологических рабочих; — оптимальная численность рабочих; — затраты на содержание одного рабочего в день
где — средняя длина очереди i-x требований (число автомобилей) в j-й подсистеме; — средняя величина потерь от простоя одного автомобиля задень; — средняя величина затрат yа функционирование j-йподсистемы, приходящаяся на одного рабочего и день; —- средняя численность рабочих на i-м воздействии в j-й подсистеме.
График изменения суммарных затрат представлен на рис. 6.3. Минимум затрат позволяет произвести выбор оптимальных мощностей подсистем. Однако сумма оптимальных затрат в отдельных подсистемах не обеспечивает оптимальную работу всей системы в целом, 1ак как при этом не учитывается взаимодействие между различными подсистемами.
Для оптимизации работы интегрированной системы ТО и ТР автомобилей может быть использован комплексный экономический показатель, В качестве такого критерия оптимизации работы всей системы представляется целесообразным использовать условие обеспечения максимальных удельных прибылей ПУД от работы автомобилей, приходящихся на единицу затрат на функционирование системы:
Рис. 6.3. График изменения суммарных затрат в j-й подсистеме ТО и ТР:
— штатная численность рабочих: — численность технологических рабочих; - число автомобилей в /-и подсистеме ТО и ТР: — потери от простоя одного автомобиля и день; затраты на содержание одного рабочего в день: суммарные потери от простоя подвижного состава в j-й подсистеме
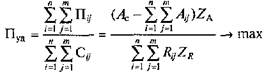
где — списочное число автомобилей.
Графически оптимизация интегрированной системы ТО и ТР автомобилей по комплексному экономическому критерию представлена на рис. 6.4.
Как следует из графика, увеличение производственных мощностей системы ведет к увеличению прибылей АТП вследствие работы на линии освободившихся из очереди в системе ТО и ТР автомобилей, но в то же время происходит рост затрат на функционирование системы. В первый период рост прибылей преобладает над ростом затрат, при дальнейшем развитии, когда увеличение производственных мощностей вызывает лишь незначительное сокращение очереди простаивающих в системе автомобилей, затраты на систему начинают расти быстрее, чем прибыли. Таким образом, отношение прибылей предприятия к затратам системы при различных ее мощностях описывается экстремальной кривой
, максимум которой соответствует оптимальной мощности системы.
Выбор оптимальных мощностей интегрированной системы по комплексному экономическому критерию является сложным и трудоемким процессом, вследствие того, что возникает необходимость в последовательном переборе численности производственных рабочих и постои для различных подсистем и различного их сочетания по подсистемам. Для оптимизации системы ТО и ТР в условиях, приближенных к реальным, используется метол математического моделирования.
6.3. Математическая модель системы технического обслуживания и текущего ремонта автомобилей
Построение математической модели является составной частью исследования сложных систем, таких как система ТО и ТР автомобилей. Математические модели позволяют, не проводя длительных и дорогостоящих натурных исследований, получить близкие к реальным условиям параметры процессов, происходящих в системе, установить количественные связи между условиями функционирования, принимаемыми решениями и показателями эффективности работы системы.
Рис. 6.5. Алгоритм розыгрыша среднесуточного пробега автомобилей:
— время в наряде; — эксплуатационная скорость автомобиля; — средне-квадратическое отклонение; — число выполненных расчетов: — псевдо-
случайные числа; — число реализаций случайных чисел; — среднесуточный
пробег автомобиля
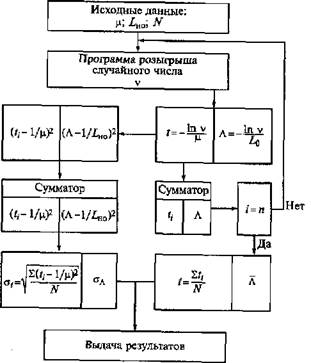
Рис. 6.6. Алгоритм розыгрыша времени выполнения воздействий и параметра потока отказов: — интенсивность выполнения воздействий; — нормативный пробег авто-
мобиля до ТО; — число выполненных расчетов; — продолжительность выполнения воздействия; — параметр потока отказов; — среднеквадратическое отклонение времени обслуживания; — среднеквадратическое отклонение параметра потокаоткатав
Для исследования системы, на работу которой влияет большое число факторов, в том числе имеющих случайный характер, используются методы аналитического и статистического моделирования. Показатели, используемые в модели и имеюшие случайный характер, определяются с помощью специальных компьютерных программ или генераторов случайных чисел. Алгоритмы розыгрыша случайных величин среднесуточного пробега автомобилей, а также трудоемкостей выполнения воздействий и параметра потока отказов приведены на рис. 6.5 и 6.6.
Высокая достоверность разыгрываемых случайных величин достигается в результате большого числа розыгрышей. Минимально возможное число розыгрышей, необходимых для получения достоверных показателей, определяется расчетным путем.
Математическое моделирование выполняется по специально разработанным компьютерным программам с использованием функциональных зависимостей для определения показателей, не имеющих случайный характер, и розыгрышей случайно изменяющихся показателей. Оптимальные размеры производственных мощностей определяются с помощью приведенных в этой главе параметров оптимизации. Математическая модель интегрированной системы ТО и ТР автомобилей позволяет с помощью математических зависимостей выявить взаимосвязи между различными подсистемами и определить количественные значения параметров эффективности, что дает возможность вывести систему в оптимальный режим работы.
Эффективность работы системы ТО и ТР в целом зависит от того, насколько каждая из участвующих в процессе восстановления работоспособности подвижного состава подсистем справляется со своими задачами. Так, недостаточная пропускная способность одной из подсистем будет вызывать увеличение простоя подвижного состава в неисправном состоянии, снижая тем самым эффективность работы всей системы. И наоборот, чрезмерное увеличение производительности отдельных подсистем связано с неоправданным увеличением затрат на функционирование системы.
Таким образом, наибольшая эффективность работы системы ТО и ТР, представляющей собой интеграцию различных взаимосвязанных подсистем, может быть обеспечена только при оптимальном сочетании пропускных способностей этих подсистем.
Составление математических моделей отдельных подсистем будет заключаться в описании с помощью математических выражений системы соотношений, связывающих характеристики Состояний производственного процесса с его параметрами, исходной информацией и условиями функционирования системы.
Приняв основное производство за блокирующую подсистему требуется согласовать с ней работу других подсистем ТО и ТР Такое согласование в целях упрощения задачи может производиться путем попарной оптимизации каждой подсистемы совместно с работой основного производства.
Изменение производительности основного производства приводит к необходимости изменения производительности подсистем вспомогательного и обслуживающего производства. В свою очередь, по условию эффективного функционирования системы возникает необходимость в изменении пропускной способности основного производства в соответствии с входящим потоком требований.
Эффективное совместное функционирование различных подсистем с подсистемой основного производства возможно при условий:

Производительность работы системы ТО и ТР будет зависеть от входящего потока требований , пропускной способности диагностирования , основного , вспомогательного и
обслуживающего производства. Отсюда суммарная произво-
дительность системы

Рациональное сочетание пропускных способностей различных подсистем может быть выявлено по степени влияния этих подсистем на эффективность работы всей системы (значимости работы подсистем). Повышение эффективности работы системы ТО и ТР автомобилей можно достичь обеспечением более высокой пропускной способности менее значимых подсистем. Это позволит за счет незначительного повышения затрат увеличить вероятность безотказной работы более значимых подсистем, т. е. чем ниже значимость работы и затраты подсистемы, тем выше должна быть ее пропускная способность по отношению к более значимым (блокирующим) подсистемам.
Общее условие функционирования интегрированной системы ТО и ТР можно записать в следующем виде:

Увеличение пропускных способностей подсистем обеспечивается наличием соответствующего резерва производственных мощностей . Однако чрезмерное увеличение резерва связано с большими затратами на функционирование системы. Следовательно, разницу между интенсивностью входящего потока требовании и пропускной способностью необходимо выбирать оптимальной, чтобы затраты на функционирование системы С были минимальными, или чтобы прибыль системы П была максимальной.
Изложенное является основанием для составления математической модели интегрированной системы ТО и ТР автомобилей, которая может быть представлена в следующем виде:
!
5

Многочисленные расчеты, выполненные в МАДИ с использованием метода математического моделирования, позволили разработать номограммы определения технологически необходимой численности рабочих для выполнения расчетного объема технических воздействий (рис. 6.7) и дополнительной численности рабочих, необходимых для обеспечения оптимальной пропускной способности системы ТО и ТР (рис. 6.8).
Номограммы разработаны с использованием большого объема статистических материалов и позволяют с достаточной точностью определять технологически необходимую численность рабочих и
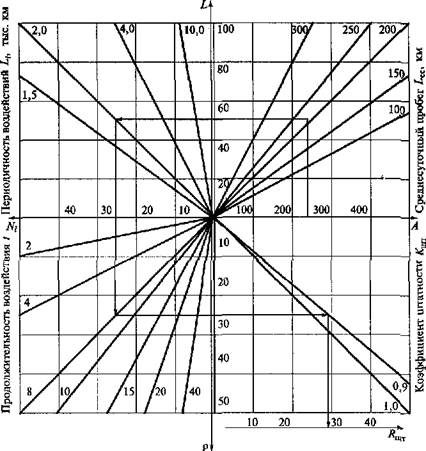
Рис. 6.7. Номограмма определения технологически необходимой численности рабочих:
А - число автомобилей на предприятии; - штатная численность рабочих
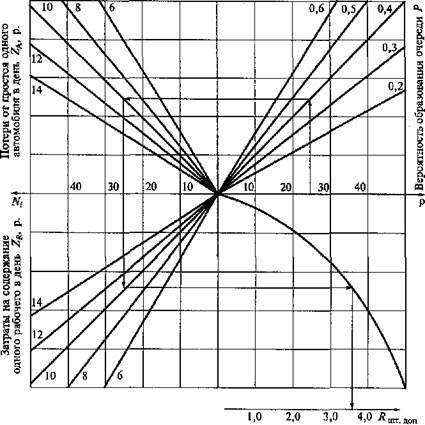
Рис. 6.8. Номограмма определения дополнительной численности рабочих, необходимых для обеспечения оптимальной пропускной способности системы:
— входящий поток требований; — дополнительная численность рабо-
чих; — приведенная плотность потока требований
с некоторой погрешностью оптимизировать производственные мощности предприятия.
Проведенные статистические исследования и расчеты показали, что для ЛТП среднего размера распределение трудоемкостей
по подсистемам составляет: основное производство — 39%; вспомогательное производство — 29%; обслуживающее производство — 27 %; диагностирование — 5 %.
Оптимизация производственных мощностей с рациональным их размещением в подсистемах ТО и ТР позволит обеспечить максимальную эффективность работы АТП, обеспечив сокращение
потерь от простоя подвижного состава в технически неисправном состоянии и увеличив прибыли предприятия от работы автомобилей на линии.
Оптимизацию производственных мощностей осуществляют в определенной последовательности. Используя результаты технологического расчета, показатели параметра потока отказов, интенсивности отказов и других параметров, имеющих случайный характер, а также учитывая экономические показатели работы предприятия (например, прибыль от работы автомобилей на линии в день, удельные затраты на содержание одного ремонтного рабочего и пр.), определяют дополнительную численность ремонтных рабочих и число производственных постов подсистемы основного производства.
По оптимальным мощностям основного производства с учетом распределения объемов работ по подсистемам корректируются производственные мощности вспомогательного и обслуживающего производств и подсистемы диагностирования. Сумма мощностей всех подсистем будет составлять оптимальную производственную мощность предприятия. Выполнение расчетов на компьютерах по специально разработанным программам позволяет получать наилучшие результаты по оптимизации интегрированных систем. По полученным оптимальным мощностям предприятий производят корректировку численности производственного персонала, числа постов и линий ТО и ТР, площадей производственных участков и цехов.
Контрольные вопросы
1. Опишите АТП и систему ТО и ТР автомобилей как систему массового обслуживания.
2. Из каких служб состоят и как взаимодействуют подсистемы Т0 и ТР автомобилей?
3. Для чего осуществляется и в чем заключается оптимизация производственных мощностей системы ТО и ТР автомобилей в АТП?
4. Какова цель и принципы разработки математической модели системы ТО и ТР?
5. Какие критерии используются для оптимизации производственных мощностей? Дайте графические изображения оптимизации системы ТО и ТР автомобилей в АТП с использованием различных критериев.
6. Для чего выполняется математическое моделирование системы ТО и ТР автомобилей? Какие показатели используются при составлении математической модели системы?
7. Как с помощью математической модели осуществляется оптимизация системы ТО и ТР? В чем конечная цель оптимизации системы ТО и ТР автомобилей в АТП?
ГЛАВА 7
ОБЩИЕ ТРЕБОВАНИЯ К РАЗРАБОТКЕ ПРОЕКТНЫХ
РЕШЕНИЙ
Планировка предприятия
Планировка предприятия осуществляется на основании выполненных технологических расчетов с учетом оптимизации производственных мощностей. Исходя из потребности в производственных площадях, специфики предприятия, принятой технологии производства и прочего выбирается земельный участок под строительство предприятия. Определяются ориентировочные объемы и этапы строительства, а также возможные для использования строительные конструкции и материалы. Прорабатываются компоновочные решения отдельно стоящих зданий, составляется генеральный план предприятия, а затем выполняются планировки цехов, участков и зон.
В процессе планировки решаются следующие вопросы: обеспечение эффективного использования и застройки земельного участка; рациональное взаимное расположение зданий, сооружений, помещений, цехов, участков и постов с учетом принятой технологии выполнения работ; обеспечение научной организации труда на рабочих местах, технологических связей и движения на территории и в зданиях предприятия; размеры, этажность и конструкции зданий и сооружений; соблюдение технологических и строительных норм и требований; минимизация затрат на проектные, строительно-монтажные и эксплуатационные работы и т.д.
Особое значение для обеспечения эффективности строительства имеет выбор земельного участка под строительство предприятия. Место расположения земельного участка определяется исходя из прогнозов развития пассажирских и грузовых потоков в строгой увязке с генеральным планом развития города, населенного пункта, района.
Грузовые авто предприятия желательно размещать вблизи гру-зообразующих или грузополучающих объектов, грузовые станции — в узловых пунктах автомобильных дорог, вблизи грузооб-разующих объектов и грузовых терминалов других видов транспорта, городские автобусные предприятия — вблизи от наиболее напряженных городских маршрутов, автовокзалы — на террито-
риях, прилегающих к автомобильным дорогам и имеющих хорошее транспортное сообщение со спальными районами города, а также железнодорожными, водными и авиационными вокзалами.
При выборе земельного участка необходимо учитывать, что резкий рельеф местности (перепады высот на участке) требует большого объема земляных работ, а близкое расположение грунтовых вод (выше глубины размещения технологических устройств и осмотровых канав) могут создать трудности для использования принятой технологии производства или привести к подорожанию строительства из-за выполнения дополнительных водоизоляцион-ных работ. Особое внимание при выборе участка следует уделять наличию на прилегающих территориях инженерных сетей (тепловые сети, электроэнергия, газ, вода, канализация) и возможности подключения к ним.
Выделение земельного участка оформляется решением администрации города или района, затем в соответствующих муниципальных службах уточняются точки подключения к инженерным сетям и определяются требования, предъявляемые к архитектурно-планировочному решению проекта.
7.2. Объемно-планировочное решение
Объемно-планировочное решение позволяет определить общий вид и объемы будущего строительства, типы и размеры строительных конструкций и материалов. Объемно-планировочное решение должно приниматься с учетом назначения и особенностей эксплуатации предприятия; природно-климатических условий и рельефа местности; обеспечения требований унификации строительных конструкций и основных параметров проектируемых зданий и сооружений; особенностей организации технологического процесса; возможности реконструкции предприятия при изменении расчетных параметров.
Здания из железобетонных конструкций наиболее часто используются при проектировании и строительстве. Для снижения стоимости проектных работ, изготовления строительных конструкций и выполнения строительно-монтажных работ но возведению зданий и сооружений из железобетонных конструкций осуществляется унификация объемно-планировочных и конструктивных решений. Унификация достигается благодаря производству типовых строительных конструкций и разработке типовых проектов предприятий.
Для изготовления строительных конструкций (колонн, плит перекрытия, стеновых панелей и т.д.) индивидуальных размеров и конструкций необходимо выполнить расчеты конструкций, изготовить соответствующие формы, разработать технологию, под-
готовить производство, специалистов и рабочих. Это связано с большими производственными затратами, что приведет к значительному удорожанию проекта. Таких затрат можно избежать, если на заводах железобетонных изделий производить несколько типоразмеров конструкций, которые будут использоваться при проектировании.
Разработка проекта представляет собой длительный и трудоемкий процесс. Использование типового проекта с привязкой к местности или с небольшими изменениями в типовом проекте позволяет значительно сократить сроки проектирования и строительства предприятия. Типовые проекты разрабатываются по заказам министерств и ведомств в крупных отраслевых или специализированных проектных институтах.
На автомобильном транспорте основным разработчиком типовых проектов является Государственный институт проектирования предприятий автомобильного транспорта (Гппроавтотранс).
При проектировании предприятий, изготовлении строительных конструкций и строительстве используется унифицированный на территории всей страны типаж конструкций, сетка колонн и размеры пролетов. Унифицированные типоразмеры строительных конструкций и параметры зданий определены в нормативных документах Строительные нормы и правила (СНиГТ). При разработке индивидуальных проектов строительства или реконструкции также используются элементы типовых проектов и типовые строительные конструкции.
В соответствии с требованиями СНиПа, шаг колонн в одноэтажных прои яюдственных зданиях (расстояния между разбивоч-пыми осями здания в продольном направлении) принимается равным 6 или 12 м. Размеры пролетов (расстояния между разби-вочпыми осями здания в поперечном направлении) могут быть 6: 12; 18; 24; 30 м (кратно 6 м). Общий вид железобетонного каркаса предприятия в разрезе представлен на рис. 7.1.
Высота одноэтажного производственного здания определяется исходя из типа здания, особенностей технологического процесса, пролет здания, наличия и типа технологического и подъемио-транспортного оборудования. Высота до низа несущих конструкций производственных зданий зависит от выбираемого типа колони, они могут быть: 3,6; 4,2; 4,8; 6; 7,2; 8,4 м. Высота многоэтажных производственных зданий принимается равной 3,6 или 4,8 м, для предприятий автомобильного транспорта, как правило - 3.6 м.
Размеры пролетов многоэтажных производственных зданий принимаются кратными 3 м (3; 6; 9; 12; 15; 18 м), а шаг колонн — 6 м. Этажность здания определяется с учетом технической и экономической целесообразности, технологии производства, архитектурных требований к строящемуся объекту, потребности в
I08
Рис. 7.1. Железобетонный каркас производственного здания: 1- фундамент; 2 - колонна; 3 - подстропильная ферма; 4 - стропильная ферма; 5 - светоаэрационный фонарь; 6 - плита покрылия; 7 - утеплитель; 8 - выравнивающий слой; 9- кровельный ковер; 10- воронка внутреннего водостока; 11 - стеновая панель; 12 - ленточное остекление; 13 - крановый рельс; 14 - подкрановая палка; 15 - связи; 16 - фундаментная балка, 17 - отмостка
производственных площадях и размеров земельного участка. Нагрузка на пол в многоэтажном производственном здании не должна превышать 2,5 т/м2. Среди предприятий автомобильного транспорта в многоэтажном исполнении наиболее часто встречаются гаражи и стоянки (в том числе таксомоторных или иных авто
предприятий).
Знания АТП в типовых проектах обычно бывают прямоуголь-ной конфигурации в плане с параллельно расположенными про-летами. Допускается использование пролетов различных размеров В пролетах с меньшими размерами и высотой рекомендуется раз-мещать производственные цеха и участки, а в пролетах с больши-
ми размерами по ширине и высоте — посты и линии обслуживания и ремонта автомобилей.
В каркасных железобетонных производственных зданиях предусматривается устройство навесных или самопесущих стеновых панелей. Навесные панели выполняют функции ограждений и крепятся к колоннам с внешней стороны. Самонесущие стены применяются при необходимости использования панелей большей толщины и веса, способных обеспечить теплоту и шумоизоляцию. Такие степы возводятся на собственных фундаментах. Допускается также применение кирпичных самонесущих стен и стен из других (местных) материалов при условии их соответствия требованиям, предъявляемым к строящемуся зданию.
Покрытие железобетонных зданий занимает особое место в процессе проектирования, строительства и эксплуатации предприятия. Затраты па покрытие составляют около 50 % от всех затрат, приходящихся на строительство и эксплуатацию здания.
В зависимости от конфигурации и типа зданий покрытия подразделяются на односкатные, двухскатные, многоскатные, криволинейные и плоские. Односкатные покрытия применяются в однопролетных небольших зданиях. В типовых проектах автотранспортных предприятий обычно используются двухскатные или многоскатные покрытия.
Нa покрытиях многопролетных зданий большой ширины и длины должны быть предусмотрены световые или светоаэрационные фонари для обеспечения помещения естественным светом и проветривания. Для предприятий, строящихся в регионах с теплым климатом, рекомендуется предусматривать шедовые фонари с их ориентацией на север. При необходимости на покрытии могут быть установлены также крышные вентиляторы.
Основными элементами покрытия являются несущие балки иди фермы. На них устанавливаются железобетонные плиты покрытия, зачем укладываются слой утеплителя, выравнивающий слой и кровля.
Унифицированные здания из легких металлических конструкций (модули) получили широкое применение в проектировании и строительстве предприятий автомобильного транспорта начиная с 80-х гг. XX в. Они представляют собой сборные металлические конструкции, которые изготавливают на заводах металлоконструкций и поставляют в комплекте. В зависимости от заказа модули могут поставляться с легкими утепленными стеновыми панелями, иконными переплетами, воротами и элементами покрытия и т.д.
Российские заводы выпускают несколько типов модульных конструкций, отличающихся между собой размерами, используемым металлопрокатом, назначением и эксплуатационными характеристиками (рис. 7.2 — 7.4).
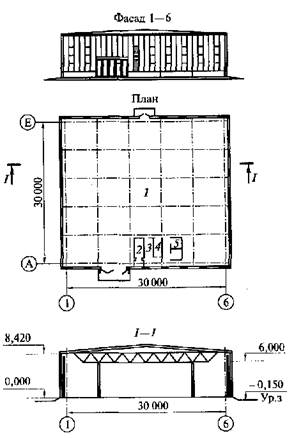
Рис. 7.2. Унифицированное здание (модуль) из легких металлических пространственных конструкций типа «Кисловодск»: I — производственное помещение; 2 — вентиляционно-проточный агрегат ВПА-40: 3 — тепловой узел; 4 — электротехническое помещение; 5— санузел
Использование металлических модульных конструкций позво-ляет значительно сократить затраты и сроки строительства по срав-нению с использованием железобетонных конструкций. При воз-ведении модульных конструкций заливают бетонные фундаменты под стойки опор и производят сборку конструкций. За считанные дни здание из модульных конструкций может быть введено в экс-плуатацию.
Незаменимы модульные конструкции при чрезвычайных ситу-ациях, когда требуется в кратчайшие сроки построить и ввести в эксплуатацию здания производственного или иного назначения.
Наибольшее распространение получили модульные конструк-ции при строительстве производственных зданий в регионах с
мягким и умеренным климатом, т.е. там, где не предъявляются особые требования к теплоизоляции зданий. Наиболее удачными оказались проекты, разработанные для южных регионов России, когда в здании из спаренных или учетверенных модульных конструкций размещены посты и линии обслуживания и ремонта автомобилей, а цеха и участки — в пристройке к модулям.
Ворота здания должны быть выполнены с учетом габаритных размеров наиболее крупных транспортных средств с грузом, проезжающих через ворота. Размеры ворот должны превышать габаритные размеры этих транспортных средств по высоте па 0,2 м и по ширине на 0,6 м. В типовых проектах могут быть предусмотрены распашные, раздвижные или подъемные ворота.
Покрытия полов в производственных цехах, участках и зонах выполняют с учетом видов и интенсивности механических и теп-
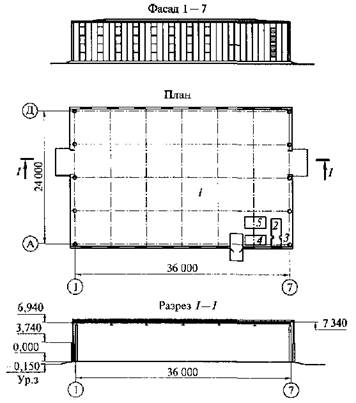
Рис. 7.3. Унифицированное здание (модуль) из легких металлических рамных конструкций типа «Канск»:
1 — производственное помещение: 2 — воздухозаборная камера: 3 - тепловой узел; 4 — санузел: 5 — электрощитовая
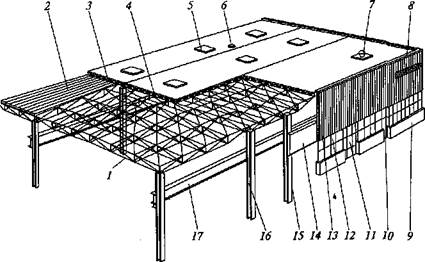
Рис. 7.4. Унифицированное здание (модуль) из легких металлических конструкций типа «ЦНИИСК». Объемно-планировочное решение:
1 — структурный блок; 2 — профилированный настил; 3 — утеплитель; 4 — водоизоляционный ковер; 5 — зенитный фонарь; 6— водосточная воронка; 7 — крышный вентилятор; 8 — жалюзийная решетка; 9 — цокольная панель; 10 — дверь; 11 — ворота; 12 — окопная панель; 13 — стеновая панель; 14 — ригель стеновой; 15 — колонна фахверка; 16 — колонна; 17 — подкрановая балка
ловых воздействий, воздействий агрессивных жидкостей и удобства очистки от загрязнений. В зонах по обслуживанию и ремонту автомобилей, механическом, моторном и агрегатном цехах рекомендуются следующие типы покрытия полов: бетонный Шлифованный; бетонный мозаичный; мозаичные плиты. Для покрытия полов в кузнечно-рессорном цехе используется клинкерный кирпич или брусчатка, в аккумуляторном — керамическая кислотоупорная плитка, в деревообрабатывающем и обойном цехах — асфальтобетон, в электротехническом, топливном и медницком цехах — керамические плитки или мозаичные плиты.
7.3. Генеральный план предприятия
Генеральный план предприятия является одним из основных частей проекта и представляет собой соединенное в единое целое технологическое и архитектурное решения проекта. Генеральным планом определяется порядок использования земельного участка предприятия, рациональное размещение зданий и сооружений, эффективная организация работы и взаимодействия основного.
вспомогательного и обслуживающего производства, размещение зоны хранения автомобилей, пути прокладки инженерных сетей и т.д.
При разработке генерального плана необходимо учитывать принятую схему производственного процесса и технологию выполнения работ; особенности природно-климатических условий района размещения предприятия; преобладающее направление ветров; стороны света; рельеф местности; площади производственных участков, цехов, зон обслуживания, ремонта и хранения автомобилей в соответствии с технологическими и оптимизационными расчетами.
Расчетные площади производственных и складских помещений необходимо корректировать в соответствии со строительными нормами и правилами и требованиями унификации строительных конструкций. Инженерные сети должны быть предусмотрены с учетом условий, определенных соответствующими муниципальными службами при согласовании проекта, технологии производства и экономической целесообразности.
Ворота для въезда и выезда из предприятия должны быть расположены с отступлением от красной линии застройки, отделяющей территорию предприятия от городской улицы или проезда не менее чем на длину наиболее длинного транспортного средства, проезжающего через эти ворота. Причем ворота въезда должны предшествовать по ходу уличного движения воротам выезда, чтобы исключить пересечение путей движения въезжающих и выезжающих автомобилей. Для АТП с подвижным составом более 100 автомобилей должны быть предусмотрены также запасные ворота шириной не менее 3,5 м.
Минимальное расстояние от проезда до наружных стен здания или ограждения при отсутствии въезда и длине стен (ограждения) не более 20 м составляет 1,5 м, а при длине более 20 м — 3 м. На территории предприятия со стороны въездных ворот и проходной рекомендуется устройство площадки для стоянки (хранения) легковых автомобилей работников и посетителей из расчета 25 м2 (удельная площадь на один легковой автомобиль) на 10 работающих.
Движение автомобилей внутри предприятия желательно организовать по кольцевому одностороннему маршруту, избегая пересечения путей движения. Ширина проезжей части на территории предприятия вне производственных зданий должна быть не менее 3 м при одностороннем движении и не менее 6 м при двухстороннем движении.
Степень застройки участка автотранспортного предприятия одноэтажными производственными зданиями при закрытом хранении автомобилей обычно составляет 30...50%, а при открытом хранении — 15...20%. Застройка участка может быть моноблоч-
Is
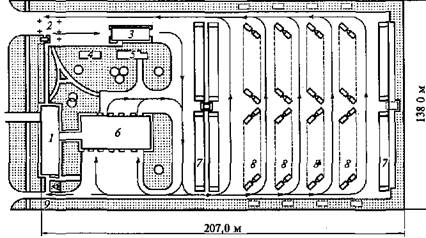
Рис. 7.5. Схема генплана АТП на 200 грузовых автомобилей при моноблочном строительстве с отдельно стоящей линией мойки:
Не нашли, что искали? Воспользуйтесь поиском по сайту:
©2015 - 2025 stydopedia.ru Все материалы защищены законодательством РФ.
|