Синтез кремнемедных контактных масс
Собственно кремний в отсутствие катализатора в реакции с органохлоридом неактивен. Известно четыре основных метода получения кремнемедных контакт-ных масс: сплавление компонентов, смешение их в виде порошков, восстановле-ние меди на кремнии, таблетирование и спекание с последующим восстановлени-ем при высоких температурах.
Сплавление компонентов. Это самый распространенный способ активации кремния для вовлечения его в последующие реакции.
Сплавные контактные массы из меди и кремния или меди и ферросилиция готовят в высокочастотных индукционных печах при 1673-1773 К с последующим охлаждением расплава. Основное преимущество сплавных контактных масс - об-разование при сплавлении интерметаллического соединения СuSi, придающего
им более высокую активность и снижающего продолжительность индукционного периода. Каталитическая активность кременемедных катализаторов определяется, в первую очередь, их химическим составом.
Структура сплава и способ приготовления также оказывают большое влия-ние на его активность. Это связано с тем, что реакция между алкилхлоридом и кремнием протекает на границе раздела фаз – кремний-медь. Уменьшение разме-ров кристаллов сплава и увеличение поверхности фазовых границ улучшают кон-такт твердых фаз и этим способствуют увеличению скорости образования алкил-хлорсиланов. Поскольку в сплавы при плавлении вводят промоторы, действие ко-торых проявляется лишь в строго определенных концентрациях, скорость охлаж-дения расплава имеет особенно важное значение для предотвращения ликвации – неравномерности распределения по объему компонентов сплава. Промотор вводят в сплавную контактную массу при плавлении, а также смешением порошков спла-ва и промотора.
Смешение порошков.Кремнемедные контактные массы, полученные смешением порошков меди и кремния, применяют в производстве алкил-хлорсиланов в реакторах различного типа с низкими скоростями газового потока. Этот способ также нашел промышленное применение, но не такое широкое, как сплавление компонентов.Возможно использование интерметаллического соедине-ния СuSi, промотированного цинком или алюминием. Однако этот контакт значи-
тельно менее активен, чем другие.
Восстановление меди на кремнии.Контактные массы с восстановленной медью приготавливают сухим смешением или осаждением на кремнии соедине-ний меди из растворов ее солей, например методом пропитки.Восстановление со-лей меди (преимущественно хлорида одновалентной меди) рекомендуется прово-дить при 473-573 К и атмосферном давлении в течение 2-8 ч в токе метилхлорида или водорода.Способы приготовления контактных масс путем осаждения и затем восстановления меди очень сложны и поэтому не имеют большого промышленно-го значения.
Таблетирование и спекание порошков. Таблетированные контактные массы приготавливают путем обработки кремния или ферросилиция водным рас-твором соли меди и едкого натра. Массу прессуют в полоски, высушивают при 373 К, режут на таблетки и при 523 К восстанавливают в токе водорода в течение 1-3 ч.Таблетированные контактные массы имеют более высокую избирательную активность в реакции образования диметилдихлорсилана по сравнению со сплав-ными и восстановленными на кремнии.
Таблетированные контактные массы не технологичны в изготовлении и хра-нении и, несмотря на их высокую активность, не имеют промышленного значения.
Синтез метилхлорсиланов
Метилхлорсиланы – соединения общей формулы (СН)SiClH, где m и n
3mn4-m-n= 1÷3 и (m+n) < 4, – бесцветные легко подвижные жидкости с раздражающим за-пахом; хорошо растворяются в органических растворителях.
Метилхлорсиланы получают взаимодействием метилхлорида с контактной массой (Si/Сu):
473-523 К
CHCl + Si (CH)SiCl + (CH)SiCl +CHSiHCl + (CH)SiHCl .
Процесс прямого синтеза метилхлорсиланов наиболее экономичен, если ди-метилдихлорсилан является главным продуктом реакции. Одним из основных ус-ловий экономичности процесса является обеспечение оптимального и максималь-но равномерного температурного режима в реакционном объеме, зависящего от целого ряда других условий синтеза. Активность всех видов контактных масс за-висит от степени их измельчения. Считается, что оптимальный размер частиц для кремнемедного сплава составляет 74-105 мкм. При дроблении создается активная поверхность кремния, которая при соприкосновении с воздухом пассивируется. Для сохранения реакционной активности измельчение кремния проводят в инерт-ной жидкости - парафине, силиконовом масле и др. -при 353-373 К.
Синтез метилхлорсилана можно проводить как при атмосферном, так и при повышенном давлении. С повышением давления конверсия метилхлорида и про-изводительность увеличиваются до максимума, а затем замедляются. Величина максимума зависит от температуры и объемной скорости. Как правило, оптималь-ным является давление 0,3-0,6 МПа.
Минимальная температура, при которой метилхлорид взаимодействует с кремнием в присутствии меди - 473 К. Эта температура благоприятствует пре-имущественному образованию диметилдихлорсилана: его выход составляет до 90%. Однако скорость реакции очень низкая. Повышение температуры способст-вует увеличению скорости реакции, но при этом выход диметилдихлорсилана снижается. С повышением температуры интенсифицируется пиролиз хлороргани-ческих соединений, особенно интенсивно протекает разложение метилхлорида:
3RCl + Si RSiCl + R—R.
На рис. 16.1 показана зависимость выхода метилхлорсиланов от температу-ры.
Рис. 16.1. Зависимость содержания метилхлор- силанов от температуры
(----- - производительность процесса)
1 - диметилдихлорсилан; 2 – метилтрихлор-
силан; 3 - метилдихлорсилан
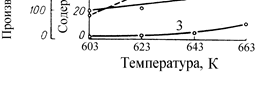
Максимально допустимая температура,
при которой процесс поддается регулирова-
нию, составляет 653-663 К.
Прямой синтез органохлорсиланов осу-
ществляют в реакторах с кипящим слоем", механическим перемешиванием, во
"
вращающихся и вибрирующих реакторах. В промышленности преимущественно
используют реакторы с "кипящим слоем". Скорость реакции и состав получаемого
конденсата определяются составом и способом приготовления контактных масс,
способом их активирования, временем контакта, температурой, давлением про-
цесса.
Добавление к метилхлориду водорода приводит к увеличению выхода ме-
тилхлоркремнийгидридов.
На рис. 16.2 представлена принципиальная технологическая схема синтеза
метилхлорсиланов в реакторе с "кипящим слоем" катализатора.
Рис. 16.2. Принципиальная технологическая схема синтеза метилхлорсиланов
1, 4 - емкости; 2 - испаритель; 3 - перегреватель; 5 - электронагревательные
элементы; 6 - дозатор; 7, 10-13 - бункеры; 8 - реактор; 9 - циклон; 14, 15 - фильтры;
16-18 - теплообменники; 19 - сборник.
Потоки: I - кремнемедный сплав; II - метилхлорид; III – пар; IV – вода; V –
рассол; VI – пыль; VII – фреон; VIII – отходящие газы; IX – смесь метилхлорсила-
нов
В реактор 8 загружают кремнемедный сплав и разогревают аппарат до 583 К. Из расходной емкости 1 через испаритель 2 и перегреватель 3 в реактор непре-рывно поступают пары метилхлорида, которые поднимаются в верхнюю часть ре-актора через слой порошкообразного кремнемедного катализатора со скоростью 0,1-0,3 м/с – из расчета создания "кипящего слоя", т.е. получения таких гидроди-намических условий, при которых каждая частица сплава может перемещаться в различных направлениях. Количество сплава в реакторе поддерживается постоян-ным путем непрерывной подачи его дозатором 6 из бункера 7. Реакция протекает при 573-633 К и 0,4-0,5 МПа.
Реакционные газы поступают на очистку в циклон 9, затем на фильтр 14, от-куда уловленную пыль периодически выгружают в бункер 13. Фильтр 15 мокрой очистки улавливает частицы пыли менее 10 мкм во избежание загрязнения по-верхностей конденсации в теплообменниках 16-18. В них из реакционных газов конденсируются продукты синтеза и непрореагировавший метилхлорид. Конден-сат метилхлорсилана с фильтра 15 и из конденсаторов поступает в сборник 19, от-куда насосом передается на ректификационные установки для выделения непро-реагировавшего метилхлорида и индивидуальных мономерных соединений.
В промышленности используются также и непрерывные процессы в реакто-рах, подобных описанному, а также в реакторах типа "вращающийся барабан".
Если процесс осуществляют в реакторе типа "вращающийся барабан", в смеси содержится 10—15% метилхлорида, но соотношение остальных продуктов сохраняется.
Синтез этилхлорсиланов
Этилхлорсиланы используются в промышленности в существенно меньшем объеме, чем метилхлорсиланы.
При увеличении молекулярной массы алкилхлорида вследствие снижения его термической стабильности в продуктах реакции прямого синтеза резко увели-чивается содержание водородсодержащих соединений типа RsiHCl, HSiClВысо-
23. кий выход водородсодержащих соединений связан с участием в реакции образо-вания алкилхлорсиланов продуктов дегидрирования алкилхлорида. Например, при синтезе этилхлорсилана образуется в 8-10 раз больше этилдихлорсилана, чем в сравнимых условиях метилдихлорсилана при синтезе метилхлорсилана. Это свя-зано с распадом этилхлорида в количествах, достигаемых половины от вводимого количества. Оптимальные результаты получаются при проведении процесса в
"кипящем слое". При этом достигается наибольший выход целевых продуктов – этил- и диэтилдихлорсиланов, а потери этилхлорида из-за распада минимальны.
При реакции кремния с этилхлоридом в присутствии меди образуется смесь, основными компонентами которой являются: этилдихлорсилан (15-20%), диэтил-дихлорсилан (25-40%), и этилтрихлорсилан (35-40%). Большее применение в про-мышленности находит этилдихлорсилан и меньшее – этилтрихлорсилан. Поэтому исследования направлены на поиск путей увеличения в составе продуктов синтеза этилдихлорсилана за счет подавления реакции образования этилтрихлорсилана.
Минимальная температура взаимодействия этилхлорида с кремнием в при-сутствии катализатора (медь) в зависимости от активности контактной массы со-ставляет 423-473 К. При увеличении температуры (рис. 16.3) в противополож-ность процессу синтеза метилхлорсилана, содержание этилдихлорсилана умень-шается, а диэтилдихлорсилана – возрастает.

Рис. 16.3. Зависимость состава продуктов синтеза
Не нашли, что искали? Воспользуйтесь поиском по сайту:
©2015 - 2025 stydopedia.ru Все материалы защищены законодательством РФ.
|