Станки для электрофизической и электрохимической
Обработки
Открытие в 1943 г. электроэрозионного явления положило начало использованию физических явлений для обработки материалов плохо поддающихся традиционной обработке резанием. На технологическом оборудовании, использующем физические явления, выполняют сквозные отверстия с цилиндрическими стенками и произвольным контуром, узкие прямолинейные и криволинейные щели в деталях типа матриц, сложных штампов, пресс-форм, фасонного режущего инструмента, шаблонов, фильер и других деталей, имеющих, в том числе, малые размеры отверстий (до 0,05 мм).
Физическое явление при обработке материалов выполняет функцию режущего инструмента. Понятие о характеристическом образе (вспомогательном элементе) инструмента, сформулированное в разделе 2, полностью относится также и к используемым при обработке материалов физическим явлениям.
При обработке труднообрабатываемых материалов используются также комбинированные способы обработки, например, обработка резанием с наложением электростатического или электромагнитного поля и т.п.
Электроэрозионные станки
Электроэрозионная обработка, основана на физическом явлении, заключающемся в направленном разрушении материала обрабатываемой детали под воздействием электрических разрядов. Сущность направленного разрушения состоит в следующем. При электрическом разряде сфокусированный поток электронов, двигаясь с большой скоростью от одного электрода к другому, создает на поверхности электродов ударные волны сжатия. Возникшее в металле механическое напряжение распространяется по всем направлениям, в том числе, и откуда пришла ударная волна. Достигнув первоначальной поверхности, она отражается от нее и меняет знак на обратный, вследствие чего на поверхности возникают растягивающие напряжения. В результате этого происходит выброс частиц металла в направлении, встречном ударной волне сжатия. Электрод постепенно погружается в заготовку, копируя в ней свою форму.
В зависимости от вида применяемых разрядов эрозионная обработка делится на три вида, получивших широкое распространение: электроискровая, электроимпульсная и комбинированная с использованием электроэрозионного явления.
Электроискровая обработка осуществляется при использовании искровых разрядов малой длительности (порядка нескольких сотых секунду), которые следуют с большой скважностью. Обрабатываемая деталь 1 (рис. 3.123) погружена в жидкую среду 2 (керосин, трансформаторное масло, смесь керосина и индустриального масла и т.п.). Инструмент 3 (медь М1, М2, медный сплав МЦ-1, алюминий и его сплавы) перемещается поступательно-возвратно. Электрический ток от специального генератора Г подводится к детали-аноду и инструменту-катоду. Необходимый искровой зазор между деталью и инструментом поддерживается автоматическим регулятором АР. Форма разрушения детали зависит от формы торцовой части инструмента.
Электроискровая обработ- ка характеризуется широким диапозоном режимов обработ ки – от черновой производи- тельностью 1,5 – 10 мм3/с при Rz = 160 – 40 мкм до отделоч- ной производительностью око- ло 0,001 мм3/с при Ra = 1,25 – 0,16 мкм. Особенность этого процесса - сравнительно низ- кая производительность, большой износ электродов, об- Рис. 3.123. Схема станка для электроис- разование на обрабатываемой кровой обработки поверхности тонкого дефект- ного слоя толщиной 0,2 –0,5мм на черновых и 0,02 – 0,05 мм на чистовых режимах.
Область использования – обработка заготовок небольших размеров, изготовление твердосплавных матриц, отверстий малого диаметра.
Электроимпульсная обработка отличается от электроискровой тем, что обрабатываемая деталь является катодом, а инструмент – анодом. Импульсные разряды создают машинными и полупроводниковыми генераторами. Процесс осуществляется, как правило, на низких и средних частота (400 – 300 Гц) с низким напряжением (25 - 30 В) и большой силе тока (50 – 500 А). Длительность импульсов 0,5 – 1, мкс. Особенность процесса обработки - относительно небольшой износ электродов (например, для графита 0,1 – 0,5 %) и относительно высокая производительность, например, на черновых режимах 100 – 300 мм3/с при Rz = 80 – 40 мкм.
Электроимпульсная обработка используется при обработке средних и крупных штампов, пресс-форм лопаток турбин, решеток и т.п. деталей из закаленных и труднообрабатываемых деталей.
Станки для электроискровой и электроимпульсной обработки образуют размерный ряд, в котором в качестве основного параметра принят размер стола. К этому ряду относятся электроэрозионные копировально-прошивочные координатные станки высокой точности, например, моделей 4Д722А, 4Е723А, 4726 и группа станков с ЧПУ для профильной вырезки перематывающейся латунной проволокой, например, станок модели 4532Ф3.
Электроэрозионный вырезной станок с ЧПУ модели 4532Ф3.Предназначен для изготовления вырубных штампов холодной штамповки, фасонных фильер в матрицах, шаблонов и подобных деталей из токопроводящих материалов: легированных закаленных сталей, металлокерамических твердых сплавов и т.д. В качестве источника технологического тока в станке применен тиристорный генератор коротких импульсов.
3.124. Электроэрозионный вырезной станок модели 4532Ф3
Техническая характеристика. Наибольшие размеры обрабатываемой заготовки 250 × 160 × 75 мм; наибольшая масса 45 кг. Точность изготовления контура 0,032 мм. Наибольшая производительность при обработке: стали 35 мм3/мин, твердого сплава 18 мм3/мин.
Станок оснащен устройством ЧПУ типа «Контур» с линейным интерполятором. Может быть также оснащен мини-ЭВМ, где программа вводится посредством перфоленты или клавиатуры.
Класс воспроизведения вырезаемой поверхности копирование + след. Поэтому кинематическая структура станка содержит одну формообразующую группу Фv(П1П2) и три вспомогательные группы Вс(В3), Вс(П4), Вс(П5).
Группа Фs(П1П2) воспроизводит направляющую - профиль обрабатываемой поверхности посредством перемещения скобы с проволокой в горизонтальной плоскости в двух взаимно перпендикулярных направлениях (прямоугольная система координат). Конструктивно эта группа смонтирована в отдельном корпусе, перемещающемся по направляющим качения, выполненным в виде линейных подшипников (танкеток). Особенность группы – применение двух шаговых электродвигателей и синхронной электронной связи между ними, осуществляющей согласование продольной и поперечной кареток, несущих скобу (аналог инструментального суппорта).
Внутренняя связь:
продольная каретка (П1) → 1/tТВ=5 → 75/24 → 60/18 → М2 → М3 →
→ 18/60 → 24/75 → tТВ=5 → поперечная каретка (П2).
Группа включает две одинаковых внешних связи, обеспечивающие внутреннюю связь энергией движения.
Первая внешняя связь:
М2 → 18/60 → 24/75 → tТВ=5 → продольная каретка (П1).
Вторая внешняя связь:
М3 → 18/60 → 24/75 → tТВ=5 → продольная каретка (П2).
Звено соединения связей – «электрический вал», или система синхронизации, функцию которой выполняет линейный интерполятор системы ЧПУ, связывающая оба шаговые электродвигателя.
Группа настраивается на траекторию и скорость – системой ЧПУ.
При линейном перемещении скобы по одной из двух координат в любую сторону за один импульс от пульта ЧПУ (при минимальном повороте вала шагового двигателя на 1,5о) составит
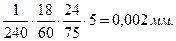
Ручное установочное перемещение скобы осуществляется в продольном направлении непосредственно от ТВ, в поперечном направлении через винтовую зубчатую передачу 28/28 и ТВ.
Скоба служит для установки и крепления всех устройств и механизмов, обеспечивающих перемотку и натяжение электрода-проволоки. Для устранения влияния износа проволоки на обработку ее перематывают с небольшой скоростью.
Перемотка проволоки осуществляется группой Вс(В3). Ее внутренняя связь:
подшипниковые опоры скобы → гильза шпинделя приемной катушки (В3).
Внешняя связь:
М4 → ременная передача → гильза шпинделя приемной катушки (В3).
Скорость перемотки регулируется в пределах 8 – 20 мм/с посредством изменения частоты вращения ротора частотно регулируемого реактивного электродвигателя М4 типа РД – 09.
Перемотка проволоки сопровождается ее укладкой на приемной катушке. Это движение осуществляется группой Вс(П4), имеющей общий электродвигатель с группой Вс(В3).
Внутренняя связь группы укладки проволоки:
гильза → шпинделя приемной катушки (П4).
Внешняя связь:
М4 → 20/80 → 20/80 →20/80 → вал XIII → кулачок 2 →
→ качающийся рычаг 1 → шпинделя приемной катушки (П4).
Скорость раскладки ненастраивается, а изменяется одновременно с изменением скорости перемотки проволоки.
В нижней части станины расположена подъемная ванна для рабочей жидкости. В ванне расположен Г-образный стол для закрепления обрабатываемой заготовки. Подъем и опускание ванны осуществляется посредством ненастраиваемой группы Вс(П5). Ее внешняя связь:
М1 → 2/77 → ТВ → ванна (П5).
Скорость перемещения ванны
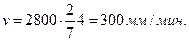
Не нашли, что искали? Воспользуйтесь поиском по сайту:
©2015 - 2025 stydopedia.ru Все материалы защищены законодательством РФ.
|