Роботизированные технологические комплексы
При обработке деталей на станках ПР используют главным образом для автоматизации вспомогательных процессов, связанных с обеспечением потоков заготовок и инструментов.
На рис. 3.114 приведена схема гибкого производственного модуля, состоящего из токарного станка 1, обслуживающего его универсального ПР 2 и транспортно-накопительного устройства 3 для заготовок и обработанных деталей. Рабочая зона ПР охватывает загрузочные и разгрузочные позиции транспортера-накопителя, зону обработки на станке, примыкающую к шпинделю, контрольно-измерительную позицию специального автоматического устройства 4.
Автоматический манипулятор имеет пять степеней подвижности: осевое перемещение по оси X руки на длине 800 мм; вертикальное перемещение по оси Y руки относительно стойки (перпендикулярно плоскости чертежа); поворот В руки на угол 3000 в горизонтальной плоскости; поворот А кисти руки на угол 1800 относительно продольной оси руки; поворот (качание) С кисти в вертикальной плоскости. Захватное устройство должно, кроме того, выполнять движения зажима-разжима заготовки или детали. Рабочая зона робота имеет ограждение 5, обеспечивающее безопасность для обслуживающих данный модуль рабочих и наладчиков.
Микропроцессорное устройство ЧПУ централизовано управляет всем оборудованием модуля во время автоматического цикла работы.
В составе гибкого производственного модуля ПР обслуживает, как правило, три позиции: загрузочную позицию накопителя заготовок, рабочую позицию станка и разгрузочную позицию транспортера или накопителя. Фактическая производительность модуля определяется коэффициентом использования станка кс, который зависит от длительности Тр его обслуживания роботом, отнесенной к общей продолжительности То обработки детали на станке: кс = 1 – Тр/То.
Рис. 3.114. Гибкий производственный модуль для токарной обаботки:
● – заготовка; ○ - деталь
Рассмотрим диаграмму цикла Тр обслуживания манипулятором токарного станка в производственном модуле (рис. 3. 115). Начало этого цикла отнесено к моменту остановки шпинделя, когда формируется команда на выполнение манипуляционных действий. Окончание периода обслуживания совпадает с выходом захватного устройства манипулятора из рабочей зоны станка и включением цикла Тм.
Общее время простоя станка (заштрихованные участки)
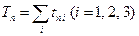
в основном определяется временем манипулирования заготовкой и деталью. Для сокращения этого времени необходимо либо увеличить скорости движения манипулятора и уменьшить общую длину перемещений его рабочего органа, либо совместить время манипулирования с рабочим циклом станка, создав рациональную компоновочную схему гибкого производственного модуля.
| | | Рис. 3.115. Циклограмма обслуживания токарного станка промышленным роботом
Гибкая производственная система для обработки деталей типа тел вращения (рис. 3. 116) состоит из двух токарных станков с ЧПУ и обслуживающего их ПР портального типа. Каретка 2 с установленной на ней механической рукой 3 перемещается по направляющим портала 1, смонтированного на колоннах 4. Рука 5 манипулятора двухзвенная и состоит из плечевого и локтевого рычажно-шарнирных механизмов. На базирующем фланце конечного звена руки установлен механизм кисти 6 с захватным устройством 7. Манипулятор имеет четыре степени подвижности: перемещение каретки по оси X, поворот А руки в плечевом шарнире, поворот D руки в локтевом шарнире, поворот С кисти вокруг своей оси на угол 90 или 1800. Кроме того для зажима и разжима деталей предусмотрено движение W губок схвата.
Управление приводами перемещений X, A, D осуществляется в режиме позиционирования от устройства 9 числового управления, а перемещений С, W – с помощью цикловой автоматики. Приводы манипулятора – гидравлические с автономным питанием от гидростанции 8. Конструкция манипулятора позволяет установить на его кисти дополнительные механизмы и устройства для контроля правильности базирования заготовки в центрах или патроне станка, измерения обрабатываемого диаметра заготовки и для очистки базирующих поверхностей от стружки путем обдува их сжатым воздухом.
В состав гибкой производственной системы помимо основного оборудования (станков 10 и обслуживающего их ПР) входят вспомогательные накопительные устройства 11 и 12 для установки в них в ориентированном положении заготовок и обработанных деталей, находящихся также в рабочей зоне манипулятора. Рабочая зона манипулятора имеет ограждение 13.
Рис. 3. 116. Гибкая производственная система
для обработки деталей типа тел вращения
Гибкая производственная система по рис. 3. 116 выполнена по схеме с линейной компоновкой. Возможна также круговая компоновка технологического оборудования, по которй станки располагают по дуге окружности, а в центре окружности размещают ПР. Круговые компоновки целесообразно использовать для небольшого числа технологических позиций (до пяти-шести) и при малых размерах рабочей зоны обслуживающего их ПР стационарного типа. При установке большого числа станков, а также для увеличения зоны обслуживания целесообразно использовать линейные компоновочные схемы и ПР передвижного типа.
Проектирование гибких производственных систем, в которых несколько ПР обслуживают большое число станков, транспортно-накопительных и других вспомогательных устройств, образующих участки или линии требует нахождения оптимального режима работы всей системы. При этом выбору ПР для обслуживания такой системы должен предшествовать анализ геометрических характеристик и массы изготавливаемых деталей, а также основных параметров станков, на которых обработка соответствующих заготовок наиболее эффективна.
Агрегатные станки
К агрегатным относят многоинструментальные специальные станки, проектируемые из стандартных и нормализованных узлов. Они предназначены для обработки сложных, как правило, корпусных деталей в серийном, крупносерийном и массовом производстве. На этих станках выполняют сверление, зенкерование, развертывание, растачивание, фрезерование и нарезания резьбы.
Достоинства агрегатных станков:
- более высокая производительность по сравнению с универсальными станками, обусловленная многоинструментальной обработкой;
- относительная простота изготовления вследствие унификации узлов и деталей;
- сокращение сроков проектирования и изготовления;
- возможность обслуживания станков рабочими относительно невысокой квалификации.
Наибольшее распространение получили агрегатные станки сверлильно-расточной и фрезерной групп. Компоновка этих станков весьма разнообразна. Она зависит от формы, размеров и точности обрабатываемых деталей, расположения на них обрабатываемых поверхностей и принятого технологического процесса.
Не нашли, что искали? Воспользуйтесь поиском по сайту:
©2015 - 2025 stydopedia.ru Все материалы защищены законодательством РФ.
|