Станки для обработки конических зубчатых колес
Конические зубчатые колеса используют для передачи вращательного движения между пересекающимися и скрещивающимися осями. Форма зубьев конических колес по длине может быть прямолинейной или криволинейной, наклоненной к образующей начального конуса под некоторым углом. Из криволинейных зубьев чаще всего применяют круговой, так как его проще нарезать, кроме того, круговой зуб с углом наклона на малом диаметре колеса β=0 воспринимает меньшее осевое давление. Станки для обработки конических колес, как правило, содержат две частных кинематических структуры, одна из которых реализует метод формообразования зубчатой поверхности копирование + след, а другая – след + обкат.
Обработка зубьев конических колес при профилировании обкатом основана на представлении о производящем колесе, т.е. воображаемом плоском или плосковершинным коническом колесе, с которым обкатывается в процессе обработки заготовка. Рассмотрим понятие о производящем колесе на примере обработки прямозубого колеса. Характерным для плоского колеса является угол при вершине начального конуса 2φ0 = 1800 (рис.3.73, а), благодоря чему
Рис. 3.73. Производящее колесо: Рис. 3.74. Схема образования
а – плоское; в – плосковершинное зубьев конического колеса
дополнительный конус превращается в цилиндр с осью ZZ и образующей ab. При развертке цилиндра на плоскость зубья колеса образуют прямобочную зубчатую рейку. Процесс формообразования зубьев на заготовке можно представить следующим образом. Предположим, что заготовка выполнена из идеального пластичного материала. Если ее перекатывать без скольжения по стальному плоскому коническому производящему колесу, то его зубья на поверхности заготовки будут формировать впадины. После одного оборота заготовки вокруг своей оси образуется зубчатый венец, зубья которого будут очерчены по октоидальному профилю. Он мало отличается от принятого эвольвентного и вполне удовлетворяет практическим требованиям. То же самое произойдет и в случае, если, перекатывая заготовку, вместе с ней вращать производящее колесо. Вращение заготовки и производящего колеса должны быть кинематически согласованы и, происходить без скольжения по начальным конусам. В рассматриваемом случае, имея в виду плоское коническое колесо (2φ0 = 1800), начальный конус нарезаемого колеса должен катиться по начальной плоскости xx.
Оставим на производящем колесе 1 только два зуба (рис.3.74). Сообщим заготовке 2 и производящему колесу 1 вращение в направлении стрелок. После того как заготовка перекатится через два зуба, реверсируем вращение и возвращаем оба колеса в исходное положение. В результате этих перемещений два зуба производящего колеса образуют на заготовке две впадины: зуб 5 – впадину 4, а зуб 6 – впадину 3. Таким образом, будет получен первый зуб на заготовке.
Повернем заготовку в исходное положение вокруг своей оси против часовой стрелки на угол, соответствующий шагу зацепления, и повторим весь цикл предыдущих движений. Тогда зуб 5 образует на заготовке новую впадину, а зуб 6 будет входить в контакт с уже имеющейся впадиной 4. В итоге второго цикла движений получим второй зуб на заготовке и так далее, до тех пор, пока не будут образованы все зубья. Таким образом, процесс формообразования профиля зубьев совершается в результате ряда чередующихся циклов движений. Каждый же цикл состоит из:
- обкатного движения производящего колеса и заготовки, в процессе которого зубья колеса внедряются в материал заготовки, образуя впадины;
- реверсирования движения обката в обратном направлении;
- движения деления в конце обратного хода, когда заготовка поворачивается на один зуб.
Зубья 5 и 6 производящего колеса заменяют двумя резцами 7 и 8. Резцы попеременно совершают прямолинейное поступательно-возвратное движение в радиальном направлении. Режущие кромки аb и а1b1 в своем поступательном движении в плоскостях abcd и a1d1c1d1 образуют впадину производящего колеса. Поэтому, если наряду с прямолинейным перемещением сообщить резцам вращение вместе с производящим колесом вокруг точки О, то в обкатном движении резцы, врезаясь в заготовку, выстрагивают в ней впадины. Режущие кромки ab и a1b1 в своем относительном движении огибают боковые поверхности зуба нарезаемого колеса. Так как толщина резцов меньше толщины зуба производящего колеса, то впадины 3 и 4 при первом контакте с резцами не будут иметь полной ширины.
Таким образом, при формообразовании зубьев конических колес необходимо осуществлять следующие движения:
- движение скорости резания – прямолинейное поступательно-возвратное движение резцов при обработке прямозубого колеса или вращательное движение резцовой головки при обработке колеса с дуговым зубом;
- движение обката (круговой подачи), состоящее из согласованных вращательных движений заготовки и производящего колеса;
- движение деления – поворот заготовки в конце обратного хода.
При обработке впадины необходимо вершины резцов перемещать вдоль образующей yy дна впадины нарезаемого колеса, т. е. под углом к плоскости перпендикулярной к оси вращения производящего колеса (см. рис. 3.73, а). Этот угол различен для разных колес. Следовательно, траекторию движения резцов необходимо настраивать по этому углу, что усложняет конструкцию резцового узла и снижает его жесткость.
В практике в целях упрощения конструкции резцового узла допускают отступление: образующую yy дна впадины совмещают с плоскостью xx, перпендикулярной к оси вращения производящего колеса, и вершины резцов перемещают в этой плоскости (рис. 3.73, в). В связи с этим величина угла 2φ0 будет меньше 1800. Из схемы следует,
2φ0 = 1800 - 2γ,
где γ – угол ножки нарезаемого колеса.
Полученное таким образом производящее колесо, называется плосковершинным.
Число зубьев производящего колеса определяется на основании известных зависимостей для конических колес. Можно написать

где z – число зубьев нарезаемого колеса; zп – число зубьев производящего колеса.
Откуда, число зубьев плосковершинного производящего колеса

У плоского колеса угол γ = 0, следовательно, cosγ =1. Тогда, число зубьев плоского производящего колеса

Конструктивно производящее колесо с приводом резцов или резцовой головки выполняется в виде узла, называемого люлькой.
Нарезание прямозубых конических колес осуществляется преимущественно посредством двух зубострогальных резцов, а нарезание колес с дуговым зубом – резцовыми головками, режущие зубья которых расположены на окружности. Кинематическая структура этих станков однотипна. Она содержит простую группу скорости резания Фv(П1) или Фv(В1), обеспечивающую движение резцов или резцовой головки для получения линии зубьев по длине, сложную группу подачи Фs(В2В3), обеспечивающую обкатное движение заготовки и производящего колеса, для воспроизведения профиля зубьев и группу деления Д(В4). Шпиндель заготовки является общим исполнительным органом групп Фs и Д. Поэтому эти группы должны иметь между собой кинематическую связь. Для этого применяют один из трех способов соединения кинематических групп: параллельный, последовательный и смешанный (параллельно-последовательный). В зависимости от способа соединения групп Фs и Д видоизменяются кинематическая структура станков и их настройка. Рассмотрим типовую структуру зуборезных станков (рис. 3.75).
Структура групп Фv(П1) и Фv(В1) простая. Внутренняя связь или поступательная пара
направляющие люльки → ползуны резцов (П1),
или вращательная пара
подшипниковые опоры на люльке → шпиндель резцовой головки (В1).
Внешняя связь: кинематическая цепь
М → 1 → 2 → iv → 3,
соединяющая электродвигатель М или с ползунами резцов (П1), или со шпинделем резцовой головки (В2).
Группа Фv(П1) настраивается по четырем параметрам: на траекторию - изменением угла между направлениями поступательно-возвратного движения резцов; на скорость – органом настройки iv; на путь и исходную точку – изменением плеч механизма, преобразующего вращательное движение в поступательно-возвратное резцов.
Рис. 3.75. Кинематическая структура зуборезного станка для нарезания
конических колес: а – при параллельном соединении групп Фs и Д;
б – при смешанном соединении групп Фs и Д
Группа Фv(В1) настраивается только по одному параметру: на скорость – органом настройки iv.
Группа Фs(В2В3) сложная. Ее внутренняя связь - кинематическая цепь
В3 → 5 → 6 → iпроф→ ∑→ iдел → В2,
называемая цепью обката или профилирования.
Внешняя связь - кинематическая цепь
М → 1→ 2 → is → Р → iкл → 6,
передающая энергию движения от электродвигателя во внутреннюю связь через звено соединения связей 6.
Группа настраивается на траекторию – органом настройки iпроф; на скорость – органом настройки is; на путь – угол качания Ө0 люльки, необходимый для полного профилирования одного зуба нарезаемого колеса, после чего люлька должна возвратиться в исходное положение для профилирования следующего зуба - органом настройки iкл.
Группа деления Д(В4) простая. Ее внутренняя связь вращательная пара
делительная бабка → шпиндель заготовки.
Внешняя связь при параллельном соединении групп Фs и Д (рис. 3.75,а): М → 1 → 2 → is → 8 → 10 → ДД → 11 →∑ → iдел → 7 → В4 .
Внешняя связь при смешанном соединении (рис. 3.75,б):
М → 1 → 2 → 10 → 11 → 12 → 8 → 6 → iдел → 7 → В4..
Группа настраивается на путь – органом настройки iдел. Управление делением – периодическое включение и отключение его – осуществляется распределительным валом Б-А.
Рассмотрим общие принципы настройки станков анализируемого класса и выведем ФН для их органов настройки, которые выполняют, как правило, в виде гитар сменных зубчатых колес.
Орган настройки iv. РП при обработке конических прямозубых колес:
пМ мин-1 → пР дв. ходов/мин резцов.
УКЦ:
пР = пМ i01 iv.
ФН:
iv = nр/(пМ i01),
где i01 – произведение передаточных отношений постоянных передач расчетной цепи.
Выразим пР через скорость резания v:
пР = 1000v/(2L),
где L –ход резцов в движении П1, состоящий из длины линии зуба колеса и величин перебегов резца на входе и выходе из зоны резания.
После замены пр, окончательно получим
i v = c1 v L,
где с1 – константа конкретной модели станка, равная 1000/(2пМi01L).
РП при обработке конических колес с дуговым зубом:
пМ мин-1 → пРГ мин-1
УКЦ:
пРГ = пМ i01 iv.
ФН:
iv = nРГ/(nМ i01) = пРГ/с2,
где с2 – константа, равная пМ i02.
Орган настройки iпроф. Расчетная цепь совпадает с внутренней связью группы обката ФS. РП:
1 об. люльки (В3) → zп/z об. заготовки (В2).
УКЦ при параллельном соединении групп Фs и Д:
zп/z = 1 i03 iпроф i∑ iдел.
ФН:
iпроф = zп/(z i03 i∑ iдел) = zп/(с3 z iдел),
где с3 – константа, равная i03 i∑.
Орган настройки is. Все зуборезные станки рассматриваемого класса, являясь полуавтоматами, оснащены временной системой управления и, следовательно, работают в цикловом режиме. За время цикла принимают время обработки одного зуба (впадины.). Этим же временем условно задается подача, и поэтому ее называют цикловой. Время цикла есть сумма
tц = tр + tх ,
где tц – время цикла; tр – время рабочего хода люльки (ее поворот в процессе профилирования зуба); tх – время вспомогательного хода (ее поворот в исходное положение).
Для повышения производительности стремятся, чтобы tх ‹ tр. Для этого нередко в зуборезных станках во внешней связи группы Фs применяют передачи или цепь передач, позволяющие получить ускоренное вращение люльки при вспомогательном ходе. Включение и отключение этих передач осуществляется с помощью распределительного вала, который за время цикла всегда совершает один оборот. В рассматриваемой структуре (см. рис. 3. 75,б) эту функцию выполняет распределительный вал Б – А, управляющий муфтами М1 и М2.
РП для структуры по рис. 3.75,а (варианта 1):
1 об. распределительного вала → (nМ/60) tц об. электродвигателя.
Если при вспомогательном ходе люльки движение к ней передается минуя орган настройки is, то распределительный вал имеет две различные скорости, причем во время вспомогательного хода распределительный вал всегда вращается с постоянной скоростью. В этом случае (вариант 2) РП по рис. 3.75,б имеют иной вид
δ0р/3600 об. распределительного вала → (nМ/60) tр об. электродвигателя,
где δ0р–угол поворота распределительного вала, соответствующий времени tр.
Угол δ0р зависит от соотношения скоростей вращения люльки при рабочем и вспомогательном ходах и определяется для каждого конкретного станка и передаточных отношений зубчатых передач механизма реверса люльки.
УКЦ по варианту 1:
(пМ/60) tц = 1 i04 is.
ФН:
is = с4/tц ,
где с4 = пМ/(60 i04) – константа; i04 – произведение постоянных передач расчетной цепи электродвигатель – распределительный вал.
УКЦ по варианту 2:
(пМ/60) tр = (δ0р/3600) i05 is.
ФН:
is = c5 tр,
где с5 = (пМ60) (δ0р/3600) tр.
Настройка движения Фs на путь, т.е. на угол качания Ө0 люльки, зависит от способа соединения групп Фs и Д. При параллельном соединении групп периодическое делительное движение суммируется через дифференциал ∑ с движением заготовки В2 в период реверсирования движения обката Фs, т.е. возврата люльки в исходное положение для профилирования следующего зуба или впадины нарезаемого колеса. При этом заготовка за время реверсирования, т.е. за tх , как правило, поворачивается на 1/z оборота.
При смешанном соединении групп реверсируется только люлька, а заготовка продолжает непрерывно вращаться в одну сторону. Причем за время возвращения люльки в исходное положение заготовка поворачивается на zi/z оборота, где zi – число зубьев заготовки, пропускаемых между двумя последовательными циклами делений. Это число, т.е. zi не должно иметь общих множителей с z заготовки.
При обоих способах соединения групп для возврата люльки в исходное положение в структуре станка необходим реверс. При параллельном соединении для реверсирования люльки и заготовки реверс располагают во внешней связи группы Фs на участке 8 – 6. При смешанном соединении надо реверсировать только люльку, и поэтому реверс располагают во внутренней связи группы Фs на участке 6 – 15 – 16 – 5 цепи профилирования от звена присоединения внешней связи к внутренней до люльки. В этом случае наибольшее распространение получил специальный реверс в виде составного колеса, рассмотренный в разделе 2. Вращение ведущего колеса реверса в одну сторону и постоянство его зацепления с внутренним замкнутым контуром составного колеса будет сообщать последнему вращательное движение то в одну, то в другую сторону и тем самым осуществлять реверсирование люльки. Ведущее колесо реверса обходит один раз полностью весь внутренний контур составного колеса за время цикла обработки одного зуба нарезаемого колеса.
При параллельном соединении групп Фs и Д настройка на путь осуществляется органом настройки iкл. Для этого органа УКЦ имеет вид:
δ0р/3600 об. распределительного вала → Ө0/3600 об. люльки.
Угол Ө0 = ψ0(z/zп), где ψ0 – угол поворота заготовки для полного профилирования зуба нарезаемого колеса, который выбирают по специальным номограммам в зависимости от числа нарезаемых зубьев, модуля и других параметров колеса.
УКЦ:
Ө0/3600 = δ0р/3600(i06 iкл).
ФН:
iкл = (1/i06)(Ө0/δ0р),
где i06 – произведение передаточных отношений постоянных передач расчетной цепи распределительный вал – люлька.
При смешанном соединении групп путь движения обката Фs настраивают посредством органов настройки iпроф и iдел, в ФН которых фигурирует число zi, являющееся функцией угла качания люльки и соответственно угла поворота ψ0 заготовки. Функцию zi = f (ψ0) определяют отдельно для каждого конкретного станка, используя для этого следующее соотношение: zi = (Ө0/δ0р) zп.
Орган настройки iдел. РП при параллельном соединении групп:
поз об. отсчетного звена → 1/z об. заготовки,
причем отсчетным звеном может быть, например, делительный диск ДД.
УКЦ:
1/z =п i07 i∑ iдел.
ФН:
iдел = с7/z,
где с7 – константа конкретной модели станка.
РП: при смешанном соединении групп:
1об. распределительного вала → zi/z об. заготовки.
УКЦ:
zi/z = 1 i08 iдел.
ФН:
iдел = с8 zi/z,
где с8 – константа конкретной модели станка.
Зубонарезание конических колес при профилировании обкатом используется при чистовой обработке. При незначительной переналадке рассмотренные типовые кинематические структуры зуборезных станков позволяют также осуществлять профилирование зубьев по методу копирования. В этом варианте зубонарезания конических колес класс воспроизведения зубчатой поверхности копирование + след. Этот вариант используется для черновой обработки. При нарезании прямозубых колес при профилировании копированием из типовой структуры исключается группа обката, и вводится простая группа врезания Вр(П2) на высоту зуба. При нарезании конических колес с круговым (дуговым) зубом группа обката из кинематической структуры не исключается, но существенно на 2-3 порядка замедляется скорость движения обката, что при профилировании равнозначно остановке этого движения.
Существуют также станки для шлифования зубьев конических колес. Прямозубые колеса шлифуют двумя дисковыми кругами с продольной подачей их вдоль линии зуба. Конические колеса с круговыми зубьями шлифуют чашечным кругом. Структура такого станка аналогична структуре станка, работающего резцовой головкой.
Рассмотрим возможные циклы зубонарезания при профилировании обкатом и при профилировании копированием.
Цикл нарезания прямозубого колеса при профилировании обкатом:
- заготовка быстро подводится к резцам и устанавливается на глубину предварительной (черновой) обработки (рис. 3.76, а);
- предварительная обработка боковых поверхностей одного зуба движениями Фv и Фs (рис. 3.76, б);
- реверсирование движения Фs до горизонтального положения оси профиля обрабатываемого зуба и подвод заготовки на глубину окончательной (чистовой) обработки (рис.3.76, в);
- окончательная обработка зуба движениями Фvи Фs(рис.3.76, г);
- быстрый отвод заготовки и деление на зуб при продолжающемся движении обката;
- повторение цикла до тех пор, пока не будут обработаны все зубья.
При обработке прямозубых колес последним вращающимся звеном внешней связи группы Фv является кривошипный диск 5, расположенный в центре люльки (рис. 3.77). Этот диск посредством шатуна 6 сообщает качательное движение диску 7, в прямолинейном пазу которого размещены сухари, соединенные посредством пальцев с ползунами 1. Ползуны расположены в направляющих, смонтированных так, чтобы резцы 2 образовали угол 2δ' с центром вращения люльки (воображаемого производящего колеса).
Угол δ1 установки резцов определяют по формуле
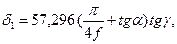
где α - угол зацепления; γ – угол ножки зуба; f – коэффициент высоты зуба.
Обычно α = 200, а f = 1,1236, то для этого случая δ1 = 60,884 tgγ.
Рис. 3.76. Схема образования зубьев Рис. 3.77. Исполнительный механизм группы Фv
Цикл работы станка при профилировании колеса копированием:
- быстрый подвод стола с бабкой, несущей заготовку;
- врезание на высоту зуба при рабочей подаче стола;
- быстрый отвод стола из зоны резания;
- одинарное или двойное деление;
- повторение цикла до тех пор, пока не будут обработаны все зубья.
При одинарном делении используется два стандартных резца. При этом каждый резец выстрагивает свою часть впадины. При двойном делении используются нестандартные резцы. Каждый резец выстрагивает всю впадину.
На некоторых моделях станков предусмотрена также возможность обработки бочкообразных зубьев. Для этого на люльке прямолинейные направляющие для ползунов 1заменяют соответствующими криволинейными.
При обработке конических колес с круговыми зубьями в качестве производящего колеса принимают плоское колесо 1, зубья которого направлены по дуге окружности радиуса r (рис. 3.78). Заготовка 2 в процессе обработки обкатывается с производящим колесом 1, зубья которого воспроизводятся резцовой головкой 3, вращающейся вокруг точки О1. Профиль резцов соответствует профилю зубьев производящего колеса. Проходя участок АА1, они имитирую один зуб производящего колеса.
Согласованность вращения люльки 1 (рис. 3.79) и заготовки 2 (станочное зацепление) обеспечивается сменными зубчатыми колесами 4, подбираемыми в зависимости от числа зубьев нарезаемого колеса. Вершины резцов 3 должны передвигаться по образующей внутреннего конуса нарезаемого колеса. Поэтому колесо необходимо установить под углом φi внутреннего конуса к плоскости, в которой передвигаются вершины резцов.
Рис.3.78. Схема нарезания конических Рис. 3.79. Схема установки заготовки при
колес с круговыми зубьями нарезании круговых зубьев
Заготовка должна устанавливаться относительно центра станка, под которым понимается точка пересечения горизонтальной оси ОО2 люльки, оси ОО1 шпинделя бабки и вертикальной оси О поворотного стола. Через центр стола должна проходить плоскость, в которой передвигаются вершины резцов головки, и с центром стола должна совпадать вершина начального конуса нарезаемого колеса.
Резцовая головка (рис. 3.80, а) выполняется в виде диска с пазами, в которые вставляются и крепятся резцы перпендикулярно торцовой плоскости диска. Резцы бывают наружные (рис. 3.80, б) и внутренние (рис. 3.80, в). Резцы подразделяются также на праворежущие и леворежущие, отличающиеся только расположением режущих кромок. Стандартные резцовые головки имеют диаметр 150–300 мм.
Возможный цикл нарезания колеса с дуговым зубом при профилировании обкатом:
- подвод заготовки к резцовой головке;
- прорезка впадины вращающейся резцовой головкой (движение резания) при согласованном вращении люльки, несущей резцовую головку, и шпинделя с заготовкой (движение обката);
- отвод заготовки от резцовой головки при продолжающемся вращении заготовки в туже сторону, одновременно реверсирование и ускоренное обратное вращение люльки;
- подвод заготовки, реверсирование люльки и повторение цикла.
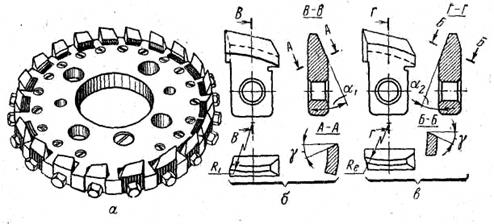
Рис. 3.80. Резцовая головка
Обработка конических зубчатых колес с дуговым зубом при профилировании обкатом используется при нарезании колес с большим углом начального конуса. В этом случае угол обката (качания) люльки велик, и профилирование обкатом становится малопроизводительным. Однако, чтобы не усложнять структуру станка введением дополнительных механизмов, а использовать те же кинематические цепи, движение обката не выключается, а только замедляется так, чтобы за время цикла обработки заготовка повернулась всего на один зуб.
Цикл обработки:
- прорезка одной впадины при рабочей подаче врезания заготовки на резцовую головку и медленном движении обката;
- отвод заготовки при продолжающемся ее вращении в туже сторону, и одновременное реверсирование и вращение люльки в обратном направлении;
- подвод заготовки, реверсирование люльки повторение цикла прорезки соседней впадины.
За время цикла прорезки впадины люлька по-прежнему совершает одно двойное качание, а заготовка, вращаясь в одном направлении, повернется, за это же время относительно люльки, на один зуб (впадину).
Нарезание конических колес с круговыми зубьями при профилировании обкатом характеризуется длительным циклом обработки, так как для устранения огранки зубьев при обработке и получения высокого класса чистоты поверхности, приходится увеличивать время огибания (обката). Много времени затрачивается на холостые ходы. Поэтому в крупносерийном и массовом производстве спирально-конических и гипоидных передач используется более производительный способ полуобкатной обработки. В полуобкатной передаче при профилировании обкаткой нарезают шестерню, имеющую небольшое число зубьев, а колесо нарезают резцовой головкой или круговой протяжкой при профилировании копированием.
На рис. 3.81 жирными линиями очерчены профили зубьев полуобкатной передачи. Для сравнения тонкими линиями показаны профили зубьев обычной передачи, нарезаемой при профилировании обкатом. Профиль зуба колеса в этом случае получается полнее. Такое утолщение профиля колеса должно соответствовать утонению профиля шестерни. Это изменение профиля шестерни называют модификацией. В ряде моделей Рис. 3.81. Профили зубьев станков рассматриваемого класса для модифика- полуобкатной передачи ции профиля шестерни использует- с ся механизм модификации, выполненный в виде дополнительной настраиваемой кинематической цепи во внутренней связи группы обката, включающей суммирующий механизм с червячной передачей, в котором равномерное вращение червяка люльки суммируется с его неравномерным поступательным перемещением.
В станочном парке технологического оборудования машиностроительного производства используются различные модификации базовых моделей станков 523, 526 для нарезания прямозубых конических колес и 525, 528 для нарезания колес с круговыми зубьями, реализующих рассмотренную обобщенную структурную схему станка для нарезания конических колес. Станки моделей 5А26 и 525 подробно описаны в [2.8].
Не нашли, что искали? Воспользуйтесь поиском по сайту:
©2015 - 2025 stydopedia.ru Все материалы защищены законодательством РФ.
|