Способ И.И. Остромысленского
Другой способ получения бутадиена, предложенный русским химиком И.И. Остромысленским еще в 1915 г., был реализован в США в годы Второй мировой войны. В отличие от способа С.В. Лебедева этот процесс протекает в две стадии.
На первой стадии дегидрированием этанола получают ацетальдегид:
С2Н5ОН СН3СНО + Н2
На второй стадии смесь спирта и ацетальдегида в мольном соотношении 3:1 пропускают над катализатором (оксид тантала на силикагеле):
СН3СНО + С2Н5ОН СН2 =СНСН=СН2 + 2 Н2О
Селективность процесса – 63,9% от теоретической.
По этой технологии дегидрирование осуществляют при 523-573 К. В ка-честве катализатора используют медь, нанесенную на асбестовое волокно. В качестве промоторов к катализатору добавляют 5 % оксида кобальта и 2% ок-сида хрома (в расчете на медь). Выход ацетальдегида на пропущенный этанол составляет 30-40% при селективности ~ 92%. Основными побочными продук-тами являются масляный альдегид, этилацетат и уксусная кислота.
Вторая стадия получения бутадиена по этому способу представляет собой совместное превращение этанола и ацетальдегида в присутствии в качестве ка-тализатора оксида тантала, нанесенного на силикагель, при 603-623 К и атмо-сферном давлении. Синтез бутадиена протекает через стадию образования кро-тонового альдегида:
2CH3—CHO CH3—CH=CH—CHO + H2O
CH3—CH=CH—CHO + CH3—CH2OH CH2=CH—CH=CH2 + CH3CHO + H2O
В годы Второй мировой войны по методу Остромысленского в США выпус-
калось ~ 60% всего бутадиена, использованного для производства синтети-
ческого каучука.
После 1952 г. все заводы, использовавшие этот процесс, были закрыты из-за их нерентабельности.
Получение бутадиена из ацетилена
В Германии часть бутадиена производилась из ацетилена, который полу-чали из карбида кальция. Были разработаны два многостадийных процесса:
- синтез бутадиена через альдоль - этот способ осуществлялся на заводах е фирмы "И.Г. Фарбениндустри";
- синтез бутадиена через бутиндиол – этот способ был реализован, в част-ности, на заводе в г. Людвигсгафене фирмой БАСФ.
Синтез бутадиена через альдоль (альдольный метод)
Альдольный метод включает четыре стадии: гидратацию ацетилена до ацетальдегида, конденсацию ацетальдегида в альдоль, гидрирование альдоля до бутиленгликоля, дегидратацию бутиленгликоля в бутадиен.
Гидратация ацетилена в течение ряда лет являлась основным методом полу-
чения ацетальдегида, однако в последнее время этот процесс вытесняется
методами, базирующимися на более дешевом сырье - этилене.
В промышленности используют метод получения ацетальдегида из аце-тилена гидратацией в жидкой фазе в присутствии ртутных катализаторов (реак-ция Кучерова). Впервые в промышленном масштабе она была реализована в присутствии раствора сульфата двухвалентной ртути в серной кислоте:
СНºСН + H2O СН3СНО DН = 142 кДж/моль
Сульфат ртути образуется непосредственно в реакторе гидратации из метал-
лической ртути. Соль ртути образует с ацетиленом сложные промежуточные
соединения, которые разлагаются на ацетальдегид и сульфат ртути. В связи
с тем, что катализатор постепенно теряет активность, часть ртути выводится
из реактора в виде шлама, а в реактор периодически вводят свежую метал-
лическую ртуть. Синтез осуществляют при температуре ~373 К и давлении
0,25 МПа. Выход бутадиена достигает 90-97% от теоретического.
Жидкофазная гидратация ацетилена проводится при 348-368 К в присут-ствии 10-20% (мас.) серной кислоты и 0,5-1,0% (мас.) ртутного катализатора (в пересчете на HgО).
Высокая токсичность ртути привела к необходимости разработки процес-са парофазной гидратации ацетилена над нертутными катализаторами. Наи-большую активность и стабильность проявляет кадмийкальцийфосфатный ка-тализатор. Катализатор представляет собой смесь средних фосфатов кальция и кадмия, которая содержит некоторое количество кислых фосфатов при моль-ном соотношении (СаО + СdО):Р2О5, равном 2,8. Процесс проводят при 623 К. На поверхности катализатора в ходе процесса накапливаются смолистые веще-ства. Регенерацию катализатора осуществляют смесью воздуха и водяного пара при 673-703 К.
Конденсация ацетальдегида в альдоль проводится в присутствии 8-12%-ных растворов щелочи при атмосферном давлении и комнатной температуре:
2СН3СНО СН3СНОНСН2СНО DН = 72,2 кДж/моль
Выход альдоля составляет ~ 50% на пропущенный и 84-88% на превра-щенный ацетальдегид.
Гидрирование альдоля в бутиленгликоль
СН3СНОНСН2СНО + Н2 СН3СНОНСН2СН2ОН
проводят при 328-343 К и давлении 30,0 МПа. В качестве катализаторов ис-пользуют нанесенные на оксид алюминия или оксид кремния металлы: Со, Ni, Cu и другие.
Процесс дегидратации бутиленгликоля с получением бутадиена
СН3СНОНСН2СН2ОН СН2=СНСН=СН2 + 2Н2О DН = -118 кДж/моль
осуществляют при 543-553 К и атмосферном давлении в присутствии разбави-теля - водяного пара. В качестве катализатора используют кокс или графит, пропитанные фосфорной кислотой. Выход бутадиена на этой стадии ~ 47% за один проход или 97% от теоретического.
Синтез бутадиена через бутиндиол
В годы Второй мировой войны в Германии был разработан и реализован в промышленности синтез бутадиена на основе ацетилена через бутиндиол. Бу-тиндиольный метод включает взаимодействие ацетилена и формальдегида с образованием 2-бутиндиола-1,4 и последующее гидрирование его в бутиленди-ол и бутандиол; бутандиол дегидрируют в бутадиен.
Основную стадию - конденсацию ацетилена с формальдегидом с образо-ванием 2-бутиндиола-1,4 (метод Реппе) проводят при 373 К и 0,5 МПа.
СНºСН + 2СН2О НОСН2-СºС-СН2ОН DН = 231 кДж/моль
В качестве катализатора используют ацетиленид меди, нанесенный на си-ликагель. Формальдегид используют в виде 8%-ного водного раствора. Выход бутиндиола достигает по ацетилену около 80% и по формальдегиду около 90%.
Синтез бутиндиола протекает в две стадии.
На первой стадии образуется пропаргиловый спирт, который в присутст-вии катализатора присоединяет вторую молекулу формальдегида:
НСºСН + СН2О СНºС-СН2ОН,
СНºС-СН2ОН + СН2О НО—СН2-СºС-СН2ОН.
На второй стадии бутиндиол гидрируется с образованием бутандиола:
НОСН2-СºС-СН2ОН + 2Н2 НОСН2СН2СН2СН2ОН + 252 кДж .
Гидрирование водного раствора бутиндиола проводят при 423-473 К и 30 МПа в присутствии медноникельхромового катализатора (9% меди, 90% нике-ля, 1% хрома, носитель - силикагель). Селективность образования бутандиола достигает 98%.
На третьей стадии бутандиол подвергают дегидратации с образованием тетрагидрофурана:
CH2—CH2
CH2OH—CH2—CH2—CH2OH
| CH2
| CH2+ H2O.
| O
Дегидратация осуществляется в жидкой фазе в присутствии кислого ка-тализатора (фосфорная кислота) при ~533-548 К и 7,0 МПа.
На заключительной стадии проводят дегидратация тетрагидрофурана с образованием бутадиена:
CH2—CH2
CH2
| CH2
| CH2=CH—CH=CH2 + H2O .
| O
|
|
| Процесс проводят при 543-553 К и 0,1 МПа в присутствии в качестве ка-тализатора дигидрофосфата натрия NaН2РО4, нанесенного на кокс или графит.
Метод Реппе в отличие от альдольного способа не получил широкого рас-
пространения ввиду сложности технологии.
Синтез бутадиена через димеризацию ацетилена
Этот метод включает димеризацию ацетилена с последующим гидриро-ванием винилацетилена в бутадиен:
2СНºСН СН2=СH—CºСН,
СН2=СH—CºСН + Н2 СН2=СН—СН=СН2.
Метод, несмотря на относительную простоту технологии, не нашел про-
мышленного применения главным образом из-за взрывоопасности реакци-
онных смесей, в состав которых входит ацетилен.
Пиролиз углеводородного сырья
Техническая возможность получения бутадиена пиролизом нефтяных фракций была показана В.Б. Бызовым в России в 1916 г.
При пиролизе любого углеводородного сырья, а особенно легких бензи-нов, в качестве побочного продукта образуется бутадиен, количество которого зависит от целей и условий проведения процесса. Если целевым продуктом пи-ролиза является не только этилен, но и пропилен и бутены, то выход бутадиена может достигать 5% (мас.) на пропущенное сырье, а содержание его во фрак-ции С4 может колебаться от 20 до 60% (мас.).
Промышленные способы получения бутадиена
Из бутана или бутена-1
Производство бутадиена из углеводородов С4 (н-бутан и н-бутены) мето-дами каталитического дегидрирования является основным направлением в со-временной технологии получения бутадиена. В промышленности используют различные технологические варианты получения бутадиена дегидрированием углеводородов С4. Применяемые процессы можно условно разделить на сле-дующие группы: дегидрирование бутана в бутены, дегидрирование бутенов; одностадийное дегидрирование бутана в бутадиен.
Характерной особенностью реакций дегидрирования с образованием олефинов является ограничение степени превращения условиями равновесия. Реакции дегидрирования всегда являются эндотермическими и, следовательно, равновесие в сторону образования ненасыщенных углеводородов должно сдви-гаться с повышением температуры. Степень превращения углеводородов воз-растает с повышением температуры и понижением давления. На практике при температурах выше 773-823 К даже в отсутствие катализаторов предельные уг-
леводороды претерпевают реакции изомеризации, крекинга и др. Поэтому про-цесс дегидрирования бутана проводят при температурах до 923-973 К, т.е. при температурах более низких, чем термодинамически оптимальные. Применение катализаторов позволяет достигнуть высокой скорости процесса при относи-тельно низкой температуре, когда еще не существенен вклад побочных реак-ций. Ввиду обратимости реакций дегидрирования –гидрирования и, следова-тельно, способности катализаторов ускорять обратимые реакции в обоих на-правлениях, эти реакции катализируются одними и теми же соединениями.
При дегидрировании вследствие отщепления водорода всегда происходит увеличение объема газа и понижение давления благоприятствует повышению степени конверсии. По этой причине процессы дегидрирования проводят при давлении, близком к атмосферному, а в некоторых случаях процесс осуществ-ляют в вакууме.
Иногда вместо применения вакуума предпочтительнее разбавлять реак-ционную массу газом, инертным в условиях реакции, или паром, что также приводит к снижению парциальных давлений реагентов и возрастанию равно-весной степени конверсии. Снижение парциального давления позволяет также понизить температуру реакции и, следовательно, уменьшить образование по-бочных продуктов.
Важным параметром при проведении реакции дегидрирования является время контакта реакционной смеси с катализатором. Рис. 4.1 иллюстрирует влияние температуры и времени реакции на содержание бутенов.
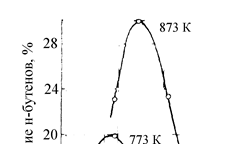
Рис. 4.1. Зависимость содержания н-бутенов при ка-
талитическом дегидрировании н-бутана от температуры
И времени реакции
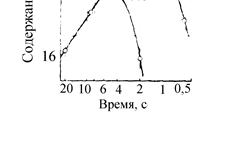
Максимальный выход олефинов не соот-ветствует рассчитанной равновесной концентрации при соответствующей тем-пературе: он всегда значительно ниже. С увеличением времени реакции выше оптимального выход олефинов уменьшается, так как увеличивается вклад по-бочных реакций.
Работы по каталитическому дегидрированию н-бутана по двухстадийно-му варианту: н-бутан ® н-бутен ® бутадиен были начаты в США в 1920-х го-
дах. В Советском Союзе фундаментальные исследования в этой области прово-дили С.В. Лебедев, Н.И. Шуйкин, А.А. Баландин, Б.А. Казанский и др.
Не нашли, что искали? Воспользуйтесь поиском по сайту:
©2015 - 2025 stydopedia.ru Все материалы защищены законодательством РФ.
|