|
Одностадийное дегидирование бутана в бутадиен
Одностадийный процесс дегидрирования алканов:
C4H10 C4H6 + 2H2
имеет очевидные преимущества перед двухстадийным процессом ввиду отсут-ствия необходимости разделения газовых смесей после каждой стадии и более низких энерго- и капитальных затрат. На рис. 4.2 представлена зависимость со-става равновесной смеси при дегидрировании бутана в бутены и бутадиен от температуры и давления.
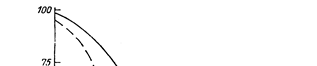
Рис. 4.2. Зависимость состава равно-
весной смеси при дегидрировании бу-
Тана в бутены и бутадиен от темпера-
Туры и давления
Сплошные линии - 0,1 МПа, штриховые
- 0,01 МПа.
1 – бутан; 2 – бутены; 3 – бутадиен
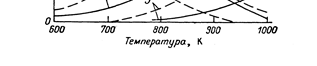
Термодинамические расчеты показывают, что равновесный выход диена существенно возрастает с повышением температуры и с уменьшением парци-ального давления алкана. Поскольку повышение температуры связано с поте-рей селективности реакции, одностадийное получение диенов из алканов было реализовано в условиях вакуумного дегидрирования. В одностадийном процес-се дегидрирования используют алюмохромовые катализаторы, содержащие 18-30% оксида хрома.
Фирма "Гудри" (США) впервые реализовала процесс получения бутадие-на из бутана в одну стадию (аналогично процессу получения изопрена из изо-пентана). В присутствии алюмохромового катализатора протекают побочные превращения бутана, бутенов и бутадиена. Применение алюмохромового ката-лизатора исключает использование водяного пара в качестве разбавителя. Принципиальная технологическая схема этого процесса, который проводят под вакуумом (0,015-0,020 МПа) в стационарном слое катализатора, приведена на рис. 4.3.

Рис. 4.3. Принципиальная технологическая схема процесса одностадийно-
Го дегидрирования бутана
1 - испаритель; 2 - трубчатая печь; 3 - топка; 4 - реакторы; 5 - котел-
утилизатор; 6 - скруббер; 7 - холодильник; 8 - турбокомпрес-
сор; 9 - абсорбер; 10 - десорбер; 11, 12 - ректификационные колонны;
13 - узел экстрактивной ректификации.
Потоки: I - свежий бутан; II - возвратная бутан-бутиленовая фракция;
III - воздух; IV - топливный газ; V - линия вакуума; VI - сброс в ат-
мосферу; VII - отдувкн в топливную сеть; VIII - углеводороды С3 на
сжигание; IX - фракция С4-С12; X - бутадиен
Сырье - смесь бутана и возвратной бутан-бутеновой фракции - испаряется в испарителе 1 и при 313 К поступает в трубчатую печь 2. Перегретые пары сы-
ч-1направляют в реактор 4, где при 863-898 К и остаточ-рьясоскоростью 240
ном давлении 11,3-22,7 кПа происходит процесс дегидрирования. Реактор представляет собой горизонтальный цилиндрический аппарат диаметром 6 м и длиной 12 м. Полный рабочий цикл продолжается 21 мин. 30 с., дегидрирова-
ние - 8 мин. 15 с., продувка паром, опорожнение реактора - 2 мин. 35 с. Из ре-акторного блока контактный газ подают в орошаемый охлаждающим маслом скруббер 6, в котором его охлаждают до 328 К, и затем в блок выделения бута-диена.
Конверсия бутана в одностадийном процессе составляет ~20%, а выход бутадиена 50-55% на превращенное сырье. Контактный газ содержит 37-39% бутана, 23-25% бутенов, 12-13% бутадиена.
Основные параметры процессов дегидрирования алкенов С4-С5 приведе-ны ниже:
| Фракция
| Фракция
| Параметр
|
|
|
| бутенов
| изопентенов
|
Температура в реакторе, К
| 873-923
| 873-923
| Объемная скорость подачи сырья, ч-1
| 130-180
| 150-220
| Мольное соотношение алкен:водяной пар 1:20 1:20
Температура регенерации катализатора, К 873-923 873-923
Перепад давления по слою катализатора, МПа 0,05-0,09 0,04-0,09
Степень конверсии исходного сырья, % 40 40-43
Селективность образования диена, % 85 76
Выход диена в расчете на пропущенное сырье, % 33 32-33
Содержание в контактном газе, %
Алкенов 59 45
Выделение бутадиена
Во всех процессах бутадиен получается в смеси с другими углеводорода-ми, близкими к нему по летучести. Выделение из таких смесей концентриро-ванного бутадиена, используемого для производства каучука, является весьма сложной задачей. Для стереоспецифической полимеризации необходим бутади-ен, тщательно очищенный от примесей других углеводородов диенового и аце-тиленового ряда и соединений неуглеводородного характера. В России для сте-реоспецифической полимеризации применяется бутадиен с концентрацией не ниже 99% (масс.) и содержанием примесей в нем не выше (% мас.):
Ацетиленовые углеводороды……………………0,005
Алленовые углеводороды………………………..0,01-0,03
Циклопентадиен……………………………….….0,001
Карбонильные соединения……………………….0,01
Азотистые соединения…………………………0,001-0,002
(в расчете на азот)
В табл. 4.2 приведен углеводородный состав продуктов дегидрирования бутана, бутенов и фракции С4 пиролиза бензина.
Таблица 4.2. Углеводородный состав продуктов дегидрирования бутана, бутенов
и фракции С4 пиролиза бензина ( в % (мас.))
Дегидрирование бутана Дегидрирование бутенов Пиролиз бензина
обычное вакуумное окисли-обычное на окислительное средний жесткий
на алю-на алюмо-тельное с кальций-на фосфор-при при
Компонент
мохромо-хромовом иодом и никель-висмут-1033 К1123 К
вом ката-катализа-акцепто-фосфатном молибденовом
лизаторе торе ром катализаторекатализаторе
С1-С3
| 9,48
| 4,75
| 9,20
| 2,45
| 0,05
| 1,1
| 0,31
| Изобутан
| 22,45
| 2,05
| 0,10
| 0,40
| 0,25
| 2,5
|
|
|
|
|
|
|
|
| 6,68
| н-Бутан
| 50,60
| 47,35
| 14,50
| 7,30
| 8,50
| 9,3
|
| Изобутен
| 1,90
| 5,5
| 1,50
| 8,55
| -
| 29,0
| 23,98
| Бутен-1
| 10,40
| 9,90
| 2,90
| 18,30
| 4,80
| 14,0
| 6,27
| Бутен-2
| 23,30
| 15,75
| 7,80
| 29,32
| 16,80
| 10,0
| 7,75
| Бутадиен
| 1,50
| 14,00
| 63,10
| 32,95
| 68,80
| 32,7
| 50,08
| С5
| 0,31
| 0,63
| 0,70
| 0,50
| 0,74
| 0,5
| 0,6
|
|
|
| Вредные
| примеси
|
|
|
| Пропин
| 0,002
| 0,005
| 0,20
| 0,013
| 0,003
| 0,24
| 0,86
| Бутин-1
| 0,005
| 0,005
| 0,07
| 0,040
| -
| 0,11
| -
| Аллен
| -
| 0,003
| 0,04
| 0,015
| 0,008
| 0,17
| -
|
Метилаллен
| 0,003
| 0,025
| 0,09
| 0,09
| -
| 0,04
| -
| Циклопента-0,04 0,02 0,2 0,1 0,03 0,03 - диен
Для выделения бутадиена из различных бутадиенсодержащих фракций в промышленности используют два метода: экстрактивную ректификацию с раз-личными полярными агентами и хемосорбцию медноаммиачноацетатными рас-творами.
При экстрактивной ректификации в качестве разделяющих агентов ис-пользуют N-метилпирролидон, диметилформамид и диметилацетамид.
Хемосорбция основана на образовании комплексных соединений нена-сыщнных углеводородов (преимущественно диенов) с солями металлов пере-менной валентности. Промышленное применение для выделения бутадиена хе-мосорбцией нашел способ с использованием водноаммиачного раствора ацета-та одновалентной меди. Взаимодействие бутадиена и бутенов с медно-аммиачным раствором происходит с образованием комплексов:
(CH3COO)2Cu2(NH3)4 + C4H6 C4H6(NH3)3Cu2(CH3COO)2 + NH3.
Процесс связывания бутадиена носит характер вытеснения молекулы ам-
миака из внутренней координационной сферы центрального атома молеку-
лой углеводорода.
Технологические схемы установок хемосорбции включают три основные стадии:
- поглощение, на которой бутадиен вместе с небольшим количеством дру-гих ненасыщенных углеводородов растворяется в экстрагенте;
- обогащение, при котором бутены удаляются из раствора;
- десорбция, при которой бутадиен практически полностью отгоняется из раствора.
Обогащение бутадиена осуществляется за счет подачи части десорбиро-ванного бутадиена противотоком к насыщенному хемосорбенту, в результате чего поглощенные бутилены замещаются в комплексе на бутадиен.
Десорбция бутадиена может осуществляться за счет разрушения ком-плекса нагреванием или уменьшением парциального давления бутадиена в сис-теме путем создания вакуума или продувкой хемосорбента инертным газом или паром.
ИЗОПРЕН
Более 130 лет известно, что изопрен является основным звеном макромо-лекул натурального каучука, однако до конца 1940-х годов ни один синтетиче-ский каучук не мог по комплексу свойств заменить натуральный. Ситуация в корне изменилась после открытия К. Циглером и Дж. Натта новых каталитиче-ских систем для стереоспецифической полимеризации ненасыщенных углево-дородов. В результате усилий ученых многих стран (США, СССР, Италии и др.) были разработаны эффективные способы получения цис-1,4-полиизопрена, являющегося структурным аналогом и заменителем натурального каучука. Ми-ровые мощности по производству синтетического изопренового каучука сего-дня превышают 1,3 млн т/ год.
В промышленном масштабе освоены шесть методов получения изопрена:
- из изобутилена и формальдегида;
- дегидрированием изопентана;
- окислительным дегидрированием изопентана;
- из пропилена;
- из ацетилена и ацетона;
- жидкофазным окислением углеводородов.
Почти каждый из перечисленных методов существует в нескольких тех-нических вариантах. Одной из причин такого многообразия методов получения изопрена, в первую очередь, является возможность использования многих ви-дов сырья.
Наиболее простой вариант получения изопрена - извлечение из фракций С5 пиролиза нефти, содержащей обычно 15-20% изопрена. Эта фракция образу-ется в качестве побочного продукта при получении этилена и пропилена в ко-личествах, не превышающих 15-20% от выхода этилена. Однако для промыш-ленной реализации метода необходимо транспортировать эту фракцию с раз-личных нефтеперерабатывающих заводов, что создает определенные трудно-сти.
Изопентан и изопентены, обладающие углеводородным скелетом конеч-ного продукта, являются дефицитными продуктами в связи с тем, что они ши-роко применяются как высокооктановая добавка к качественным бензинам (не содержащим тетраэтилсвинец). Это ограничивает возможность их применения для получения изопрена.
Не нашли, что искали? Воспользуйтесь поиском по сайту:
©2015 - 2025 stydopedia.ru Все материалы защищены законодательством РФ.
|