|
А условие прочности на смятие
σсм
FtAсм
σсм ,
где Ft – срезающая сила (осевая или окружная);
i – число поверхностей среза;
Ac
Ac τc σсм
– площадь штифта при срезе;
– площадь поверхности смятия (сжатия);
= 70–80 МПа – допускаемое напряжение при срезе;
= 200–300 МПа – допускаемое напряжение при смятии.
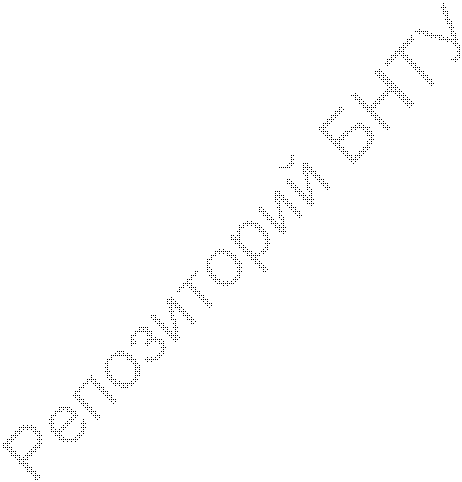

Рис. 26.15. Схемы к расчету соединений радиальным (а) и осевым (б) штифтами:
d – диаметр штифта; d1 – диаметр вала
Срезающая сила при передаче вращающего момента Ft
Осевые штифты (круглые шпонки) применяют в машинострое- нии для передачи вращающего момента в неразъемных соединениях. Штифты диаметром d = (0,1–0,15)dви длиной l = (3–4)dв (dв – диаметр вала) устанавливают по посадке с натягом Н7/r6 в отверстия, сов- местно просверленные и развернутые при сборке в валу и ступице по
стыку посадочных поверхностей (рис. 26.15, б). Материалы детали и вала должны иметь примерно одинаковую твердость для исключения увода сверла в сторону менее твердого материала.
Число штифтов для передачи заданного вращающего момента
z
Многоштифтовые соединения этого типа по прочности близки к шлицевым.
Резьбовые соединения
Резьбовыми называют соединения деталей с помощью резьбы. Они являются наиболее распространенным видом разъемных соеди- нений.
26.5.1. Крепежные детали и стопорящие устройства
Наибольшее распространение среди резьбовых деталей полу- чили крепежные болты, винты, шпильки, гайки. Под болтом или винтом понимают стержень с головкой и одним резьбовым кон- цом. Шпилька имеет два резьбовых конца. Гайка – это деталь с резьбовым отверстием.
С помощью этих деталей образуют разъемные соединения бол- том, винтом и шпилькой в разнообразных конструкциях. Тип со- единения определяется прочностью материалов соединяемых дета- лей, частотой сборки и разборки соединений в эксплуатации, а так- же особенностями конструкции и технологии изготовления со- единяемых деталей.
Для предохранения повреждений поверхностей соединяемых де- талей при завинчивании и увеличения опорной поверхности гайки используют шайбы.
При статических нагрузках самоотвинчивания резьбовых дета- лей не наблюдается, так как все крепежные резьбы выполняются самотормозящимися (явление самоотвинчивания не должно наблю- даться). При динамических и вибрационных нагрузках может про- изойти самоотвинчивание гаек и винтов.
Для предотвращения самоотвинчивания резьбовых деталей при- меняют различные средства стопорения. Основные из них – контр- гайки, пружинные шайбы, стопорные шайбы, шплинты. Если не требуется разборка соединения, гайки устанавливают внаклеп, про- изводят кернение, расклепывание и приварку.
Штифты, винты, упругие контргайки, проволока также могут выполнять функции стопорения.
Болты, винты, шпильки и гайки изготавливают из мало- и сред- неуглеродистых сталей Ст 3 кп, Ст 5, 10, 10 кп, 15, 20, 30, 45 и др. В ответственных случаях (ударные нагрузки, высокие температуры) применяют легированные стали 40Х, 38ХА, 30ХГСА, 35ХГСА, 40ХН2МА и др., а также титановые сплавы (резьбовые детали из титановых сплавов по сравнению со стальными имеют повышен- ную прочность и примерно в два раза легче).
Пружинные шайбы изготавливают из рессорно-пружинных ста- лей 65, 70, 75, 65Г.
Гайки изготавливают из стали Ст 3.
Механические характеристики материалов крепежных деталей нормированы ГОСТ 1759–82. Для стальных болтов, винтов и шпи- лек предусмотрено 12, а для гаек – семь классов прочности и соот- ветствующие им марки сталей.
26.5.2. Резьба и ее параметры
Резьба является основным элементом резьбового соединения. Она образует выступы по винтовой линии на поверхности винта и гайки (наружная и внутренняя), может изготавливаться на ци- линдрической (цилиндрическая резьба) и конической (кониче- ская резьба) поверхностях заготовки, бывает правая, если винто- вая линия направлена вверх слева направо, и левая – при направ- лении ее вверх права налево. Наиболее применяемые правые резьбы. Если на поверхность детали наносится один винтовой выступ, резьбу называют однозаходной. Применяют также мно- гозаходные резьбы.
Основные параметры цилиндрической резьбы (рис. 26.16): d, D – наружные диаметры соответственно болта и гайки; d1, D1; d2, D2 – внутренние и средние диаметры резьбы;
d3 – внутренний диаметр болта по дну впадины;
Р – шаг (расстояние между одноименными сторонами двух смежных профилей);
ψ – угол подъема резьбы, т. е. угол развертки винтовой линии по
среднему диаметру резьбы: tgψ
;
πd2
ph– ход резьбы (осевое перемещение гайки за один оборот): для однозаходной резьбы ph= p, для многозаходной ph= n ∙ p, где n – число заходов резьбы (рис. 26.17).
|
| Рис. 26.16. Метрическая резьба
| Рис. 26.17. Образование винтовой линии
|
По форме профиля крепежные резьбы бывают треугольные и круглые; резьбы винтовых механизмов (ходовые резьбы) – трапеце- идальные, упорные, прямоугольные.
Метрическая резьба (ГОСТ 24705–81) – основной вид резьбы крепежных деталей (см. рис. 26.16). Она бывает с крупным и мел- ким шагом, но чаще выполняют наиболее износостойкую и техно- логичную резьбу с крупным шагом.
Дюймовая резьба подобна метрической (α = 55°, у метрической α = 60°).
Трубные резьбы (цилиндрическая и коническая) служат для со- единения труб и арматуры.
Трапецеидальная резьба технологична, отличается высокой прочностью витков и является основной для винтовых механизмов.
Упорная резьба имеет несимметричный профиль витков и вы- полняется на винтах, воспринимающих значительную односторон- нюю нагрузку.
Прямоугольная резьба сложна в изготовлении и применяется редко.
Геометрические параметры резьб (кроме прямоугольной) и их допуски стандартизованы.
Резьбу получают методом резания, накатыванием, литьем и прессованием.
26.5.3. Силовые зависимости в резьбовом соединении
Надежность резьбового соединения оценивается легкостью сборки (легкостью затяжки гайки или болта) и сохранностью затяж- ки (самоторможением).
При завинчивании гайки надо преодолеть момент сопротивления затяжки
Т3 = Tр + Tт,
где Tр – момент сил трения в резьбе;
Тт – момент сил трения на опорном торце гайки.
Для определения Тр и Тт необходимо установить зависимость между силами, возникающими в винтовой паре при завинчивании.
Развернем среднюю винтовую линию резьбы на плоскость, а гайку представим в виде ползуна (рис. 26.18, а).
Рис. 26.18. К анализу сил в винтовой паре
При подъеме ползуна по наклонной плоскости (это соответст- вует завинчиванию гайки) сила F взаимодействия наклонной плос- кости с движущимся ползуном представляет собой равнодейству- ющую нормальной силы и силы трения. Из схемы сил, действую- щих на ползун (рис. 26.18, б),
где φ
Ft ,
– приведенный угол трения;
f – приведенный коэффициент трения в резьбе;
f – коэффициент трения.
При перемещении ползуна вниз (рис. 26.18, в)
где
Ft – окружная сила при отвинчивании гайки.
Полагая, что сила Ftсосредоточена и приложена к среднему ра- диусу резьбы 0,5d2 (см. рис. 26.19, а):
Tp .
(26.5)
Силу трения на торце гайки f1·F, зависящую от коэффициента трения f1 на торце гайки, считают сосредоточенной и приложенной к среднему радиусу опорной поверхности (рис. 26.19, а):
Tт
Dср
Момент завинчивания гайки Tз, прикладываемый к ключу:
Tз
(26.6)
Момент сопротивления затяжки Tз преодолевается моментом си- лы, приложенной к гаечному ключу (рис. 26.19, б). Приравняв оба момента, получим
Fкл
(26.7)
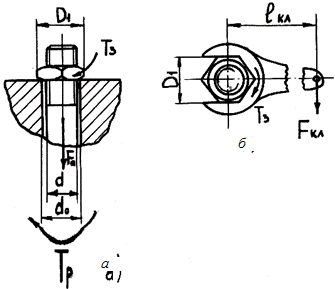
Рис. 26.19. К определению момента завинчивания
Величины, входящие в формулу (26.7), имеют определенные значения. Например, при стандартном ключе lкл 15d для метриче-
ских резьб можно принять: ψ = 2,5°;
d2 0,9d ;
Dср ;
f Из анализа формулы (26.7) следует, что обычно
Fa . Таким образом, сила в 1 H, приложенная на
конце ключа, создает силу прижатия деталей 60–100 Н. Такой вы- игрыш в силе обеспечивает легкость сборки соединения.
26.5.4. Самоторможение и коэффициент полезного действия винтовой пары
Если при опускании ползуна по наклонной плоскости (см.
рис. 26.18, в) Ft
0 или tg φ
, то резьба будет самотормо-
зящейся. Условие самоторможения:
ψ < φ.
Для крепежных резьб угол подъема резьбы ψ = 2°30'–3°30', а приведенный угол трения φ изменяется в зависимости от коэф-
фициента трения в пределах от 6° (при f ) до 11° (при
f ). Таким образом, все крепежные резьбы – самотормозящи- еся. Это объясняет важное преимущество крепежной резьбы – надежное стопорение гайки (винта) в любом положении. Однако это
свойство проявляется главным образом при статических нагрузках.
При переменных нагрузках условие самоторможения не соблюдает- ся. Поэтому необходимо стопорение резьбовых соединений.
Коэффициент полезного действия винтовой пары определяют
как отношение
, где Tз
Tз
находят по формуле (26.6), а – по той
же формуле, но без учета сил трения (f1 = 0, φ = 0). Для собственно винтовой пары (Тт = 0)
η= tgψ . tg ψ + φ
С увеличением ψ и уменьшением φ коэффициент полезного действия возрастает. Для самотормозящейся винтовой пары, где
ψ ; т. к. большинство винтовых механизмов самотор-
мозящиеся, их КПД меньше 0,5.
26.5.5. Расчет резьбовых соединений на прочность
Виды разрушения резьбовых крепежных деталей: разрыв стерж- ня по резьбе или переходному сечению у головки; повреждение или разрушение резьбы (смятие и износ, срез, изгиб); повреждение го- ловки болта (винта).
Размеры стандартных болтов, винтов и шпилек отвечают усло- вию равнопрочности всех элементов соединения. Поэтому можно ограничиваться расчетом по одному, основному критерию – проч- ности нарезной части, а размеры винтов, болтов и гаек принимать по таблицам стандарта в зависимости от рассчитанного диаметра резьбы. Длину болта, винта и шпильки выбирают в зависимости от толщины соединяемых деталей.
Рассмотрим расчет на прочность резьбовых соединений при по- стоянной нагрузке.
Болт нагружен внешней силой F (болт без предварительной за- тяжки), например, нарезанный участок крюка для подвешивания груза. Опасным является сечение крюка, ослабленное нарезкой (рис. 26.20). Из условия прочности на растяжение
σp (26.8)
откуда
d3 (26.9)
где
= 0,6
– допускаемое напряжение при рас-
тяжении болта из углеродистой стали.
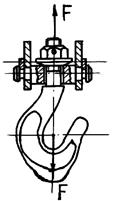
Рис. 26.20. Крюковая подвеска
Болт затянут силой затяжки Fз, а внешняя нагрузка отсутствует (ненагруженные крышки, кронштейны и т. п.). Стержень болта ис- пытывает совместное действие растяжения и кручения, т. е. растя- гивается осевой силой Fз от затяжки болта и скручивается момен- том, равным моменту сил трения в резьбе Tp(формула (26.5)), Прочность таких болтов (рис. 26.21) определяют по эквивалентному напряжению
где σp
σэ
– напряжение от растяжения, определяемое по форму-
ле (26.8) при F = Fз;
τк – напряжение от кручения:
τ
к
S – требуемый коэффициент запаса прочности болта, прини-
маемый в зависимости от материала болта, характера нагрузки и диаметра болта.
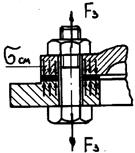
Рис. 26.21. К расчету болта, нагруженного только силой затяжки
Для стандартных метрических резьб σэ
, т. е. расчет бол-
та на совместное действие растяжения и кручения можно заменить расчетом на растяжение, но по увеличенной в 1,3 раза силе Fр. Для метрических резьб
Fр .
Расчетный диаметр резьбы болта определяют по формуле (26.9), принимая
F = Fр.
Болтовое соединение нагружено силами, сдвигающими детали в стыке. Условием надежности соединения является отсутствие сдви- га деталей в стыке.
В соединении с зазором (рис. 26.22, а) болт устанавливают с предварительной затяжкой. Внешняя сила F непосредственно на болт не передается, поэтому его рассчитывают на растяжение по силе затяжки Fз.
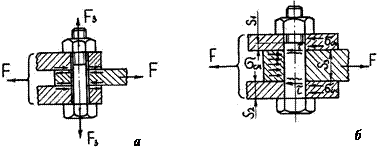
Рис. 26.22. К расчету болта, нагруженного поперечной силой:
а – поставленного с зазором; б – без зазора
Во избежание сдвига деталей при наличии зазора сила трения на поверхностях стыка должна быть не меньше внешней сдвигающей силы F:
F
где i – число стыков в соединении;
f – коэффициент трения;
K – коэффициент запаса (K = 1,3–1,5 при статической и K =
= 1,8–2,0 при переменной нагрузке);
z – число болтов в соединении.
Болт в этом случае рассчитывают по силе затяжки:
dз
При установке болта без зазора (рис. 26.22, б) предварительная затяжка не требуется. Болт испытывает срез и смятие. Стержень болта рассчитывают на срез, а при тонких деталях – и на смятие. Условия прочности
τ
σсм
где τ, τ – соответственно расчетное и допускаемое напряжения для материала болта на срез, τ = (0,2–0,3) σт;
do – диаметр ненарезанной части болта;
σсм , σсм
– соответственно расчетное и наименьшее допуска-
емое напряжения смятия (для материала болта или детали), (0,8–1,0) σт;
S – наименьшая толщина детали.
σсм =
Болт затянут, а внешняя нагрузка стремится раскрыть стык (бол- ты для крепления крышек резервуаров для газа и жидкости, на- груженные давлением выше атмосферного, крепления цилиндров, насосов, станин к фундаментам и др.). Затяжка болтов должна обес- печить герметичность соединения или нераскрытие стыка (не допу- стить появления зазора) под нагрузкой. Эта задача решается с уче- том деформации деталей соединения.
Внешняя нагрузка F
(R – равнодействующая нагрузки; z –
z
число болтов) вызывает удлинение болта на Δδ (рис. 26.23), а де- формация деталей уменьшается на ту же величину. Нагрузка со стороны деталей на болт также уменьшится. Именно поэтому счи-
тают, что болт воспринимает часть внешней нагрузки χ .
а б
Рис. 26.23. К расчету затянутого болта
с учетом деформации и соединенных деталей
Суммарная нагрузка на затянутый болт
Fδ
(26.10)
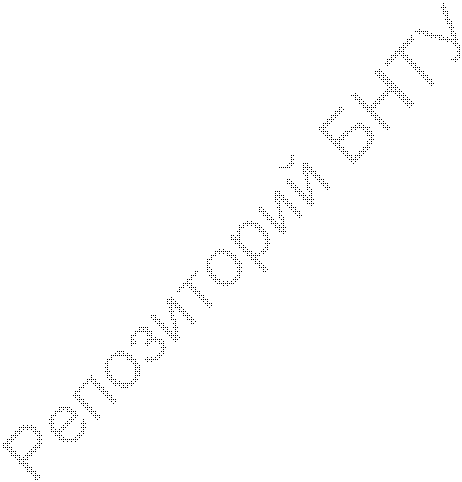
где χ – коэффициент внешней нагрузки, показывающий, какая часть внешней нагрузки воспринимается болтом (учитывает подат- ливость болта и соединяемых деталей).
Величина χ – определяется по условию равенства дополнитель- ных деформаций болта и деталей:
χF (26.11)
где
λб , λд – коэффициенты податливости соответственно болта и
деталей, численно равные изменению их длины при действии силы, равной 1 H.
Из равенства (26.11) следует, что
χ = λд . λб + λд
Точный расчет коэффициента χ сложен, а так как на практике величину затяжки болтов в большинстве случаев не контролируют, то смысл точного расчета теряется.
При приближенных расчетах принимают:
– для соединений стальных и чугунных деталей без упругих про- кладок χ = 0,2–0,3;
– для соединения тех же деталей, но с упругими прокладками (резина, полиэтилен, асбест, паронит и др.) χ = 0,4–0,5.
Предварительная затяжка болта Fз должна быть больше мини- мальной силы предварительной затяжки болта:
Fз min .
Из условия сохранения плотности стыка соединяемых деталей (невозможности образования зазора) принимают
Fз
где Kз – коэффициент запаса предварительной затяжки: при посто- янной нагрузке Kз = 1,25–2,0; при переменной Kз = 2,5–4.
При расчете на прочность, если возможна последующая затяж- ка болта, его рассчитывают по расчетной нагрузке Fр с учетом кручения:
Fh (26.12)
26.5.6. Расчет резьбовых соединений при переменном режиме нагружения
Крепежные детали, работающие при переменном режиме нагру- жения, рассчитывают на усталость. Болты устанавливаются с пред- варительной затяжкой, при которой создается напряжение
σз . Вследствие этого циклическое изменение рас-
четной силы Fб значительно меньше по сравнению с изменением внешней силы F.
Расчет на усталость ведут как проверочный по двум коэффициен- там запаса прочности: по амплитуде цикла и по наибольшему напря- жению цикла (рис. 26.24). Предварительно болт рассчитывают из условия его статической прочности с учетом формул (26.10) или (26.12).
Рис. 26.24. Циклы переменных напряжений
Коэффициент запаса прочности по амплитуде цикла
S
a
где σ 1 – предел выносливости материала болта (шпильки);
σa – амплитуда переменных напряжений:
σ
a
Sa – требуемый коэффициент запаса прочности по амплитуде
Sa = 2,5–4,0.
Коэффициент запаса по наибольшему напряжению цикла
S
где
Sa = 1,25–2,5.
При
Sa ≥
Sa и S ≥ [S] болт удовлетворяет условию проч-
ности при действии переменных напряжений.
За счет уменьшения коэффициента внешней нагрузки может быть повышена прочность резьбового соединения при переменных нагрузках. Это может быть достигнуто уменьшением податливости стыка и увеличением податливости болта, в частности, диаметр стержня болта уменьшают до диаметра d3.
ЛИТЕРАТУРА
1. Аркуша, А.И. Руководство к решению задач по теоретиче- ской механике / А.И. Аркуша. – М.: Высш. школа, 1989; 1990; 1999.
2. Артоболевский, И.И. Теория механизмов и машин / И.И. Артоболевский. – М.: Машиностроение, 1975. – 639 с.
3. Артоболевский, И.И. Сборник задач по теории механизмов и машин / И.И. Артоболевский, Б.В. Эдельштейн. – М.: Маши- ностроение, 1975. – 256 с.
4. Беляев, Н.М. Сопротивление материалов / Н.М. Беляев. – М.: Наука, 1976. – 608 с.
5. Гернет, М.М. Курс теоретической механики / М.М. Гернет. – М.: Высшая школа, 1970.– 440 с.
6. Дубейковский, Е.Н. Сопротивление материалов: учебное по- собие для машиностроительных специальностей технику- мов / Е.Н. Дубейковский, Е.С. Савушкин. – М.: Высшая шко- ла, 1985. –192 с.
7. Иосилевич, Г.Б. Прикладная механика: учеб. для вузов / Г.Б. Иосилевич, Г.Б. Строганов, Г.С. Маслов; под ред. Г.Б. Иоси- левича. – М.: Высшая школа, 1989. – 360 с.
8. Ицкович, Г.М. Сборник задач по сопротивлению материалов: учебное пособие / Г.М. Ицкович, А.И. Винокуров, Н.В. Ба- рановский. – 4-е изд. – Л.: Судостроение, 1972.
9. Каленик, В.В. Текст лекций по разделу «Теория механизмов и машин» курса «Прикладная механика» для студентов немеха- нических специальностей / В.В. Каленик, В.К. Акулич. – Минск: БПИ, 1983.
10. Кильчевский, Н.А. Основы теоретической механики / Н.А. Киль- чевский, Н.И. Ремизова, Н.Н. Шепелевская. – Киев: Технiка, 1968. – 260 с.
11. Кинасошвили, Р.С. Сопротивление материалов / Р.С. Кина- сошвили. – М.: Главная редакция физико-математической литературы изд-ва «Наука», 1975. – 384 с.
12. Методические указания по решению задач по курсу «При- кладная механика» для студентов немеханических специаль- ностей: в 2 ч. / А.А. Миклашевич [и др.]. – Минск: БПИ, 1985. – Ч 2. – 37 с.
13. Мовкин, М.С. Теоретическая механика / М.С. Мовкин, А.Б. Из- раелит. – Л.: Судостроение, 1972.
14. Никитин, Е.М. Теоретическая механика для техникумов / Е.М. Никитин. – М.: Наука, 1971 (и последующие издания).
15. Осадчий, В. И. Руководство к решению задач по теоретиче- ской механике / В.И. Осадчий, А.М. Фаин. – М.: Высш. шко- ла, 1972.
16. Павловский, М.А. Теоретическая механика: в 2 ч. / М.А. Пав- ловский, Л.Ю. Акинфеева, О.Ф. Бойчук. – Киев: Вища шко- ла, 1989; 1990. – 350 с.
17. Подскребко, М.Д. Задания по расчетно-графическим работам курса «Прикладная механика»: в 2 ч. / М.Д. Подскребко,
С.С. Томило, А.Н. Шинкевич. – Минск: БИМСХ, 1990. – Ч. 1. – 59 с.
18. Пособие к решению задач по сопротивлению материалов: учеб. пособие для техн. вузов / И.М. Миролюбов [и др.]. – 5-е изд., перераб. и доп. – М.: Высшая школа, 1985. – 399 с.
19. Прикладная механика: методические указания и контрольные задания для студентов-заочников / под ред. П.Г. Гузенкова. – М.: Машиностроение, 1982. – 112 с.
20. Прикладная механика: учеб. пособие/ А.Т. Скойбеда [и др.]; под общ. ред. А.Т. Скойбеды. – Минск: Вышэйшая школа, 1997. – 552 с.
21. Руденок, Е.Н. Техническая механика: сб. заданий: учеб. по- собие / Е.Н. Руденок, В.П. Соколовская. – Минск: Высшая школа, 1990. – 238 с.
22. Сборник задач по сопротивлению материалов / под ред. В.К. Качурина. – М.: Наука, 1970. – 432 с.
23. Сборник задач по технической механике / В.В. Багреёв [и др.]. – Л.: Судостроение, 1968.
24. Соколов, Б.Ф. Методические указания к семестровым задани- ям по объединенному курсу «Теоретическая и прикладная ме- ханика» / Б.Ф. Соколов [и др.]. – Челябинск: Челябинский ин-т механизации и электрификации сельского хозяйства, 1985.
25. Феодосьев, В.И. Сопротивление материалов / В.И. Фе- одосьев. – М.: Наука, 1986. – 512 с.
26. Феодосьев, В. И. Избранные задачи и вопросы по сопротив- лению материалов / В.И. Феодосьев. – 4-е изд., испр. и доп. – М.: Главная редакция физико-математической литературы изд-ва «Наука», 1973. – 400 с.
27. Шапиро, Д.М. Сборник задач по сопротивлению материалов: учебное пособие для машиностроительных техникумов / Д.М. Шапиро, А.И. Подорванова, А.Н. Миронов. – 3-е изд., перераб. – М.: Высшая школа, 1970.
28. Юдин, В.А. Теория механизмов и машин / В.А. Юдин, Л.В. Петрокас. – М.: Машиностроение, 1977. – 527 с.
29. Яблонский, А.А. Курс теоретической механики: в 2 ч. / А.А. Яблонский. – 7-е изд., стереотип. – СПб.: Лань, 1999. – Ч. 1: Статика, кинематика.
ПРИЛОЖЕНИЕ СОРТАМЕНТ ПРОКАТНОЙ СТАЛИ
П1. Сталь горячекатаная. Балки двутавровые. ГОСТ 8239–89.
Обозначения:
h – высота двутавра;
b – ширина полки;
s – толщина стенки;
t – средняя толщина полки;
R – радиус внутреннего скругления;
r – радиус скругления полки.
| | |
Номер двутавра
| Размеры
| Площадь попе- речного сечения, см2
|
Масса 1 м, кг
| Справочные значения для осей
| h
| b
| s
| t
| R
| r
| X – X
| Y – Y
| не более
| Iх, см4
| Wх, см3
|
iх, см
| Sх, см3
| Iу, см4
| Wу, см3
| iу, см
| мм
|
|
|
| 4,5
| 7,2
| 7,0
| 2,5
| 12,0
| 9,46
|
| 39,7
| 4,06
| 23,0
| 17,9
| 6,49
| 1,22
|
|
|
| 4,8
| 7,3
| 7,5
| 3,0
| 14,7
| 11,50
|
| 58,4
| 4,88
| 33,7
| 27,9
| 8,72
| 1,38
|
|
|
| 4,9
| 7,5
| 8,0
| 3,0
| 17,4
| 13,70
|
| 81,7
| 5,73
| 46,8
| 41,9
| 11,50
| 1,55
|
|
|
| 5,0
| 7,8
| 8,5
| 3,5
| 20,2
| 15,90
|
| 109,0
| 6,57
| 62,3
| 58,6
| 14,50
| 1,70
|
|
|
| 5,1
| 8,1
| 9,0
| 3,5
| 23,4
| 18,40
|
| 143,0
| 7,42
| 81,4
| 82,6
| 18,40
| 1,88
|
|
|
| 5,2
| 8,4
| 9,5
| 4,0
| 26,8
| 21,00
|
| 184,0
| 8,28
| 104,0
| 115,0
| 23,10
| 2,07
|
|
|
| 5,4
| 8,7
| 10,0
| 4,0
| 30,6
| 24,00
|
| 232,0
| 9,13
| 131,0
| 157,0
| 28,60
| 2,27
|
|
|
| 5,6
| 9,5
| 10,5
| 4,0
| 34,8
| 27,30
|
| 289,0
| 9,97
| 163,0
| 198,0
| 34,50
| 2,37
|
|
|
| 6,0
| 9,8
| 11,0
| 4,5
| 40,2
| 31,50
|
| 371,0
| 11,20
| 210,0
| 260,0
| 41,50
| 2,54
|
|
|
| 6,5
| 10,2
| 12,0
| 5,0
| 46,5
| 36,50
|
| 472,0
| 12,30
| 268,0
| 337,0
| 49,90
| 2,69
|
|
|
| 7,0
| 11,2
| 13,0
| 5,0
| 53,8
| 42,20
|
| 597,0
| 13,50
| 339,0
| 419,0
| 59,90
| 2,79
|
|
|
| 7,5
| 12,3
| 14,0
| 6,0
| 61,9
| 48,60
|
| 743,0
| 14,70
| 423,0
| 516,0
| 71,10
| 2,89
|
|
|
| 8,3
| 13,0
| 15,0
| 6,0
| 72,6
| 57,00
|
| 953,0
| 16,20
| 545,0
| 667,0
| 86,10
| 3,03
|
|
|
| 9,0
| 14,2
| 16,0
| 7,0
| 87,7
| 66,50
|
| 1231,0
| 18,10
| 708,0
| 808,0
| 101,00
| 3,09
|
|
|
| 10,0
| 15,2
| 17,0
| 7,0
| 100,0
| 78,50
|
| 1589,0
| 19,90
| 919,0
| 1043,0
| 123,00
| 3,23
|
|
|
| 11,0
| 16,5
| 18,0
| 7,0
| 118,0
| 92,60
|
| 2035,0
| 21,80
| 1181,0
| 1356,0
| 151,00
| 3,39
|
|
|
| 12,0
| 17,8
| 20,0
| 8,0
| 138,0
| 108,00
|
| 2560,0
| 23,60
| 1491,0
| 1725,0
| 182,00
| 3,54
| П2. Сталь горячекатаная. Швеллер. ГОСТ 8240–89
h – высота;
b – ширина полки; s – толщина стенки; t – толщина полки;
Обозначения:
R – радиус внутреннего скругления;
r – радиус скругления полки;
Z0 – расстояние от оси Y–Y до наружной грани стенки.
Швеллеры с уклоном внутренних граней полок
Номер швеллера
| Размеры
| Площадь попе- речного сечения, см2
|
Масса 1 м, кг
| Справочные значения для осей
|
Z0,
см
| h
| b
| s
| t
| R
| r
| X – X
| Y – Y
| не более
| Iх, см4
| Wх, см3
| iх, см
| Sх, см3
| Iy, см4
| Wy, см3
| Iy, см
| мм
|
|
|
| 4,4
| 7,0
| 6,0
| 2,5
| 6,16
| 4,84
| 22,8
| 9,1
| 1,92
| 5,59
| 5,61
| 2,75
| 0,95
| 1,16
| 6,5
|
|
| 4,4
| 7,2
| 6,0
| 2,5
| 7,51
| 5,90
| 48,6
| 15,0
| 2,54
| 9,00
| 8,70
| 3,68
| 1,08
| 1,24
|
|
|
| 4,5
| 7,4
| 6,5
| 2,5
| 8,98
| 7,05
| 89,4
| 22,4
| 3,16
| 23,30
| 12,80
| 4,75
| 1,19
| 1,31
|
|
|
| 4,5
| 7,6
| 7,0
| 3,0
| 10,90
| 8,59
| 174,0
| 34,8
| 3,99
| 20,40
| 20,40
| 6,46
| 1,37
| 1,44
|
|
|
| 4,8
| 7,8
| 7,5
| 3,0
| 13,30
| 10,40
| 304,0
| 50,6
| 4,78
| 29,60
| 31,20
| 8,52
| 1,53
| 1,54
|
|
|
| 4,9
| 8,1
| 8,0
| 3,0
| 15,60
| 12,30
| 491,0
| 70,2
| 5,60
| 40,80
| 45,40
| 11,00
| 1,70
| 1,67
|
|
|
| 5,0
| 8,4
| 8,5
| 3,5
| 18,10
| 14,20
| 747,0
| 93,4
| 6,42
| 54,10
| 63,30
| 13,80
| 1,87
| 1,80
| 16а
|
|
| 5,0
| 9,0
| 8,5
| 3,5
| 19,50
| 15,30
| 823,0
| 103,0
| 6,49
| 59,40
| 78,80
| 16,40
| 2,01
| 2,00
|
|
|
| 5,1
| 8,7
| 9,0
| 3,5
| 20,70
| 16,30
| 1090,0
| 121,0
| 7,24
| 69,80
| 86,00
| 17,00
| 2,04
| 1,94
| 18а
|
|
| 5,1
| 9,3
| 9,0
| 3,5
| 22,20
| 17,40
| 1190,0
| 132,0
| 7,32
| 76,10
| 105,0
| 20,00
| 2,18
| 2,13
|
|
|
| 5,2
| 9,0
| 9,5
| 4,0
| 23,40
| 18,40
| 1520,0
| 152,0
| 8,07
| 87,80
| 113,0
| 20,50
| 2,20
| 2,07
|
|
|
| 5,4
| 9,5
| 10,0
| 4,0
| 26,70
| 21,00
| 2110,0
| 192,0
| 8,89
| 110,00
| 151,0
| 25,10
| 2,37
| 2,21
|
|
|
| 5,6
| 10,0
| 10,5
| 4,0
| 30,60
| 24,00
| 2900,0
| 242,0
| 9,73
| 139,00
| 208,0
| 31,60
| 2,60
| 2,42
|
|
|
| 6,0
| 10,5
| 11,0
| 4,5
| 35,20
| 27,70
| 4160,0
| 308,0
| 10,90
| 178,00
| 262,0
| 37,30
| 2,73
| 2,47
|
|
|
| 6,5
| 11,0
| 12,0
| 5,0
| 40,50
| 31,80
| 5810,0
| 387,0
| 12,00
| 224,00
| 327,0
| 43,60
| 2,84
| 2,52
|
|
|
| 7,0
| 11,7
| 13,0
| 5,0
| 46,50
| 36,50
| 7980,0
| 484,0
| 13,10
| 281,00
| 410,0
| 51,80
| 2,97
| 2,59
|
|
|
| 7,5
| 12,6
| 14,0
| 6,0
| 53,40
| 41,90
| 10820,0
| 601,0
| 14,20
| 350,00
| 513,0
| 61,70
| 3,10
| 2,68
|
|
|
| 8,0
| 13,5
| 15,0
| 6,0
| 61,50
| 48,30
| 15220,0
| 761,0
| 15,70
| 444,00
| 642,0
| 73,40
| 3,23
| 2,75
|
| | |
Швеллеры с параллельными гранями полок
Не нашли, что искали? Воспользуйтесь поиском по сайту:
©2015 - 2024 stydopedia.ru Все материалы защищены законодательством РФ.
|