Соединения типа «вал–ступица». Общая характеристика и особенности расчета
Для передачи вращения от вала к ступице зубчатого колеса, шкива, звездочки и других соосных деталей широко используют различные соединения зацеплением. В соединениях зацеплением (шпоночных, шлицевых и др.) передача нагрузки осуществляется за счет силового замыкания деталей через шпонки, зубья и другие подобные детали. Благодаря этому соединения являются разъ- емными, осуществляют фиксацию деталей в окружном направле- нии и допускают осевое взаимное смещение деталей в процессе работы. Однако трудоемкость изготовления таких соединений до- вольно высокая.
255
26.4.1. Шпоночные соединения
Соединение двух соосных цилиндрических деталей (вала и сту- пицы) для передачи вращения между ними осуществляется с помо- щью шпонки 1 – специальной детали, закладываемой в пазы со- единяемых вала 2 и ступицы 3 (рис. 26.12).
Рис. 26.12. Соединение призматической шпонкой
В машиностроении применяют ненапряженные (без нагрузки) соединения (с помощью призматических и сегментных шпонок) и напряженные (с помощью клиновых шпонок). Шпонки этих типов стандартизованы, их размеры выбирают по ГОСТ 23360–78, ГОСТ 24071–80 и ГОСТ 24068–80.
Основные достоинства соединений: простота конструкции и воз– можность жесткой фиксации насаживаемой детали в окружном направлении.
Однако соединения трудоемки в изготовлении, требуют ручной пригонки или подбора. Это ограничивает использование со- единений в машинах крупносерийного и массового производства. Не рекомендуется применение соединений для быстро вращающих- ся валов ответственного назначения из-за сложности обеспечения концентричной посадки сопрягаемых деталей.
Основным для соединений призматическими шпонками является условный расчет на смятие (упругопластическое сжатие в зоне контакта).
Если принять для упрощения, что напряжения в зоне контакта рас- пределены равномерно и плечо равнодействующей этих напряжений равно 0,5d (где d – диаметр вала), то средние контактные напряжения (напряжения смятия, вызывающие смятие рабочих граней)
σсм
(26.4)
где T – вращающий момент;
lp – рабочая длина шпонки (см. рис. 26.12);
t2 = 0,4h – глубина врезания шпонки в ступицу;
σсм
– допускаемое напряжение на смятие.
На практике сечение шпонки подбирают по ГОСТ 23360–78 в зависимости от диаметра вала, а длину l шпонки назначают на 5– 10 мм меньше длины ступицы. Затем по формуле (26.4) оценивают прочность соединения на смятие или вычисляют предельный мо-
мент, соответствующий напряжению
σсм .
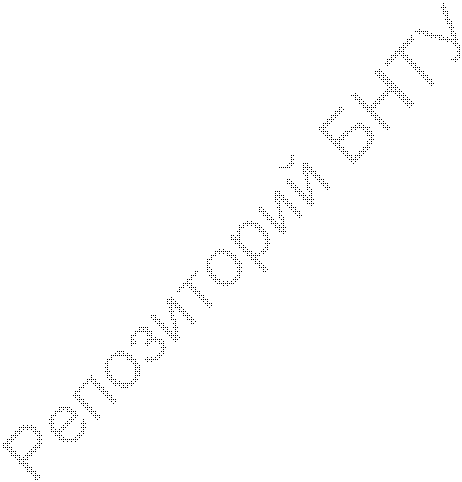
26.4.2. Шлицевые соединения
Общие сведения.Шлицевое соединение условно можно рас- сматривать как многошпоночное, у которого шпонки выполнены как одно целое с валом. По сравнению со шпоночными соединени- ями они имеют меньшие радиальные габариты, высокую несущую способность, взаимозаменяемы и обеспечивают хорошее центриро- вание деталей. Эти преимущества позволяют использовать соеди- нения в условиях массового производства конструкций и при боль- шей частоте вращения валов (рис. 26.14).
По форме поперечного сечения различают три типа соединений: прямобочные ГОСТ 1139–80; эвольвентные ГОСТ 6033–80; тре- угольные (изготовляются по отраслевым стандартам).
Проектирование и расчет соединений.Основные размеры (на- ружный диаметр D и длину l) шлицевого соединения задают при конструировании вала. Длину соединения принимают не более 1,5D; при большей длине существенно возрастают неравномерность распределения нагрузки вдоль зубьев и трудоемкость изготовления.

Рис. 26.13. Расчетная схема зуба шлицевого соединения
Учитывая, что соединения в машинах выходят из строя преиму- щественно из-за повреждения рабочих поверхностей зубьев (смя- тие, износ) и усталостного разрушения шлицевых валов, после про- ектирования выполняют проверочный расчет зубьев.
Условие прочности по допускаемым напряжениям смятия имеет вид
σсм
где dm – средний диаметр соединения;
z – число зубьев;
h и l– соответственно высота и длина поверхности контакта зубьев;
ψ – коэффициент, учитывающий неравномерное распределение нагрузки между зубьями и вдоль зубьев (ψ = 0,5–0,7);
стях.
σсм
– допускаемое напряжение смятия на боковых поверхно-
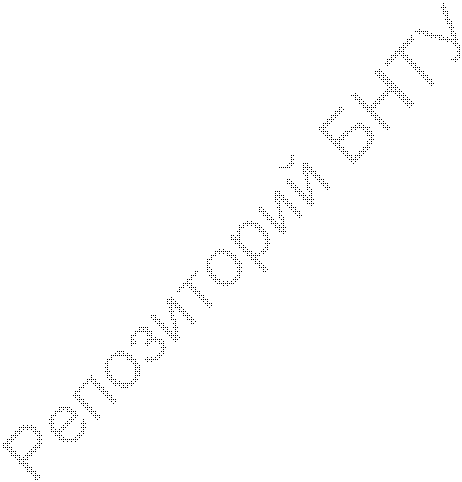
26.4.3. Профильные соединения
Общие сведения. Профильными называют соединения, в кото- рых ступица (втулка) насаживается на фасонную поверхность вала и таким образом обеспечивается жесткое фиксирование деталей в окружном направлении и передача вращения (рис. 26.14).

Рис. 26.14. Профильное соединение
Профильные соединения рассчитывают на смятие. Условие прочности по допускаемым напряжениям для соединения
σ
см
где l – длина соединения, обычно l = (1–2)d;
b – ширина прямолинейной части грани;
σсм
– допускаемое напряжение смятия, для термообработан-
ных поверхностей
σсм
= 100–140 МПа.
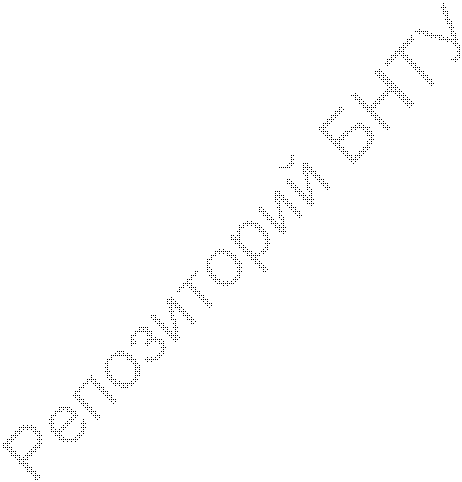
26.4.4. Штифтовые соединения
Штифтовые соединения применяют при небольших нагрузках, преимущественно в приборостроении.
Основные типы штифтов стандартизованы. Их изготовляют из углеродистых сталей 30, 45, 50 и др.
Штифтовое соединение работает на срез и смятие. Для расчета соединения используют те же зависимости. Условие прочности при срезе радиального штифта(рис. 26.15)
τ
Не нашли, что искали? Воспользуйтесь поиском по сайту:
©2015 - 2024 stydopedia.ru Все материалы защищены законодательством РФ.
|