ПРОЦЕССЫ ПЕРЕРАБОТКИ УГЛЯ И ГАЗА
ГАЗИФИКАЦИЯ УГЛЯ
Газификация угля представляет собой процесс превращения каменного или бурого угля с помощью газифицирующих агентов в смесь газов: оксида и диоксида углерода, водорода, метана, водяного пара и азота. В качестве га-зифицирующих агентов обычно используют воздух, кислород, водяной пар, диоксид углерода и водород, а также смеси этих веществ.
Образующийся при газификации угля метан применяется как замени-тель природного газа, а смесь СО и Н2 (синтез-газ) с разным соотношением компонентов используется во многих последующих синтезах. Основными реакциями при газификации являются реакции неполного окисления углеро-да органической массы:
С + 0,5О2 СО,
С + СО2 2 СО,
С + Н2О СО + Н2.
Эти реакции описывают гетерогенные превращения угля с образовани-ем газообразных продуктов. Следует учитывать, что первичные продукты га-зификации, например СО2, могут реагировать с углеродом угля. Из твердого топлива также получают продукты его термического разложения: диоксид углерода, воду, водород и продукты полукоксования (углеводороды), кото-рые в свою очередь могут взаимодействовать с раскаленным углеродом.
Наряду с описанными реакциями происходят вторичные превращения :
С + 2 Н2О СН4 + О2,
С + О2 СО2,
СО + Н2О СО2 + Н2 ,
СО + 3Н2 СН4 + Н2О.
Реакции газификации протекают со скоростью, приемлемой для техни-ческих целей, только при таких высоких температурах, при которых образо-вание высших углеводородов практически исключается. Серу, находящуюся в твердом топливе в связанном состоянии и являющуюся нежелательной примесью, переводят в сероводород и сероуглерод.
Основные газифицирующие агенты, состав образующихся продуктов, а также возможное применение полученных газовых смесей приведены на схеме 2.1.
Схема 2.1
Газификация воз-Газификация Газификация кисло-
Газификация
духом и паром под кислородом родом и паром под
воздухом
и паром давлением и паром давлением
Горючий (гене-Горючий газ Синтез-газ, Бы-Газ- заме-
раторный) газ (CO, H2, N2, CH4)газ-восста-товой газ нитель при-
(CO, H2, N2, новитель (H2, СH4, родного
небольшие (CO, H2, N2)возможны газа (СH4,
количества CH4)N2 и CO2) возможны
N2 и CO2)
Для различных Для энергетиче-Синтез NH3 Бытовое
промышленных ских предприя- и CH3OH, синтез газоснабжение
предприятий тий (предвари-Фишера-Тропша,
тельно газ оксосинтез, вос-
направляют в становление руд
турбины)
Газификация угля является процессом эндотермическим. По способу подвода тепла различают процессы автотермические, при которых тепло, не-обходимое для газификации, получают путем сжигания части введенного то-плива в присутствии кислородсодержащих газифицирующих агентов, и алло-термические, при которых требуемое тепло подводится извне с помощью твердого или газообразного теплоносителя.
Первые процессы газификации угля, разработка которых была начата в США в 1950-х годах, предназначались в основном для получения газа, спо-собного заменить природный газ. В связи с этим первичный сырой газ дол-жен был содержать возможно больше метана и не содержать нежелательные продукты полукоксования угля: масла, смолы, фенолы. Для производства синтез-газа, используемого в производстве аммиака и метанола, в оксосинте-зе или в синтезе Фишера-Тропша, напротив, необходимо поддерживать оп-ределенные соотношения СО:Н2 и Н2:N2, что достигается не только подбором условий процесса, но и выбором состава газифицирующего агента: он в ос-новном должен состоять из кислорода и водяного пара.
Другая важная характеристика процесса - температура газификации. Она зависит от состава газифицируемого сырья, типа реактора и других па-раметров. Ниже представлена блок-схема производства синтез-газа (схема 2.2).
Схема 2.2
топлива (камен-Жидкие углеводородные Газообразные углево-
Твердые
ный уголь , бурый уголь, топлива дородные топлива
кокс, дрова)
Пар, О2, О2 + пар Газификация или частичное окисление с получением
или воздух + пар смеси H2 + CO (возможны примеси CO2, CH4 и N2)
Очистка от смолы, пыли и сернистых соединений
Конверсия CH4 (CH4 + H2O CO + 3H2),
Конверсия CO (CO + H2O CO2 + H2),
Отмывка от CO2
CO + H2
Тонкая очистка от СО
H2 (+N2)
В основу классификации способов газификации могут быть поло-
жены различные принципы. По состоянию топлива в газогенераторе раз-
личают способ газификации в неподвижном слое или в медленно опус-
кающемся слое твердого топлива, газификацию в "кипящем слое", гази-
фикацию в потоке пылевидного топлива. Другая классификации основана
на различии способов подвода тепла к реактору газификации. По этой
классификации различают процессы автотермические и аллотермические.
Важной характеристикой этих способов является также размер частиц угля. Если перерабатывают мелкозернистый или пылевидный уголь, процес-сы систематизируют по принципу организации потока. Такие угли газифици-руют при подаче в одном направлении и угля, и газообразного газифици-рующего агента. Это техническое решение имеет ряд преимуществ по срав-нению с процессами газификации в неподвижном слое:
- более низкую стоимость мелкозернистого топлива по сравнению с кусковым;
- возможность применения сырья любой степени газификации, прежде всего любой спекаемости;
- отсутствие побочных продуктов - смолы, масла, фенолов и др.
Если газификацию проводят при повышенном давлении, значение этих факторов еще более возрастает, так как производительность генератора уве-личивается пропорционально давлению.
Автотермические процессы
Автотермические способы газификации, широко используемые в про-мышленности, проводятся в стационарном и "кипящем слое", в потоке пыле-видного топлива.
Газификация кускового топлива в стационарном слое является самым старым способом производства газа: смесь воздуха и водяного пара в качест-ве газифицирующего агента применили впервые примерно 150 лет назад.
Газификацию, как правило, проводят в цилиндрической шахте, обору-дованной вращающейся решеткой. В этом случае топливо, подаваемое свер-ху, газифицируется газообразным агентом, поступающим к нему противото-ком. Уголь сначала подсушивают и затем газифицируют при температуре свыше 1273 К. Золу удаляют снизу с помощью вращающейся решетки. Если в качестве газифицирующего агента применяют кислород и водяной пар, можно установить такую температуру, при которой зола удаляется в жидком состоянии.
На рис. 2.3 представлены газогенераторы трех различных типов для газификации угля в стационарном слое. Агрегаты различаются конструкцией отдельных узлов, например решетки, систем шлюзования угля и распределе-ния угля по сечению.
Генераторы с вращающейся решеткой (рис. 2.3, а, б) благодаря про-стейшей конструкции наиболее пригодны для газификации кокса. Обычно промышленные генераторы имеют диаметр до 5 м при высоте слоя топлива 1,3-1,8 м. В непрерывном производстве при использовании воздуха, обога-щенного кислородом, и водяного пара, получают низкокалорийный газ (теп-
лотворная способность 5,2 кДж/м) следующего состава (в % (об.)):
СО ………………27,8
| СО2 …………… 3,6
| Н2………………..12,4
| N2 ……………… 56,О
| Генераторы с жидким шлакоудалением (рис. 2.3, в) не имеют решеток. Шахта цилиндрической формы к низу переходит в конус и оканчивается ци-линдрической частью, в которой и собирается жидкий шлак. Обычно в каче-стве сырья используют кокс. Смесь водяного пара и кислорода или осушен-ного воздуха, которую применяют в качестве газифицирующего агента, предварительно перемешивают и с помощью форсунок, равномерно распре-деленных по окружности, вводят поверх слоя шлака. Шлак периодически удаляют через выпускное отверстие. Температура выходящего газа (если в процессе используют смесь кислорода и водяного пара) составляет 623-673 К. Производительность процесса при газификации доменного кокса кислоро-
дом - ~ 15000 м/ч, теплотворная способность 11,8 МДж/м. Газ имеет сле-дующий состав (в % (об.)):
СО………….. 64,6 СО2 ………….. 5,7
Н2 …………… 28,7 N2 …………… 1,0
Расход кислорода в газогенераторе составляет 0,25 м/м неочищенного
синтез-газа, а расход пара - 0,3 кг/м.

а бв
Рис. 2.3. Газогенераторы с вращающейся решеткой (а, б) и жидким шлакоудале-
Нием (в)
а - 1 - водяная охлаждающая рубашка; 2 - вращающаяся решетка; 3 - чаша
для золы;
б - 1 - шлюз; 2 - водяная рубашка; 3 - мешалка, охлаждаемая водой; 4 - вра-
щающаяся решетка; 5 - чаша для золы
В промышленности реализован также процесс газификации угля сме-сью кислорода и водяных паров под давлением при удалении золы в твердом состоянии. Газификацию осуществляют при давлении 3 МПа парокислород-ной смесью, подаваемой в реактор через вращающуюся колосниковую ре-шетку. Частицы угля размером преимущественно 5-30 мм загружают через шлюзовую емкость в генератор, в котором уголь с помощью распределителя насыпается равномерно по всему сечению шахты.
Широкое применение в промышленности нашли также газогенераторы со стационарным слоем и жидким шлакоудалением. Такие реактора разрабо-тали немецкая фирма Лурги" (рис. 2.4) и позднее английская фирма "Газ
"
Коунсил"(рис. 2.5). Протекающие в верхней части реактора реакции анало-
гичны газификации под давлением с сухим удалением золы. Поэтому на ри-сунке 2.5 изображена только нижняя часть генератора.
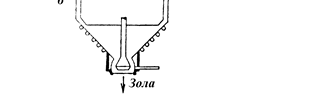
Рис. 2.4. Генератор для газификации угля в стационарном
слое под давлением по способу "Лурги"
1 - шлюзовая емкость для угля; 2 - привод питателя; 3 - ре-
шетка; 4 - привод решетки; 5 - водяная рубашка; 6 - шлюзо-
вая емкость для золы; 7 - скруббер-холодильник; 8 - зона сушки;
9 - зона термического разложения; 10 - зона газификации; 11- зона
горения
В этом случае газифицирующим агентом является кислород со столь небольшим количеством пара, что зола остается жидкой. Жидкий шлак соби-рается в днище ванны газогенератора и находится там до момента поворота кислородно-газовой горелки в сторону отверстия в днище ванны. При этом давление понижается и шлак переходит в "закалочную" камеру, в которой осуществляется его гранулирование в воде. Гранулы периодически выгру-жают через шлюзовую емкость, работающую под давлением.
Этот способ эффективен для получения синтез-газа, причем соотноше-ние СО:Н2 в газе можно изменять в широком интервале. Процесс осуществ-ляют при давлении свыше 2,0 МПа.
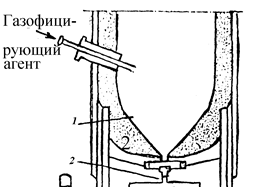
Рис. 2.5. Газогенератор под давле-
Не нашли, что искали? Воспользуйтесь поиском по сайту:
©2015 - 2025 stydopedia.ru Все материалы защищены законодательством РФ.
|