Краткие теоретические сведения
Обжиг сульфидных руд относится к типовым процессам, применяемым в цветной металлургии в качестве первой стадии переработки концентрата цветного металла, в производстве серной кислоты и целлюлозы с целью получения двуокиси серы и т. п. Закономерности, лежащие в основе этого процесса, справедливы для обжига любого сульфидного сырья: пирита FeS2, пиротина Fe7S8, халькопирита CuFeS2, медного блеска Cu2S, цинковой обманки ZnS и т. п. Общая скорость обжига сульфидных руд, как и для многих других высокотемпературных процессов обжига, при температурах выше 600 °С лимитируется диффузионными стадиями подвода реагентов (кислорода воздуха) и отвода продукта (двуокиси серы) из зоны реакции.
Рассмотрим закономерности обжига сульфидного сырья на примере обжига колчедана – основного сырья для производства двуокиси серы, состоящего из пирита и примесей. Химические реакции, сопровождающие обжиг колчедана, можно выразить следующим суммарным уравнением, применяемым для материальных расчетов этого процесса:
4FeS2 + 11О2 = 2Fe2O3 + 8SO2 + Q . (1)
Фактически при обжиге сульфидных руд происходит целый ряд последовательных и параллельных реакций, ход которых определяется в основном температурой. Все эти реакции, как и процесс обжига в целом, протекают необратимо. При нагревании в печи выше 500 °С происходит быстрая диссоциация термодинамически неустойчивого соединения FeS2..
2FeS2 = 2FeS + S2. (2)
Выделившаяся сера быстро сгорает
S2 + 2О2 = 2SO2 (3)
Выше 600 °С окисление сульфида железа происходит по суммарному уравнению 4FeS + 7О2 = 2Fe2O3 + 4SO2 + Q(4)
через ряд стадий с последовательным образованием FeO, а затем Fe3O4 и Fe2O3. В результате каталитического действия окислов железа в печи образуется небольшое количество серного ангидрида SO3 за счет окисления двуокиси серы.
Окисление сульфида железа FeS лимитирует общую скорость обжига сульфидных руд вследствие медленных диффузионных стадий, предшествующих окислению по реакции (4) и сопровождающих его. Зерна сульфида железа в процессе окисления покрываются пленкой окислов железа, затрудняющей диффузию кислорода к неокисленному ядру FeS и обратную диффузию двуокиси серы в газовую фазу.
Газ обжига колчедана содержит в зависимости от типа печи SO2 7–13 %, О2 4–11 %, SO3 до 0,5 % и азот. Твердый остаток обжига – огарок – состоит из окислов железа (Fe2O3 и Fe3O4) и содержит 0,5–2% невыгоревшей серы. Оптимальные условия обжига колчедана (а также и другого сульфидного сырья) определяются кинетикой диффузии реагентов к поверхности взаимодействия фаз и могут быть рассчитаны из общего кинетического уравнения массопередачи:
,
где – общая скорость обжига, выраженная дифференциалом количества продукта SO2 во времени; kм – коэффициент массопередачи; F – величина межфазной поверхности, равная поверхности всех частиц; DС – движущая сила обжига, зависящая от концентрации кислорода в воздухе и содержания серы в колчедане.
Увеличить движущую силу обжига DС можно обогащением сульфидного сырья многократной флотацией, например, с увеличением содержания чистого пирита (FeS2) в сырье до 90 % и выше, а также обогащением воздуха кислородом. На практике для увеличения доступа кислорода к поверхности обжигаемых частиц применяют избыток кислорода в 1,2–1,8 раза больший, чем это требуется теоретически по расчетному стехиометрическому уравнению (1).
Коэффициент массопередачи можно увеличить повышением температуры и интенсивным гидродинамическим режимом в печи, способствующим перемешиванию реагентов (частиц колчедана в потоке воздуха). Повышение температуры (ускоряющее химические реакции и диффузию) возможно лишь до оптимальной, составляющей, в зависимости от типа печи, 850–1000 °С. Дальнейший рост температуры ограничивается термической нестойкостью исходного реагента – колчедана, который легко спекается в крупные агрегаты, в результате чего резко уменьшается межфазная поверхность и нарушается работа в печи.
Для увеличения kM используют перемешивание, которое не только уменьшает диффузионные сопротивления, но и увеличивает и обновляет F – поверхность соприкосновения сульфида железа с кислородом воздуха. Для этого применяют измельченный колчедан с размером частиц 0,03–0,3 мм. Способы перемешивания частиц обжигаемого материала с воздухом определяются типом и конструкцией печи.
В настоящее время для обжига сульфидного сырья применяются три типа печей: механические полочные, пылевидного обжига ивзвешенного (кипящего) слоя (КС). Все эти печи работают автотермично, т. е. нагрев в них происходит за счет тепла реакций окисления серы и сульфидов.
В механических полочных печах обжиг измельченного материала производится в слоях, лежащих на сводах печи. Перемешивание (перегревание) и передвижение обжигаемого материала на сводах осуществляется механическими мешалками. Интенсивность этих печей (типа ВХЗ) составляет около 225 кгколчедана (45 % S) в сутки на 1 м2пода. В печах пылевидного обжига тонкоизмельченный материал распыляется в потоке воздуха, а в печах кипящего слоя – обжигаемые частицы взвешены в потоке воздуха. В печах последних двух типов достигается максимальная интенсивность обжига и наиболее высокая концентрация SO2 в печном газе (до 15 % SO2 в печах КС). При обжиге в пылевидном состоянии, и особенно во взвешенном слое, наблюдаются следующие преимущества: 1) высокая дисперсность обжигаемого материала (что резко уменьшает внутренне-диффузионные сопротивления и увеличение F); 2) турбулентное омывание всех частиц потоком воздуха; 3) возможность понижения коэффициента избытка воздуха, в результате чего повышается концентрация SO2 в газе; 4) высокая теплопроводность взвешенного слоя (тепло передается с большой скоростью конвективным движением частиц), позволяющая регулировать температуру, размещая непосредственно в слое холодильников – секций парового котла; 5) подвижность и текучесть материала во взвешенном слое, облегчающая выгрузку огарка из печи. Весь процесс обжига в печах взвешенного слоя (КС) легко регулируется и может быть полностью автоматизирован.
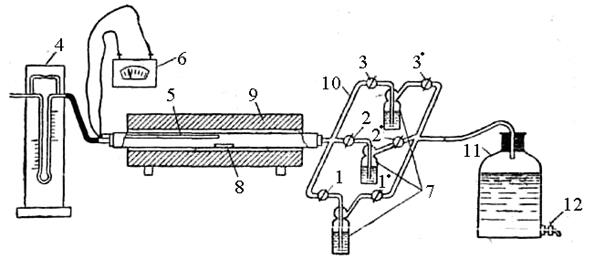
Рис. 2.6.1. Схема установки
для обжига колчедана в неподвижном слое
Основным недостатком печей КС является большой пылеунос и, следовательно, высокая запыленность печного газа (до 300 г/м3).Это сильно усложняет очистку газа от пыли.
В настоящей работе исследуется влияние режимных факторов (температуры и избытка воздуха, содержания серы в колчедане, размера частиц, типа печи) на скорость обжига, выражаемую как изменение концентрации SO2 в печном газе по времени или как производительность печи. В лабораторных установках моделируем процесс обжига колчедана в неподвижном слое в двух вариантах.
Не нашли, что искали? Воспользуйтесь поиском по сайту:
©2015 - 2025 stydopedia.ru Все материалы защищены законодательством РФ.
|