Особенности монтажа внутренних выводов БИС и СБИС
Одним из методов обеспечения в СБИС высоких скоростей ереключения, а также предотвращение деградации сигнала и перекрестных искажений, вносимых соседними выводами, является автоматизированная сборка кристаллов на гибкой ленте. Широкие выводы ленточных носителей с низким сопротивлением рассеивают тепло эффективнее, чем традиционные проволочные. В связи с этим в последние годы возрос интерес к разработке оборудования и совершенствованию технологии сборки СБИС на ленточных носителях.
Развитие поверхностного монтажа компонентов на печатные платы обусловлено уменьшением габаритов и веса радиоэлектронной аппаратуры. Поверхностный монтаж привел к необходимости разработки новых видов корпусов ИС, БИС и СБИС с большим количеством выводов. Широко используются плоские корпуса высотой 2-3 мм, имеющие сотни внешних выводов. Определяющими при выборе формы и конструкции корпуса являются размеры и технология изготовления кристалла. К конструкции корпуса предъявляются жесткие требования по надежности: хороший теплоотвод от кристалла, качественное крепление кристалла к основанию корпуса и присоединение внутренних выводов на кристалле с внешними выводами на корпусе. Различие в коэффициентах термического расширения кристалла и материала корпуса ведет к появлению механических напряжений в кристалле и корпусе, что может привести к растрескиванию кристалла, особенно у СБИС площадью до 100 мм2. БИС и СБИС с большим (до миллиона и более) количеством транзисторов, резисторов, диодов и пр. на кристалле выполняются со специальными теплоотводами.
Корпуса ИС, изготавливаемые заливкой пластмассы, не обеспечивают достаточную надежность при количестве выводов >100. Предлагается использовать силиконовый гель, который позволяет защитить кристалл от примесей (Cl-, NO3-, SO42-, Na+, NH4+, K+) и улучшить его герметизацию, что обеспечивается слиянием молекул геля и воды при термообработке.
За последние годы неуклонно уменьшается ширина линий металлизации: в новых перспективных схемах до 0,18 мкм и менее. Однако несмотря на существенное уменьшение размеров элементов и увеличение сложности схем, требования к их надежности неуклонно повышаются.
Электрические и механические характеристики металлизации должны удовлетворять следующим основным требованиям: малое электрическое сопротивление, хорошая адгезия с изоляционной поверхностью кристалла, согласованность с другими материалами, применяемыми при изготовлении схем. На этапах изготовления ИС малой и средней степени интеграции широко применялась алюминиевая металлизация, легированная кремнием. Известно, что при увеличении концентрации Si в металлизации от 0,5 до 1,1 (вес. %) удельное сопротивление Al-металлизации увеличивается более чем вдвое. Алюминиевая, а также Al с присадкой Si металлизация является неприемлемой для быстродействующих СБИС.
Добавка меди в Al-Si-металлизацию приводит к снижению интенсивности отказов. Однако при содержании Cu>0,1 % ее влияние на интенсивность отказов незначительно.
Расчетами с использованием метода конечных элементов установлено распределение механических напряжений в Al-Si-металлизации. Отмечается, что максимальные напряжения возникают при ширине линий разводки 2-3 мкм, что объясняется образованием пустот под разводкой на ступеньках SiO2. При локальных напряжениях (около 450 МПа) перетекание кластерных вакансий может приводить к образованию микропустот даже при низких температурах.
В Al-металлизации, покрытой органическим компаундом, возникают процессы коррозии, связанные с электромиграцией. Очистка поверхности ИС перед заливкой компаундом позволяет подавить данное явление. Для очистки используют следующие методы: обдув сжатым азотом под высоким давлением; плазменную обработку в атмосфере кислорода; промывку во фреоне с последующей обработкой УФ-излучением и промывкой в деионизованной воде. Коррозионные характеристики Al-металлизации, покрытой различными полимерными материалами, показали высокую эффективность очистки кристалла во фреоне и УФ (озоновой) обработкой.
С увеличением числа выводов и размеров кристалла значительно увеличиваются габариты корпусов и длина межсоединений, а вследствие этого – значения сопротивлений, индуктивностей и емкостей.
Поэтому методы сборки многовыводных СБИС в металлокерамические (пластмассовые) корпуса с помощью термокомпрессионной или ультразвуковой сварки проволочных выводов имеют ряд принципиальных ограничений дальнейшего развития. В связи с этим возникла необходимость разработки групповых способов монтажа с использованием паучковых выводов. В производстве используются следующие схемы присоединения паучковых выводов к кристаллу: ультразвуковая групповая сварка, микропайка с косвенным подогревом без инструмента и термоимпульсная микропайка.
Наиболее широкое применение в производстве нашел метод термоимпульсной микропайки (рис. 7.9).
При термоимпульсной микропайке паучковые выводы 2, закрепленные на диэлектрической пленке 3, совмещаются с шариковыми контактами 4 на кристалле 5. Инструмент 1 опускается, прижимая паучковые выводы к шариковым контактам. Через инструмент пропускается импульс тока. Тепло передается в места контакта, нагревая их до температуры пайки. Слой клеящего вещества 6, удерживающий кристаллы на подложке 7 в ориентированном положении, расплавляется, и при поднятии инструмента кристалл, припаянный к паучковым выводам, отрывается от подложки за счет силы, вызванной предварительной упругой деформацией паучковых выводов. Силы сцепления кристалла с клеящим веществом и подложкой должны быть меньше этой силы.
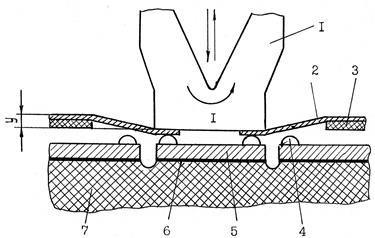
Рис. 7.9. Схема термоимпульсной микропайки: 1 – инструмент; 2 – паучковый вывод; 3 – диэлектрическая пленка; 4 – шариковый контакт; 5 – кристалл; 6 – клей; 7 – подложка
При проектировании оборудования для термоимпульсной микропайки необходимо рассчитывать оптимальные упругие деформации паучковых выводов и усилия, обусловленные этими деформациями. Знание этих величин позволит правильно выбирать материал и конструкцию паучковых выводов.
При групповом монтаже паучковых выводов к шариковым контактам кристаллов ИС из-за различных коэффициентов термического расширения выводов, кристалла и подложки в собранном узле возникают значительные термомеханические напряжения. Их величина зависит от соединяемых материалов, геометрических размеров и температуры процесса микропайки. Компенсировать термомеханические напряжения можно путем создания предварительных упругих деформаций паучковых выводов.
Для определения напряжения сдвига в направлении длины выводов получено выражение

где у – величина прогиба паучкового вывода, мм; h – толщина паучкового вывода в месте микропайки, мм; l – длина паучкового вывода от защемления до центра шарикового контакта, мм; r – радиус шарикового контакта, мм; Dх – расстояние от центра шарикового контакта до центра кристалла, мм; DТ1 и DТ2 – разность температур паучкового вывода и кристалла при микропайке и окружающей средой, ºС; a1 и a2 – коэффициенты термического расширения материалов паучкового вывода и кристалла соответственно, 1/ºС; Е – модуль упругости материала паучкового вывода, МПа.
Напряжения сдвига в зависимости от прогиба, длины и толщины выводов приведены на рис. 7.10. Для практического использования расчетов следует ввести ограничения по максимально возможным упругим деформациям. Пунктирная линия (рис. 7.10) разграничивает области упругих и пластических деформаций для толщины вывода h = 0,02 мм. При длине паучкового вывода в 1 мм снизить термомеханические напряжения до нуля за счет упругих деформаций не удается. Таким образом по данной методике можно определять оптимальную длину паучкового вывода.
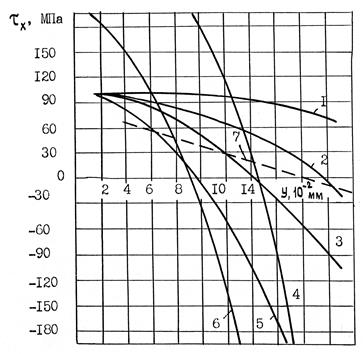
Рис. 7.10. Зависимость tх от прогиба y: 1 – при h = 0,02 мм и l = 3 мм; 2 – при h = 0,02 мм и l = 2 мм; 3 – при h = 0,02 мм и l = 1,5 мм; 4 – при h = 0,08 мм и l = 1,5 мм; 5 – при h = 0,02 мм и l = 1 мм; 6 – при h = 0,04 мм и l = 1 мм; 7 – кривая, разграничивающая области упругих и пластических деформаций для кривых 1, 2, 3 и 5 при h = 0,02 мм
Определение оптимальных размеров паучковых выводов позволит получать надежные микросоединения при групповом монтаже. На рис. 7.11 приведена номограммы для определения размеров паучковых выводов.
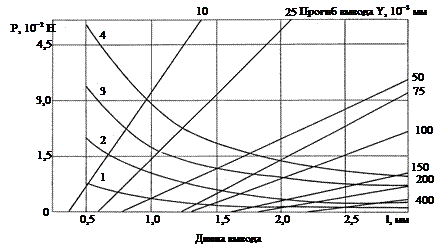
Рис. 7.11. Номограммы для определения размеров паучковых выводов при групповом монтаже ИС при b0 = 0,60 мм; 1 – h = 0,02 мм; 2 – h = 0,03 мм; 3 – h = 0,04 мм; 4 – h = 0,05 м
Одним из способов сборки БИС является монтаж кристалла на прокладке с паучковой разводкой с последующим монтажом на подложке с микропроволокой. Например, 320-выводной корпус размером 16,5´16,5 мм всего в 1,9 раза превышает размеры кристалла. Кроме того, технология монтажа с использованием паучковой прокладки позволяет уменьшать расстояние между внешними выводами до 143 мкм.
Так как монтаж осуществляется способом перевернутого кристалла, то обратная сторона кристалла может быть использована для эффективного теплоотвода. Схема монтажа кристалла показана на рис. 7.12.
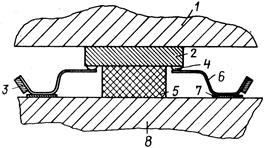
Рис. 7.12. Схема сборки БИС с использованием паучковых выводов: 1 – теплоотвод; 2 – кристалл; 3 – полиимидный несущий вывод; 4 – шариковый контакт; 5 – эластичный элемент; 6 – вывод; 7 – контактная площадка; 8 – монтажная подложка
Шариковые контакты БИС формируют методом электролитического осаждения нескольких слоев. Золотое покрытие, наносимое химическим осаждением на шариковые контакты, повышает их стойкость в процессе хранения перед монтажом кристалла. Структура столбикового электрода должна обладать стой-костью при термических операциях при монтаже кристалла. Высота шарикового контакта должна иметь размеры 18±1 мкм по всей площади кристалла.
Паучковая прокладка представляет собой трехслойную структуру из металлических проводников, наклеенных на полиимидную пленку. Разводка 320 контактных площадок кристалла БИС размером 11,54×12,67 мм2 осуществляется выводами с шагом 143 мкм, поэтому необходимо разветвление выводов для обеспечения расстояния между ними 175 мкм. Паучковая прокладка для монтажа кристаллов БИС кроме центрального квадратного окна имеет прорези с четырех сторон от центрального окна для монтажа кристалла на тестовой плате. Материалом паучковых прокладок является упругая медная лента толщиной 35 мкм, на верхнюю поверхность которой наносится пленка Sn.
Изготовители и разработчики СБИС затрачивают очень много времени и средств на разработку аппаратуры для проверки характеристик изделий. Выбор правильного направления разработки тестеров для СБИС требует не только оценок необходимости проверок, но и выбора оптимального направления проектирования СБИС. Нужно знать, какие СБИС и в каком количестве будут изготавливаться промышленностью. Испытательные установки являются экономически приемлемыми, если стоимость испытаний при серийном производстве составляет от 3 до 5 % стоимости серийных схем.
Основной трудностью анализа отказавших ППИ является вскрытие корпусов, особенно пластмассовых. Рекомендуется механический способ вскрытия пластмассовых корпусов с помощью торцовой фрезы. Фрезой получают поперечный паз на корпусе с обратной стороны до кристаллодержателя; затем удаляют кристаллодержатель; фрезеруют замкнутую по периметру кристалла канавку на глубину на 0,2 мм, превышающую толщину кристалла. После обработки в струе горячего газа при Т = 170 °С кристалл легко отделяется от пластмассы. При этом полностью сохраняется физическая картина коррозии металлизации на кристалле или на отпечатке пластмассы.
Не нашли, что искали? Воспользуйтесь поиском по сайту:
©2015 - 2025 stydopedia.ru Все материалы защищены законодательством РФ.
|