|
Выбор оптимального режима УЗС соединения Al-Ag
После пайки кристаллов присоединение алюминиевых выводов к контактным площадкам кристалла и траверсам корпуса проводят ультразвуковой сваркой.
Качество соединений определяется множеством факторов: физико-механическими свойствами проволоки и металлизации; режимами УЗС; материалом инструмента, геометрическими формой и размерами его рабочей площадки; наличием или отсутствием загрязнений на соединяемых поверхностях и т. д.
Вопросу оптимизации режимов УЗС алюминиевой проволоки с серебряной металлизацией корпусов ППИ посвящен данный раздел. Представим процесс УЗС в виде «черного ящика» (рис. 6.30). Х1, Х2, …, Хn – входные параметры, действующие в исследуемом процессе. Y – выход системы, называемый функцией отклика, является функцией входных параметров. В этом случае задача выбора оптимальных режимов УЗС заключается в следующем: найти математическую модель процесса в виде некоторой функции Y=f(Х1, Х2,…, Хn) и значения Хi, обеспечивающие экстремум (максимум) функции.
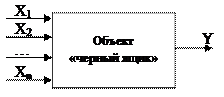
Рис. 6.30. Условное представление процесса УЗС
Необходимо получить математическую модель процесса УЗС алюминиевых проволочных выводов с серебряным гальваническим покрытием корпусных деталей СПП, с целью определения оптимальных режимов сварки.
В процессе проведения эксперимента варьировались три фактора: усилие нагружения на микросварочный инструмент (Х1), мощность УЗ генератора (Х2) и время сварки (Х3) (табл. 6.11). В качестве критерия качества, а, следовательно, функции отклика исследуемого процесса принята прочность соединений. Прочность соединений определялась натяжением вывода под углом 90º к плоскости образца до разрушения соединений с одновременным контролем характера разрушения.
Табл. 6.11. Значения уровней варьирования
Уровни варьирования
| Параметры
| Х1, сН
| Х2, дел
| Х3, мс
| Основной
Верхний
Нижний
Интервал варьирования
|
| 6,3
6,8
5,8
0,5
|
| Примечание: мощность генератора УЗ колебаний (Х2, дел.) устанавливается по числу делений регулятора мощности в установке УЗ-сварки.
Для проведения экспериментальных исследований осаждение серебра на медные пластины проводили в электролите следующего состава (г/л): AgCl – 40; K4[Fe(CN6)]3H2O – 200; K2CO3 – 20. В качестве анодов использовались пластины из чистого серебра. Режимы осаждения: Iк = 1-1,5 А/дм2, температура электролита 50 ºC, время 10 мин для толщины покрытия 6 мкм. После осаждения покрытий образцы отмывались в дистиллированной воде. Перед сваркой медные пластины с серебряным покрытием отжигались в водороде при температуре 390 ± 20 ºC с целью имитации процесса напайки кристаллов на основания корпусов. Предварительный отжиг образцов в кислороде не проводился из-за образования на поверхности серебряного покрытия оксидной пленки Ag2O толщиной 500-600 Å. Оксидная пленка Ag2O обеспечивает необходимое растекание припоя при пайке, но при сварке не способствует заданному качеству сварных соединений.
Для оценки влияния параметров УЗС на качество микросоединений алюминиевой проволоки с серебряной металлизацией использовали проволоку марки АОЦПоМ (ТУ 6365‑051‑46594157‑2004) диаметром 250 мкм. Химический состав проволоки, %: Si – 0,01; Cu – 0,01; Mg – 0,01; Mn – 0,01; Fe – 0,01; Sb ≤ 0,02; Ti – (0,003-0,08); Zn – (0,03-0,28); Al – остальное. Разварку выводов производили на установке для ультразвуковой сварки типа У-153 инструментом с треугольной канавкой на рабочем торце марки КУТ-41-250-600 (ОСТ 11 31 5001.8-92).
Для удобства обработки результатов проводится преобразование значений управляемых переменных (учитываемых в эксперименте факторов Хi) к безразмерным величинам
Хiб=(Хi-Xoi)/ΔХi,
где Хi – текущее значение i-го фактора; Xoi – базовое или начальное значение i-го фактора в центре плана; ΔХi – значение интервала варьирования по i-му фактору.
Поскольку в эксперименте используются 3 фактора, а предполагаемая математическая модель исследуемого процесса линейна, то она соответствует полиному вида
Y=b0+b1x1+b2x2+b3x3+b12x1x2+b13x1x3+b23x2x3+b123x1x2x3,
где Y – значение функции отклика; x1x2x3 – значения исследуемых факторов; b0 – значение функции отклика в центре плана; b1, b2, b3 – коэффициенты, характеризующие степень влияния факторов на функцию отклика; b12, b13, b23, b123 – коэффициенты, характеризующие взаимовлияние факторов.
При варьировании каждым из трех факторов (к = 3) на двух уровнях число опытов N будет составлять N = 2к = 23 = 8. Для каждой комбинации факторов было проведено 15 параллельных опытов (n = 15).
По известной методике составлена матрица планирования полного факторного эксперимента типа 23, представленная в табл. 6.12.
Табл. 6.12. Матрица планирования и результаты полного факторного эксперимента
Номер опыта
| Х0б
| Х1б
| Х2б
| Х3б
| Х1бХ2б
| Х1бХ3б
| Х2бХ3б
| Х1бХ2бХ3б
| Экспериментальная прочность yξ, сН
| Теоретическая прочность yξ t,
сН
|
| +
| –
| –
| –
| +
| +
| +
| –
| 321,0
| 317,71
|
| +
| +
| –
| –
| –
| –
| +
| +
| 305,4
| 311,09
|
| +
| –
| +
| –
| –
| +
| –
| +
| 286,0
| 283,91
|
| +
| +
| +
| –
| +
| –
| –
| –
| 291,0
| 290,53
|
| +
| –
| –
| +
| +
| –
| –
| +
| 291,7
| 286,27
|
| +
| +
| –
| +
| –
| +
| –
| –
| 290,0
| 292,89
|
| +
| –
| +
| +
| –
| –
| +
| –
| 265,0
| 265,71
|
| +
| +
| +
| +
| +
| +
| +
| +
| 257,4
| 259,09
|
Проведена оценка однородности дисперсий функции отклика в соответствии с критерием Кохрена, ее результаты (для N = 8 и n = 15: σmax = 0,2787 ≤ 0,29 = σкр) позволяют сделать вывод о воспроизводимости эксперимента, а отклонения значений функции отклика носят случайный характер и вызваны влиянием неконтролируемых и неуправляемых факторов.
Вычислены коэффициенты полинома по формуле
,
где bi – коэффициент полинома, соответствующий i-фактору; ξ = 1, …, N – номера опытов; xξi – значение безразмерного фактора в матрице планирования, соответствующего ξ-строке и i-столбцу; yξ – значение функции отклика в ξ-опыте.
Проверка значимости коэффициентов с помощью t-критерия Стьюдента показала, что коэффициенты b1, b12, b13, b23 признаны статистически незначимыми, поэтому соответствующие им члены полинома исключаются из уравнения математической модели процесса. Остальные коэффициенты имеют следующие значения: b2 = – 13,59; b3 = – 12,41; b123 = – 3,31; b0 = 288,4. Исключение члена полинома, соответствующего фактору х1, означает, видимо, что этот фактор, а именно, усилие инструмента в выбранном интервале его значений не оказывает влияния на функцию отклика (прочность соединений). Влияние двух других факторов примерно равнозначно. Некоторое влияние оказывает взаимодействие трех факторов.
Таким образом, математическая модель с учетом значимости коэффициентов полинома имеет вид
Y = b0+b2x2+b3x3+b123x1x2x3,
Y = 288,4 – 13,59x2 – 12,41x3 – 3,31x1x2x3.
Теоретические значения прочности соединений для каждого опыта yςt, предсказываемые математической моделью, вычислены и представлены в табл. 6.12.
Проведена проверка адекватности математической модели результатам эксперимента. По известным формулам, вычислена дисперсия адекватности S2ад = 21,45, которая не превышает дисперсию опыта S2{y} = 165, следовательно, можно сделать вывод о том, что полученная математическая модель адекватно представляет результаты эксперимента.
Полученная функция исследована на экстремум. Максимальное значение прочности соединений достигается при следующих значениях безразмерных факторов: х1опт = – 1; х2опт = – 1; х3опт = – 1. Следовательно, оптимальными параметрами процесса УЗС будут следующие значения: Qопт = 250 сН; Wопт = 5,8 дел; τопт = 50 мс. Максимальная теоретическая прочность соединений при этих значениях параметров, предсказываемая математической моделью, составляет 317,71 сH.
Прочность соединений в значительной степени зависит от механических свойств проволоки в состоянии поставки. С целью стабилизации прочности и пластичности проволоки проводят ее отжиг перед сваркой. Перед проведением исследований проволоку отжигали в вакууме при Т=210±10 ºС в течение 7 мин. После отжига проволока имела следующие свойства: σт = 31-33 МПа, σв = 69-71 МПа и твердость в пределах 210-310 МПа.
Для экспериментальной оценки качества микросоединений Al-Ag на оптимальных режимах было разварено по 50 образцов. Деформация проволоки в зоне сварки определялась под микроскопом с точностью ±2 мкм. Анализ прочности соединений показал, что разрушение происходит, в основном, на участке перехода сварного соединения в проволоку.
На рис. 6.31 представлены гистограммы деформации алюминиевой проволоки и прочности соединений алюминиевой проволоки с серебряным покрытием, сформированных на оптимальных режимах УЗС. Из рис. 6.31 видно, что соединения Al-Ag имеют стабильную прочность в пределах 320-325 сН.
Для прогнозирования надежности СПП, имеющих соединение Al-Ag, необходим анализ данной контактной пары. Известно, что диаграмма состояния Al-Ag со стороны алюминия относится к эвтектическому типу. Растворимость серебра в твердом алюминии существенно зависит от температуры:
Температура, ºC
|
|
|
|
|
|
|
|
| Растворимость, %
| 55,6
| 49,4
| 28,0
| 16,0
| 8,0
| 3,2
| 1,1
| 0,7
| Увеличение содержания серебра приводит к повышению удельного электросопротивления сплава Al-Ag:
Содержание Ag, %
| 1,97
| 3,39
| 6,58
| 10,02
| 16,8
| Удельное электросопротивление, мкОм·см
| 3,46
| 3,79
| 4,70
| 5,47
| 7,07
| 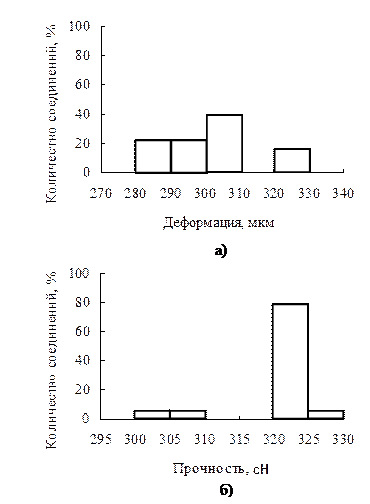
Рис. 6.31. Гистограммы распределения деформации алюминиевой проволоки (а) и прочности соединений алюминиевой проволоки с серебряным покрытием траверс корпусов (б)
Зависимость растворимости серебра в алюминии от температуры приводит к упрочнению сплавов Al-Ag при термической обработке (закалке и старении). В процессе закалки и старения твердость по Бринеллю у сплава с 8,7 % Ag увеличивается с 363 до 710 МПа и предел прочности со 120 до 210 МПа, а у сплава с 20 % Ag предел прочности повышается со 180 до 340 МПа. Повышение концентрации серебра в сплаве Al-Ag до 10 % повышает модуль упругости алюминия (каждый процент серебра на 527 МПа).
Не нашли, что искали? Воспользуйтесь поиском по сайту:
©2015 - 2025 stydopedia.ru Все материалы защищены законодательством РФ.
|