Микросварные соединения к корпусам с покрытиями Ni и его сплавами
В производстве ППИ постоянно ведутся работы по изучению возможности применения металлизации корпусов никелем и его сплавами, алюминированию, использованию медной рамки и металлизации на основе медных паст, а также комбинированных покрытий корпусов. Для получения никелевой металлизации корпусов, отвечающей требованиям микросварки, необходимо внедрение новых электролитов никелирования с добавками, повышающими температурную стойкость покрытия, например, сплав никель – бор. Никелировать можно и некоторые типы серийно выпускаемых корпусов, но только после соответствующей доработки, снижающей их шероховатости поверхности контактных площадок.
Вакуумное алюминирование и алюминиевая плакировка пригодны только для пластмассовых и металлостеклянных корпусов, поэтому не решают проблему замены золота на корпусах приборов повышенной надежности. Внедрение гальванического алюминирования сдерживается сложностью технологического процесса покрытий из расплава солей, а также отсутствием соответствующего серийного оборудования для этих целей.
Применение медных рамок и медных покрытий сильно усложняет технологический процесс сборки и может снижать надежность приборов из-за быстрого окисления меди, роста сульфидов и низкой коррозионной стойкости, особенно в контакте с алюминиевым выводом.
Анализ пленочной металлизации показал, что пленки никеля и его сплавов, а также алюминия являются наиболее перспективными технологическими покрытиями корпусов ППИ. Следует отметить, что соединения алюминиевой проволоки с алюминиевым покрытием корпусов ППИ характеризуются нестабильностью как при сварке, так и при технологических испытаниях по причине низкого качества алюминиевых покрытий. Технологический процесс гальванического алюминирования корпусов достаточно сложен, структура покрытий неодинакова у различных партий корпусов, полученных на одних и тех же режимах, что недопустимо в условиях массового производства ППИ.
Из вышеприведенного следует, что в настоящее время наиболее технологичными покрытиями корпусов ППИ являются никель и его сплавы. Известно, что качественные соединения Al-Ni формируются в основном ультразвуковой сваркой (УЗС) при отсутствии на никеле оксидных пленок толщиной более 0,005-0,007 мкм и значительной площади взаимодействия контактируемых материалов, т. е. при малой шероховатости поверхности пленочной металлизации (Ra = 0,32-0,16 мкм). Это связано с большей микротвердостью никеля по сравнению с алюминием, что практически исключает пластическую деформацию покрытия при сварке.
Исследования прочности соединений Al-Ni. Как отмечалось выше, качество микросоединений Al-Ni, выполненных УЗС, существенно зависит от состояния никелевых пленок и технологии их получения.
Для оценки прочности сварных соединений алюминиевой проволоки с различными никелевыми покрытиями были изготовлены две партии образцов:
• партия 1 – основания, покрытые химическим способом слоем никеля толщиной 2-3 мкм;
• партия 2 – основания, покрытые электрохимическим способом слоем никеля толщиной 3-6 мкм.
В качестве материала внутренних выводов использовалась алюминиевая проволока АК09ПМ35, которая присоединялась к никелевым пленкам УЗС. Режимы сварки подбирались для каждой партии образцов исходя из условий получения максимальной прочности сварных соединений.
По результатам контроля 100 микросварных контактов от каждой партии образцов построены гистограммы распределения прочности микросоединений алюминиевой проволоки с различными никелевыми покрытиями (рис. 6.26). Никелевое покрытие обеспечивает удовлетворительную прочность сварных соединений с алюминиевым проволочным выводом только при достаточной площади физического контакта. Увеличить площадь контакта вывода с пленкой можно за счет повышения чистоты поверхности никелевых покрытий. Повышение чистоты поверхности осуществляется введением операции химического или электрохимического полирования до осаждения слоя никеля. Затем никелевые пленки наносятся химическим или электрохимическим способами.
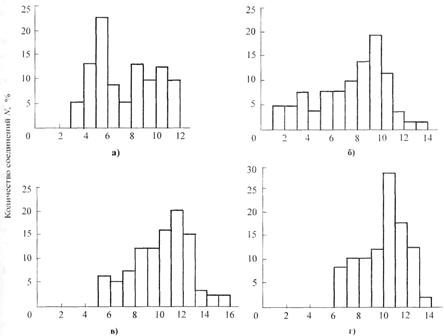
Разрушающая нагрузка Р, 10–2 Н
Рис. 6.26. Гистограммы распределения прочности микросварных соединений, выполненных УЗС, алюминиевой проволоки с различными никелевыми покрытиями: а – химическое никелирование; б – электрохимическое никелирование; в – химическое полирование поверхности с последующим электрохимическим никелированием; г – электрохимическое полирование поверхности с последующим электрохимическим никелированием
Для оценки влияния подготовки поверхности на прочность микросварных соединений были изготовлены еще две партии образцов:
• партия 3 – основания с предварительной химической полировкой поверхности и последующим электрохимическим осаждением слоя никеля толщиной 3-6 мкм;
• партия 4 – основания с предварительной электрохимической полировкой поверхности и последующим осаждением слоя никеля из того же электролита и той же толщины, что и для партии 3.
Таким образом, установлено, что УЗС алюминиевой проволокой по покрытиям, полученным электрохимическим никелированием с предварительной электрохимической полировкой поверхности, повышает прочность микросварных соединений Al-Ni в среднем на (2-4)·10–2 Н по сравнению с покрытиями, полученными химическим и электрохимическим никелированием без предварительной подготовки поверхности (рис. 6.26, г).
Исследование коррозионной стойкости микросоединений алюминиевой проволоки с покрытиями из никеля и его сплавов. Для проведения коррозионных испытаний были изготовлены образцы – корпуса из сплава железо – никель, покрытые слоем гальванического никеля и сплавами никеля с бором, индием и фосфором. Сплавы никеля с бором и индием наносились гальваническим способом, а сплав никеля с фосфором – химическим. Для сравнения испытывались образцы с золотым гальваническим покрытием.
Формирование микросварных соединений алюминиевой проволоки с покрытиями из золота, гальванического никеля, сплавов никеля, легированного бором, индием, фосфором, осуществляли УЗС на установке УЗСМ-2,5. При этом одной перемычкой проволоки марки АК09ПМ35 соединялись две изолированные площадки каждого корпуса. Для исследований использовалось по 50 корпусов с различными покрытиями.
Коррозионные испытания проводили путем погружения исследуемых контактов в электролит, имитирующий конденсат промышленной атмосферы (КПА), следующего состава (моль/л): 0,01NaCl + 0,001Na2SO3 + 0,001Na2SO4.
Кинетику разрушения контактов изучали кондуктометрическим методом с помощью омметра с одновременным измерением потенциала коррозионной пары высокоомным вольтметром ВК2-22. О степени разрушения контактов судили по измерению электросопротивления, а также визуально с помощью микроскопа МБС-1. При полном разрушении контакта электросопротивление резко возрастало с 0,15 Ом до 1 кОм.
Электрохимические измерения исследуемых материалов проводились потенциодинамическим методом на потенциостате П-5827М с использованием самопишущего потенциометра КСП. Электрод сравнения – насыщенный хлорсеребряный (ХСЛ), вспомогательный – из платины.
В табл. 6.10 приведены результаты коррозионных испытаний микросоединений алюминиевой проволоки с покрытиями из никеля и его сплавов.
Табл. 6.10. Стационарный потенциал Ест, среднее время разрушения τср и ток коррозии Iкор сварных контактов алюминиевой проволоки с покрытием из никеля, его сплавов и золота в КПА
Контакт
| Eст, В
| τср, ч
| Iкор, мкА/см2
| Al-(Ni+P)
| -0,35
|
|
| Al-(Ni+Jn)
| -0,39
|
|
| Al-(Ni+B)
| -0,41
|
|
| Al-Ni
| -0,44
|
|
| Al-Au
| -0,32
| 0,5
|
|
Из табл. 6.10 видно, что среднее время полного разрушения микросоединений в КПА существенно различается в зависимости от материала покрытия. Наименьшее значение тока коррозии (2 мкА) получено для никеля, легированного 2-4 %-ным фосфором (химический способ нанесения покрытия). Электрохимическое легирование никеля индием и бором повышает ток коррозии. Несколько большее значение тока коррозии наблюдается для гальванического никеля – 17 мкА/см2, а для золотого покрытия – 39 мкА/см2. Это обусловлено большой пористостью покрытия и уменьшением поляризуемости. Наименее пористые покрытия получаются для никеля, легированного фосфором, что объясняет снижение тока коррозии.
Не нашли, что искали? Воспользуйтесь поиском по сайту:
©2015 - 2025 stydopedia.ru Все материалы защищены законодательством РФ.
|