Точностной расчет контрольного приспособления
4.4.2.1 Расчет исполнительных размеров пробки
Расчет измерительной пробки производится по /21/.
Предельные размеры измерительной пробки определяются по формулам (4.17 - 4.19)



где – наименьший предельный размер измерительной пробки;
– наибольший предельный размер измерительной пробки;
– размер предельно изношенной измерительной пробки;
– размер предельно изношенного поэлементного проходного калибра для контроля базовой поверхности детали;
H– допуск на изготовление измерительной пробки;
W– величина износа измерительной пробки.
При позиционном допуске поверхности в диаметральном выражении мм, величина износа, допуск на изготовление и величина позиционного допуска измерительной пробки в диаметральном выражении составляют:
F=0,026; мм; W мм.



4.4.2.2 Расчет погрешности измерения приспособления
Выполняется расчет погрешности приспособления. Схема к расчету представлена на рисунке 4.8.
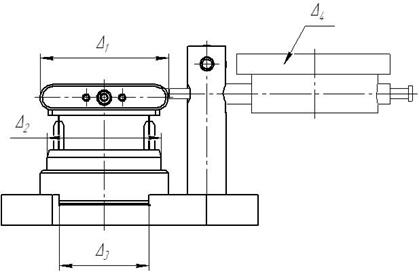
Рисунок 4.8 – Схема для расчета погрешности измерения
Погрешность измерения определяется по формуле
(4.20)
где – погрешность базирования измеряемой детали на базовом пальце приспособления;
– погрешность базирования базового пальца в пазу основания приспособления;
– погрешность индикатора, мм.
Погрешность базирования измеряемой детали на базовом пальце приспособления составляет:
.
Погрешность базирования базового пальца в пазу основания приспособления составляет:
.
Тогда по формуле (4.25) погрешность измерения данным приспособлением составит:
.
Общая погрешность приспособления не должна превышает трети допуска на скрещивания осей отверстий.

Общая погрешность приспособления не превышает трети допуска на скрещивание осей отверстий.
5 Организационно - экономический раздел
Исходные данные
Расчет ведется по методике /28/. Исходные данные:
- годовая производительность 3000 деталей;
- тип производства - среднесерийное;
- материал детали – Д16 ГОСТ 1583-93;
- цена 1 кг заготовки – 206 руб.;
- цена 1кг стружки – 35 руб.;
- масса заготовки – 0,68 кг;
- масса детали – 0,06 кг;
- оборудование работает в одну смену.
Нормы времени и коэффициенты загрузки на операции технологического процесса приведены в таблице 5.1.
Таблица 5.1 – Нормы времени и коэффициенты загрузки на операции техпроцесса
Номер операции
| Основное время
| Вспомогательное время
| Штучное время
| Расчетное количество оборудования
| Принятое количество оборудования
| Коэффициент загрузки по штучному времени
| Коэффициент загрузки по основному времени
|
| 0,93
| 5,53
| 7,2
| 0,08
|
| 0,08
| 0,01
|
| 0,35
| 1,14
| 1,66
| 0,02
|
| 0,02
| 0,004
|
| 0,53
| 9,6
| 11,3
| 0,14
|
| 0,14
| 0,006
| Таким образом деталь производиться за три операции, общие затраты времени составляют 20,16 на трех станках.
5.2 Труд и заработная плата
5.2.1 Расчёт численности промышленно-производственного персонала
5.2.1.1 Расчёт количества основных производственных рабочих
Явочное число основных производственных рабочих на участке механической обработки определяется по формуле
, (5.1)
где Сi – количество единиц оборудования на i-ой операции;
Mi – норма обслуживания рабочих мест (коэффициент многостаночности оборудования), принимается Mi = 1;
n – количество операций по изготовлению детали, n = 3.
Тогда:
RЯВ.= человека.
Явочное число рабочих принимается 3 человек.
Списочное число рабочих в смену определяется по планируемому проценту невыходов на работу по формуле
, (5.2)
где b – коэффициент, учитывающий дополнительное количество рабочих, требующихся для замены находящихся в отпуске или отсутствующих по какой-либо другой уважительной причине, ;
S – количество рабочих смен в сутки, S = 1 .
RСП. = (1 + 0,1) × 1 × 3 = 3,3 человека.
Списочное число рабочих принимается 4 человека.
Данные о явочной численности рабочих, а также их профессиональном и квалификационном составе сведены в таблицу 5.2.
Таблица 5.2 – Ведомость основных рабочих механического участка
№ опе-
рации
| Наименование профессии
| Количество рабочих по профессии
| Количество рабочих по разрядам
|
|
|
|
|
|
|
| Оператор
|
|
|
|
|
|
|
|
| Станочник
|
|
|
|
|
|
|
|
| Оператор
|
|
|
|
|
|
|
| 5.2.1.2 Расчёт численности вспомогательных рабочих и ИТР
Численность вспомогательных рабочих на участке механической обработки целесообразнее всего определять по нормам обслуживания. Для вспомогательных рабочих механического участка принимаются нормы обслуживания, приведённые в таблице 5.3.
Таблица 5.3 – Нормы обслуживания одним вспомогательным рабочим
Профессия вспомогательных рабочих
| Норма обслуживания
| Количество вспомогательных рабочих в ставках
| Контролёры
| 5–6% от числа станочников
| 0,2
| Раздатчики инструмента
| 30–35 человек
| 0,12
| Слесари-ремонтники
| 10–15% от числа станков
| 0,4
| Дежурные электромонтёры
| 80–100 станков
| 0,1
| Дежурные ремонтные слесари на станках
| 15–45 станков
| 0,2
| Уборщики производственных помещений
| 1,5–2% от числа станочников
| 0,08
| Число наладчиков Rнал определяется в зависимости от сложности наладки оборудования. В среднесерийном производстве на три - пять станков принимается один наладчик, Rнал = 1 человек (0,3 ставка).
Численность инженерно-технических работников определяется по следующим нормативам: мастер назначается для участка с числом работающих 20-30 человек. Должность старшего мастера вводится только при подчинении ему не менее трёх мастеров. Другие категории инженерно-технических работников для участка механической обработки не планируются. Количество инженерно-технических работников принимается RИТР = 0,2 чел.-ставки.
Информация о составе работающих на механическом участке сводится в таблицу 5.4.
Таблица 5.4 – Сводная ведомость общего состава работающих на механическом участке
Категория работающих
| Всего
человек
| В % от общего количества
работающих
| В % от количества основных производственных рабочих
| | | Производственные рабочие
|
| 71,6
|
| | Вспомогательные рабочие (чел/ставка)
| 7(1,39)
| 24,8
| 34,6
| | Инженерно-технические рабочие (чел/ставка)
| 1(0,2)
| 3,6
|
| | Итого
| 12(5,59)
|
| –
| |
Не нашли, что искали? Воспользуйтесь поиском по сайту:
©2015 - 2025 stydopedia.ru Все материалы защищены законодательством РФ.
|