Расчет и выбор норм времени
Определение норм времени на операцию 100.
Норма штучно – калькуляционного времени определится по формуле
, (3.29)
где – основное время;
– вспомогательное время;
– время на обслуживание рабочего места;
– время на отдых и личные надобности;
– подготовительно-заключительное время на партию деталей;
– объем партии деталей.
Основное время для всех переходов определится по формуле
, (3.30)
где – длина рабочего хода с учетом врезания и перебега,
– количество проходов.
Для пятого перехода (черновое точение поверхности)
.
Значения основного времени для остальных переходов приведены в таблице 3.5.
Вспомогательное время включает следующий ряд элементов нормы времени:
– время на изменение величины подачи;
– время на изменение частоты вращения шпинделя;
– время на смену инструмента в резцовой головке;
– время на подвод и отвод инструмента;
– время на включение подачи.
Вспомогательное время на пятом переходе определится как
,
.
Для остальных переходов значение вспомогательного времени представлено в таблице 3.5.
Время на обслуживание рабочего места определится по формуле
, (3.31)
где – оперативное время,
, (3.32)
,

Время на отдых и личные надобности
, (3.33)

Подготовительно – заключительное время включает ряд элементов:
– время на организационную подготовку ( – время на инструктаж мастера; – время на ознакомление с работой, чертежом, технологической документацией и осмотр заготовок; – время на получение на рабочем месте наряда, чертежа, технологической документации, программоносителя, режущего и вспомогательного инструмента, заготовки.)
– время на наладку ( – время на внесение в память системы ЧПУ программы с программоносителя; – время на растачивание кулачков на длину до 40мм;
– время на установку в револьверной головке необходимого режущего инструмента; – время на настройку нулевого положения).
, (3.34)
.
По формуле (3.29) определяется норма штучно – калькуляционного времени

Расчет основного и вспомогательного времени на операцию 100 сведен в таблицу 3.5.
Таблица 3.5 – Расчет основного и вспомогательного времени
100 токарная с ЧПУ
| Основное время То, мин
| Вспомогательное время Тв, мин
| Включение подачи
| Изменение частоты вращения шпинделя
| Изменение величины подачи
| Смена инструмента
| Подвод и отвод инструмента
| Измерение
| Снятие и установка заготовки
| Суммарное значение
|
|
|
|
|
|
|
|
|
|
| 1. Установка заготовки
| –
| –
| 0,064
| 0,064
| 2. Точение черновое
| 0,116
| 0,02
| 0,07
| 0,05
| 0,07
| 0,07
| –
| –
| 0,28
| 3. Точение чистовое
| 0,037
| 0,02
| 0,07
| 0,05
| 0,07
| 0,2
| 0,48
| 4. Переустановка заготовки
| –
| –
| 0,064
| 0,064
| 5. Точение черновое
| 0,025
| 0,02
| 0,07
| 0,05
| 0,07
| 0,07
| –
| –
| 0,28
| | | | | | | | | | | |
Продолжение таблицы 3.5
|
|
|
|
|
|
|
|
|
|
6. Точение чистовое
| 0,008
| 0,02
| 0,07
| 0,05
| 0,07
| 0,07
| 0,2
| –
| 0,48
| 7. Сверление отверстия
| 0,014
| 0,07
| 0,05
| 0,07
| –
| 0,28
| 8. Расточка отверстия черновая
| 0,079
| 0,07
| 0,05
| 0,07
| –
| 0,28
| 9. Расточка отверстия чистовая
| 0,021
| 0,07
| 0,05
| 0,07
| 0,2
| 0,48
| 10. Точение фаски
| 0,007
| 0,07
| –
| 0,07
| 0,2
| 0,43
| 11.Центровка 3-х
отверстий
| 0,009
| 0,07
| –
| 0,07
| –
| 0,21
| 12. Сверление 3-х отверстий
| 0,123
| 0,07
| 0,05
| 0,07
| 0,2
| 0,48
| 13. Зенкерование 3-х отверстий
| 0,055
| 0,02
| –
| 0,05
| 0,07
| 0,07
| 0,2
| –
| 0,41
| 14.Центровка 6-ти
отверстий
| 0,018
| 0,07
| –
| 0,07
| –
| 0,21
| 15.Сверление 4-х отверстий
| 0,109
| –
| 0,05
| 0,07
| –
| 0,21
| 16. Сверление 2-х отверстий
| 0,072
| –
| 0,05
| –
| –
| 0,14
| 17. Зенковка шести фасок
| 0,008
| –
| 0,05
| 0,07
| –
| 0,21
| 18. Нарезание шести резьб
| 0,23
| –
| 0,05
| 0,07
| 0,2
| 0,41
| 19. Снятие детали
| –
| –
| 0,064
| 0,064
| Итого на операции
| 0,927
| 5,533
| | | | | | | | | | | | | | 3.10 Расчёт суммарной погрешности обработки
Суммарная погрешность определяется по методике /13/.
Производится оценка суммарной погрешности обработки поверхности диаметром 71,8d10( ) на операции 100 (точение торца).
Суммарная погрешность обработки для линейных размеров определяется по формуле:
, (3.35)
где – погрешность, связанная с упругими отжатиями, мкм;
– погрешность, связанная с геометрической точностью станка, мкм;
– погрешность, связанная с тепловыми деформациями, мкм;
– погрешность, связанная с базированием, мкм;
– погрешность закрепления, мкм;
– погрешность приспособления, мкм;
– погрешность смещения центра группирования относительно настроенного размера, мкм;
– погрешность измерения, мкм;
– погрешность, связанная с позиционированием резцедержателя, мкм.
Погрешность, связанная с упругими отжатиями, определяется по формуле
=ωmax×Pzmax – Pzmin×ωmin , (3.36)
где ωmax и ωmin – максимальная и минимальная податливость станка, мкм/кН;
Pоmax и Pоmin – максимальная и минимальная осевая сила резания, кН.
Сила резания Pz определится по формуле (3.19)
Максимальная сила резания при глубине резания tmax вычисляется по формуле (3.19).
tmax= tmin + , (3.37)
где tmin – минимальная глубина резания, tmin=0,2мм,
TD – допуск на обработанную поверхность, .
tmax= 0,2 + =0,26мм.
Максимальная сила резания:

Минимальная сила резания:

Максимальная податливость станка:
ωmax= ωmin + ωинстр , (3.38)
где ωmin= ωст – минимальная податливость станка, ωmin=16 мкм;
ωинстр – податливость инструмента, мкм/кН (можно принять равной нулю, т.к. применяется импортный резец и его вылет довольно мал)
Тогда по формуле (3.36):
=16×0,0402 – 16×0,0310=0,15 мкм.
Погрешность, связанная с геометрической точностью станка:
= , (3.39)
где Сm – допускаемое отклонение от параллельности оси шпинделя направляющих станка в вертикальной плоскости, Сm =5 мкм;
lm – длина обрабатываемой поверхности, lm =41 мм;
L – базовая длина, L=100 мм;
= .
Погрешность, вызванная тепловыми деформациями, определяется по формуле:
=B×( ), (3.39)
где В – коэффициент для лезвийной обработки, В=0,1;
=0,1×(0,17+2,5)=0.27мкм.
Погрешность базирования 
Погрешность закрепления 
Погрешность приспособления 
Погрешность смещения центра группирования определяется по формуле:
= , (3.40)
где ωm – мгновенное поле рассеивания, мкм;
m – количество пробных деталей, m=3.
ωm =1,2× , (3.41)
ωm =1,2× 
Тогда по формуле (3.40)
= 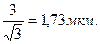
Погрешность измерения – =3 мкм.
Погрешность, связанная с позиционированием резцедержателя мкм.
Тогда суммарная погрешность обработки для диаметральных размеров определяется по формуле (3.33)
Δε=2,4× .
Так как Δε=26,7мкм удовлетворяет условию: Δε≤0,8TD=96мкм, то заданный размер будет обеспечиваться на данном переходе с достаточной точностью.
3.11 Определение загрузки станков и требуемого количества оборудования
Требуемое количество оборудования определяется по формуле (расчет ведется для операции 100)
, (3.42)
.
т.е. необходим один станок для выполнения операции.
Коэффициент используемого оборудования определяется по формуле:
, (3.43)
.
т.е. оборудование используется на 8%.
Для 120 операции
,
т.е. необходим один станок для выполнения операции.
Коэффициент используемого оборудования
,
т.е. оборудование используется на 2%.
Для 140 операции
,
т.е. необходим один станок для выполнения операции.
Коэффициент используемого оборудования
,
т.е. оборудование используется на 14%.
Определяется средний коэффициент использования оборудования
, (3.44)
.
4 Проектирование технологической оснастки
4.1 Описание конструкции и принципа работы станочного приспособления для 120 операции
В дипломном проекте разработано приспособление для 120 операции на фрезерном станке СФ 676 . Операционный эскиз обработки представлен в карте эскизов ТПЖА.20141.04302 техпроцесса. Конструкция приспособления приведена на листе графической части ТПЖА.293000.043 – 01СБ.
4.1.1 Описание конструкции станочного приспособления
Приспособление для 120 операции представленное на рисунке 4.1 имеет механизированный привод.
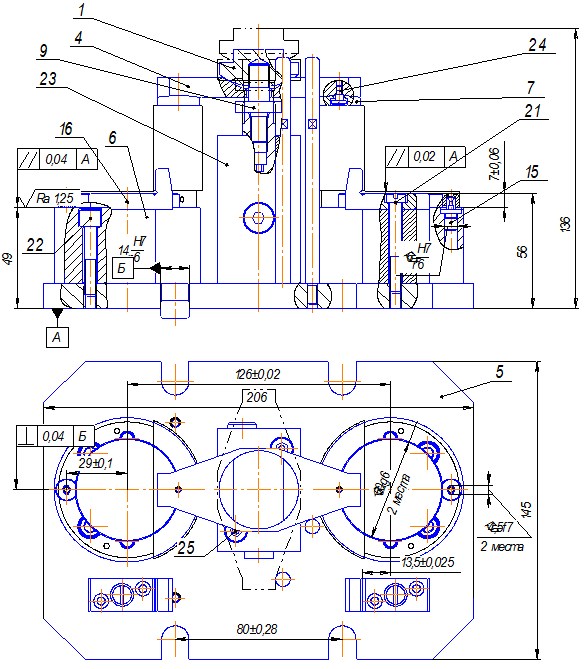
Рисунок 4.1 – Общий вид станочного приспособления
Исходя из конструкции детали и данных задания, спроектирована конструкция приспособления с механизированным приводом. В качестве привода, который обеспечивает исходную силу для закрепления заготовки, используется гидроцилиндр.
В качестве зажимного элемента, для создания усилий противодействующих внешним силам, которые могут сместить заготовки с установочных поверхностей, используется планка (поз. 4). На планке закреплены пятки (поз.7), которые непосредственно прижимают детали. Планка присоединяется к штоку гидроцилиндра (поз. 20) через шпильку (поз. 9) и сферическую гайку (поз. 1). Установочными деталями в приспособлении являются пальцы (цилиндрический (поз. 2) и ромбический (поз. 15)) и опорные пластины (поз.3). Опорные пластины (поз.3) закрепляются на плите (поз.5) приспособления при помощи винтов (поз. 14) и штифтов (поз. 19). Гидроцилиндр (поз.20) закрепляется на плите с помощью винтов (поз. 11). На приспособлении имеются упоры (поз. 16) для настройки инструмента. Упоры ( поз. 16) установлены на призмы (поз. 6), а призмы закрепляются на плите с помощью винтов (поз. 13) и штифтов (поз. 18). Приспособление ориентируется на станке при помощи двух шпонок (поз. 17)
Заготовки устанавливается на два пальца и опорные пластины, установленные на плиту приспособления, затем сверху прижимаются планкой, приходящей в движение от гидроцилиндра. Ход штока гидроцилиндра составляет 10 мм.
4.1.2 Расчёт усилия зажима
При фрезеровке плоскости и уступа сила резания не должна передаваться на базовые цилиндрические поверхности. Для этого зажимное усилие должно создать на опоре силу трения, предотвращающую перемещение детали под действием силы резания. Расчёт необходимо вести по силе, максимально стремящейся сместить заготовку в направлении цилиндрических поверхностей, по которым происходит базирование детали в приспособлении, то есть расчёт необходимо вести по самому неблагоприятному фактору. Самым неблагоприятным фактором будет сила резания , возникающая при фрезеровании плоскости, которая стремиться сместить деталь в направлении базовых цилиндрических поверхностей. На рисунке 4.2 приведена схема для определения силы зажима.
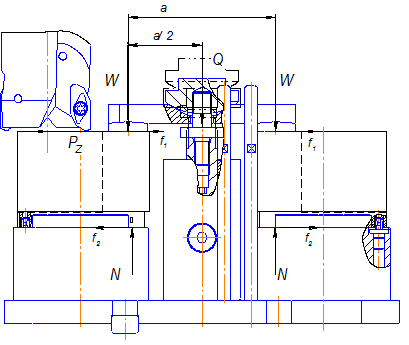
Рисунок 4.2 - Расчётная схема для определения силы зажима
В соответствии со схемой уравнение равновесия заготовки:

где – сила резания, Н;
К – коэффициент надёжности закрепления;
f1 – коэффициент трения между обрабатываемой деталью и зажимным элементом приспособления, ;
f2 – коэффициент трения между обрабатываемой деталью и опорой, .
Коэффициент запаса определяется по формуле /19/

где – гарантированный коэффициент запаса, /19/;
– коэффициент, учитывающий увеличение сил резания из-за случайных неровностей на обрабатываемых поверхностях, /19/;
– коэффициент, характеризующий увеличение сил резания вследствие износа режущего инструмента, /19/;
– коэффициент, учитывающий увеличение сил резания при прерывистом резании, /19/;
– коэффициент, характеризующий постоянство силы закрепления в зажимном механизме, /19/;
– коэффициент, характеризующий эргономику механизированного зажимногомеханизма /19/;
– учитывается только при наличии моментов, стремящихся повернуть заготовку,установленную плоской поверхностью, /19/.

Принимается К=2,5.
Сила резания при фрезеровании плоскости концевой фрезой определяется по формуле /13/

где – постоянная для данных условий и показатели степени; ;
– показатели степени, ;
– ширина фрезерования, ;
– глубина фрезерования, ;
– подача, ;
– число зубьев фрезы, ;
D – диаметр фрезы, D=50 мм;
– частота вращения фрезы, ;
– постоянный коэффициент, Кмр=1,0;
– коэффициент силы резания для алюминия, .


4.1.3 Расчёт исходной силы
Расчётная схема для определения исходной силы представлена на рисунке 4.2.Для данного зажима, исходная сила на штоке определяется по формуле


4.1.4 Подбор механизированного привода
В качестве механизированного привода к данному приспособлению выбирается гидравлический привод. Данный привод предпочтителен, так как усилия зажима велики. В соответствии с расчётами для создания необходимого усилия зажатия выбирается гидроцилиндр марки AMF 65250 /26/. Усилие на штоке равно 4 кН, при давлении масла равном 3,5 МПа.
Относительная разность действительного и расчётного усилий Δ равно

где – усилие на штоке, ;
– расчетное усилие зажима, .

Таким образом, выбранный механизированный зажим гарантированно создает необходимую силу зажима.
4.2 Описание конструкции и принцип работы станочного приспособления для 140 операции
Спроектировано станочное приспособление на операцию 140 технологического процесса механической обработки детали. Операционный эскиз обработки представлен в карте эскизов ТПЖА.20141.04303 техпроцесса. Чертеж станочного приспособления представлен в графической части ТПЖА.293226.043-04 СБ
4.2.1 Описание конструкции и принцип работы станочного приспособления
Приспособление состоит из стального корпуса (поз.1), на котором устанавливаются остальные детали приспособления. Обрабатываемая деталь устанавливается на оправку (поз.2) и две опоры (поз.7). Оправка устанавливается на корпус и фиксируется с помощью штифта (поз.10) и крепятся к корпусу винтами поз.5. Таким образом обеспечивается установка детали по внешней цилиндрической поверхности, на отверстие и установка на три опорные точки.
Деталь зажимается двумя прихватами (поз.4) с использованием двух гаек с буртиком (поз.6). Прихваты устанавливаются в стаканы (поз.3). Стаканы фиксируются от проворота штифтами (поз.9). Для базирования приспособления на столе станка предусмотрены две шпонки (поз.8), которые запрессовываются в корпус.
Принцип работы приспособления: заготовка устанавливается на оправку (поз.2) и опоры (поз.7). После установки заготовки станочник вручную передвигает прихваты (поз.4) к детали. Затем станочник затягивает гаечным ключом гайки с буртиками (поз.6). Прихваты зажимают деталь. После обработки детали станочник гаечным ключом раскручивает гайки. Станочник вручную отодвигает прихваты в сторону от детали. Происходит снятие детали.
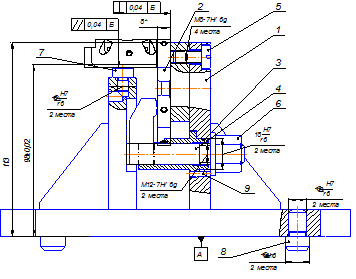
Рисунок 4.3 – Общий вид станочного приспособления
4.2.2 Силовой расчет станочного приспособления
Для обеспечения надежного закрепления заготовки необходимо произвести расчет необходимой силы зажима, чтобы исключить отрыв и смещение заготовки в процессе обработки. Все силы, приложенные к детали, показаны на рисунке 4.4.

Рисунок 4.4 – Схема приложения сил
Силы резания и крутящий момент рассчитываются по методике /14/. Сила резания PZ для фрезерования алюминиевого сплава рассчитывается по формуле

где – постоянная для данных условий и показатели степени; ;
– показатели степени, ;
– ширина фрезерования, ;
– глубина фрезерования, ;
– подача, ;
– число зубьев фрезы, ;
D – диаметр фрезы, D=25 мм;
– частота вращения фрезы, ;
– постоянный коэффициент, Кмр=1,0;
– коэффициент силы резания для алюминия, .

Крутящий момент при фрезеровании определится по формуле /14/

Сила Ph, смещающая заготовку вдоль оси фрезерования, рассчитывается по формуле

Расчет усилия зажима ведется по методике /19/:

Тогда
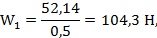

Значение коэффициента запаса К для зажима детали определяется по следующей формуле (4.2)

где К0 = 1,5 – коэффициент гарантированного запаса;
К1 = 1,2 – коэффициент, учитывающий увеличение сил резания из-за случайных неровностей на обрабатываемой поверхности;
К2 = 1,2 – коэффициент, учитывающий увеличение сил резания вследствие износа инструмента;
К3 = 1,1 – коэффициент, учитывающий увеличение сил резания при прерывистом резании;
К4 = 1,0 – коэффициент, характеризующий постоянство усилия зажима, развиваемым зажимным механизмом, (ручной зажимной механизм );
К5 не учитывается, так как это коэффициент, характеризующий эргономику немеханизированных зажимных механизмов;
К6 = 1,0 – коэффициент, учитывающий наличие момента, стремящегося повернуть заготовку, (заготовка установлена на пальцы).
Подставляя численные значения в формулу (4.2), получаем:

Суммарное усилие зажима находится /19/:

Усилие зажима создается двумя прихватами. Тогда усилие зажима одного прихвата будет равно W/2=1296Н. Схема приложения сил показана на рисунке 4.5. Исходное усилие, создаваемое одним прихватом, вычисляется по формуле
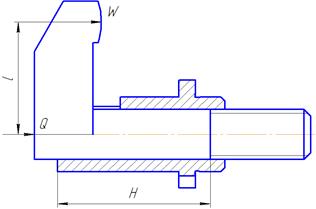
Рисунок 4.5 – Схема приложения сил

Усилие затяжки гайки вычисляется по формуле

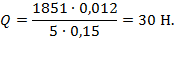
Усилие затяжки не превышает допустимого значения [Q]=100 Н.
4.3 Описание конструкции и расчёт контрольного приспособления для контроля позиционного допуска шести резьбовых отверстий М3-7H относительно наружной цилиндрической поверхности диаметром 66h12 мм
4.3.1 Описание конструкции и принцип работы контрольного приспособления
Контрольное приспособление разработано для контрольной операции технологического процесса. Данное приспособление предназначено для контроля позиционного допуска шести резьбовых отверстий М3-7H относительно наружной цилиндрической поверхности диаметром 66h12. Контрольное приспособление представлено в графической части на чертеже ТПЖА.401123.043-02 СБ. Базовым элементом приспособления является каленое кольцо. Кольцо присоединяется при помощи винтов к основанию.
Деталь устанавливается на базовую цилиндрическую поверхность кольца, затем по очереди вкручиваются резьбовые калибры в контролируемые отверстия. Размеры резьбы калибра – пробка /24/.
Не нашли, что искали? Воспользуйтесь поиском по сайту:
©2015 - 2025 stydopedia.ru Все материалы защищены законодательством РФ.
|