Режущий инструмент, применяемый для высокопроизводительного токарного станка TS46-SMC
Составной частью системы инструментального обеспечения станков с ЧПУ является широкая номенклатура режущего инструмента, который в основном имеет те же конструкции, что и для станков с ручным управлением. Однако, как указывалось выше, в связи с высокой стоимостью оборудования с ЧПУ эксплуатировать инструмент необходимо на экономически обоснованной скорости резания, обеспечивающей минимальную себестоимость операции. Это накладывает ряд требований к конструкциям режущего инструмента.
На станках с ЧПУ рационально применять только прогрессивные конструкции режущего инструмента, удовлетворяющего комплексу требований, вытекающих из особенностей эксплуатации этих станков.
В первую очередь для достижения высокой эффективности использования оборудования с ЧПУ режущий инструмент должен обеспечивать повышенные экономические режимы резания, что позволит снизить время резания при обработке конкретных поверхностей и деталей.
Другим неотъемлемым требованием к инструменту является обеспечение заданной стойкости (надежности) в работе, исключающей потерю его режущей способности в течение установленного программой времени работы, и снижение вероятности случайных поломок инструмента, а следовательно, простоев станка и возможного брака деталей. Это означает, что для уменьшения числа возможных случайных поломок инструмента должны программироваться более короткие периоды его стойкости при меньшем износе, чем износ при эксплуатации на станках с ручным управлением.
Режущая способность инструмента и его надежность более всего зависят от материала режущей части, конструктивных элементов и геометрических параметров режущей части, а также и от других факторов. Материал режущей части инструмента по своим физико-механическим свойствам нужно выбирать оптимальным для каждого вида инструмента и обработки в конкретных условиях. Основными факторами, влияющими на выбор материала режущей части конкретных инструментов, являются свойства материала заготовки, жесткость и виброустойчивость системы станок-приспособление-инструмент-заготовка, условий отвода стружки и подвода СОЖ, требования к обрабатываемой поверхности, припуски на обработку и др.
Для современных станков с ЧПУ наиболее эффективны режущие инструменты, оснащенные твердым сплавом или целиком изготовленные из твердого сплава, особенно инструменты малых размеров. Иногда весьма эффективно при работе с небольшими припусками для изготовления инструмента (резцов и фрез) применять новые инструментальные материалы: режущую керамику, синтетические сверхтвердые материалы на основе нитридов бора и кремния и т. п. На инструменты из быстрорежущей стали рационально наносить износостойкие покрытия из нитридов титана и др.
Существенное влияние на работу инструмента оказывают правильный выбор конструктивных элементов и геометрических параметров режущей части, особенно в конкретных условиях его применения, от этого в значительной степени также зависят выбор экономически обоснованных режимов резания и качество обработанной поверхности деталей.
Целесообразно конструкции специализировать по видам обрабатываемых материалов, требованиям к обработанной поверхности, условиям эксплуатации на данном станке и особенностям конкретной детали, например ее жесткости. Для обработки деталей из материалов основных групп (из стали, чугуна, алюминиевых сплавов, труднообрабатываемых сплавов) необходимо использовать соответствующие конструкции инструмента. Это связано как с назначением геометрических параметров режущей части, так и с рядом конструктивных элементов многолезвийных инструментов, в том числе числа зубьев, размеров и форм стружечных канавок для сверл, фрез, разверток, метчиков. Конструкции должны быть специализированы в соответствии с требованиями к параметрам шероховатости и точности обрабатываемых поверхностей.
Помимо требований к режущим свойствам инструмента для эффективной эксплуатации станков с ЧПУ инструмент должен обладать быстросменностью, т. е. обеспечивать сокращение времени на восстановление или замену затупившихся режущих кромок, а также сохранять первоначальные рабочие размеры (диаметр, длину и т. п.) С максимально возможным исключением подналадки. Для сокращения номенклатуры весьма важным является возможность использования одних и тех же режущих инструментов для обработки нескольких поверхностей, а также использования унифицированных режущих элементов и исключения, по возможности, переточки режущих частей инструмента. Перечисленным требованиям более всего отвечают конструкции сборного инструмента с механическим креплением сменных многогранных пластин. /1/
На отдельных видах инструментов применение сменных пластин позволяет существенно упростить их конструкцию.
В этом случае инструментальный блок с хвостовиком для установки на станке может состоять только из корпуса, на котором в специальных гнездах закреплены унифицированные режущие пластины. Такой инструмент обладает повышенной жесткостью (например, концевые фрезы). На сборных инструментах применяют сменные пластины из твердого сплава, режущей керамики и синтетических сверхтвердых материалов (СТМ).
В настоящее время широко выпускают со сменными пластинами токарные резцы различных типов, сверла, расточные одно- и двухлезвийные головки, торцовые и концевые фрезы и т. д.
Режущий инструмент со сменными режущими пластинами, в том числе с износостойким покрытием, при эксплуатации на станках с ЧПУ имеет ряд существенных преимуществ, главные из которых следующие:
- обеспечиваются более высокие режимы резания, стойкость и надежность за счет исключения напайки и переточки;
- обеспечивается стабильное формирование и отвод стружки за счет специальных форм передней поверхности пластин;
- позволяет на одном корпусе инструмента использовать оптимальные марки твердого сплава в соответствии с характеристиками материала заготовки;
- сохраняются постоянными (или мало изменяются) размеры инструментов;
- исключаются переточка и изменение размеров многолезвийного и мерного инструмента.
В силу указанных преимуществ инструменты, оснащенные сменными пластинами, являются основным видом режущего инструмента для станков с ЧПУ.
В последнее время широкое распространение получает модульный (агрегатный) принцип создания инструмента для многоцелевых станков. Этот принцип построения инструмента позволяет создать систему унифицированных взаимосвязанных элементов режущего инструмента, обеспечивающую повышение универсальности инструмента при решении различных технологических задач, и сократить номенклатуру применяемого инструмента, особенно специального.
Конструктивные элементы и основные размеры модульного инструмента построены по определенной системе, обеспечивающей выбор длин и диаметров в широком диапазоне, особенно при обработке отверстий. В этом случае инструментальные блоки можно собирать более оптимальными по жесткости, точности и другим параметрам.
Для станков с ЧПУ сверлильно-расточно-фрезерной группы модульная система инструмента может быть более развитой.
В систему входят режущие инструменты (сверла, фрезы, резцы и т. п.), наборы удлинителей и переходников с большего диаметра на меньший. Модульный принцип построения инструментальной оснастки наиболее эффективен для станков с ЧПУ.
Он позволяет быстро создавать инструмент любых размеров, в том числе и специальные конструкции в зависимости от типа используемого станка, материала заготовки и масштабов производства.
В процессе эксплуатации станков с ЧПУ весьма существенную роль играет применение смазочно-охлаждающих жидкостей. Роль СОЖ общеизвестна, однако при работе инструмента на автоматизированном оборудовании она еще более существенна. Помимо значительного повышения стойкости режущего инструмента СОЖ способствует более стабильному стружкоформированию и лучшему отводу стружки из зоны резания.
На оборудовании с ЧПУ в настоящее время начинают применять более эффективный метод подвода СОЖ - внутренний через инструмент непосредственно в зону резания под повышенным давлением, в том числе через вращающийся инструмент. В последнем случае СОЖ подается через шпиндель станка или применяют сменные специальные патроны, подающие СОЖ по заданной программе.
Внутренний подвод СОЖ с обязательной ее фильтрацией существенно повышает стойкость режущего инструмента и качество обработанной поверхности при работе чистовых инструментов. Режущий и вспомогательный инструмент в этом случае изготовляют со специальными каналами.
Ниже рассмотрены некоторые конструкции режущего инструмента, применяемого для обработки на токарном станке TS46-SMC и фрезерном станке VC-560. Это фрезы и сверла фирмы HANITA (рисунок 1.44–1.49), резцы фирмы ISCAR (рисунок 1.50–1.51), сверло центровочное фирмы Dormer (рисунок 1.52) и миниатюрные резьбовые фрезы для внутренней резьбы фирмы Vargus (рисунок 1.53).

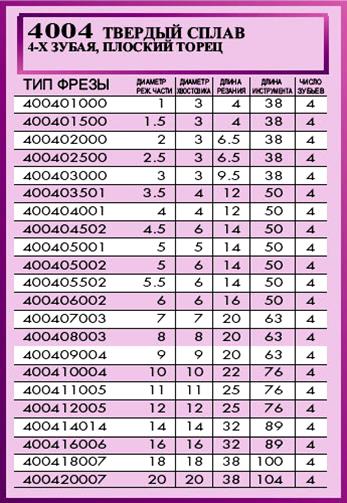
Рисунок 1.44 – Четырехзубая фреза 4004 с плоским торцем для чистовой обработки цилиндрической частью фрезы
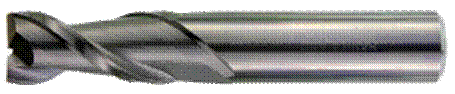
Рисунок 1.45 – Двухзубая фреза с плоским торцем и большим углом наклона канавки для обработки пазов в алюминии

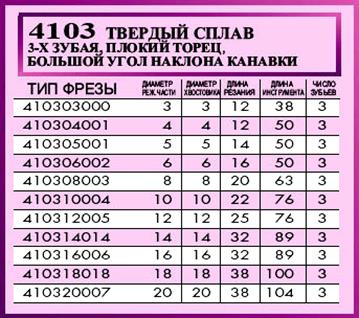
Рисунок 1.46 – Трехзубая фреза 4103 с плоским торцем и большим углом наклона канавки для обработки пазов в алюминии
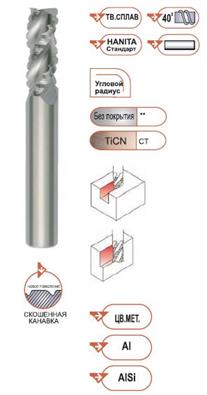
Рисунок 1.47 – Фреза для черновой и получистовой обработки алюминиевых сплавов
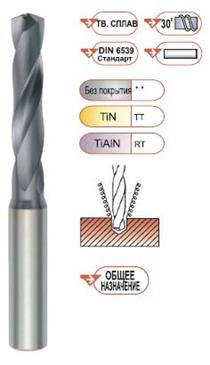
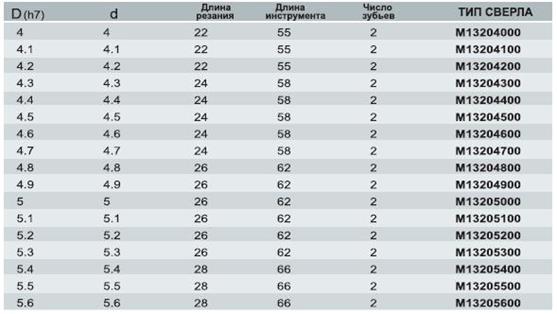
Рисунок 1.48 –Сверло М132 стандартной длины с углом при вершине 135° для обработки неглубоких отверстий
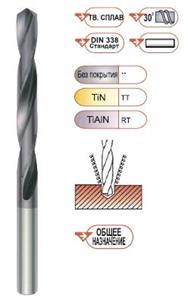
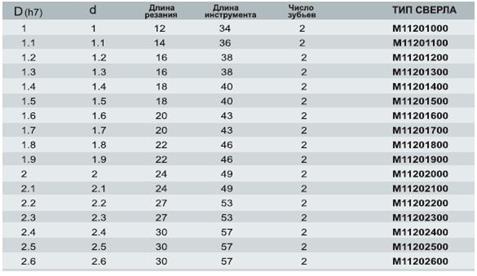
Рисунок 1.49 – Высокопроизводительное удлиненное твердосплавное сверло М112 с углом при вершине 118°
|
| а
| б
| Рисунок 1.50 – Резец проходной
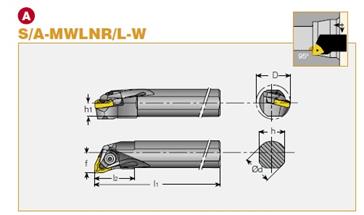
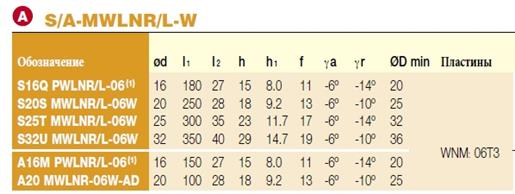
Рисунок 1.51 – Резец расточной
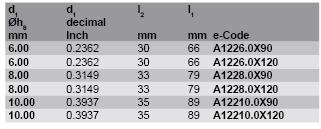
Рисунок 1.52 – Сверло центровочное для станков с ЧПУ DIN 1897
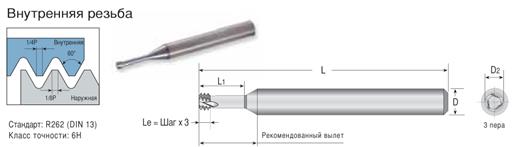
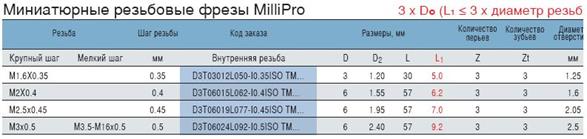
Рисунок 1.53 – Миниатюрные резьбовые фрезы MilliPro для внутренней резьбы
Выводы по обзорной части
Для механической обработки детали «Основание 4043» были выбраны высокопроизводительный токарный станок с ЧПУ TS46-SMC и фрезерный станок типа обрабатывающий центр с ЧПУ VC-560. В обзорной части дипломной работы были рассмотрены параметры и движения станков, которые были признаны удовлетворяющими для получения поверхностей детали необходимого качества и размеров детали нужной точности.
Выбор вспомогательного инструмента осуществляется также из имеющегося в наличии в каталоге. Это новые инструменты компании EROGLU – резцедержатель цниверсальный формы D1, резцедержатель для осевого инструмента, патрон осевой S1+S2/ESX-32, патрон осевой ESX-32, патрон радиальный ESX-32, патрон цанговый, патрон быстросменный резьбонарезной.
Используемый режущий инструмент - фрезы и сверла фирмы HANITA и резцы фирмы ISCAR.
Сверла используются твердосплавные – М132 стандартной длины с углом при вершине 135° для обработки неглубоких отверстий и высокопроизводительное удлиненное сверло М112 с углом при вершине 118°. Находит применение четырехзубая фреза 4004 с плоским торцем для чистовой обработки цилиндрической частью фрезы. Для нарезания резьбы применяется резьбовая фреза MilliPro.
Для токарной обработки – резец проходной MWLN/R
Таким образом, оборудование, вспомогательный и режущий инструмент для обработки детали «Основание 4043» подобраны.
2 Техническое и социальное – экономическое обоснование. Задачи дипломного проекта
Эффективность производства, качество выпускаемой продукции во многом зависят от опережающего развития производства нового оборудования, машин, станков и аппаратов, от всемирного внедрения методов технико-экономического анализа, обеспечивающего решение технических вопросов и экономическую эффективность технологических и конструкторских разработок.
Главная цель дипломного проекта – разработать технологический процесс обработки детали "Основание 4043" с использованием современного оборудования в условиях мелкосерийного производства. При этом необходимо в предлагаемом варианте технологического процесса детали "Основание 4043" уменьшить трудоёмкость изготовления детали. При переводе обработки с универсальных станков происходит экономия средств, так как на универсальных операциях один рабочий обслуживает только один станок, а на программной операции один станочник обслуживает 4-5 станков одновременно.
Задачи дипломного проектирования следующие:
- выполнить анализ технических требований и определить тип производства изготовления детали "Основание 4043";
- спроектировать конструкции станочных и контрольных приспособлений;
- выполнить расчёт себестоимости детали;
- выполнить анализ травмоопасных и вредных производственных факторов на механическом участке станков с ЧПУ, рассмотреть средства защиты от травмоопасных и вредных производственных факторов и схему системы стружкоудаления на участке.
Технический эффект при проектировании технологического процесса заключается в следующем:
- снижение времени нахождения детали во всем производственном цикле обработки;
- существенное повышение производительности труда в год за счёт применения современного оборудования;
- повышение точности изготовления детали за счёт применения точных станков.
Социально-экономический эффект, возникающий при проектировании технологического процесса, заключается в следующем:
- снижение себестоимости изготовления детали и, следовательно, повышение прибыли предприятия;
- повышение заработной платы.
3 Технологическая часть
3.1 Анализ конструкции детали с точки зрения технологичности
Как правило, детали типа «основание» являются основными во многих механизмах и как следствие самыми сложными, так как имеют множество поверхностей подлежащих обработке.
Деталь «Основание 4043» представлена на чертеже ТПЖА.711117.043.
Основание представляет собой сочетание поверхностей простой формы, обработка которых не вызывает трудностей.
Деталь изготавливается из дуралюмина марки Д16, который отлично обрабатывается резанием и допускает применение высокопроизводительных режимов обработки.
В связи с небольшим объемом партии и типичностью данной детали, наиболее целесообразные виды механической обработки – наружное точение, растачивание отверстия, подрезание торцов, сверление, нарезание резьбы, фрезерование возможно осуществить на широко распространенном оборудовании: токарном и фрезерном станках. Применение станков с ЧПУ, а именно многооперационных центров в данном случае значительно снизит стоимость обработки.
Механическую обработку целесообразней на выбранном оборудовании вести инструментом со сменными многогранными пластинами, а также имеющимся на каждом предприятии инструментом. Проходные, подрезные и расточные резцы, осевой инструмент являются широко распространенным, хорошо освоенным инструментом. На детали нет труднодоступных для обработки мест, что значительно упрощает обработку. Все заданные на чертеже размеры можно проконтролировать широко распространенным мерительным инструментом: пробками, скобами, шаблонами.
К детали не предъявляется никаких специфических требований, то есть не нужно никаких дополнительных технологических операций. Все размеры и заданную шероховатость поверхностей легко получить на выбранном оборудовании, таким образом, нет необходимости в дополнительной обработке. Все указанные на чертеже допускаемые отклонения по геометрической форме и взаимному расположению поверхностей можно получить на выбранном оборудовании, учитывая геометрические погрешности станков.
Таким образом, конструкция данной детали может быть признана технологичной.
3.2 Определение такта выпуска и типа производства
Тип производства в основном зависит от двух факторов, а именно: заданной программы и трудоемкости изготовления изделия. На основании заданной программы рассчитывается такт выпуска изделия , а трудоемкость определяется средним штучным временем по операциям действующего на производстве или аналогичного технологического процесса. Отношение этих величин называется коэффициентом серийности
. (3.1)
Приняты следующие значения коэффициента серийности:
- для массового производства ;
- для крупносерийного производства ;
- для среднесерийного производства ;
- для мелкосерийного производства 
Величина такта выпуска , мин/шт, рассчитывается по формуле
, (3.2)
где FД – действительный годовой фонд времени работы оборудования, ч.;
N – годовая программа выпуска деталей, шт.
Действительный годовой фонд времени работы оборудования при двухсменном режиме равняется 4015 часам /12/. Значение годовой программы выпуска деталей приведено в задании на проект и равно трем тысячам штук. Подставив эти значения в формулу (3.2) определяют такт выпуска
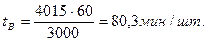
Для определения среднего штучного времени по операциям нужно провести нормирование вновь разрабатываемого технологического процесса данные значения времени приводятся в таблице 3.1.
Таблица 3.1 – Значения штучного времени на операциях технологического процесса
Операция
| Тшт, мин
|
|
| 100. Токарная с ЧПУ
| 7,2
| 120. Вертикально-фрезерная
| 1,66
| 140. Фрезерная с ЧПУ
| 11,3
| Формула для расчета среднего штучного времени имеет вид
, (3.3)
где – штучное или штучно-калькуляционное время на каждой операции, мин;
n – число операций.
Таким образом, среднее штучное время:
.
Подставив значение среднего штучного времени в выражение (3.1) определяется коэффициент серийности производства:
.
Из этого следует, что данное производство является среднесерийным.
Рассчитывается число деталей Nп в партии по формуле
(3.4)
где а – число дней, на которое необходимо иметь запас деталей, принимается, а = 3 дней /12/;
F – число рабочих дней в году, F = 247 дней.
штуки.
Расчетное число смен на обработку партии деталей:
, (3.5)
смены.
Принимается число смен спр = 1.
Тогда число деталей в партии будет равно
, (3.6)
штук.
Принимается количество деталей в партии 57 штук.
3.3 Анализ требований к точности обрабатываемых поверхностей
В детали «Основание 4043» большинство основных элементов под обработку составляют гладкие цилиндрические поверхности различных квалитетов точности: от свободных размеров по тринадцатому квалитету, до поверхностей седьмого квалитета. Отверстия обрабатываются в сплошном материале детали. Также фрезеруются боковые плоские поверхности и горизонтальные установочные плоскости. Дополнительными элементами являются фаски.
Самые жесткие требования предъявляются к поверхностям диаметром 50 мм и 44,6 мм которые обрабатываются по 7 и 8 квалитету точности соответственно. Поверхности имеют шероховатости Rа=1,25 мкм и Rа=2,5 мкм. Но данные требования без проблем обеспечиваются за счет обработки детали на современном оборудовании с ЧПУ импортным режущим инструментом.
Ко многим поверхностям детали предъявляются требования взаимного расположения и позиционные допуски, которые обеспечиваются за счет обработки за один установ, что позволяет избежать погрешности установки, что может возникнуть при перезакреплении детали, и за счет применения специально разработанного станочного приспособления. Также требования к расположению поверхностей полностью обеспечиваются современным оборудованием с ЧПУ фирмы Spinner.
Не нашли, что искали? Воспользуйтесь поиском по сайту:
©2015 - 2025 stydopedia.ru Все материалы защищены законодательством РФ.
|