Состав и характеристики основного технологического оборудования ТУС
4.2.1 Технология укладки подводного трубопровода заключается в его наращивании путем последовательной приварки секций труб, находящихся на палубе трубоукладочного судна и последующем спуске на дно. Процесс изготовления и укладки трубопровода организован по циклам: основные технологические операции выполняются в период остановки судна, а в периоды перемещения судна вдоль сваренной трубы выполняется подача трубных секций к рабочим постам.
Состав оборудования и механизмов, задействованных в сборке и последующей укладке трубопровода на дно:
- оборудование для подготовки кромок трубной секции;
- комплекс сварочного технологического оборудования;
- оборудование для контроля качества сварного шва;
- оборудование для ремонта сварного шва;
- изоляционное оборудование;
- транспортирующее оборудование для перемещения трубной секции по технологическому маршруту;
- механизмы для центрирования и стыковки трубных секций укладываемого трубопровода;
- механизмы для удержания трубопровода и регулирования его натяжения (натяжители);
- устройство для спуска трубопровода на дно:
а) стингер – для S-метода укладки трубопровода;
б) подъемная рампа – для J-метода укладки трубопровода;
- оборудование для спуска и подъема трубопровода при неблагоприятных гидрометеоусловиях;
- грузоподъемные механизмы для работы с трубными секциями.
При выборе оборудования технологической линии решающее значение имеет принятая технология сварки. Проведенный анализ сварочных технологий, применяемых при строительстве морских трубопроводов, показал, что на сегодняшний день наибольшее распространение и признание получил метод электродуговой автоматической сварки.
4.2.2 Автоматическая электродуговая сварка
Технология автоматической дуговой сварки имеет следующие основные преимущества:
- качественные и стабильные показатели механических свойств сварного соединения;
- устойчивое качество сварки, даже при незначительных ошибках оператора–сварщика;
- высокий коэффициент наплавки;
- возможность быстрого освоения технологии сварки и обучения операторов–сварщиков непосредственно перед началом проекта.
Немаловажное значение имеет тот факт, что оборудование дуговой сварки применимо для большого диапазона диаметров трубопроводов.
Технологические комплексы оборудования для дуговой сварки обеспечивают высококачественную сварку трубопроводов диаметром до 1600 мм и толщиной стенки до 45 мм, скорость укладки подводного трубопровода при дуговой сварке изменяется от 300 до 5000 м/сут в зависимости от диаметра трубы, толщины стенки трубы и количества сварочных постов, среднее время технологического цикла – 12 минут.
Наибольшее признание получила технология дуговой сварки в среде защитного газа, разработанная компанией CRC–EVANS (США). В процессе реализации проекта «Голубой поток» при сварке трубопровода диаметром 1220 мм по технологии CRC–EVANS был достигнут показатель 207 стыков за двенадцатичасовую смену.
Кроме технологии автоматической сварки, разработанной компанией CRC–EVANS (США), на трубоукладочных судах различных компаний нашли широкое применение технологии автоматической сварки в среде защитного газа, аналогичные технологии CRC:
- «Saturm», Франция;
- «H.C. Price», США;
- «McDermott», США;
- «Arkos – Passo», Италия.
Все эти технологии используют практически одинаковый принцип наложения сварочных слоев с наружной стороны трубы. Отличительной особенностью технологии CRC-EVANS является то, что первый корневой шов выполняется изнутри трубы.
Наряду с применением технологии CRC-EVANS широкое признание получила технология STT - сварка корня шва наружными сварочными головками.
Разновидностью дуговой сварки является сварка под слоем флюса. Технология и качество сварки полностью соответствуют требованиям современных нормативно-технических документов, данный вид сварки применяется для сварки поворотных стыков. Автоматическая сварка под слоем флюса является одной из самых дешевых и эффективных и имеет ряд преимуществ перед другими. К их числу относятся:
- высокий коэффициент и скорость наплавки;
- низкая стоимость расходных материалов;
- возможность сварки труб со стандартной (заводской) разделкой кромок, что позволяет исключить процесс переточки кромок, необходимый для большинства других способов автоматической сварки. Исключение из технологического цикла операции подготовки кромок приводит к уменьшению количества необходимого персонала и позволяет отказаться от закупки дорогостоящего импортного оборудования;
- постоянство пространственного положения точки сварки относительно трубы позволяет упростить процесс управления режимами сварки и добиться более стабильных характеристик по всей протяженности шва;
- отсутствие технологических газов гарантирует отсутствие проблем, связанных с их замерзанием при низких температурах, а также затрат на их хранение и транспортировку к месту проведения работ;
- высокая плотность тока и проплавление, характерные для автоматической сварки под слоем флюса, обеспечивают удаление практически всех сварочных дефектов, образовавшихся при сварке предыдущих слоев шва. Данная особенность в сочетании с высокой стабильностью и качеством автоматической сварки позволяет максимально снизить процент брака по всему объему наплавленного металла.
При использовании технологии автоматической дуговой сварки важным фактором, определяющим стабильное качество стыков, является качество подготовки кромок труб. Специальная разделка кромок (рисунок 4.12), требующаяся для CRC-технологии, позволяет значительно повысить качество сварки, увеличить производительность, снизить объем наплавляемого металла и расход сварочных материалов. Отсутствие открытого зазора уменьшает объем наплавляемого металла, укорачивает время сборки стыка и фактически исключает прожог.
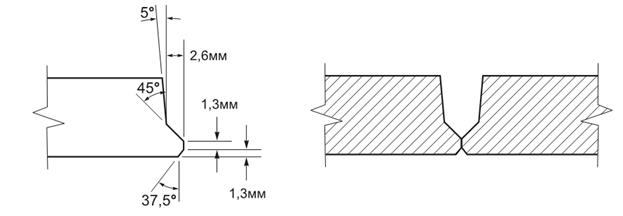
Рисунок 4.12 – Схема разделки кромок и сборки стыка для дуговой сварки
Применение технологии дуговой сварки (в среде защитных газов и под слоем флюса) предполагает очень высокие требования к точности стыковки концов труб перед сваркой, а также наложение на стык от четырех до восьми заполняющих слоев, что существенно увеличивает время технологического цикла формирования сварочного шва.
4.2.3 Контактная стыковая сварка непрерывным оплавлением (КССНО)
Контактная стыковая сварка непрерывным оплавлением (КССНО) получила широкое распространение при прокладке наземных трубопроводов. Этот способ сварки показал себя как наиболее эффективный, сочетающий в себе высокую скорость прокладки трубопроводов и хорошее качество сварных швов. При укладке наземных трубопроводов обеспечивается их горизонтальное положение без деформаций, поэтому снижаются требования к обеспечению показателей ударной вязкости металла в зоне сварки.
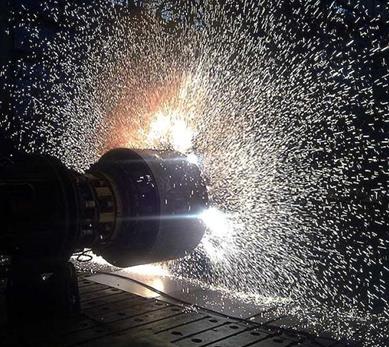
Рисунок 4.13 – Контактная стыковая сварка оплавлением
Метод автоматической контактной стыковой сварки оплавлением имеет следующие преимущества по сравнению с дуговой сваркой:
- возможность организовать однопостовую сварку труб;
- высокая производительность сварки (2-3 мин.);
- небольшое количество обслуживающего персонала;
- нагрев при сварке и остывание сварного соединения происходит одновременно по всему периметру, что позволяет получать сварные соединения с низким уровнем остаточных напряжений;
- не требуется специальная (фигурная) разделка концов труб под сварку;
- не требуется предварительный подогрев свариваемых кромок;
- цикл сварки выполняется автоматически по заданной программе, что исключает какое-либо отклонение режимов сварки от заданных параметров, а процент брака составляет не более 0,3%;
- в соединениях, выполненных методом автоматической контактной стыковой сварки оплавлением невозможно появление дефектов, свойственных дуговой сварке, таких как шлаковые включения, поры, раковины и т.п.;
- сварочные машины для контактной сварки комплектуются компьютерной системой контроля параметров и режимов сварки, что позволяет в 100% случаев выявлять любые отклонения от установленных режимов, которые фиксируются регистрирующей аппаратурой, что позволяет избежать субъективного фактора при их рассмотрении и оценке. После сварки сварочная машина автоматически выдает паспорт на сварное соединение;
- при контактной сварке не используются дорогостоящие сварочные материалы (электроды, сварочная проволока, защитный газ), что исключает необходимость организации специальных рабочих зон для обеспечения условий хранения сварочных материалов и подготовки их к использованию, например: сушка и прокаливание электродов, очистка проволоки, заполнение баллонов инертным газом и пр.
Российское производственно-торговое объединение «CentrPipe» разработало сварочные комплексы для сварки труб в секции (ТКУС) и для сварки секций в нитку трубопровода (ТКУП) методом КССНО. Трубы диаметром 1420 мм сваривают установкой типа ТКУП, названной «Север- 1». В ее состав входят: сварочная машина К-700 с внутренним гратоснимателем, передвижная дизельная электростанция, агрегаты для зачистки концов труб и снятия наружного грата. Все агрегаты установки оснащены системами автоматического управления процессом сварки. Сварочный комплекс «Север-1» позволяет сваривать в смену до 50-60 стыков труб диаметром 1420 мм.
Специалистами института сварки им. Е.О. Патона была разработана и внедрена технология сварки КССНО наземных и морских трубопроводов:
- диаметром от 57 до 720 мм - наружными трубными сварочными машинами;
- диаметром от 720 до 1420 мм - внутритрубными сварочными машинами.
В 1977 г. компания McDermott закупила действующую модель сварочной машины для КССНО. После демонстрации объединенному комитету Американского нефтяного института и проверки пробных швов на трубопроводе АД-1.51 контактная сварка была одобрена для включения в стандарт API 1104. Механические свойства сварного шва, выполненного методом КССНО, нормализованы стандартом API 5/X.
Производительность контактной сварки в значительно выше всех существующих технологий. Компанией McDermott была достигнута производительность – 400 стыков в сутки.
Начиная с 1975 года в СССР строительство магистральных газонефтепроводов осуществлялось, в основном, с использованием сварочных комплексов «Север», которые выпускались на заводе тяжелого электросварочного оборудования в г.Пскове. Было изготовлено более 60 единиц оборудования для сварки труб диаметром 114-159мм, 168 мм, 219 мм, 273 мм, 325 мм, 377 мм, 426 мм, 530 мм, 720 мм, 820 мм и 1420мм, которые успешно работали в системе «Стройтрансгаза» и «Газпрома» в Надыме, Новом Уренгое, Красноярске, Перми. За время эксплуатации комплексов «Север» сварено более 60 тыс. км трубопроводов разного диаметра.
В настоящее время конструкторские службы завода «Псковэлектросвар» разрабатывают сварочные комплексы нового поколения для сварки труб диаметром от 25 до 1220 мм, на заводе разработан и проходит испытания морской сварочный комплекс КСМ-01 для сварки труб диаметром 1220 мм и толщиной стенки 27 мм методом контактной стыковой сварки. Этот комплекс разработан для установки на трубоукладочной барже для строительства морских трубопроводов в условиях окружающего воздуха от минус 40°С до плюс 40°С и влажности воздуха 80% [15].
К недостаткам контактной стыковой сварки следует отнести следующее:
- сварочная машина может выполнять сварку труб ограниченного диапазона диаметров, т.е. для расширения диапазона диаметров свариваемых труб требуется несколько типоразмеров сварочных машин. Например, для сварки труб диаметром от 720 до 1420 мм требуются сварочные машины трех типоразмеров;
- по сравнению с дуговой сваркой метод КССНО является достаточно энергоемким;
- проблемным вопросом является обеспечение показателей ударной вязкости металла в зоне сварного шва. Для повышения показателей ударной вязкости в составе сварочной технологической линии присутствует пост для термообработки и охлаждения стыка. Охлаждение производится орошением зоны стыка водой, для чего требуется подвод к посту охлаждающей жидкости, система сбора жидкости, охлаждения и последующего отвода ее за борт.
Из-за перечисленных недостатков в настоящее время применение КССНО на ТУС не получило широкого распространения. 26-27 июля на территории ЗАО «Псковэлектросвар» был в работе продемонстрирован комплекс КСМ-01 для контактной стыковой сварки трубопроводов с диаметром трубы 1220 мм, предназначенный для работы на ТУС при строительстве морских трубопроводов.
Не нашли, что искали? Воспользуйтесь поиском по сайту:
©2015 - 2025 stydopedia.ru Все материалы защищены законодательством РФ.
|