Устройства для оценки адгезионной прочности локальных пленочных площадок с подложкой
Известно, что кристаллы ППИ имеют на своей поверхности десятки и сотни пленочных контактных площадок. Причем эти пленки имеют различную площадь и всевозможную конфигурацию. Для экспресс-контроля необходимы такие установки, которые позволили бы за короткое время дать оценку адгезионной прочности всех пленочных контактных площадок, расположенных на данной подложке.
Нами разработано устройство для контроля адгезионной прочности локальных пленочных площадок с подложкой. На рис. 3.13 показан общий вид крепления подложки с пленочными площадками, а на рис. 3.14 – схема устройства.
Устройство работает следующим образом. Исследуемая подложка 1 с пленочными площадками 5 помещается на столе крепления 11 и прижимается к столу электромагнитами 10. С помощью несущего кронштейна 23 и основания 8 соосно с исследуемой подложкой 1 над ней располагается матрица вакуумной головки 2, вакуумные отсеки 4 которой находятся над каждой пленочной площадкой 5. После этого на электромагниты 16 системы перемещения вакуумной головки подается напряжение, в результате чего магнитная пластина 15 притягивается к сердечникам электромагнитов и обеспечивается прижатие матрицы вакуумной головки 2 к исследуемой подложке 1.
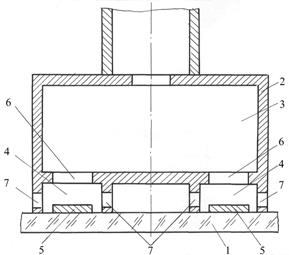
Рис. 3.13. Схема крепления подложки с пленочными площадками: 1 – подложка; 2 – матрица вакуумной головки; 3 – вакуумная камера; 4 – вакуумные отсеки; 5 – пленочные площадки; 6 – калиброванные отверстия; 7 – дросселирующие пазы
Перемещение пластины и прижатие матрицы фиксируется при помощи фоторегистрирующего преобразователя 17, оптическая шторка 18 которого перемещается вместе с магнитной пластиной 15. Сигнал с выхода этого фоторегистрирующего преобразователя поступает на вход усилителя мощности 19, где усиливается и поступает на обмотку электромагнитного клапана 20 и реле времени 21. Электромагнитный клапан 20 срабатывает и открывает вакуумную магистраль: вакуумный насос 25, вакуумную демпфирующую емкость 24, электромагнитный клапан 20, штуцер вакуумной головки 14, общую вакуумную камеру 3. Через систему калиброванных отверстий 6 и дросселирующих пазов 7 воздушный поток отсасывается из системы вакуумных отсеков 4.
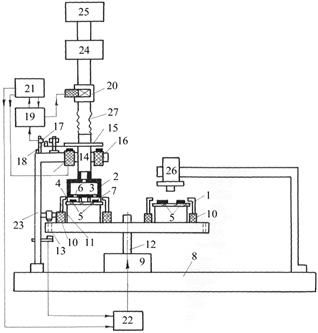
Рис. 3.14. Схема устройства для контроля адгезионной прочности локальных пленочных площадок с подложкой: 1 – подложка; 2 – матрица вакуумной головки; 3 – вакуумная камера; 4 – вакуумные отсеки; 5 – пленочные площадки; 6 – калибровочные отверстия; 7 – дросселирующие пазы; 8 – основание; 9 – исполнительный механизм; 10 – электромагниты; 11 – стол; 12 – вал; 13 – фотопреобразователь; 14 – штуцер вакуумной головки; 15 – магнитная пластина; 16 – электромагнит; 17 – фоторегистрирующий преобразователь; 18 – оптическая шторка; 19 – усилитель мощности; 20 – электромагнитный клапан; 21 – реле времени; 22 – блок совпадений; 23 – несущий кронштейн; 24 – демпфирующая емкость; 25 – вакуумный насос; 26 – микроскоп; 27 – сильфон
За счет возникающего в отсеках разряжения воздушный поток начинает поступать из окружающей среды через дросселирующие пазы 7 внутрь отсеков и, встречая на пути пленочные покрытия, стремится оторвать их от подложки, на которую они нанесены. Размеры дросселирующих пазов зависят от геометрических размеров пленочных площадок. Чем толще напыленная пленка, тем выше может быть дросселирующий паз. Усилие отрыва зависит, кроме размеров дросселирующего паза, от глубины образования вакуума в вакуумной магистрали. Чем глубже вакуум и интенсивнее отсос, тем больше скорость истечения воздушного потока через дросселирующие пазы, тем больше значение усилия отрыва пленки от подложки.
Через определенное время, задаваемое на реле времени, сигнал подается снова на усилитель мощности 19, где усиливается и поступает на электромагнитный клапан 20, который перекрывает вакуумную магистраль. Одновременно с реле времени 21 подается сигнал на снятие напряжения с обмоток электромагнитов 16 системы перемещения вакуумной головки и на блок совпадений 22. В результате этого под действием сжимающей силы растянутого сильфона 27 матрица вакуумной головки 2 отходит от подложки 1. При приходе электрических сигналов на блок совпадения 22 одновременно с реле времени 21 и фоторегистрирующего преобразователя углового положения стола 13 с выхода блока совпадения подается электрический сигнал на исполнительный механизм 9 углового положения стола крепления, который жестко закреплен на валу 12 исполнительного механизма. В результате стол поворачивается на определенный угол, который задается на исполнительном механизме и зависит от числа подложек, закрепленных на столе.
После этого поворота подложка помещается под микроскопом 26, где визуально регистрируются вздутия и отслоения пленок от подложки.
Затем все операции повторяются сначала, при этом синхронизация работы всей установки задается режимом работы реле времени 21.
Для определения величины адгезионной прочности пленки к подложке разработано специальное устройство, схема которого приведена на рис. 3.15. Исследуемую подложку с нанесенными на нее пленочными площадками крепят в кронштейнах 6. Кронштейны через шток 3 соединены с основанием 1.
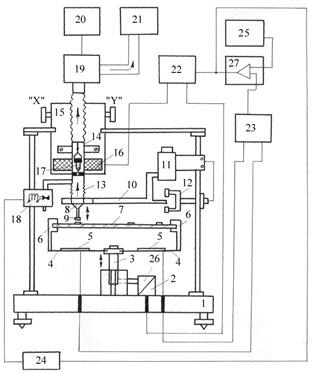
Рис. 3.15. Структурная схема устройства для определения величины адгезионной прочности пленки к подложке: 1 – основание; 2 – исполнительный механизм; 3 – шток; 4 – упругие элементы; 5 – тензодатчики; 6 – кронштейны; 7 – подложка с пленочными площадками; 8 – вакуумный присос; 9 – вакуумная подушка; 10 – рычаг; 11 – механизм вертикального перемещения; 12 – концевой выключатель; 13 – сильфон; 14 – неподвижная часть вакуумного присоса; 15 – двухкоординатный позиционер «Х-Y»; 16 – индуктивный датчик момента прижима присоса; 17 – подвижный цилиндр; 18 – электромагнитный клапан; 19 – вакуумная емкость; 20 – вакууметр; 21 – вакуумный насос; 22 и 24 – усилители мощности; 23 – усилитель; 25 – задатчик механических напряжений; 26 – реверс; 27 – блок измерения величины адгезии
С помощью двухкоординатного позиционера «Х-Y» 15 перемещают вакуумный присос 8 до совмещения подвижной части вакуумного присоса с исследуемой пленочной площадкой на подложке 7. Затем при помощи механизма вертикального перемещения 11 перемещают подвижную часть вакуумного присоса до соприкосновения вакуумной подушки 9 с исследуемой пленочной площадкой. Это вызывает уменьшение потока воздуха, всасываемого в сопло вакуумной подушки вакуумного присоса. Одновременно происходит перемещение подвижного цилиндра 17 индуктивного датчика фиксации момента прижима 16 внутри неподвижной части вакуумного присоса 14 к обмотке индуктивного датчика фиксации момента прижима подвижной части вакуумного присоса. После прижима вакуумной подушки к исследуемой пленочной площадке происходит отключение механизма вертикального перемещения 11 подвижной части вакуумного присоса вследствие соприкосновения рычага 10 с концевыми выключателями 12 ограничителя перемещения. Электрический сигнал с индуктивного датчика фиксации момента прижима 16 усиливается усилителем мощности 22 и поступает на исполнительный механизм вертикального перемещения подложки 2, который перемещает вниз шток 3. Это способствует отрыву подложки от присоса вакуумной подушки, изгибу упругих элементов 4 и деформации тензодатчиков 5. Электрический сигнал с тензодатчиков усиливается усилителем 23 и поступает на первый вход компаратора блока измерения величины адгезии 27. На второй вход компаратора поступает электрический сигнал, соответствующий заданной величине силы отрыва вакуумной подушки от пленки на подложке. Исполнительный механизм 2 перемещает шток 3 вниз до тех пор, пока увеличивающийся в результате деформации упругих элементов электрический сигнал с тензодатчика 5 не достигнет величины сигнала, поступающего с задатчика на второй вход компаратора. Как только эти сигналы сравняются на выходе компаратора появляется электрический импульс, поступающий на электромагнитный клапан 18 через усилитель мощности 24. Электромагнитный клапан срабатывает и соединяет внутреннюю полость вакуумного присоса с атмосферой, в результате чего под действием силы упругого сильфона 13 вакуумная подушка 9 отходит от пленки на подложке. Воздушный поток, протекающий через сопло вакуумной подушки, увеличивается, перемещая вверх подвижный цилиндр 17 индуктивного датчика фиксации момента прижима 16. При этом сигнал с датчика через усилитель мощности поступает на обмотку блока реверса 26 исполнительного механизма перемещения по вертикали исследуемой подложки до выхода подложки в первоначальное положение. После чего с помощью двухкоординатного позиционера «Х-Y» и механизма вертикального перемещения совмещают вакуумный присос с новой пленочной площадкой, и все операции повторяются снова. Задатчиком механических напряжений 25 можно выставить любое значение напряжения на одном из входов компаратора. Чем больше это значение, тем больше должен быть сигнал на другом входе компаратора, поступающий сюда с тензодатчиков 5, а это достигается при большем деформировании упругих элементов 4, следовательно большем перемещении вниз штока 3. Все это ведет к увеличению силы отрыва вакуумной подушки 9 от исследуемой подложки. Таким образом, задавая задатчиком определенный порог напряжения, соответствующий определенной силе отрыва вакуумной подушки от подложки, можно проверить все пленочные площадки на адгезионную прочность без их отрыва от подложки. Задатчиком можно задать такую величину напряжения, которая соответствует отрыву самой пленочной площадки от исследуемой подложки. Глубина вакуума контролируется вакууметром 20 в демпфирующей вакуумной емкости 19, где заданная глубина вакуума достигается с помощью вакуумного насоса 21.
Глава 4. Монтаж полупроводниковых кристаллов к основаниям корпусов
В технологии производства ППИ наиболее трудоемкими являются сборочные операции. Из общей стоимости изготовления ИС на монтажно-сборочные работы приходится около 65 %. Эти затраты являются вполне обоснованными, так как от качества выполнения этих работ во многом зависит эксплуатационная надежность готовых изделий.
В электронной промышленности для присоединения полупроводниковых кристаллов к основаниям корпусов применяют различные способы: пайку припоями и эвтектическими сплавами, приклеивание токопроводящими клеями, крепление кристаллов с помощью легкоплавких или тугоплавких стекол.
Совершенствование существующих, а также разработка новых способов и технологий монтажа кристаллов к основаниям корпусов постоянно находятся в центре внимания разработчиков ППИ. Соединения кристаллов с основаниями корпусов должны обеспечивать заданную механическую прочность, отвод тепла, стойкость к ударам и вибрациям. В тоже время одним из основных условий является экономическая сторона данной технологической операции: снижение трудоемкости и повышение качества.
Выбор способа монтажа полупроводниковых кристаллов во многом зависит от требований, предъявляемых к соединению кристалл-корпус, а также от вида микросварки, применяемой для крепления выводов на кристалле, и режимов герметизации микроприборов. В зоне паяных соединений должны отсутствовать трещины и отслоения покрытия, непропаяные участки.
Одной из основных трудностей, связанных с эксплуатацией автоматических установок для проволочного монтажа, является посадка кристалла в корпус. В полуавтоматических установках операцию коррекции неточности посадки кристалла в корпус выполняет оператор, а пересчет программы позиционирования – ЭВМ.
Независимо от способов крепления кристаллов ППИ на подложки или основания корпусов должно быть обеспечено заданное расположение контактных площадок кристалла относительно контактных площадок корпуса (основания). Погрешность совмещения не должна превышать 25 мкм. Поэтому установку кристалла выполняют с помощью манипулятора, а контроль точности совмещения осуществляют при помощи микроскопа с высоким разрешением.
При монтаже кристалла в корпус на клей, эвтектику или с помощью припоев возможно образование пустот, что ухудшает отвод тепла от кристалла, а тепловое воздействие оказывает влияние на электрические параметры ППИ. Кроме того, снижается механическая прочность контактного соединения, в приконтактных областях кристалла возникают внутренние напряжения, которые могут привести к катастрофическим отказам из-за появления со временем микротрещин в кристалле.
При разработках по созданию новых композиционных материалов, покрытий и припоев для монтажа кристаллов в корпуса, альтернативных золото – кремниевой эвтектике, необходимо проведение исследований физических процессов, приводящих к разрушению кристаллов большой площади. Диагностика технологического процесса сборки БИС, основанная на тензометрическом методе и статистической теории прочности, позволяет с достаточной степенью вероятности предсказать предел прочности для кристаллов БИС различной площади и установить оптимальные значения механических напряжений БИС в корпусе.
Пайка кристаллов
Пайка широко используется в технологии производства ППИ. На операции пайки (монтаж кристаллов, присоединение внутренних выводов, герметизация) приходится более 25 % общей трудоемкости сборочных операций.
Особенности пайки полупроводниковых кристаллов к основаниям корпусов. Качество сборочно-монтажных операций существенно зависит от подготовки поверхности металла корпуса ИС, заключающееся в получении микрорельефа с малой высотой микронеровностей. Установлено, что структура и морфология поверхности исходного металла и покрытия претерпевают существенные изменения на различных технологических операциях изготовления корпуса ИС. Средняя высота микронеровностей поверхности металла основы (ковара) в исходном состоянии составляет 0,4-0,52 мкм, а на заключительной операции гальванического никелирования корпуса – 1,9-2,7 мкм. Снизить величину микронеровностей покрытий до 0,9 мкм можно применением химической полировки материала основы перед нанесением блестящих никелевых покрытий, осаждающихся в нестационарных режимах электролиза из сернокислого электролита с блескообразователями. Кроме того, применение химической полировки металла основы (ковара) перед нанесением блестящих никелевых покрытий позволяет снизить внутренние напряжения с 200-400 до 45-56 МПа.
При сборке кристаллов больших размеров появляются проблемы, связанные как с увеличением размеров соединения кристалл-корпус, так и невозможностью обеспечить высокое качество и надежность монтажа кристаллов с помощью традиционных процессов присоединения кристаллов. Основными трудностями получения качественных паяных соединений являются неплоскостности монтажных площадок, достигающих у металлокерамических корпусов 50 мкм.
Для компенсации неплоскостности основания корпуса при монтаже кристаллов методом контактно-реактивной пайки на золото-кремниевую эвтектику используют прокладки из золотой фольги или сплава золота с кремнием. Толщина фольги обычно составляет 16 или 20 мкм, а площадь колеблется от 60 до 100 % площади кристалла.
При контактно-реактивной пайке с образованием эвтектики золото – кремний получаемое соединение обладает наименьшим тепловым сопротивлением контакта кристалл-кристаллодержатель и имеет максимальную механическую прочность. Качество паяного шва зависит от высоты и количества микронеровностей на поверхности кристалла и корпуса, а также от толщины золотого покрытия. В корпусах ИС высота микронеровностей поверхности основания достигает 6 мкм. Класс чистоты коллекторной стороны кристалла значительно выше, поэтому фактическая площадь физического контакта определяется классом чистоты поверхности корпуса.
При пайке кристаллов больших размеров на эвтектику золото-кремний в кристаллах возникают остаточные механические напряжения, возникающие из-за различия коэффициентов термического расширения кремния и материала корпуса и высокой температуры процесса. Эти напряжения при определенных условиях могут привести к растрескиванию кристаллов при воздействии механических и тепловых нагрузок в процессе испытаний и эксплуатации.
С увеличением размеров кристалла механические напряжения возрастают. Например, для кристаллов размером 3,3´7,2 мм максимальные напряжения достигают 90-100 МПа, а для кристаллов 4,7´9,1 мм – 100-120 МПа.
Одной из причин разрушения кристаллов являются пустоты в зоне соединения кристалла с основанием корпуса. Наличие пустот резко снижает прочность кристаллов и приводит к их разрушению при напряжениях значительно ниже расчетных. Особенно опасны краевые пустоты, которые вызывают разрушения кристаллов в большинстве случаев (95-98 %). Теоретическими расчетами доказано, что с увеличением размеров кристаллов напряжения растут, а следовательно, опасность разрушения от краевых пустот возрастает.
В процессе сборки и испытаний ППИ механические напряжения изделий изменяются в пределах 15 %. Отклонение этих значений вызывает разрушение БИС при напряжениях гораздо ниже расчетных и разработчику потребуется устранять конструктивно-технологические недоработки изделия.
При выборе состава припоя и разработке процесса пайки следует стремиться к созданию паяного соединения с оптимальными фазовым составом, структурой и толщиной переходного слоя на соединяемых поверхностях. Изменять толщину переходного слоя можно введением в припой добавок металлов, которые имеют большое химическое сродство к адгезионно – активному компоненту припоя.
Сопротивление паяных соединений усталостному разрушению, т. е. их долговечность можно повысить за счет уменьшения разницы ТКЛР соединяемых элементов. Например, для повышения долговечности соединений кремниевого кристалла размером 6,6´6,6 мм с корпусом мощного транзистора (ТО-3) предлагается следующее сочетание материалов Si-Pb-Mo-Cu-сталь.
Оценку долговечности паяных соединений в ППИ, например, транзисторах, можно провести, зная количество циклов до разрушения соединений и пластическую деформацию за один цикл. Однако в действительности число циклов до разрушения паяных соединений зависит от конструктивно-технологических параметров и изменяется в широких пределах. Поэтому истинную долговечность паяных соединений необходимо определять экспериментальным путем для конкретной конструкции изделия. В некоторых случаях используются ускоренные испытания (температурные, коррозионные, под токовой нагрузкой и др.).
Проблема обеспечения качества пайки кристаллов к основаниям корпусов усугубляется с увеличением площади кристаллов БИС. Площадь кристаллов, особенно в запоминающих и микропроцессорных устройствах уже в 1991 году составляла 128 мм2 и это увеличение происходит ежегодно. Доля отказов ИС 3-5 степени интеграции по причине разрушения кристаллов составила на входном контроле 267,2 изделий, а при испытаниях и эксплуатации радиоэлектронной аппаратуры – 127,6 изделий на миллион поставленных.
Следует отметить, что повышение качества паяных соединений можно прогнозировать уже на стадии проектирования вследствие продуманного и обоснованного выбора покрытий корпусов и кристаллов под пайку. Следующий этап, на котором возможно повышение надежности паяных соединений – разработка технологической документации, где играют роль выбор оптимальных для данного типа изделия технологии получения покрытий, способов и режимов пайки. На стадии серийного производства неизбежно загрязнение различными примесями припоев, покрытий корпусов и коллекторной стороны кристаллов, что не всегда бывает связано с отклонениями от разработанной технологии, но может носить и объективный характер. Выбор способа пайки кристаллов зависит от конструктивных особенностей ППИ, их электрических и тепловых характеристик, типа корпусов и других показателей.
При креплении полупроводникового кристалла эвтектической пайкой на поверхность корпуса или подложки в заданном месте наносится пленка золота толщиной в несколько микрометров, на которую помещается кристалл. После этого подложка с кристаллом разогревается до температуры, превышающей температуру эвтектики кремний-золото. При нагреве и некотором давлении на кристалл происходит взаимное растворение кремния и золота с образованием эвтектического сплава в зоне соединения. В случае, когда толщина золотой пленки недостаточна между основанием корпуса и кристаллом помещают прокладку эвтектического сплава толщиной 10-20 мкм. Процесс сборки данным способом проводят в защитной среде.
Расчеты минимально необходимой толщины золотого покрытия tAu в зависимости от максимальной высоты микронеровностей tвыст. на поверхности кристаллодержателя показали, что для получения качественного паяного шва необходимо соблюдать следующее условие: tAu ≥ 0,79 tвыст.
Установлено, что использование контактно-реактивной пайки дает положительный результат в случае присоединения кристалла к детали корпуса – золоченому коваровому донышку, прошедшему все стадии технологической обработки при толщине золотого покрытия не менее 6 мкм.
При пайке кристаллов на позолоченную поверхность корпусов прочность паяных соединений на отрыв уменьшается из-за охрупчивания припоя присутствующим в нем золотом. При увеличении толщины золотого покрытия (по подслою химического никеля) прочность паяных соединений падает на 66 % от исходной.
Таким образом, применять под пайку детали с золотым покрытием нужно с определенным сомнением. На границе припой – золотое покрытие детали появляются хрупкие участки, разрушающиеся при эксплуатации изделий. Появление таких дефектов надо постоянно иметь в виду и стараться устранять их соответствующими конструкторскими и технологическими приемами.
Нами проведены исследования монтажа кристаллов БИС с использованием припоя на основе цинка. Оценивалось качество соединений кристалла с основанием корпуса по следующим критериям: площадь смачивания обратной стороны кристалла, прочность соединения «кристалл – корпус» на сдвиг, величина и распределение остаточных механических напряжений, возникающих в кристалле, устойчивость к длительному воздействию температуры (150 ºС) и циклическому изменению температуры в диапазоне от 150 ºС до минус 60 ºС. Рассматривались две группы кристаллов: без подготовки и с предварительным травлением обратной стороны пластины с последующим напылением алюминия толщиной 0,7-1,2 мкм. При пайке кристаллов дополнительно использовались прокладки из припойной фольги того же состава толщиной 20 и 80 мкм и площадью, составляющей 80 % от площади кристалла.
Оценка смачиваемости обратной стороны кристаллов припоем Zn-Al-Ge показывает, что наилучшие результаты монтажа кристаллов достигаются в случае предварительного нанесения на обратную сторону пластины алюминиевого покрытия толщиной около 1 мкм.
Исследования защитных покрытий корпусов КТ-4 при температуре пайки 440±5 ºС показали, что наилучшей термостойкостью обладают покрытия никеля с добавками от 2 до 8 % рения. Другие покрытия окисляются при более низких температурах и расходе защитного газа свыше 50 л/ч.
Покрытия из палладия и его сплавов не растворяются в процессе пайки и хорошо смачиваются припоями при пайке. Например, для гальванического покрытия сплавом Pd-In толщиной 6 мкм паяемость сохраняется при термообработке до 620 ºС, что позволяет использовать сплавы палладия в качестве паяемых покрытий для изделий силовой электроники.
В качестве покрытия под монтажные операции в некоторых приборах применяют серебро. Данный металл используется в качестве конечного покрытия коллекторной поверхности кристалла и корпуса. На пластину с кристаллами серебро наносят напылением, а на корпуса гальваническим способом. При этом серебряное покрытие на корпуса наносят локально на участки под пайку кристаллов и разварку внутренних выводов.
Серебряные покрытия существенно снижают паяемость при естественном старении под действием окружающей атмосферы. В чистом воздухе на серебре имеются оксидные пленки толщиной 10-20 нм. В атмосферных условиях на поверхности образуется труднорастворимое соединение сульфид серебра (Ag2S).
Технологам известно, что нельзя применять подслой серебра под покрытия золотом, палладием и родием, а использовать под данные покрытия подслой никеля. Подслой никеля обеспечивает получение покрытий с заданными характеристиками, хотя и требует надлежащей организации техпроцесса, обеспечивающего квалифицированным персоналом.
В производстве диодов Шоттки в качестве барьерных металлов применяют Al, Ni, Pt, Pd, Ti, Va, W, Mo и силициды этих металлов. Из перечисленных металлов, при одинаковых требованиях к электрическим характеристикам на прибор, рекомендуется применять Mo, который имеет хорошую адгезию к кремнию и SiO2 и близкий к кремнию ТКЛР. В процессе исследований и испытаний установлено, что использование на планарной стороне кристаллов диодов Шоттки пленочной металлизации Мo-Ni-Niхим-Sn обеспечивает изготовление изделий высокой надежности. При этом кристаллы диода Шоттки с применением в качестве барьерного металла Мо должны изготавливаться с применением LOCOS-технологии.
Для соединения кремниевых кристаллов с медным основанием корпусов мощных транзисторов применяются композиционные припои системы свинец – никель. Введение в зазор между кристаллом и теплоотводом никелевой губчатой прокладки толщиной 0,1-0,2 мм и пористостью 65-80 %, пропитываемой в процессе пайки свинцово-содержащим припоем, повышает термическую стабильность и термоциклостойкость паяного контакта. Рекомендуется использовать свинцовые припои, армированные никелевой губкой, в конструкциях типа кремний – медь, кремний – медь – сталь.
При пайке кристаллов мощных транзисторов достаточно трудно обеспечить получение качественного соединения без пор и пустот. С целью исключения этих дефектов процесс пайки кристалла к основанию корпуса предлагается вести в вакууме, а после расплавления припоя впускать под колпак воздух.
Для увеличения площади спая между кристаллом и корпусом на верхней плоскости корпуса формируют V-образные канавки глубиной 25-75 мкм, располагаемые друг от друга на расстоянии 0,25-1 мм. В случае использования корпусов с канавками необходимо при пайке корпус или кристалл подвергать воздействию ультразвуковых или низкочастотных колебаний. Механические колебания должны быть направлены вдоль канавок. В противном случае при пайке кристаллов больших размеров V-образные канавки являются очагами непропаев (рис. 4.1).
Рис. 4.1. Рентгенограмма паяного соединения кристалла с корпусом с V-образными канавками. Размер кристалла 5,1×5,6 мм.
При пайке кристаллов размеров менее 3´3 мм используют как ультразвуковые, так и низкочастотные колебания, а при пайке кристаллов больших размеров применяются в основном низкочастотные колебания с амплитудой до 0,5-0,8 мм.
Пайка в вакууме имеет ряд преимуществ. Она обеспечивает образование боле плотных и прочных швов, чем пайка в инертных и активных газовых средах, в результате дегазации жидкого припоя.
Качество пайки кристалла с основанием корпуса во многом зависит от места расположения припоя перед пайкой. Возможно традиционное расположение прокладки припоя непосредственно под кристаллом, однако в процессе пайки оксидные пленки и загрязнения на поверхности прокладки при расплавлении остаются в зоне шва, что ухудшает смачиваемость припоем поверхности кристалла и основания корпуса, нарушает сплошность шва, а это, в свою очередь, приводит к ухудшению теплопроводности шва и снижению надежности ППИ.
Для улучшения смачивания припоем паяемой поверхности кристалла и основания корпуса широко используют капиллярный эффект заполнения зазора припоем в процессе пайки кристалла. Перед пайкой в непосредственном касании одной из боковых граней кристалла располагается навеска припоя в виде шарика (рис. 4.2). Детали фиксируются относительно корпуса специальной кассетой. Кассету со сборками помещают в печь, где при температуре пайки происходит расплавление припоя, который за счет капиллярных сил заполняет микрозазор между коллекторной стороной кристалла и корпусом, смачивает эти поверхности и при кристаллизации образуется паяный шов. Характерной особенностью этого процесса является то, что оксидные пленки и загрязнения остаются за пределами паяного шва – в месте первоначального расположения навески припоя.
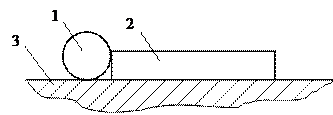
Рис. 4.2. Схема напайки кристалла на никелированное основание с использованием капиллярного эффекта: 1 – навеска припоя; 2 – кристалл; 3 – основание
К недостаткам указанного способа следует отнести температуру нагрева при пайке значительно выше температуры плавления припоя с целью разрушения оксидной пленки припоя и обеспечения его капиллярного течения. Кроме того, при пайке кристаллов больших размеров, особенно в ППИ для силовой электроники, невозможно получить площадь спая равную площади кристалла. Из-за неполного смачивания соединяемых поверхностей в паяном шве образуются непропаи, которые снижают мощность рассеивания приборов.
Известен способ изготовления ППИ, по которому к подложке присоединяют кристалл с помощью припоя, который расплавляется между подложкой и полупроводниковым кристаллом. При этом над подложкой устанавливают кожух, который соединен с устройством для понижения давления. С помощью кожуха над нагревателем, на который устанавливают подложку, создают пониженное давление и заполняют кожух газообразным азотом или водородом.
В технологии производства ППИ широко используют пайку кремниевого кристалла с использованием никелевых (или медных) пористых сред (рис. 4.3).
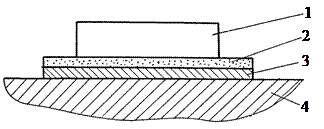
Рис. 4.3. Пайка кристалла с использованием пористых сред: 1 – кристалл; 2 – пористая металлическая прокладка; 3 – свинцовый припой; 4 – основание корпуса
Объем навески припоя определяется расчетным путем с учетом пористости фильтрующего элемента, его размеров и уточняется экспериментальными исследованиями.
Пайка кристаллов мощных транзисторов на мягкий припой более предпочтительна, нежели эвтектическая контактно-реактивная, так как в жестких эвтектических швах, особенно при пайке кристаллов больших размеров, могут возникать внутренние напряжения, приводящие к разрушению кристалла. В паяных соединениях кристаллов, образованных мягкими припоями, внутренние напряжения частично релаксируются и разрушения кристаллов даже при циклических испытаниях не наблюдаются.
Не нашли, что искали? Воспользуйтесь поиском по сайту:
©2015 - 2025 stydopedia.ru Все материалы защищены законодательством РФ.
|