Инструмент для монтажа выводов и кристаллов
Назначение:
1. Инструмент для монтажа выводов: присоединение золотой и алюминиевой проволоки или лент методом ультразвуковой, термозвуковой и термокомпрессионной сварки.
2. Инструмент для монтажа кристаллов: посадка кристаллов на эвтектику, клей и мягкие припои.
Основные технические характеристики
Диаметр проволоки, толщина ленты
| от 0,012 до 0,8 мм
| Размеры кристаллов
| от 0,3´0,3 до 20´20 мм
| Материал инструмента
| карбид, вольфрама, рубин, нихром, керамика
| Примечание: разработка и производство ОКБТЭМ-СО (г. Минск, Республика Беларусь)
Глава 3. Методы и устройства для оценки адгезии пленок к подложкам
Надежность работы различных устройств с пленочными элементами (ИС, микросборки, устройства на поверхностных акустических волнах и др.) помимо функциональных параметров пленок и подложек зависят от прочности адгезии пленок к подложкам.
Известно, что кристаллы ППИ имеют на своей поверхности десятки и сотни пленочных контактных площадок. Причем эти пленки имеют различную площадь и всевозможную конфигурацию. Для экспресс-контроля необходимы такие установки, которые позволили бы за короткое время дать оценку адгезионной прочности всех пленочных контактных площадок, расположенных на данной подложке.
В производстве многих ППИ последовательно наносят пленки различных материалов на подложку, т. е. используют многослойные тонкопленочные структуры. Адгезия пленок между собой, а также пленок с подложкой является основным параметром, определяющим качество изделий и их надежность. На адгезионную прочность пленок с подложкой влияют остаточные напряжения, пограничные слои, геометрия и физические параметры адгезива и подложки.
Для повышения качества ППИ необходимо оценивать адгезию пленок с подложкой на всех этапах технологического процесса производства: образования пленок, фотолитографии для получения заданной топологии рисунка, наращивания слоя проводника и монтажа кристаллов и внутренних выводов. Выбор оптимальных параметров производства тонкопленочных изделий осложняется отсутствием достаточно совершенной методики измерения адгезионной прочности.
Адгезия* – это связь или взаимодействие между поверхностями двух разнородных контактируемых тел. Различают адгезию частиц и жидкости к твердым поверхностям и адгезию пленок и покрытий. Существует принципиальное отличие адгезии пленок от адгезии частиц и жидкости. Адгезия пленок количественно определяется методами, основанными на отрыве пленок. Усилие, необходимое для отрыва пленок, тратится не только на преодоление адгезии, но и на другие побочные явления. Таким образом, истинную адгезию пленки с подложкой существующими методами практически невозможно определить. Кроме того, величина адгезии не поддается точному расчету.
Мерой адгезионной прочности σ (Па) является удельное значение силы, измеренное при отрыве пленок
σ = Р / S,
где Р – сила, измеренная при отрыве (Н); S – площадь разрушенного контакта (мм2).
Методы определения адгезионной прочности пленок с подложкой разделяются на две группы: разрушающие и неразрушающие. Следует отметить, что результаты оценки адгезионной прочности, полученные различными методами, в некоторых случаях имеют противоречивые результаты. В каждом конкретном случае нужно выбирать свои, наиболее приемлемые методы определения адгезионной прочности.
Неразрушающие методы
Проблема выбора оптимальных параметров производства тонкопленочных изделий осложняется отсутствием достаточно совершенной методики измерения адгезионной прочности. Измерение адгезионной прочности неразрушающими методами основано на корреляции между адгезионной прочностью пленки с подложкой и некоторыми физическими свойствами адгезионного соединения (электросопротивление, электроемкость, поглощение и др.). Неразрушающие методы контроля в настоящее время мало применяются в промышленности из-за невысокой точности и неоднозначной зависимости силы сцепления от контролируемой физической величины. Разработка надежных методов неразрушающего контроля является особенно актуальной для всех отраслей промышленности, выпускающих изделия электронной техники. К основным методам неразрушающего контроля относят следующие: ультразвуковой, фотометрический, рентгеновский и метод измерения емкости.
Для измерения адгезии тонких пленок к подложке в системе подложка-пленка ультразвуковым методом возбуждают механические колебания ультразвуковой частоты до момента отделения пленки от подложки. С целью уменьшения погрешности измерения горизонтальные механические колебания ультразвуковой частоты прикладывают к пленке через прижатый металлический проводник. В данном случае при увеличении амплитуды возбужденных колебаний ультразвуковой частоты пленка захватывается металлическим проводником, в результате чего проводник и пленка перемещаются относительно поверхности подложки. Для реализации этого способа можно использовать промышленные установки для ультразвуковой микросварки проволочных проводников.
Известен неразрушающий способ измерения прочности сцепления тонких металлических слоев посредством акустического анализа. Способ отличается тем, что поверхностный бесконтактный нагрев осуществляется специальным элементом, который излучает акустический сигнал. При данной температуре элемента меньшая прочность сцепления вызывает появление более раннего и сильного звукового излучения. Используя калибровочные данные, рассчитывают по сумме импульсов и температуре элемента фактическую прочность сцепления пленки с подложкой.
Известен способ оценки адгезии пленки к подложке, при котором пленку освещают сначала в недеформированном, а затем в деформированном состоянии, и по изменению оптических свойств одного из элементов адгезионного соединения судят об ацгезии пленки к подложке. С целью расширения вида исследуемых материалов пленку можно освещать светом с изменяющейся длиной волны.
Для определения степени адгезии электропроводящих покрытий на электропроводящем основании разработано устройство, которое снабжено высокочастотным нагревателем и измерителем температуры в зоне контроля. Контролируемый участок пленки с подложкой нагревают и одновременно возбуждают вихревые токи. В момент нарушения сцепления пленки с подложкой за счет сил Лоренца покрытие начинает колебаться, что фиксируется с помощью пьезоэлектрического преобразователя. Температура в зоне контроля измеряется в момент возникновения колебаний и служит количественной характеристикой степени адгезии пленки с подложкой.
Для определения адгезии проводящих или полупроводниковых пленок к подложкам разработано устройство (рис. 3.1), позволяющее проводить неразрушающий контроль. При испытании адгезионной прочности через исследуемый элемент подают электрический ток и производится регистрация низкочастотных флуктуаций напряжения детектором 5 и фильтром низких частот 6. Компенсация напряжения до нулевого значения осуществляется блоком 7. При воздействии лазерного луча на исследуемую пленку с подложкой пороговым элементов 9 производится регистрация превышения сигналов порогового уровня, пропорционального интенсивности низкочастотных флуктуаций, предшествующей нарушению адгезии. Блоком 10 производится отключение лазера 11 и фиксация значения энергии луча, соответствующего величине адгезии. Контроль низкочастотных флуктуаций и их изменение при воздействии усилий, нарушающих адгезию, позволяет определить не только момент нарушения адгезии, но и момент, предшествующий отрыву.
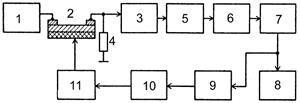
Рис. 3.1. Схема устройства для определения адгезии: 1 – источник постоянного напряжения; 2 – пленка с подложкой; 3 – низкочастотный широкополосный усилитель; 4 – балластная нагрузка; 5 – детектор; 6 – фильтр низкой частоты; 7 – блок первоначальной компенсации; 8 – индикатор; 9 – пороговый элемент; 10 – блок контроля; 11 – лазер
Известно устройство для испытания на адгезию токопроводящих пленок на диэлектрической подложке (рис. 3.2), которое содержит источник напряжения 1, электростатический зонд 2, привод осевого перемещения 3, держатель 4 для размещения подложки 5 с пленкой 6. Контроль адгезии осуществляется системой 7, представляющей собой измеритель электрической емкости между пленкой и зондом. Основным элементом данного устройства является электростатический зонд 2 в виде металлического стержня с отполированной до 14 класса чистоты рабочей поверхностью. При этом поверхность зонда покрывается оксидами металлов, например Al2O3, Ta2O5, TiO2.

Рис. 3.2. Схема устройства для испытания на адгезию токопроводящих пленок на диэлектрической подложке
Принцип работы устройства заключается в создании электростатического поля, под действием которого возникают пондемоторные силы прижатия зонда к токопроводящей пленке. Если силы прижатия зонда к пленке превышают силу сцепления (адгезии) пленки с подложкой, то в результате приложения усилия отрыва произойдет отслоение пленки от подложки. Использование измерителя емкости в качестве контрольного устройства за отрывом пленки позволяет по шкале прибора фиксировать момент отрыва.
Разрушающие методы
К разрушающим методам контроля адгезионной прочности пленки с подложкой можно отнести следующие: нормального отрыва и отслаивания, скрайбирования, вдавливания специального индентора, воздействия электрического и магнитного полей, лазерный, а также центрифугирования, вибрации, истирания, многократного изгиба, термический и электрохимический.
Наиболее широкое распространение для производственных и экспериментальных целей получили следующие методы измерения адгезионной прочности пленок: нормального отрыва и отслаивания, а также скрайбирования.
Метод нормального отрыва является основным при оценке адгезионной прочности пленок. Различают две разновидности отрыва: метод одновременного отрыва, при котором сила отрыва направлена перпендикулярно к площади пленки, и метод последовательного отрыва (метод отслаивания), при котором сила отрыва направлена под углом к поверхности пленки. Отрыв обычно осуществляют с помощью штыря, цилиндра или проволоки, которые соответствующим образом прикрепляются к поверхности пленки.
Для определения адгезионной прочности хрупких покрытий толщиной до 150 мкм разработан способ, когда в подложке выполняют отверстие, в котором размещают штифт заподлицо с поверхностью подложки, а затем наносят на их общий торец испытуемое покрытие. Адгезионную прочность покрытия определяют по величине отрывающей нагрузки от штифта и по площади отрыва покрытия. Причем измеряют площадь боковой конической поверхности, образовавшейся в покрытии при отрыве.
Известны способ и устройство для определения адгезионной способности пленки, при этом на задней поверхности подложки, покрытой тонкой пленкой, вытравлено отверстие. Образец закрепляется на подложке микрозонда, при этом кончик стержня совмещается с центром пленки. С помощью специального привода стержень прижимают к пленке. Момент отрыва пленки определяется нагрузочным устройством. При этом с помощью микроскопа измеряется радиус круговой части пленки, оторванной от материала подложки.
В некоторых случаях для измерения адгезионной прочности многослойного материала на поверхности покрытия размещают форму, в которую заливают припой для формирования держателя. Цилиндрический участок отливки захватывают цангой прибора и прикладывают растягивающее усилие в направлении, перпендикулярном к этим слоям.
Разработан способ испытания прочности связи покрытия с подложкой, при котором подложка устанавливается неподвижно в заданном направлении. Затем к покрытию с помощью специального захвата прикладывают возрастающее усилие, измеряя величину этого усилия и возникающую в результате этого деформацию. Испытание прекращают в том случае, когда скорость деформации в функции возрастающего усилия начинает уменьшаться.
Для определения прочности на отрыв контактных площадок печатной платы разработано специальное приспособление, которое можно устанавливать на разрывную машину модели РМУ – 0,05.
Известен способ контроля адгезии пленки к подложке, по которому в пленке создают решетку надрезов рабочим инструментом и по площади или количеству отслоившихся ячеек пленки оценивают адгезию. Для увеличения достоверности контроля решетку надрезов можно создавать методом ультразвукового резания, используя при этом инструмент с решетчатой формой рабочей поверхности концентратора.
Для сокращения времени при испытании группы пленок используют трафарет, с помощью которого наносят на подложку несколько одинаковых, рядом расположенных пленок. Пленки могут иметь форму круга, квадрата, элементов микросхем и т. п. Затем подложку с нанесенными на нее пленками погружают в активную жидкую среду и определяют время отслаивания заданного количества пленок. Объективным показателем качества адгезии считается время отслоения половины одновременно испытуемых пленок от их общего количества.
Сцепление пленки с подложкой также определяют путем отделения наклеенной на поверхность пленки клейкой полосы. С помощью специального устройства клейкая полоса отрывается через промежуточно включенный динамометр под определенным углом к поверхности пленки и фиксируется усилие, показанное динамометром.
Адгезию между изоляционными и металлическими слоями в различных приборах на полупроводниковых кристаллах осуществляют с помощью специального измерительного участка. Измерительный участок, имеющий размеры кристалла, может быть сформирован совместно с рабочим кристаллом на пластине. В процессе испытания на отслаивание под углом 90° слои испытательного участка последовательно отделяют вдоль непрерывной поверхности раздела.
Для оценки прочности сцепления гальванических покрытий применяют также метод нагрева согласно ГОСТ 9.302-79. Адгезию никелевых покрытий на сплавах меди контролируют по вспучиванию пленок или отслаиванию после нагрева до 250 °С и последующего охлаждения на воздухе. Установлено, что нагрев до такой температуры с охлаждением на воздухе не всегда выявляет покрытия с низкой прочностью сцепления. Для этих целей рекомендуется использовать более высокие температуры нагрева и скорости охлаждения.
Вдавливание индентора иногда осуществляют в пластичный металлический материал на некотором расстоянии от края пленки. Отпечаток формуют таким образом, чтобы в результате смещения основной материал образовывал выпуклость на краю пленки. Прочность сцепления характеризует состояние покрытия на этом утолщении.
Для повышения точности и наглядности при определении начала образования трещины в покрытии в последнее можно вдавливать два индентора с различной конусностью.
Для оценки адгезии тонких металлических пленок на стекле, кварце и других прозрачных материалах методом царапаний закругленной иглой разработана специальная приставка к микроскопу МИМ-8М. Данное устройство (рис. 3.3) позволяет вести микроскопическое наблюдение зоны царапаний со стороны прозрачной подложки в процессе испытания. Испытания на пленках меди и алюминия, нанесенных термическим испарением на стекла, показали большую точность в определении нагрузки при отслаивании покрытий. Следует отметить, что данная методика неприменима для оценки адгезии между отдельными слоями при многослойной металлизации.
При определении адгезионной прочности пленок с подложкой методом царапаний необходимо учитывать промежуточный слой загрязнений между пленкой и подложкой. Данный слой существенно ослабляет сопротивляемость системы пленка – подложка внешним нагрузкам. Например, при исследовании адгезионной прочности серебряных пленок, нанесенных на корундовые подложки, наличие на границе раздела промежуточного слоя загрязнений приводит к искажению количественной информации о степени адгезионного взаимодействия системы. Рекомендуется перед напылением пленок проводить обработку подложек в тлеющем разряде, что приводит к заметному снижению уровня поверхностных загрязнений подложки.
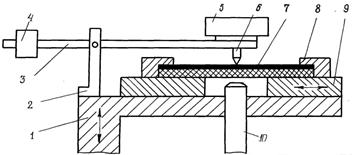
Рис. 3.3. Схема приставки к металлографическому микроскопу МИМ-8М для наблюдения следов царапаний в процессе испытания: 1 – основание столика микроскопа; 2 – стойка; 3 – коромысло; 4 – противовес; 5 – груз; 6 – игла; 7 – образец; 8 – держатель образца; 9 – столик микроскопа; 10 – объектив
Для измерения адгезии тонких пленок к ситалловым подложкам методом царапаний иглой разработана специальная установка. Адгезия определяется путем автоматического измерения критической нагрузки, необходимой для получения чистого следа на подложке. Погрешность при измерении адгезии не превышает 10 %.
Для контроля адгезионных свойств покрытий методом царапания разработан прибор, особенностью которого является то, что поперечное сечение острия царапающего элемента образует острый угол с направлением его перемещения, а его осевая линия наклонена в этом направлении.
Известен способ определения адгезионной прочности коммутационных сплавов с термоэлементами, при котором через соединение пропускают электрический ток таких величины и направления, чтобы вследствие эффекта Пельтье соединение нагревалось или охлаждалось до требуемой температуры. При каждом значении температуры к одной из сторон соединения прикладывают отрывающую нагрузку, в результате чего получают зависимость адгезионной прочности покрытия от температуры. Это позволяет определять адгезионную прочность коммутационных сплавов с термоэлементами при режимах эксплуатации изделий (рис. 3.4).
Для контроля адгезии пленки к подложке фиксируют измерение в момент отрыва ее электросопротивления на участке длиной не более 10 мм. В качестве отрывного элемента используется электрод с диэлектрическим покрытием на поверхности, предназначенной для контактирования с пленкой, а его крепление к пленке осуществляется путем подключения электрода к одному полюсу источника постоянного тока, а исследуемой пленки – к другому (рис. 3.5).
Известен способ определения адгезии металлических пленок к диэлектрическому основанию, при котором через пленку пропускают ток, при этом основание с пленкой находится в зоне действия магнитного поля. Зафиксировав величину тока и напряженность магнитного поля в момент отрыва пленки от подложки, расчетным путем определяют величину адгезии.
Снизить трудоемкость определения адгезионной прочности токопроводящих покрытий к подложкам можно путем размещения подложки с покрытием между двумя электродами в поле действия электрического разряда. По величине пятна разрушенного покрытия судят об адгезионной прочности пленок. Особенностью данного способа является то, что подложку размещают в вакуумной камере, корпус которой используют в качестве положительного электрода, а покрытие электрически соединяют с отрицательным электродом. В качестве воздействующего на покрытие разряда используют электродуговой разряд.
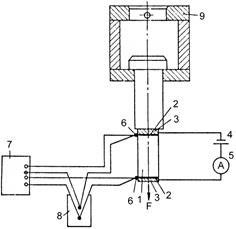
Рис. 3.4. Схема для определения адгезионной прочности покрытия: 1 – подложка; 2 – коммутационный сплав; 3 – медные пластины; 4 – источник постоянного тока; 5 – амперметр; 6 – термопара; 7 – вольтметр; 8 – сосуд Дьюара; 9 – захват разрывной машины
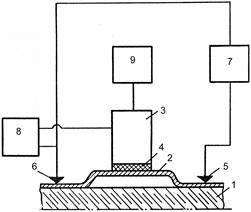
Рис. 3.5. Схема измерения адгезии металлической пленки к диэлектрической подложке: 1 – диэлектрическая подложка; 2 – металлическая пленка; 3 – электростатический зонд; 4 – оксидный слой; 5, 6 – прижимные контакты; 7 – микрометр; 8 – источник напряжения; 9 – динамометр
Разработана установка для определения электроадгезионной прочности сцепления токопроводящих покрытий с полупроводниковыми подложками (рис. 3.6). Регистрирующее устройство показывает электроадгезионную прочность токопроводящего покрытия с полупроводниковой подложкой в зависимости от величины приложенного напряжения.
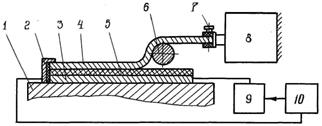
Рис. 3.6. Установка для определения прочности сцепления покрытия с подложкой: 1 – основание; 2 – съемный электрод; 3 – электрод; 4 – покрытие; 5 – полупроводниковая подложка; 6 – ролик; 7 – зажим; 8 – регистрирующее устройство; 9 – коммутатор; 10 – источник электрического напряжения
Для определения адгезии тонких проводящих пленок известен способ, по которому между покрытием на подложке и дополнительным электродом, расположенным на расстоянии, исключающем электрический пробой между ними, прикладывают возрастающее по амплитуде напряжение. Об адгезии судят по величине напряженности электрического поля между электродами в момент отрыва токопроводящего покрытия от подложки.
Адгезию электропроводящей пленки к диэлектрической подложке определяют также путем размещения с противоположной стороны диэлектрической подложки контрольного электрода. Между пленкой и электродом прикладывают переменное электрическое напряжение, повышая амплитуду от нуля до напряжения ионизации. Величина ионизации зависит от неоднородности переходного слоя между металлической пленкой и диэлектрической подложкой, т. е. от качества адгезии. На рис. 3.7 представлена схема реализации данного способа. В качестве электрода можно использовать электролит, смачивающий подложку. Исследования, проведенные на образцах ситалла с напыленными на них металлическими покрытиями, показали возможность использования данного способа в технологии производства изделий электронной техники.
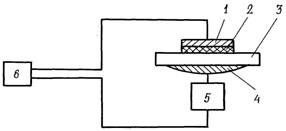
Рис. 3.7. Устройство для определения адгезии электропроводящей пленки к диэлектрической подложке: 1 – пленка; 2 – переходной слой; 3 – подложка; 4 – электрод; 5 – измеритель ионизации; 6 – источник питания
Известен способ контроля адгезии тонких металлических пленок к диэлектрической подложке, при котором подложку с пленкой размещают в электромагнитном поле сверхвысокой частоты. При этом способе используется разница волновых сопротивлений металлической пленки и диэлектрической подложки. Электромагнитная волна, пройдя пленку, отражается от поверхности диэлектрической подложки, в результате чего на границе раздела металл – диэлектрик возникают пондеромоторные силы, которые и отрывают пленку от подложки. Частота электромагнитного поля варьируется в пределах 0,6-40000 ГГц. Адгезию тонкой металлической пленки к диэлектрической подложке определяют в момент отрыва по величине напряженности электромагнитного поля.
В других случаях диэлектрическую подложку с пленкой располагают в электромагнитном поле сверхвысокой частоты таким образом, чтобы поверхность пленки находилась со стороны источника электромагнитного поля. Между источником поля и пленкой размещают поглотитель мощности электромагнитного поля (например дистиллированную воду) и прикладывают к источнику электромагнитного поля постоянное напряжение сверхвысокой частоты. Уменьшают объем поглотителя вследствие испарения воды до тех пор, пока не произойдет отслоение пленки. Измерением объема поглотителя мощности электромагнитного поля в момент отслоения пленки от подложки определяют адгезионную прочность сцепления металлической пленки с диэлектрической подложкой.
С целью повышения точности контроля качества адгезии покрытий с подложками размещают исследуемые образцы в зоне действия полей токов высокой частоты и ультразвуковых колебаний и нагревают локальные участки соединения пленки с подложкой. При взаимодействии электромагнитной волны с ультразвуковой волной в соединении проявляется эффект магнитострикции. При соответствующих режимах происходит механическое разрушение слоя покрытия (трещинообразование, отслоение или вспучивание). Соединение покрытие-подложка считается годным в случае отсутствия на поверхности покрытия вышеуказанных дефектов.
Повысить точность определения адгезии металлических пленок к поверхности подложки, выполненной из оптически прозрачного материала, можно с помощью специально разработанного устройства. Для этого подложку с пленкой помещают в ванну с гиротропной жидкостью, возбуждают в этой жидкости ультразвуковые колебания концентратором до возникновения в металлической пленке зон разрушения. Появление и характер зон разрушения регистрируют при помощи потока поляризованного излучения от источника, проходящего через подложку, зоны разрушения пленки и гиротропную жидкость и падающего на зеркальную поверхность концентратора. Для определения сил сцепления металлической пленки с полимерной подложкой разработана специальная установка, состоящая из трех блоков: акустического, гидравлического и регистрационного. Интенсивные ультразвуковые колебания, проходя через жидкость, вызывают кавитационные явления большой разрушительной силы, которые и отрывают пленку от подложки. Величину адгезии рассчитывают по числу кавитационных пузырей в единице объема, давлению, создаваемому пузырями при их захлопывании, и количеству снятого с пленки металла.
Для контроля адгезии металлической пленки к диэлектрической подложке в пленке выполняют сквозные прорези по спирали с непрерывно уменьшающимся шагом до отделения пленки от подложки. С целью повышения точности определения адгезии прорези необходимо наносить по логарифмической сходящейся или расходящейся спирали, начало и конец которой переходят в окружности. Адгезию контролируют измерением емкости или электросопротивления участка пленки между окружностями.
Используется метод определения адгезии тонкой пленки к подложке, в котором используется импульсное излучение (сфокусированный электронный или лазерный луч), направляемое на подложку со стороны пленки до ее расплавления. В этом случае величину адгезии определяют по размерам оплавленной зоны, т. к. между размером оплавленной зоны и адгезией пленки с подложкой существует тесная корреляционная связь. На рис. 3.8 показана зависимость площади оплавления пленок алюминия электронным лучом диаметром 0,5 мм с энергией 5·10 Вт/см в импульсе длительностью 1 мс от ее адгезии к подложке.
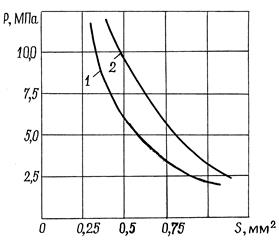
Рис. 3.8. Взаимосвязь площади оплавленной зоны пленки алюминия с ее адгезией к подложке из кремния (1) и моноокиси кремния (2)
С целью повышения точности при контроле вакуумно-напыленных пленок Cr, Cu, Au и др. нагрузку создают путем сканирования непрерывным лучом лазера, имеющим плотность мощности от 105 до 106 Вт/см2 и скорость сканирования, равную скорости распространения звука в материале пленки.
Для ускорения контроля адгезии пленок к подложке на участках протяженностью не более 100 мкм воздействуют на пленку с помощью не менее двух одинаковых источников разрушения в виде лазеров. Причем источники разрушения располагают один от другого на расстоянии l, определяемом из условия
l ≥ ,
где α – коэффициент теплопроводности материала подложки; t – длительность воздействия источников разрушения.
При размещении источников разрушения на расстоянии l меньше указанного пленка расплавляется при наложении импульсов один на другой из-за отсутствия достаточного теплоотвода в материал подложки. Для количественной оценки величины адгезии сравнивают минимальные расстояния, при которых разрушается область пленки между двумя оплавленными зонами.
Прочность сцепления пленки с подложкой можно определять по коэффициенту отражения теплового потока от поверхности покрытия. Для этого на поверхность покрытия воздействуют тепловым потоком, например лучом лазера. Сравнивают коэффициент отражения с таким же коэффициентом, измеренным на эталонном соединении, и по результатам сравнения судят о степени адгезии пленки с подложкой. Качество сцепления пленки с подложкой тем лучше, чем больше величина коэффициента отражения теплового потока от поверхности покрытия контролируемого соединения совпадает с величиной коэффициента отражения теплового потока эталонного образца. Разработан образец для определения прочности сцепления покрытия с подложкой при отслаивании, условия изготовления которого позволяют приблизиться к технологии монтажа ИС с планарными выводами на печатной плате. В этом случае на поверхности подложки формируют ряд параллельных полосок покрытия разной ширины. Затем поверхность покрытия сканируют лазерным лучом и формируют строчную развертку лазерного луча. Адгезионную прочность определяют по тепловому воздействию в данных участках пленок.
Не нашли, что искали? Воспользуйтесь поиском по сайту:
©2015 - 2025 stydopedia.ru Все материалы защищены законодательством РФ.
|