|
Олово – висмутовое покрытие
В технологии производства ППИ на сборочных операциях широко используется сплав олово-висмут как в виде покрытий, так и в виде припоев.
Покрытие сплавом Sn-Bi в некоторых случаях применяют вместо серебра. При соответствующих режимах электролиза покрытия сплавом Sn-Bi получают с мелкозернистой структурой и пониженной твердостью. Блестящие покрытия сплавов Sn-Bi наносятся на корпуса ППИ из меди и других металлов. Состав электролита (г/л): сернокислое олово 30-45; сернокислый висмут 0,5-1; серная кислота 120-140; смачиватель ОС-20 4-5; формалин (40 %) 5-10 (мл/л); лимеда Sn-2 5-10 (мл/л); температура электролита 18-25 ºС; РН раствора 1-2; скорость осаждения 0,2-0,6 мкм/м при плотности тока 1,5-3 А/дм2. Отношение поверхности катода к поверхности анода 1:1.
Покрытия сплавом Sn-Bi обладают высокой коррозионной стойкостью. Блестящие покрытия сплавом Sn-Bi имеют высокую коррозионную стойкость в камере морского тумана в течение 7 суток, в камере влаги в течение 10 и 30 суток. Коррозионная стойкость оценивалась визуальным подсчетом мест коррозионных поражений по десятибалльной системе (табл. 5.4).
Табл. 5.4. Коррозионная стойкость покрытия Sn-Bi (в баллах)
Тип
покрытия
| Морской туман,
7 суток
| Влага,
10 суток
| Влага,
30 суток
| Подслой меди
| Подслой никеля
| Подслой меди
| Подслой никеля
| Подслой меди
| Подслой никеля
| Sn-Bi
блестящее (15 мкм)
| 8,6
| 9,1
| 9,2
| 9,9
| 7,7
| 7,9
|
Коррозионная стойкость покрытий сплавом Sn-Bi зависит от состава сплава, толщины, структуры и пористости осадков. Большей коррозионной стойкостью обладают покрытия с содержанием 0,4-0,9 % Bi. Рекомендуется применять для ППИ сложной конструкции из разнородных материалов покрытия толщиной 9-12 мкм, а для тропического варианта – толщиной 18-21 мкм. При этом на стальные и латунные детали предварительно наносят подслой меди толщиной 4-6 мкм.
Покрытие составом Sn-Bi толщиной 9-12 мкм используется для коррозионной защиты деталей из меди и медных сплавов в жестких условиях эксплуатации.
Для защиты проводников печатных плат вместо серебрения применяется сплав Sn-Bi. Исследования показали, что в течение продолжительного времени сохраняется качественная пайка и исключается механическая и химическая зачистка проводников после травления.
Проводились исследования паяемости трех видов покрытий: оловянного, оловянно-свинцового и покрытия олово-висмут, нанесенных на медь и латунь по подслою никеля и меди. Установлено, что подслой никеля способствует сохранению паяемости всех видов покрытий, чем подслой меди. Внешний вид оловянных и оловянно-свинцовых покрытий после 6-7 месяцев хранения ухудшился. При этом произошло потемнение покрытий и появились очаги коррозии. Внешний вид покрытий олово-висмут с подслоем никеля практически не изменился после годового складского хранения.
Для осаждения покрытий сплавом Sn-Bi разработано большое количество электролитов. Покрытия данными сплавами могут осаждаться в виде матовых или блестящих осадков. Для широкого использования в производстве изделий микроэлектроники для осаждения сплава Sn-Bi рекомендуются электролиты с добавкой ОС-20 или двумя добавками ДДДМ и ОС‑20, позволяющие получать светлые, мелкозернистые, плотные осадки.
В сплавах системы Sn-Bi с увеличением доли висмута в олове прочность припоя возрастает, а пластичность снижается при одинаковых условиях. Припои Sn-Bi с массовой долей висмута 52-58 % имеют прочность 53-56 МПа. Такая концентрация висмута способствует измельчению структуры олова и задерживает рост зерен при длительной выдержке при повышенных температурах.
Припои на основе системы Sn-Bi с содержанием висмута 30-40 % имеют низкую пластичность. По этой причине из таких припоев получить ленту толщиной 0,05-0,2 мм без трещин при прокатке не удается.
Температурный коэффициент линейного расширения эвтектического припоя (58Bi/42Sn) при температуре плавления составляет 16,2·10–6 К–1. При этом электрическая проводимость оставляет всего 4,5 % от электрической проводимости меди. Таким образом, данный припой целесообразно применять для пайки согласованных соединений с повышенной прочностью, но работающих при температуре не выше 80 ºС.
В качестве припоя используется сплав тройной системы олово – индий – висмут. Эвтектический сплав (16,3Sn/54,02Bi/29,68In) имеет температуру плавления 81 ºС.
Для герметизации корпусов ППИ пайкой без флюса используют припойную прокладку, содержащую 99-99,5 % Sn и 0,5-1,0 % Bi. При этом основание корпуса и крышки покрыты золотом, а нагрев осуществляется струей горячего инертного газа. Особенностью данного способа герметизации является то, что золотом покрывается часть крышки, входящая в зону шва. Это не только приводит к экономии золота, но и исключает растекание припоя по внешней и внутренней поверхности крышки. Толщина золотого покрытия на крышке составляет 1,5-2 мкм.
При сборке ППИ в металлокерамических корпусах возможна пайка без припойной прокладки за счет слоя припоя Sn-Bi, нанесенного на крышку. В данном случае слой припоя наносится в виде рамки или валика только по краю внутренней поверхности крышки. Толщина его должна быть не менее 0,15 мм. На основание корпуса тоже в виде кольца нанесено золото. Герметизация осуществляется струей нагретого газа, при этом слой припоя на крышке плавится, смачивает золото и герметизирует корпус без использования флюса.
Выбор метода подачи и оптимальной толщины припоя для соединения кристалла с ножкой. Исследовались два метода подачи припоя: использование припоя в виде прокладки и нанесение припоя на коллекторную сторону кристалла.
При первом методе припой прокатывается до определенной толщины, затем вырубаются прокладки заданной геометрической формы, которые закладываются под кристалл при сборке в кассету. Достоинством данного метода является то, что облуживание ножки и присоединение кристалла выполняется за один процесс. По второму методу сборка производится без прокладки. В этом случае на коллекторной стороне пластины гальванически осаждается слой припоя Sn-Bi. Применение этого метода упрощает процесс сборки, кроме того, имеется возможность наносить покрытия любой толщины. Однако требуются дополнительные операции по защите активной стороны пластины перед облуживанием.
При первом методе подачи припоя для пайки кристалла материалом для прокладок служил припой ПОС-40. Исследовались прокладки различной толщины – от 20 до 90 мкм. При каждом значении толщины напаивалось по 20 кристаллов. Качество их присоединения к ножке оценивалось по выходу годных приборов при замере мощности рассеивания после сборки приборов. Для монтажа использовались облуженные выводы с толщиной припоя 9-10 мкм. Выход годных приборов зависит от толщины прокладки припоя (рис. 5.3): если она составляет 40 мкм, то выход – максимальный (85 %), при толщине 90 мкм он уменьшается до 50 %. Это объясняется тем, что более толстый слой припоя под кристаллом ухудшает теплопроводность прибора при работе.
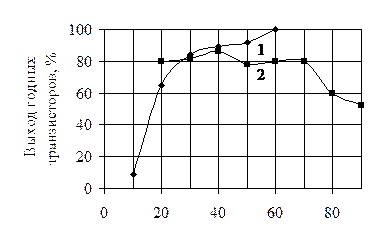
Рис. 5.3. Влияние толщины и методов подачи припоя на качество соединений кристалла с ножкой: 1 – гальваническое облуживание коллекторной стороны кристалла; 2 – использование припоя в виде прокладок
При нанесении припоя на коллекторную сторону пластины активная область должна быть защищена. Методом гальванического лужения наносилось покрытие из сплава Sn-Bi. Скорость осаждения составляла 0,75 мкм/мин при плотности тока 1 А/дм2. Толщина гальванического покрытия изменялась от 10 до 60 мкм через 10 мкм. Для каждого значения толщины покрытия изготавливалось по одной пластине. После разрезки пластин на кристаллы последние проверялись по электрическим параметрам и внешнему виду. Качество присоединения, как и в первом случае, оценивалось по выходу годных приборов при замере мощности рассеивания (рис. 5.3). Выход годных приборов изменяется от 64 % при толщине припоя 20 мкм до 100 % при толщине 60 мкм. При толщине припоя 50-60 мкм наблюдается наиболее равномерное его растекание по поверхности кристалла и ножки.
Таким образом, оптимальным методом подачи припоя под кристалл является гальваническое облуживание коллекторной стороны кристалла.
Оловянное покрытие
Некоторые зарубежные компании (например, Molex) считают, что лучшей заменой сплаву Pb-Sn является покрытие контактов печатных плат чистым оловом. Известно, что олово обладает химической устойчивостью и инертностью, а также высокой способностью к пайке. В то же время следует отметить, что олово обладает и недостатками: при воздействии низкой температуры возможно превращение β-олова, кристаллизующегося в тетрагональной системе и имеющего плотность 7,29 г/см3, в α-олово, имеющего кубическую решетку с плотностью 5,77 г/см3. Данное превращение сопровождается изменением объема и переходом контактного металла в порошкообразное состояние, которое называют «оловянной чумой». Кроме того, при хранении деталей и изделий, покрытых оловом, способность к пайке существенно снижается, что вызывает определенные трудности при сборке изделий на поточных линиях. Особо важно отметить, что даже белая модификация олова после двухлетнего хранения на 60 % теряет прочность спая. Покрытия из чистого олова обладают склонностью к образованию на поверхности нитевидных кристаллов («усов»), что ограничивает их применение для сборки.
С целью устранения недостатков, присущих оловянным покрытиям, проводят электрохимическое легирование олова другими металлами (никель, висмут, цинк, кобальт, сурьма и др.). Эти сплавы лишены недостатков, которыми обладает чистое олово, а, кроме того, имеют определенные преимущества: сохраняют паяемость, повышенную коррозионную стойкость и другие специальные свойства.
Олово и его сплавы осаждаются в виде блестящих электролитических покрытий только в том случае, если в раствор при электролизе вводят специальные поверхностно-активные или коллоидные добавки, называемые блескообразующими. Органические соединения, добавляемые в электролиты, повышают катодную поляризацию, сближают потенциалы осаждаемых металлов, улучшают мелкокристалличность покрытия, его паяемость, увеличивают блеск и рассеивающую способность, повышают качество покрытия и стабильность работы электролита.
Никелевое покрытие
Покрытия корпусов ППИ никелем и его сплавами широко используются в электронной промышленности. Основным недостатком никелевых покрытий является низкая теплостойкость, поэтому они применимы только при низкотемпературном монтаже элементов или при пайке в защитной среде. Для повышения теплостойкости никелевые покрытия легируют тугоплавкими металлами Co, W, Mo, Re и B. Практическое применение нашли никелевые покрытия, легированные до 1 % B. Легирование никеля бором существенно повышает температурную стойкость сплава даже при малой концентрации бора, а микротвердость и хрупкость покрытия уменьшаются путем отжига.
Основной целью никелирования является защита основного металла от коррозии и повышение поверхностной твердости. Для покрытия корпусов приборов (в случае пайки кристаллов в защитной среде) используется химическое никелирование. Химические никелевые покрытия намного тверже электрохимических. Повышенная твердость покрытий во многом зависит от содержания фосфора в осажденных никелевых сплавах и режимов осаждения.
Химическое никелирование осуществляется на медные корпуса из следующего раствора, (г/л): никель двухлористый (20), натрий фосфорноватистокислый (25), кислота аминоуксусная (15), натрий уксуснокислый (10). Время осаждения покрытия толщиной 4 мкм составляет 40-50 мин при температуре раствора 82-85 °С.
Свойства покрытий существенным образом зависят от подготовки медных корпусов к операции никелирования. Авторами исследованы покрытия, которые наносились на медные основания корпусов без полирования и с предварительным электрохимическим полированием поверхности. Анализ микроструктуры никелевых покрытий медных корпусов показал, что на полированной медной основе структура покрытий более мелкозернистая, чем на неполированной.
Для повышения блеска, снижения внутренних напряжений в никелевых покрытиях и интенсификации процесса никелирования используют специальный электролит. Электролит состоит, (г/л): сернокислый никель (150-250), сернокислый магний (20-60), сернокислый натрий (5-15), борная кислота (25-35), бензолсульфамид (0,1-0,8), 2,2´-дипиридил (0,005-0,01), триэтил-α-метилнафтилам-монит хлорид (0,002-0,02). Электроосаждение ведут при 40-55 °С, плотности тока 1-20 А/дм2 и рН 4,0-5,5.
Вводимый в состав электролита бензолсульфамид способствует снижению внутренних напряжений, переводя их из напряжений растяжения в напряжения сжатия. Кроме того, повышается рассеивающая способность электролита. Введение в состав электролита бензолсульфамида положительно сказывается на качестве и свойствах покрытий, которые становятся более плотными, блестящими и не отслаиваются от подложки при деформации. Повышение содержания бензолсульфамида более 0,8 г/л приводит к росту внутренних напряжений сжатия, а его снижение до 0,1 г/л вызывает хрупкость покрытий.
Сплав никель – олово
Гальванические покрытия паяемых поверхностей кристалла и основания корпуса при сборке должны обладать не только хорошей смачиваемостью, но и высокой коррозионной стойкостью. Этим требованиям в полной мере отвечают сплавы никеля с оловом (Ni-Sn).
При осаждении сплава Ni-Sn необходимо строго соблюдать условия электроосаждения: температуру электролиза, соотношение концентраций компонентов электролита, плотность тока.
Для осаждения сплава Ni-Sn существует несколько типов электролитов. Наиболее широкое применение в промышленности получили фторидхлоридные электролиты как наиболее стабильные в работе и позволяющие получать покрытия с относительно высокими защитно-декоративными свойствами. Широко используется электролит следующего состава, (г/л): хлористый никель (200), хлористое олово (40), фтористый аммоний (60), OC-20 (5). Температура электролита составляет 50 °С, а в качестве анода используется сплав никель – олово (30-50 % Ni).
Для нанесения сплавов Ni-Sn рекомендуется использовать электролит следующего состава, (г/л): хлористый никель (250-300), хлористое олово (40-50), фтористый аммоний (40-80), хлористый аммоний (60-100), 2, 4, 6-три-(морфолинометил)-фенол (0,05-0,2). Особенностью данного электролита является следующее: введение 2, 4, 6-три-(морфолинометил)-фенол обеспечивает повышение блеска и коррозионной стойкости покрытий.
С целью снижения внутренних напряжений и повышения защитно-декоративных свойств покрытий Ni-Sn электролит дополнительно содержит полиэтиленполиамин и N‑ацетонитрилморфолина гидрохлорид при следующем соотношении компонентов, (г/л): хлористый никель (200-300), хлористое олово (40-50), фтористый аммоний (30-60), фтористый натрий (20-30), полиэтиленполиамид (2-30 мл/л), N-ацетонит-рилморфолина гидрохлорид (0,03-0,15).
Исследования микроструктуры и химического состава поверхности покрытий из сплава 35Ni/65Sn, полученных из электролитов с добавкой ОС-20, показали следующие результаты: при температуре 50 °С получаются крупнокристаллические покрытия, в которых массовая доля олова составляет 99,8 %. Отжиг покрытий в вакууме, соответствующий режимам пайки кристаллов к основаниям корпусов, приводит к увеличению массовой доли никеля в поверхностном слое до 8 %. Покрытия после отжига получаются более плотными с включениями неправильной формы.
Объясняется это тем, что при температуре пайки электролитический сплав Ni-Sn переходит в интерметаллические соединения Ni3Sn2 и Ni3Sn4, что способствует обогащению поверхностного слоя никелем. Кроме того, повышенное содержание никеля в поверхностном слое данного покрытия, очевидно, обусловлено различной сублимацией компонентов сплава, которая в большей степени присуща Sn.
Серебряное покрытие
Для создания покрытий с высокой электропроводностью и стабильной величиной переходного сопротивления в местах контактов используется серебрение. Например, в производстве СПП серебро используется в качестве металлизации кристалла под пайку. В этом случае осуществляется напыление пленки серебра на пластину с кристаллами.
Серебряное покрытие формируется напылением в вакууме с применением методов магнетронного распыления серебряной мишени или термическим испарением серебра из тигля электронным лучом. Более предпочтительным является метод магнетронного распыления, который обеспечивает высокие адгезионные свойства напыляемой пленки. Этим методом получают качественные покрытия толщиной до 2 мкм с высокой производительностью, что является важным фактором в условиях серийного производства.
Для формирования металлизации методом магнетронного распыления используются промышленные вакуумные установки непрерывного действия. Процесс напыления проводится при рабочем давлении газа (аргона) р = (0,5-1,0) Па при мощности магнетрона до 4 кВт. Для улучшения адгезионных свойств напыляемой пленки поверхность пластин подвергается бомбардировке ионами Ar+. Ионная очистка осуществляется в том же рабочем объеме (камере), что и процесс напыления.
Нанесение серебряного покрытия на корпуса проводят гальваническим способом только на участки под пайку кристаллов и разварку внутренних выводов. Серебряные покрытия, полученные из обычных электролитов, характеризуются малой твердостью и незначительной износостойкостью. Для улучшения этих параметров в электролит для серебрения вводят соли никеля или кобальта, что приводит к повышению твердости покрытия в 1,5, а износостойкости – почти в 3 раза.
Корпуса для СПП изготавливают в основном из холоднокатаной листовой меди. На поверхности таких листов присутствует наклепанный слой. Авторами данной работы проводились исследования серебряных покрытий, которые наносились на медные корпуса без полирования и с предварительным электрохимическим полированием поверхности. Анализировались серебро гальваническое и серебро с подслоем никеля. Установлено, что серебряные покрытия на полированной медной основе имеют мелкозернистую структуру, характеризуются более низкой микротвердостью. Эти свойства необходимо учитывать при пайке кристаллов и присоединении внутренних выводов к корпусам с серебряным покрытием.
На медные корпуса серебряное покрытие толщиной 5-6 мкм наносят на подслой химического никеля. Для получения блестящих серебряных покрытий в широком диапазоне плотностей тока при высокой скорости осаждения металла разработан технологический процесс, состоящий из следующих операций: проводят электрохимическое обезжиривание на катоде в электролите, (г/л): NaОН (10-59), Na2CO3 (20-30), Na3PO4 (30-50), Na2SiO3 (3-5), ОП-10 (2-3) при T = 80-90 °С, Dk = 2-10 А/дм2, U = 5-12 B, t = 10-15 мин; затем промывают в горячей и холодной проточной воде и проводят процесс химического травления в растворе: HNO3 (1 л), H2SO4 (1 л), NaCl (4-10 г/л) при T = 20-25 °C, t = 2-3 с; промывают в холодной воде, после чего процесс травления повторяется 2-3 раза.
Химическое декапирование проводят в растворе: HCl (50-100 мл/л), H2O (900-950 мл) при T = 20-25 °С, t = 0,5 мин, промывают в холодной воде. Электролитическое серебрение проводят в электролите, (г/л): Ag2NO3 (10-45), К2Fе(СН)6·ЗН2O (50-150), K2CO3 (15-30) при T = 20-25 °С. Параметры импульсного тока: амплитудная плотность 5-8 А/дм2, частота 0,5-40 Гц, скважность 4-20. Параметры ультразвуковой обработки: интенсивность в импульсе 0,1-0,5 Вт/см, частота 15-80 кГц, частота посылок импульсов 0,5-40 Гц, затем идет процесс промывки деталей.
Снижение качества операций пайки кристаллов и присоединения внутренних выводов к серебряному покрытию происходит из-за наличия сульфидной пленки Ag2S на поверхности. Для очистки серебряных покрытий применяют различные методы: механические, химические и электрохимические. Однако данные способы не предотвращают процесса повторного образования Ag2S.
Не нашли, что искали? Воспользуйтесь поиском по сайту:
©2015 - 2025 stydopedia.ru Все материалы защищены законодательством РФ.
|