Оценка смачиваемости и растекания припоя по паяемой поверхности
О качестве пайки судят по способности покрытий при режимах пайки смачиваться припоем. Смачиваемость – это первая стадия физико-химического взаимодействия припоя с паяемой поверхностью изделия. В тоже время следует помнить, что смачиваемость покрытий припоем относится к технологическим факторам, позволяющим проводить экспресс-анализ пайки, как способа соединения элементов. Эксплуатационным параметром, позволяющим прогнозировать длительность хранения и эксплуатации изделий в заданных условиях, является прочность паяных соединений.
Известно, что смачиваемость и растекание припоя непосредственно связаны с краевым углом смачивания θ (рис. 4.6). Этот угол между поверхностями припоя и паяемым материалом на практике используется для оценки режимов и условий пайки.
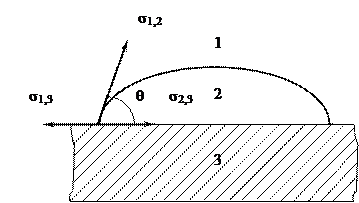
Рис. 4.6. Схема расположения векторов сил поверхностного натяжения капли припоя на поверхности твердого тела: 1 – окружающая среда; 2 – припой; 3 – твердое тело
Равновесие капли припоя на паяемой поверхности выражается в виде равновесия векторов сил поверхностного натяжения в точке на границе трех фаз
σ1,3 = σ2,3 + σ1,2 cos θ, (1)
где σ1,3 – поверхностное натяжение между твердым телом и газовой средой, действующее на каплю по периметру ее основания; σ2,3 – поверхностное натяжение припоя на границе с твердым телом; σ1,2 – поверхностное натяжение припоя на границе с окружающей средой.
Из выражения (1) следует, что
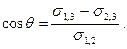
Cos θ, характеризующий способность припоя смачивать паяемую поверхность называется коэффициентом смачивания. Таким образом, зная краевой угол смачивания θ, определяют качество смачивания припоя поверхности твердого тела.
Растекание расплавленного припоя по паяемой поверхности определяется соотношением сил адгезии припоя к поверхности и когезии, характеризуемой силами связи между частицами припоя. Известно, что работа адгезии Аа определяется свободной поверхностной энергией в случае отделения припоя от основного материала
Аа = σ1,3 + σ1,2 – σ2,3
Отсюда следует, что при полном смачивании (θ=0) Аа = 2σ1,2. Когда краевой угол смачивания не равен нулю: Аа = σ1,2 (1+cos θ).
Таким образом расплавленный припой растекаться по паяемой поверхности будет в том случае, если Аа ≥ Ак. Разность между ними называют коэффициентом растекания: К= Аа – Ак.
Коэффициент растекания К находится в прямой зависимости от краевого угла смачивания, т.е. полное растекание будет только при полном смачивании, т. е. при cos θ=1.
Для выбора оптимального типа припоя, способа обработки поверхности паяемого материала и режимов пайки необходимо проведение исследований смачиваемости припоев в комплексе условий с одновременным приближением их к производственным.
Исследование смачиваемости можно осуществлять по методу «лежащей капли». В этом случае для определения величины краевого угла θ пользуются промежуточной величиной-коэффициентом растекаемости Кр, который рассчитывается по формуле
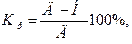
где Д – диаметр сферической капли припоя, мм; Н – высота капли после ее растекания по подложке, мм;
Величину Д для сферической капли определяют из выражения

где Р – вес исследуемой навески припоя, г; γ – удельный вес припоя, г/см3.
Величину Н с достаточной точностью определяют с помощью индикатора замером высоты капли припоя, застывшей на подложке после расплавления. Для измерения высоты капли припоя после растекания разработан прибор, в основу которого положен принцип бесконтактного измерения с помощью индуктивного преобразователя.
Зная Кр, с помощью графика определяют соответствующее значение краевых углов θ.
Оценку паяемости покрытий по растеканию дозы припоя можно провести по методу, изложенному в ГОСТе 9.302-79. В этом случае коэффициент растекания припоя определяют по формуле
Кр= Sp/So,
где Sp – площадь, занятая припоем после расплавления и растекания, мм2; So – площадь, занятая дозой припоя в исходном состоянии, мм2.
По данному ГОСТу исследуемая доза припоя имеет следующие размеры: диаметр 8 мм и толщину 0,3 мм.
Для практического использования разработана следующая шкала растекаемости припоя по паяемой поверхности в зависимости от краевого угла смачивания (табл. 4.1).
Табл. 4.1. Оценка смачивания поверхности припоем
Краевой угол смачивания θ, град
| Качество
смачивания
| Коэффициент
растекаемости Кр, %
| > 70
| Очень плохое
| > 60
| 70-55
| Плохое, удовлетворительное
| 60-70
| 55-40
| Достаточное
| 70-80
| 40-30
| Хорошее
| 80-85
| 30-20
| Очень хорошее
| 85-90
| 20-10
| Отличное
| 90-95
| 10-0
| Идеальное
| 95-100
|
При анализе качества паяных соединений полупроводникового кристалла с корпусом ППИ дозу припоя для исследований можно выбирать исходя их задаваемого объема припоя в паяном шве.
На рис. 4.7. показаны виды растекания припоя ПОС40 по различным покрытиям после нагрева в вакууме (10–1 Па) в течение 3 минут при температуре 280 ºС.
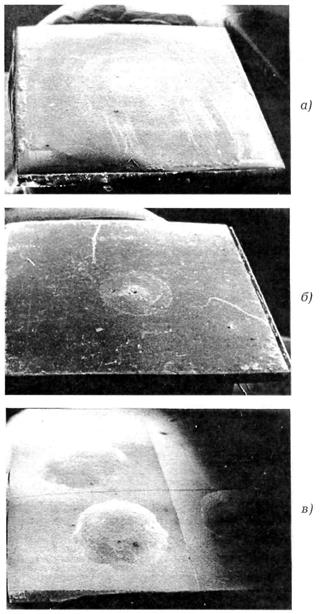
Рис. 4.7. Внешний вид растекания шарика припоя ПОС40 диаметром 1 мм по различным покрытиям: а – золотому; б – гальваническому никелю; в – никель – бор. Увеличение: 20´ (а, б), 10´ (в)
На фотографиях видно, что припой ПОС40 отлично смачивает золотое и никелевое и хорошо никель – бор покрытия.
Процесс смачивания является контактным металлургическим процессом взаимодействия припоя с поверхностью паяемого материала. Развитие этого процесса зависит как от состояния поверхности контактирующих материалов, характера развивающихся в их контакте процессов взаимодействия, так и режима пайки.
Скорость течения припоя по паяемой поверхности можно определять по способу, при котором припой помещают между излучающим и принимающим волноводами ультразвуковых колебаний. По относительному изменению энергии колебаний в единицу времени судят о скорости течения припоя по паяемой поверхности.
Определение смачивающей способности расплавов металлов возможно с помощью устройства, содержащего вертикально установленные пластины из исследуемого материала (металла) с температурой плавления выше температуры плавления расплава. При этом с целью проведения экспресс-анализа, пластины расположены под углом одна к другой. Собранные таким образом пластины помещаются основанием в емкость с исследуемым расплавом металла. После затвердевания отделяют исследуемый металл от наружных стенок пластины, а пластины разрезают по основанию. Поверхность, оставшаяся после разреза, шлифуется, полируется, травится и т. д. На месте разреза испытуемый материал образует картину зависимости высоты поднятия припоя по толщине щели, образованной пластинами.
Управлять площадью растекания припоя по поверхности твердого тела можно, используя способ, при котором твердое тело с припоем размещают в постоянном магнитном поле и подают электрический ток. С целью получения требуемой площади растекания припоя и увеличения прочности паяных соединений электрический ток пропускают через твердое тело с припоем в направлении, перпендикулярном направлению внешнего магнитного поля.
Для проведения исследований по затеканию припоя в переменный зазор в условиях невесомости и знакопеременных нагрузок можно использовать составной образец, который представляет собой две вставленные одна в другую трубы, при этом на наружной поверхности внутренней трубы выполнена проточка, эксцентричная относительно посадочных диаметров труб, с эксцентриситетом, равным половине максимального исследуемого капиллярного зазора. Наружная труба герметично соединена с внутренней трубой по посадочным соосным поверхностям, а емкость для припоя выполнена в трубе у основания эксцентричной проточки.
После размещения припоя в канавке внутренней трубы эта труба вставляется в наружную трубу. Затем детали обезгаживаются в вакууме или продуваются нейтрально-восстановительным газом и герметично завариваются по краям. Нагрев до температуры плавления припоя проводится в любых условиях (в невесомости, при знакопеременных нагрузках и т. д.). Исследования затекания припоя в капиллярный зазор в различных условиях проводят с помощью металлографического анализа паяных соединений.
Известна конструкция образца для исследования процесса заполнения капиллярных зазоров припоем, содержащая две прилегающие одна к другой пластины, на контактирующей поверхности одной из которых выполнены каналы, причем с целью подавления эффекта повышения капиллярного давления в углах каналов (по краям) выполнены углубления.
Смачиваемость паяемого материала расплавленным припоем, находящимся в динамическом состоянии (при пайке погружением или волной припоя), более правильно оценивать не по углу смачивания или площади растекания, а по силе, действующей на образец при его погружении и смачивании припоем. При пайке погружением или волной припоя (особенно при поверхностном монтаже компонентов), важнейшей характеристикой является скорость смачивания. Для этих целей широко используются испытания по методу силового баланса на приборе менискографе по методике ИСО.
Существуют различные способы оценки смачиваемости припоев. Например, известен способ, при котором погружение образца в расплав припоя осуществляется со скоростью, превышающей скорость смачивания. С помощью датчиков регистрируется изменение силы, действующей на образец во времени. Высота мениска определяется выражением
h = ,
где σ – поверхностное натяжение; ρ – плотность; θ – краевой угол; g – ускорение свободного падения.
Оценку паяемости определяют также по изменению величины усилия смачивания при погружении образца в ванну с жидким припоем. Такая оценка паяемости является наиболее объективной, особенно при использовании процесса пайки в радиоэлектронике, например, при изготовлении ИС. Для этих целей разработаны специализированные установки, позволяющие преобразовывать усилия смачивания в электрический сигнал, который автоматически регистрируется электронным самописцем в виде диаграммы. Расшифровка диаграмм позволяет определить следующие временные характеристики: прогрев образца в расплавленном припое до начала смачивания, полное смачивание и общее время смачивания. Кроме того, определяется усилие выталкивания (дисмачивания) образца, погруженного в расплавленный припой, и усилие вытягивания образца с момента начала и до завершения процесса смачивания. Разработанная оценка паяемости, как отмечают авторы данной работы, является наиболее объективной и позволяет значительно снизить трудоемкость при выполнении экспериментальных работ.
Для определения скорости, а также площади смачивания припоем металлических поверхностей, диэлектриков и полупроводников разработано специальное устройство, с помощью которого возможно исследование смачивания поверхности припоем в динамике, а не по методу «лежащей капли».
Устройство для исследования смачивания поверхности припоем содержит основание 1 с токоподводами 2, соединенными внешними концами с приборами контроля электрической цепи 3 (рис. 4.8). Токоподводы 2, представляющие собой планарно расположенную лучевую систему дорожек изолированных слоем диэлектрика 6 от материала основания, имеют толщину 0,001-0,006 мм и ширину 0,02-0,1 мм. Токоподводы наносят на основание напылением, гальваническим или другим известным способом. При ширине токоподвода 0,02-0,1 мм исключается погрешность затекания исследуемого припоя по токоподводам, т.е. опережающее течение припоя по токоподводам в сравнении с материалом основания, т. к. в данном случае преобладающими являются силы поверхностного натяжения расплавленного припоя. Меньшая ширина токоподводов 2 практически сложно выполнима с малым процентом разброса (допуском). Конкретные размеры поперечного сечения токоподводов выбирают в зависимости от необходимой точности контроля, при этом важным параметром является постоянство сечения токоподводов 2 по всей длине.

Рис. 4.8. Схема устройства для исследования смачиваемости поверхности припоем: а – расположение токоподводов на основании; б – начало расплавления припоя; в – размещение припоя перед нагревом: 1 – основание; 2 – токоподводы; 3 – прибор контроля электрической цепи; 4 – площадка для размещения исследуемого припоя; 5 – кубик исследуемого припоя; 6 – диэлектрическая пленка; 7 – капля расплавленного припоя
В центре основания имеется площадка 4 для размещения исследуемого припоя 5. Площадка представляет собой квадрат размером 4´4 мм, а для определения площади растекания используется навеска припоя объемом 64,0 мм3, по форме близкая к кубу.
Токоподводы на исследуемой подложке располагаются попарно на одной линии с центром площадки 4 с изменяющимися расстояниями между внутренними концами, которые симметричны относительно того же центра. Расстояния l1, l2, …, ln между внутренними концами пар токоподводов изменяются (увеличиваются) по определенному закону, например, линейному или логарифмическому. Например, расстояние между концами пар токоподводов увеличивается по линейному закону через 1 мм, а расстояние l1 между ближайшими токоподводами составляет 6мм.
Для исследования смачивания припоем основания из диэлектрика металл токоподводов должен иметь температуру плавления не менее чем на 50-100 ºС выше температуры плавления припоя. При исследовании смачивания припоем основания из металла токоподводы наносят на основание через диэлектрическую пленку 6, в этом случае токоподводы выполняются из того же материала, что и основание.
Исследования смачивания и капиллярного течения припоя по подложке проводят следующим образом. На площадке, в центре основания, размещают кубик припоя, совмещая ребра нижней грани куба с границами площадки, при этом оси симметрии нижней грани куба проходят через центр площадки. Внешние концы токоподводов основания соединяют через коммутирующее устройство с приборами контроля электрической цепи, например, включающими измеритель электрических сигналов с устройством для вывода информации на печатающее устройство или дисплей.
Затем основание нагревают до температуры расплавления припоя, используя при этом высокоточный регулятор температуры. При растекании капли припоя по основанию происходит замыкание токоподводов, которое фиксируется измерителем. Измеритель переключается поочередно на пары токоподводов в последовательности, соответствующей увеличению расстояния между внутренними концами токоподводов, и контролирует также падение напряжения между токоподводами. Переключение измерителя, фиксация времени появления контакта между токоподводами производится от ЭВМ.
Данные по фактической температуре основания и ее изменению снимаются с помощью быстродействующего измерителя температуры, соединенного с основанием при помощи термопары и подключенного также к ЭВМ.
Таким образом, ЭВМ получает данные о времени замыкания соответствующих пар токоподводов, по которым определяют площадь и скорость растекания припоев. Данные с ЭВМ можно подавать на графопостроитель и получать при этом информацию о площади и скорости растекания припоев в виде графиков временной зависимости. По данным с ЭВМ по падению напряжения между соответствующими парами токоподводов в зависимости от площади и скорости растекания можно определять изменение электрической проводимости припоев при смачивании исследуемой поверхности. Зависимость изменения проводимости припоев при смачивании может быть также получена в виде графиков с помощью графопостроителя.
Разработанное устройство позволяет проводить эксперименты в вакууме, в потоке защитных или восстановительных газов: водороде, азоте, аргоне, формир-газе и т. д.
Таким образом, для отработки технологических процессов пайки ППИ, особенно кристаллов к корпусам или герметизации приборов, необходимо в первую очередь провести оценку смачиваемости и растекания припоя по паяемым поверхностям. Это своего рода экспресс-анализ, позволяющий правильно выбирать оптимальный способ и режимы получения качественных паяных соединений.
Не нашли, что искали? Воспользуйтесь поиском по сайту:
©2015 - 2025 stydopedia.ru Все материалы защищены законодательством РФ.
|