Вынужденные колебания и автоколебания в процессе резания и их влияние на систему резания.
В пр-се резания в эл-тах сист. резания могут возник. колебания, наз. вибрациями. Наблюд. два осн. вида колеб.: вынужденные и самовозбуждающиеся или автоколебания.
Вынужденные колеб. возник. из-за периодичности д-я возмущ. силы вследствии: 1) прерывистого хар-ра пр-са резания; 2) дисбаланса вращ. дет. станка, заг. и ин-та; 3) дефектов в мех-мах станка (в зубчатых и ременных передачах, гидросистеме и т.п.); 4) неравномерности припуска на обработку; 5) передачи колеб. станку от др. работающих станков или машин. Для устран. этих колеб. достаточно ликвидир. причины их возникновения.
Автоколебания сист. резания возник. вследствие одноврем. или доминир. д-я нескольких физич. явл. Физич. модель возникн. и развития автоколеб. при резании может быть представлена следующей сх.: 1) любое случ. возмущение (толчок) выводит из равновесия упругую систему СПИД и приводит к измен. толщ. среза а: 2) установление равновесного сост. зоны вторич. деф-ции и длины контакта l не поспевает за измен. толщины среза а.
3) при врезании лезвия ин-та в заг. толщина среза а возраст., а при отталкив. ум-ся. Поскольку изменения а однозначно связано с измен. силы резания, то сила Р при врезании будет несколько меньше, а при отталкив. несколько больше величины силы Ро, соответствующей мгновенной толщине срезаемого слоя. 4) налич. отставания изменения силы резания Р от измен. толщины среза а переводит возникшие собствен. затухающие колеб. в незатухающие автоколеб., где энергию, поддерживающую их, создаёт изменяющаяся синхронно, но сдвинутая по фазе сила резания; 5) возникающие при этом на пов-ти резания вибрационные следы будут при каждом колебании передавать доп. энергию и усиливать колебания; 6) через определ. промеж. вр. наступ. равновесие между энергией возбуждения, поступающей в систему и энергией, рассеиваемой при колеб., и устанавливается определённый уровень автоколебаний.
Т.о, первичным источ. эн-гии возбуждения автоколеб. явл. неоднозначность силы резания вследствие запаздыв. ее измен. при измен. толщины срез. слоя. Вторич. или второстепен. источ. автоколеб. могут быть: 1) измен. углов лезвия ин-та при колеб.; 2) измен. р-ров сеч. при упругом закручив. стержнев. ин-та (сверл, зенкеров, метчиков и др.); 3) неустойчивость пр-са резания из-за нароста, налипов, образования элементной стружки и других явлений; 4) изменения силы трения.
Вибрации оказ. сущ-ное влияние на пок-ли и хар-ки пр-са резания, например, на произв-ть и кач-во обработки, интенсивность изнашив. и ст-ть РИ. Роль колеб. при этом может быть как положит., так и отриц. Положит. св-ва колеб. системы СПИД исп. в вибрационном резании, а отриц. их последствия устраняют путем: 1) повыш. виброуст. станков и их узлов; 2) примен. виброгасящих устр-в, в том числе и режущих и вспомогат. ин-тов; 3) выбором виброустойчивых диапазонов режимов резания; 4) управлением уровнем интенсивности автоколебаний и контролем технического состояния оборудования.
Автоколеб. хар-ся пост-вом частоты и переменностью амплитуды. На амплитуду колеб. оказ. влияние ряд факторов. С ув. толщины срез. слоя или подачи амплитуда колеб. ум., а с ув. ширины срез. слоя или глубины резания – ув. С ув. скор. резания амплитуда колеб. вначале возраст., а после достижения опред-го знач. скор. начинает ум. Ум. перед. угла с переходом его знач. в отриц. обл. приводит к резкому возраст. амплитуды колеб. Чем меньше перед. угол, тем больше зона скоростей резания, при к-рых возник. вибрации. С ув. гл. угла в плане амплитуда колеб. ум., что связано с ум. ширины срез. слоя и ув. его толщины. Задний угол при знач. его больших 8 …10° сущ-го влияния на вибрации не оказ., а при знач. меньших 3° уменьшает амплитуду колебаний. На амплитуду колеб. оказывают определенное влияние св-ва обрабатыв. мат-ла.
8. Температура резания, источники теплоты в зоне резания. Методы определения температуры резания: экспериментальный, аналитический и моделирования. Влияние параметров обработки на температуру резания.
При обработке резанием выделяется 2 вида тепловых потоков: 1) Теплообразующие, которые образуются за счет непосредственного нагрева от источника тепла; 2) Теплообменные потоки – вызванные дополнительным распределением тепла в результате неравномерного нагрева. Источники теплоты бывают внутренними и внешними. Первые, как следует из их наименования, возникают в самой системе. Как правил, внутренние источники являются результатом рабочего процесса или процессов, происходящих в оборудовании. Такова, например, теплота, выделяющаяся при деформировании обрабатываемого материала, при трении между ним и инструментом, при трении в зубчатых передачах станков и т.д. Внешние источники или стоки теплоты подводятся в подсистемы независимо от внутренних. Примерами могут служить дополнительных подогрев обрабатываемого материала (источник теплоты), охлаждение материала или инструмента ( стоки теплоты), система охлаждения узла станка и т.д. Все методы определения температуры делятся на: 1) косвенные и 2) прямые. К косвенным относят методы оценки значений т-ры по некоторым ее проявлениям, например по силам резания. Прямые основаны на более точном определении т-ры с использованием температурных датчиков. Температурные датчики бывают: а) контактные и б) бесконтактные. При контактных методах используются термометры, термоиндикаторы и термопары. При бесконтактных методах используются устройства, основанные на оптических, акустических и пневматических датчиках.
Экспериментами устан., что при резании констр-ных мат-лов более 99,5% работы резания переходят в тепло. Кол-во тепла, выдел. в пр-се резания, определяется по формуле:
,
где Pz- тангенц. составл. силы резания;
u- скор. резания.
Эта теплота образуется в след. очагах: в пл-ти деф-ции Qд; 2) в приконтактных обл. ин-та со стружкой QТП; 3) в приконтактных областях ин-та с заг. QТЗ. Теплота расход. на нагрев стружки Qc, нагрев заг. Qз, нагрев ин-та Qи, нагрев окруж. среды Qо. Ур-ние, связывающее образующуюся теплоту с расходной, называется уравнением теплового баланса:

При обраб. констр-ных мат-лов велич. составляющих теплоты, входящих в уравнение, по отношению к общему кол-ву теплоты колеблются в след. пределах:Qд=(60…90%)Q; QТП=(20…30%)Q; QТЗ=(5…10%)Q; Qc=(60…90%)Q; QЗ=(30…60%)Q; Qи=(5…15%)Q; Q0=(2…3%)Q.
Как видно из этих соотнош., кол-во тепла, выдел. в зоне деф-ции наибольшее, так как в этой зоне соверш. основная работа резания. Образуемое тепло в большей части расход. на нагрев стружки, что связано, прежде всего, с более высокой теплопроводностью мат-ла заг. по сравнению с ин-ным мат-лом и малыми объемами стружки. Однако темпер. на перед. пов-ти лезвия ин-та высока и примерно равна температуре стружки.
Моделир. тепловых пр-сов осущ. в основ. в двух видах:
1) физич. моделир., когда изуч. пр-са теплообмена в реальном теле производ. на основе анализа сходного пр-са распространения теплоты в модели;
2) математич. моделир., когда изуч. теплообмена в реальном теле производ. на основе анализа принципиально другого физич. явл., отлич. от пр-са распространения теплоты, но имеющего подобное математич. описание.
В кач-ве примера, иллюстрирующего первую разновидность, можно привести замену фактич. источ. теплоты на источ. в виде лазера. При этом необх. обеспеч. подобие между моделью и реальным пр-сом, усл. к-го сост. в следующем: 1) модель должна быть геометрич. подобна реальному объекту; 2) должно быть обеспечено рав-во безразмерных коорд. точек модели и реального объекта; 3) должно иметь место рав-во критериев подобия для модели и оригинала.
Второй вид моделир. может быть проиллюстрирован одинаковым математич. описанием разных по физич. природе пр-сов, например, распростр-ния теплоты и эл. тока. Диф. ур-е, описывающее пр-с распространения электрич. тока в твердом теле, выглядит следующим образом:
,
где U - потенциал в точке твердого тела с коорд. x1,y1, z1;
g-электропроводность;
с0- удельная электрическая емкость.
При анализе тепловых пр-сов в технол. сист. наиб. распростран. получили модели, в к-рых исп. электротепловая аналогия, т.е. аналогия между математич. описанием пр-сов распростран. теплоты и эл. тока. Метод эл. аналогии предусматрив. примен. моделей двух типов: 1) со сплошной электропроводящей средой; 2) с сеткой, сост. из активных сопротивлений (резисторов) и емкостей. В кач-ве сплошной среды чаще всего прим. графитизированную электропроводную бумагу. На бумаге изображ. модель тела, к пов-тям которой подводят ток заданной велич., имитирующий тепловой поток. В различ. точках модели определяют безразмерный потенциал, по которому затем с использ. метода подобия рассчитывают температуру сходной точки на нагреваемом объекте. Возможно построение на модели эквипотенциалей, которые в известном масштабе представляют собой изотермы на нагреваемом теле.
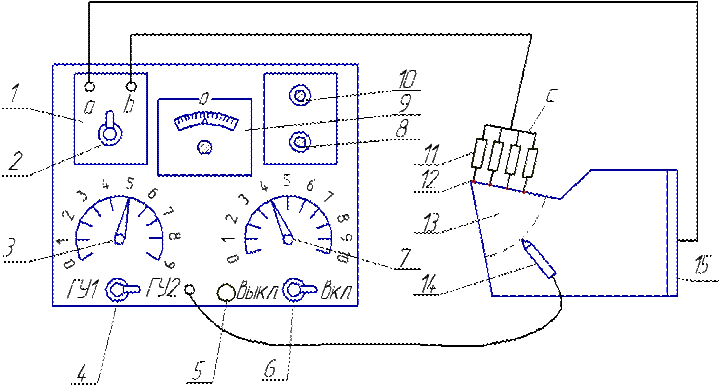
Интегратор включает блок питания 1, через контакты а и b которого подается напряж. на резисторы 11, контакты 12, модель 13 и шину 15. Резисторы 11 служат для подвода к пов-ти модели тока заданной плотности, имитирующего тепловой поток, например, со стороны стружки в резец. Блок и установка включаются контактами 2 и 6. Измерительное устройство 9 настраивается с помощью кнопки 4, переключателя декад 3 и реохорды 7. Сопротивл. резисторов 11 регулир. настройкой 8 и 10. Иглой 14 устан. точку на модели, в которой определяется безразмерный потенциал, переводимый затем в температуру.
При исп. моделей в виде эл. сеток разбивают твердое тело любой формы на элементарные объемы, в каждом из которых термическое сопротивление заменяют резистором соответ-щего сопротивления. При необходимости учета теплоемкости тел к сеточной модели из резисторов подключаются электрические конденсаторы. Затем, как и в случае электропроводной бумаги, определяют потенциалы в отдельных узлах сетки. Например, для процесса плоского шлифования устройство моделирования тепловых явлений на электрической сетке представлено на рис.
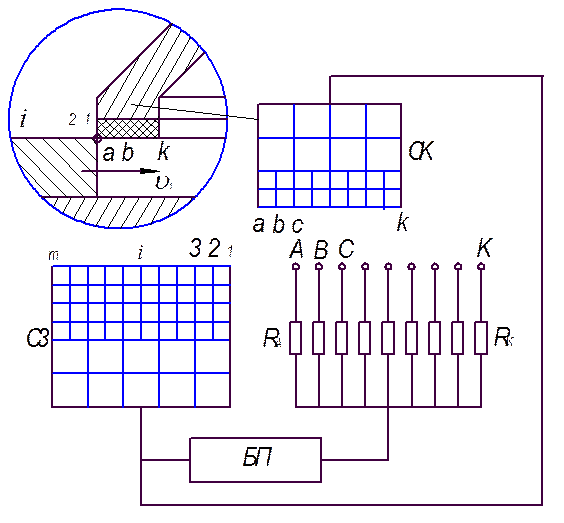
Чтобы смоделир. пр-с теплообмена, последовательно подключ. узлы сетки заготовки С3 (1, 2, 3…m) к узлам сетки абразивного круга СК (а, b, c…R) в порядке, соответствующем ходу процесса шлифования. Каждая пара узлов подключается к соответствующему истоку А, В…К, включающим резисторы RA… RK. Блок питания БП обеспечивает создание на узлах моделей СК и СЗ потенциалов, измеряя которые можно с использованием правила подобия определить температуру на поверхностях заготовки и абразивного круга.
Классич. представление о влиянии режима резания, геом. ин-та и других факторов обработки на температуру резания можно проиллюстрировать на примере эмпирической зависимости
.
Анализ этой зав-ти показ., что с ув. V возраст. кол-во тепла в зоне резания, а также температура нагрева загот., стружки и ин-та. Однако рост температуры в зоне резания отстает от роста скорости резания. Это отставание особенно усиливается в зоне высоких скоростей и характеризуется показателем степени zq<1
С ростом глубины резания t или ширины среза b прямо пропорционально растет сила, работа резания и количество выделяющейся теплоты. Во столько же раз ув. и длина активной части режущего лезвия, а соответственно и отвод тепла. Поэтому с увеличением b температура резания qрез изменяется незначительно и характеризуется показателем .
С ув. S или толщины среза а сила резания Рz растет примерно в степени 0,75, возрастают также работа резания и количество выделяемого тепла. Одновременно растет пл-дь контакта стружки с перед. пов-тью резца. Это улучшает условия отвода тепла, поэтому рост qрез отстает от роста а и показатель степени .
С ростом прочности, твердости и пластичности обрабатываемого материала (коэффициент Сq) возрастает температура резания. Чем выше теплопроводность обрабатываемого материала, тем ниже q, т. е. отвод тепла более интенсивен.
Влияние геом. реж. лезвия на темпер. резания опред-ся коэф. Кq. Например, с увеличением перед. угла лезвия g снижается сила резания Рz, работа резания и количество тепла. Однако при этом ухудш. условия отвода тепла, т.к. ум. величина угла заострения b. С ув. g выше gопт снижается массивность лезвия резца, ухудшаются условия отвода тепла, что приводит к повышению q.
С ум. угла в плане j ув. угол при вершине e, что приводит к возрастанию массы режущего лезвия и улучшению теплоотвода, а следовательно, к снижению q и, наоборот.
Используемые в настоящее время экспериментальные методы исследования тепловых процессов в зоне резания чрезвычайно разнообразны и благодаря их надежности и простоте являются основным методом исследования. Калориметрический метод позволяет определить количество теплоты, переходящей в стружку, деталь и инструмент, а также их средние температуры. Улавливая в калориметр горячую стружку, зная массы стружки и воды в калориметре и изменение т-ры воды, можно определить среднюю т-ру стружки (рис.1). [1-термометр, 2-деталь, 3-резец, 4-стружка].
Метод пленок – заключается в том, что на контактные площадки ин-та наносится в вакууме тонкий слой чистого металла с известной т-рой плавления. Теплота, выделяющаяся при резании, оплавляет пленку в области, где достигается т-ры ее плавления, и тем самым обозначает соответствующую изотерму (Рис.2).
Рис.2. Изотермы на резце из минералокерамики при точении стали 45 в течении 1 мин (v=500 м/мин, толщина пленки 0,05 мкм).
Метод искусственной термопары – заключается в том, что в ин-те просверливается отверстие малого диаметра, не доходящее до какой-либо точки передней или задней поверхности примерно на 0,2…0,5 мм, в которое вставляется изолированная термопара (рис.3).
Температура в точке соприкосновения термопары и ин-та регистрируется вклю-ченным в цепь термопары гальванометром. Этот метод дает возможность определить т-ру различных точек на передней и задней поверхностях ин-та и на поверхности стружки. Недостатками классической схемы искус-ственной термопары является сложность устройства и невозможность определить наивысшую т-ру, т.к. измерение т-ры фактически производится не на поверхности контакта резца и стружки, а на некотором удалении от них. Более точные значения температур можно получить, используя скользящие (бегущие) термопары (Рис.4).
Трубка из обрабатываемого материала защищает проводники от преждевременного замыкания. При перерезании резцом трубки проводки замыкаются, и на поверхности резания образуется точечная термопара, которая движется вместе с прирезцовым слоем стружки по передней поверхности. Это позволяет записать распределение температуры по поверхности контакта. Участки проводников, остающиеся в заготовке, позволяют определить распространение т-ры в начале по задней поверхности ин-та, а затем т-ру обработанной поверхности.
Существуют также методы полуискусственой термопары, естественной термопары, бесконтактный метод измерения т-ры. Термоэлектрический метод – заключается в том, что если нагреть спай двух проводников из различных металлов, оставляя при этом свободными концы при более низкой т-ре, на последних возникает термоЭДС, которая зависит от разности температур спая и более холодных концов. Замыкая цепь через милливольтметр, можно измерить термоЭДС. Этот метод является наиболее распространенным. К бесконтактным методам относятся: радиационный, фотоэлектрический, пневматический методы. Несмотря на прогрессивность идей в в современных бесконтактных методах они вследствие технических трудностей осуществления пока не могут конкурировать с контактными. К аналитическим методам относятся: 1) классический метод непосредственного интегрирования; 2) метод интегральных преобразований; 3) метод источников.
9. Физическая природа абразивно-механического, адгезионного и диффузионного изнашивания инструментов. Характерные черты износа различных инструментов. Период стойкости инструмента. Критерии предельного состояния инструмента.
Потеря реж. способн. ин-та вызывается изнашиванием его контактных (передней и задней) пов-тей. Изнашив. проявл. в износе лезвия ин-та. Под износом поним. велич., хар-щую измен. формы и р-ров РИ (лезвия) вследствие изнашивания при резании.
Модель абразивно-мех. изнашив. представлена. При дв-ии стружки по перед. пов-ти ин-та микровыступы приконтактной пов-ти стружки взаимодействуют с аналогичными микровыступами перед. пов-ти. Вследствие большого давл. и высокой темпер. на пл-ке контакта происходит разруш. взаимодействующих микровыступов. Это разруш. проявл. в пластич. деформировании и срезании. Наиболее вероятное срезание выступов имеет место на стружке, однако за счёт циклического воздействия на микровыступы передней поверхности инструмента имеют место разрушения инстр-ного мат-ла. С теч. вр. происх. сглажив. микровыступов ин-та, вследствие чего ув. фактич. пл-дь контакта ин-та со стружкой и заг. Снижается контактное давл. и интенсивность изнашивания уменьшается. Продукты износа, попадая между стружкой и ин-том, измельчаются в порошок и, окисляясь под действием температуры, превращаются в «абразив», который определяет дальнейший износ инструмента.
Сх. мех-мов абразив. (а) и адгезионно-диффузионного (б) изнашив. лезвия ин-та при контакте со стружкой
Адгезионно–диффузионное изнашив. - два вида изнашив. (адгезионное и диффузионное), объединённых одноврем. возд-ем на ин-т в пр-се резания.
Адгезией наз. молекуляр. схватыв. взаимодействующих тел под влиянием высокой темпер. и большого давления. Под адгезионным изнашив. лезвия поним. отрыв силами адгезии мельчайших частиц инстр-ного мат-ла в пр-се трения ин-та с обрабатыв. материалом.
Диффузией наз. взаимное проникновение атомов двух взаимодействующих тел. Высокие температуры, большие пластические деформации и адгезия в зоне контакта при высоких скоростях резания в сильной степени способствуют взаимному диффузионному растворению ин-ного и обрабатыв. мат-лов. Диффузионное изнашив. проявл. в след.: 1) в удалении стружкой диффундирующих частиц ин-ного мат-ла; 2) в проникновении частиц обрабатываемого мат-ла в ин-ный, что уменьшает прочность ин-та; 3) во взаимном растворении частиц ин-го и обрабатыв. мат-лов, что увеличивает степень их химического "родства" и влияние адгезии (к адгезии более склонны "родственные" материалы).
Рассмотрим мех-м адгезионно-диффузионного изнашив. На взаимодействующих микровыступах передней пов-ти ин-та и стружки возник. явл. адгезии. Это явл. приводит к доп. разрушениям в мат-лах стружки и ин-та при их относительном движении. Разрушения происх. чаще всего в пл-ти схватыв. и в мат-ле стружки, однако разрушения наблюдаются и в поверхностных слоях лезвия инструмента вследствие циклического воздействия сходящей стружки. В рез. адгезионного износа на поверхности ин-та появл. "вырывы". С повыш. темпер. резания число очагов схватыв. ув., что казалось бы должно привести к усилению адгезионного износа, однако "размягчение" обрабатываемого мат-ла ум. разруш. ин-ного мат-ла. И тем не менее при больших температурах (более 8000 С) наблюд. интенсив. увеличение износа ин-та. Этот износ определяется влиянием диффузии. Диффузия увеличивается с ув. температуры и времени контакта. Степень влияния температуры на диффузию значительно выше степени влияния времени контакта, поэтому с ув. скорости резания диффузия резко увеличивается.
В завис-ти от усл. резания различным оказывается внешний вид изношенного ин-та. Например, ин-ты, работающие при низких скор. резания (протяжки, фасонные и строгальные резцы) изнашив. в основном по реж. кромке. Изнашив. сверл наблюд. по зад. пов-ти. Фрезы изнашив. по реж. кромке и зад. пов-ти.
Сх. износа ин-тов в виде закругления реж. кромки с радиусом r, фаски h3, лунки lл: а – работающих при низких скоростях резания; б – сверл; в – фрез; г, д, е – токарных резцов.
Высокоскор. фрезер. ин-нт изнашив. в основном за счёт абразивно-механич. изнашив. Адгезионно–диффузионное изнашив. на фрезах не проявл., т. к. темпер. резания при фрезер. в одинак. с точением условиях меньше в 2… 3 раза.
Наиб. сложным образом изнашив. токарные резцы. У токарных резцов изнашив. проявл. в виде радиуса закругления реж. кромки, пл-ки (фаски) износа по зад. пов-ти и лунки на перед. пов-ти.
Закругление реж. кромки происх. по причине ее осыпания в рез. вибраций в пр-се резания и механич. изнашив. Износ по зад. пов-ти явл. рез. абразивно-механич. изнашив. Появление лунки обусловлено максимальной температурой на перед. пов-ти, значения которой могут достигать 1000 - 15000 С. Это и приводит к интенсификации адгезионно-диффузионного изнашивания ин-та.
Критерий затупления- критерий отказа реж. ин-та (лезвия) хар-ся максимально допустимым знач. износа реж. ин-та (лезвия), по мере достижения которого наступает его отказ.
Критерий отказа опр-ся в завис-ти от требований к обработке при выполнении конкретной технологической операции. К критериям отказа относятся:
1. Линейный р-р изношенной пл-ки на лезвии ин-та;
2. Сила резания;
3. Температура резания;
4. Шероховатость обработанной поверхности;
5. Уровень вибраций;
6. Уровень шума.
Подст-тью ин-та поним. его способн. работать до наступления износа. Ст-ть хар-ся периодом ст-ти. Период стойкости РИ (лезвия)- время резания новым или восстановленным режущим инструментом (лезвием) от начала резания до отказа.
10. Качество обработанной поверхности детали: волнистость и шероховатость, наклеп и остаточные напряжения. Формирование шероховатости при обработке острозаточенным резцом и резцом с радиусом при вершине. Влияние на качество поверхности детали условий обработки.
Под кач-вом детали поним. св-ва её пов-ного слоя, которые формируются в рез.возд-я на пов-ть одного или нескольких последовательно применяемых технологических методов обработки. Кач-во обработанной пов-ти хар-ся шер-тью и волнистостью, а также физико-механическими свойствами поверхностного слоя, такими как наклеп и остаточные напряжения.
Шероховатостью поверхности наз. сов-ть неровностей с относительно малыми шагами, образующая рельеф пов-тей детали и рассматриваемая на определённой (базовой) длине.
Под волнистостью пов-ти поним. сов-ть периодически чередующихся возвышенностей и впадин, изменяющихся примерно по синусоидальному закону. Расст. между смежными возвышенностями или впадинами превышает принимаемую при измерении шероховатости базовую длину.
Пов-ть дет. хар-ся макрогеометрией, микрогеометрией и субмикрогеометрией. К макрогеометрии можно отнести неровности на больших участках поверхности, к микрогеометрии относятся отклонения на участке примерно 1 мм2 (шероховатость) и к субмикрогеометрии относятся неровности, обусловленные несовершенством внутреннего строения металла. Субмикроскопический рельеф рассматривается на участках поверхностей от одного до нескольких микрометров.
Шероховатость оценивается критерием Rz или высотой неровностей:
,
где Нi max и Hi min – соответственно макс. и мин. отклонения профиля в пределах базовой длины,
а также арифметическим отклонением профиля:
,
где yi - отклонение профиля неровностей от средней линии.
1. При обраб. пов-тей острозаточ. резцом.
;
высота микронеровностей:
.
Как следует из формулы чистовую обработку следует вести на малых подачах и резцом с минимальными углами в плане. В связи с этим новатором Колесовым предложен резец, который снимает остаточные гребешки дополнительной режущей кромкой с =18о и производит калибровку поверхности участком режущей кромки с =0о. Причем длина того участка превосходит значение подачи S0 и составляет примерно 1.2S0. Высококачественное резание с применением таких резцов получило также название силового резания.
2. При обраб. пов-тей резцом с радиусом при вершине:
;
; ;
высота неровностей:
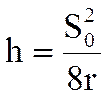
.
Как видно из формулы, для снижения шероховатости надо стремиться к уменьшению подачи и к увеличению радиуса при вершине резца.
С ув. скор. резания высота неровностей сниж. В диапаз. скор., при котором образуется нарост, характерен рост величины неровностей.
При ув. подачи высота неровностей возрастает. При малых подачах основное влияние оказывают не геометрические факторы, а пластическая и упругая деформации, скорость резания и радиус при вершине резца. При больших значениях подачи на шер-ть оказывают влияние геометрические факторы (следы движения инструмента). Глубина резания почти не влияет на шероховатость обработанной поверхности.
При обраб. заг. резанием в рез. возд-я на пов-ный слой силового и температурного полей в нём возник. пластич. деф-ии и созд. внутренние остаточ. напряж.
Поверхностная пластич. деф-ция обуславлив. появление наклёпа (упрочнения) пов-ного слоя. Наклёп обычно хар-ся микротвёрдостью и рентгенографическими показателями (расширение или размытие интерференционных линий).
Осн. причинами возникнов. остаточ. напряж. явл.:
1. Налич. пластич. деф-ции, приводящее к упрочнению и измен. физич. св-в металла;
2. Вытягивание кристаллич. зёрен металла, которые при этом претерпевают упругую и пластич. деф-ции растяжения в направлении резания;
3. Нагрев и охлаждение детали при резании, приводящие к развитию остаточ. напряж. растягивания во внешних слоях и сжатие в нижележащих слоях металла;
4. Стр-ные превращ. в металле.
С увелич. подачи и глубины резания наклёп пов-ного слоя ув.
Не нашли, что искали? Воспользуйтесь поиском по сайту:
©2015 - 2025 stydopedia.ru Все материалы защищены законодательством РФ.
|