Автоматический контроль и регулирование обжига известняка во вращающихся печах.
Одним из основных способов интенсификации процесса производства извести во вращающейся печи является автоматизация основного и вспомогательного технологического оборудования и процесса обжига. Уровень автоматизации производственного процесса при этом может быть различным.
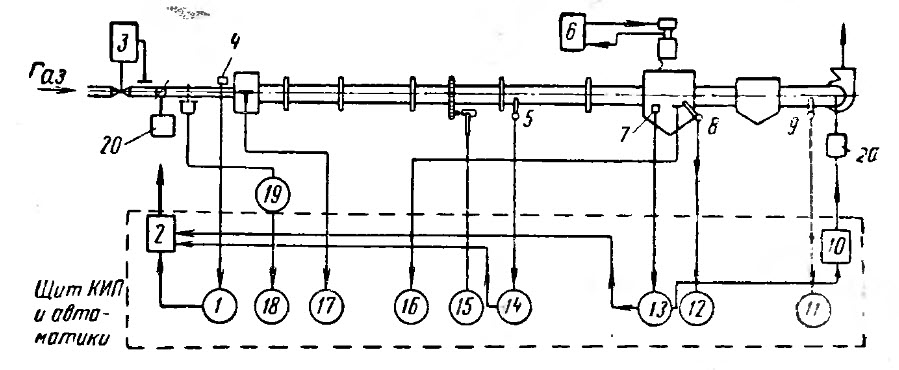
Схема системы автоматического контроля и регулирования процесса обжига извести во вращающейся печи без запечного теплообменника:
1 и 14 — потенциометры, 2 — регулятор температуры,3 — регулятор давления, 4 — радиационный пирометр, 5, 8и 9 — термометры, 6 — регулятор загрузки печи сырьем, 7 —газоотборное устройство, 10 — регулятор полноты сжигания топлива, 11 и12 — милливольтметры пирометрические, 13 — газоанализатор на кислород, 15 — сигнализирующий термометр, 16 и 17 — тягомеры мембранные показывающие, 18 — расходомер, 19 — дифференциальный манометр, 20— исполнительный механизм
Схема теплового контроля предусматривает автоматическое измерение и запись на диаграмме приборов расхода природного газа, разрежения в горячей головке печи и пылеосадительной камере; температуры газов в зоне обжига, в пылеосадительной камере и перед дымососом; температуры материала перед зоной обжига; содержания кислорода в отходящих газах.
Расход природного газа измеряется мембранным дифференциальным манометром 19 и регистрируется вторичным прибором — расходомером 18. Разрежение по тракту измеряется при помощи мембранных манометров (тягомеров) 16 и 17. Температура в зоне обжига измеряется радиационным пирометром 4 типа РАПИР, показания которого записываются автоматическим потенциометром 1. Температура газового потока в пылевой камере и дальше по газовому тракту измеряется при помощи хромель-алюмелевых термометров 8,9 и фиксируется показывающими милливольтметрами 11 и 12.
Температуру материала внутри вращающейся печи перед зоной обжига измеряют комплектом, состоящим из стандартного термоэлектрического термометра 5, помещаемого в карман, и автоматического потенциометра 14.
Содержание кислорода в отходящих печных газах измеряется автоматическим термомагнитным газоанализатором 13, снабженным записывающим прибором, шкала которого градуирована в объемных процентах. Для непрерывного отбора, очистки и подачи в прибор пробы газа служит газоотборное устройство 7, устанавливаемое в пылеосадительной камере.
Система автоматического регулирования, САР, предусматривает регулирование температуры в зоне обжига и полноты сгорания топлива, а также стабилизацию давления газа перед горелкой и количества подаваемого в печь сырья.
Температуру в зоне обжига регулируют регулятором 2 следующим образом. При отклонении температуры в зоне обжига от заданного значения потенциометр 1 посылает в измерительную схему регулятора 2 электрический импульс и регулятор через исполнительный механизм 20 поворачивает регулирующую заслонку газопровода, увеличив пли уменьшив подачу природного газа в печь.
Регулятор, кроме того, получает корректирующие импульсы при значительных отклонениях от заданной величины темпера-
туры материала перед зоной обжига (от потенциометра 14) и содержания кислорода в отходящих газах (от газоанализатора 13) и соответственно изменяет в определенных пределах подачу в печь топлива.
Полнота сгорания топлива в печи обеспечивается регулятором 10, который воздействует своим исполнительным механизмом 20 на направляющий аппарат дымососа. Например, при увеличении содержания в отходящих газах измерительная схема регулятора, получающая сигнал от газоанализатора 13, выходит из равновесия и исполнительный механизм несколько прикрывает направляющий аппарат дымососа. При этом разрежение в горячей головке печи несколько снижается, что приводит к уменьшению поступления в печь вторичного воздуха и содержание в отходящих газах снижается.
Регулятор 3 поддерживает давление в газопроводе, воздействуя на регулирующий орган (клапан, заслонку). Регулятор 6 получает импульс от датчика расхода материала в печь и воздействует на питатель, уменьшая или увеличивая его производительность. Таким образом он поддерживает постоянную величину подаваемого в печь сырья.
Сигнализирующий термометр 15 подаст световой или звуковой сигнал при повышении температуры масла в системе смазки главного привода печи выше допустимого значения.
Складирование извести.
Современный известковый комбинат выпускает известь комовую, гидратную (пушонку), молотую с добавками и известняковую муку для сельского хозяйства. Предприятия большой мощности имеют отдельные склады под каждый вид выпускаемой продукции. Емкость склада выбирается из условия продолжительности хранения продукции не более 5—6 суток. Например, для известкового комбината, рассчитанного на производство 300 тыс. т комовой извести, из которых 170 тыс. т выпускается в виде молотой извести с добавками, и 250 тыс. т известняковой муки, складские емкости составляют: для комовой извести — 2000 т; для молотой извести — 3000 т, для известняковой муки — 4000 т.
Склад молотой извести.
Склады молотой извести и известняковой муки состоят из однотипных сооружений и оборудования. Склад молотой извести емкостью 2000 т состоит из четырех силосов 6 емкостью 500 т каждый, снабженных аспирационной системой 8. Железобетонная банка силоса имеет высоту 20,6 м при диаметре 6,0 м.
Силосы загружаются пневмотранспортом по трубопроводу 7. Молотая известь распределяется по банкам с помощью двухходовых переключателей 12. Наполнение силосной банки известью контролируется по сигнализаторам нижнего и верхнего уровня. При наполнении банки известью до верхнего уровня загорается сигнальная лампочка и оператор отключает силос от питающего трубопровода.
Известь выгружается из силоса двумя пневматическими боковыми разгружателями 10 через выпускные отверстия, устроенные в нижней части банки. Выдача извести со склада предусматривается в автомобильный 9 и железнодорожный 11 транспорт.
Чтобы облегчить движение порошкового материала к выпускным отверстиям, дно силосной банки выполняют наклонным под углом 50° и на него укладывают воздухораспределительные коробки 5. Воздухораспределительная коробка состоит из чугунной рамы, в которую на замазке уложены пористые керамические плитки.
Наклонные коробки образуют дорожки по направлению к выгрузочным отверстиям силоса. Воздух подается в воздухораспределительные коробки от главного трубопровода, проложенного вдоль силосов. При подаче воздуха в силос через воздухораспределительные коробки лежащий на них материал насыщается воздухом и приобретает текучесть, в результате чего он легко стекает к выпускным отверстиям.
При длительном хранении продукции она слеживается в силосе и плохо выгружается. Чтобы предотвратить слеживание продукции, ее периодически перекачивают из одного силоса в другой.
Известь перекачивают из центрального выгрузочного отверстия банки при помощи разгрузочных шнеков 4 и пневмотранспортного шнека 3, который направляет известь в бункер пневмовинтового насоса 2. Пневмовинтовой насос подает порошкообразный материал по трубопроводу пневмоперекачки 1 в тот же бункер или другой, заполняя его сверху.
Аспирационные системы, установленные на силосных складах, отсасывают запыленный воздух в местах загрузки силосов. Очистка воздуха осуществляется в рукавных фильтрах.
При эксплуатации силосных емкостей, не имеющих совершенной системы аэрации и перекачки материала, нередки случаи уплотнения порошка с образованием сводов. Для рыхления материала следует пользоваться укрепленными на стенках силосов вибраторами, а при рыхлении вручную пользоваться специальными штангами и производить рыхление через люки, находясь снаружи силоса.
Запрещается спускаться в бункеры и силосы для рыхления материала. Бункера и силосы ремонтируют при полном отсутствии в них материала.
Люки силосов и бункеров во время их работы должны быть закрыты крышками и заперты на замок.
Рабочие, обслуживающие силосы и бункера, в связи с пылевыделением на этих участках обязаны пользоваться респираторами или марлевыми повязками.
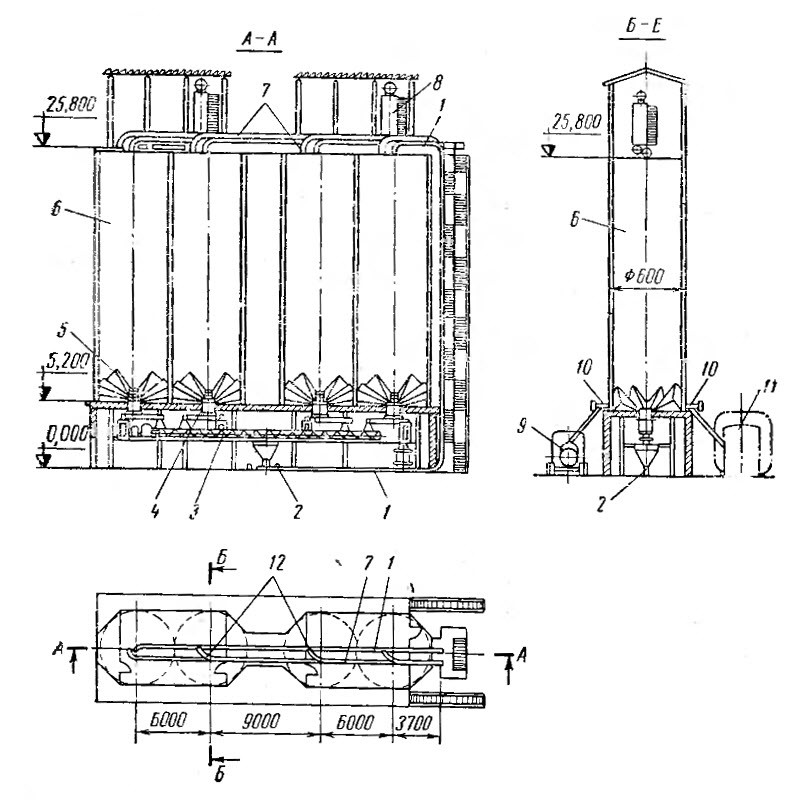
Не нашли, что искали? Воспользуйтесь поиском по сайту:
©2015 - 2025 stydopedia.ru Все материалы защищены законодательством РФ.
|