Склад известняка и твердого топлива
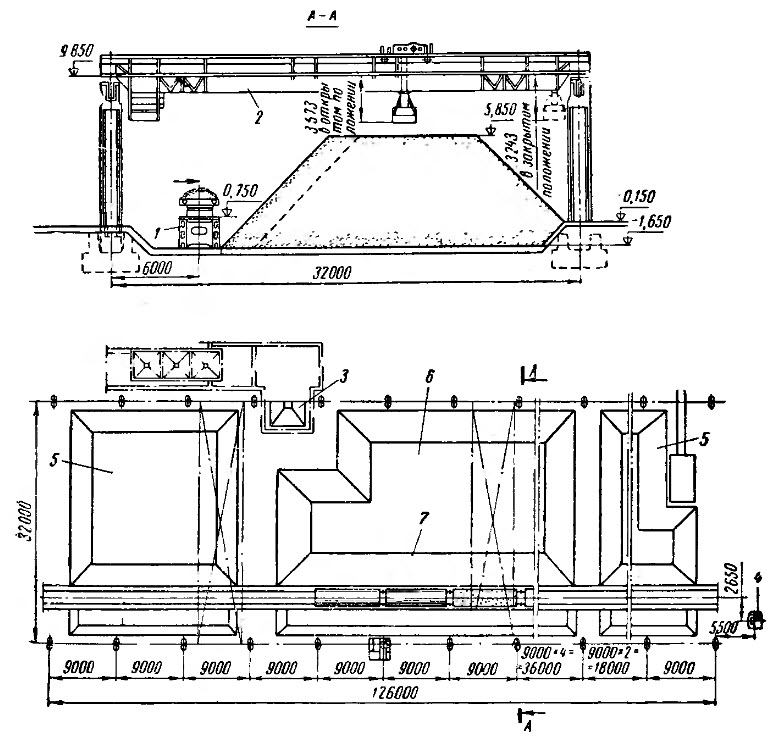
1 — железнодорожная эстакада,
2—мостовой грейферный кран,
3 —приемные бункера,
4 — маневровая лебедка,
5 — место хранения угля,
6 — место хранения известняка,
7 — траншея для выгрузки камня из саморазгружающихся вагонов
Типовой склад сырья и твердого топлива большой емкости протяженностью 100—130 м имеет бетонированный пол и стенки и оснащен двумя мостовыми кранами 2 длиной 32 м и грузоподъемностью 10 т. Одной своей стороной склад примыкает к приемным бункерам дробильно-сортировочного отделения 3 (или приемным бункерам печей). Противоположная сторона склада оборудована эстакадой с железнодорожным путем. Сырье 6 складируется в средней части площадки, а топливо 5 с обоих сторон от сырья.
Полувагоны с сырьем или топливом разгружают вдоль склада по обе стороны от эстакады. Выгрузочные люки полувагонов открывают вручную (при односторонней выгрузке) или при помощи механизмов, укрепленных на фермах мостового крана. Железнодорожный состав перемещают при помощи маневровой лебедки 4. Сырье и топливо загружают в приемные бункера мостовыми кранами.
Каменный уголь хранят в штабелях. В зависимости от склонности к самовозгоранию ископаемые угли делятся на две категории: А—опасные (бурые и каменные длиннопламенные) и Б — устойчивые (антрацит, тощие каменные угли). Угли категории А хранят в штабелях высотой до 3 м, если срок хранения не превышает двух месяцев. При большем сроке высота штабеля не должна превышать 2—2,5 м. Высота штабеля при хранении антрацита не ограничивается. Расстояние между штабелями рекомендуется не менее 5 м.
Торф складируют штабелями длиной не более 100 м, шириной в основании 15 м и высотой 5—6 м. Штабеля располагают с разрывами 4 м. Каждую пару штабелей рекомендуется располагать на расстоянии от соседней в пределах 20—30 м. Кусковой и фрезерный торф хранят отдельно, причем емкость склада на территории завода для кускового торфа не должна быть более 10 тыс. т, а фрезерного — 5 тыс. т.
При эксплуатации складов твердого топлива следует принимать следующие меры безопасности. Уголь категории А и торф, находящиеся в штабелях, необходимо систематически контролировать на возможность самовозгорания.
С этой целью штабеля оборудуют стальными трубами с закрытым дном, которые погружены в топливо на разную высоту — от 0,7 от основания штабеля до 0,3 м от его поверхности. Трубы закрыты пробками, которые вынимают при измерении температуры в трубе термометром. Минимальная температура самовозгорания составляет 60°С, максимальная 74—78°С. При повышении температуры в штабеле до 60°С необходимо срочно принимать меры для ее снижения. Для этого следует уплотнять уголь в штабеле или вынуть разгоревшееся топливо.
Тушение разгоревшегося в штабеле угля водой не допускается. Разгоревшиеся уголь или торф разбрасывают тонким слоем и складируют на новом месте лишь после его охлаждения. Это топливо рекомендуется расходовать в первую очередь.
Склады твердого топлива оборудуют противопожарным инвентарем, обеспечивают водопроводом и ящиками с песком.
Уголь доставляют со склада к бункерам дробильно-сортировочной линии или приемным бункерам печей (при фракционированном угле) чаше всего передвижными или стационарными ленточными транспортерами — конвейерами. Иногда используются скреперные установки и опрокидные вагонетки узкой колеи.
На складах сырья широко применяют мостовые грейферные краны.
Мазут хранят в резервуарах, отдаленных от других помещений на 200—300 м. Резервуары оснащаются змеевиками, по которым пропускают пар, подогревающий мазут для снижения его вязкости. Мазут подается к обжиговым печам по обогреваемому паром трубопроводу при помощи шестеренчатого насоса.
Мазутохранилища обеспечивают химическими огнетушителями, ящиками с песком и другим противопожарным инвентарем. Мазут тушат паром, песком и химической пеной.
Контроль качества сырья и топлива.
Качество исходных материалов (сырья и топлива) контролируют при их поступлении на склад, периодически при хранении на складе и раз в смену на технологической линии перед поступлением в обжиговый агрегат.
Карбонатное сырье.
Качество карбонатной породы на складе контролируют как по документации поставщика, так и непосредственным анализом проб, взятых из прибывшей партии сырья или различных мест штабеля.
На каждые 300 т прибывающего на заводской склад карбонатного сырья поставщик (карьер) высылает на предприятие паспорт, в котором указано: дата выдачи документа, класс породы, количество, номер партии, результаты испытания проб сырья.
Работники предприятия периодически, 2—4 раза в месяц» производят контрольную проверку соответствия поступающей карбонатной породы требованиям ГОСТ 9179-77 «Породы карбонатные для производства строительной извести».
Содержание мелочи в поступившей партии фракционированного сырья определяют отдельно для каждой фракции следующим образом. Карбонатную породу в количестве не менее одной десятой части объема железнодорожного вагона или одной автомашины просеивают через грохот с отверстиями, равными размеру кусков нижнего предела поставляемой фракции. Начальную пробу и прошедшие через грохот фракции сырья (мелочь) взвешивают на весах. Количество мелочи в процентах лолучают расчетом по формуле

где — количество сырья в начальной пробе, кг; — количество сырья, прошедшего через сито, кг.
Содержание мелочи в сырье данной фракции не должно превышать 5%.
Для определения физико-химических свойств сырья необходимо отобрать среднюю пробу. Карбонатную породу для средней пробы отбирают из каждой партии в размере 20 кг, равными порциями, не менее чем из 20 мест.
Перед определением влажности и химического состава карбонатного сырья отобранную пробу подвергают квартованию. Для этого пробу в количестве 20 кг измельчают в мельнице допусков 30—40 мм, перемешивают лопатой и равномерным слоем распределяют в виде квадрата со стороной, равной 1 м.
Квадрат делят диагоналями на четыре треугольника, т. е. квартуют. Материал двух любых противоположных треугольников отбрасывают, а двух оставшихся измельчают и снова размещают в виде квадрата и также квартуют.
Среднюю пробу в количестве до 1 кг, отобранную методом квартования, помещают в эксикатор и направляют в лабораторию для исследования.
Для определения влажности карбонатную породу из средней пробы измельчают до полного прохождения через сито с отверстиями 3 мм и квартованием отбирают 20—40 г. Навеску взвешивают на технических весах с точностью до 0,01 г в предварительно просушенной и взвешенной фарфоровой чашке. Далее чашку с навеской материала помещают в сушильный шкаф, где выдерживают до постоянного веса при температуре 105—110° С.
Высушенную навеску охлаждают в эксикаторе над серной кислотой и взвешивают.
Влажность материала %, определяют по формуле

где — количество исходного материала, г; —количество материала после его сушки, г.
Потери при прокаливании (П.П.П.) карбонатной породы контролируют для косвенного определения содержания в сырье углекислого кальция и магния. Потери при прокаливании химически чистого составляют 44%, в доломитизированных известняках П.П.П. несколько выше, а П.П.П. известняков, засоренных примесями, ниже 44%. При величине П.П.П. ниже 40% карбонатное сырье не рекомендуется применять для производства воздушной извести.
Подготовку пробы и определение потери при прокаливании выполняют следующим образом. 25—30 г материала средней пробы растирают в фарфоровой ступке и сокращают квартованием до 10 г, после чего растирают в агатовой ступке до тонины пудры и хранят в бюксе.
1 г материала высушивают при температуре 105―110°С к взвешивают на аналитических весах с точностью до 0,0002 г. Затем его помещают в прокаленный и взвешенный фарфоровый тигель, который постепенно нагревают в муфельной печи до температуры 1000° С и выдерживают не менее 1 ч.
Тигель вынимают из печи, охлаждают в эксикаторе и взвешивают. Затем повторяют прокаливание в течение 15 мин, охлаждают и взвешивают тигель. При получении постоянного веса П.П.П., %, вычисляют по формуле
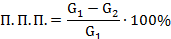
где — количество материала до прокаливания, г; — количество материала после прокаливания, г.
Далее определяют содержание в средней пробе окиси кремния полуторных окислов ( ), окиси кальция (СаО) и окиси магния (MgO).
Если контрольная проверка качества сырья показана неудовлетворительные результаты, т. е. невыполнение хотя бы одного из требований стандарта, то производят повторную проверку, отбирая двойное количество проб. При отрицательных результатах повторной проверки партия карбонатной породы не принимается предприятием и не пускается в производство.
Гранулометрический состав карбонатного сырья периодически, 1 раз в смену, проверяют на технологической линии перед его подачей в скип или питатель печи. В этом случае отбирают пробу весом 100—150 кг и определяют содержание мелочи рассмотренным выше методом.
Все данные соответствующих анализов заносят в журнал по контролю сырья.
Топливо.
Твердое топливо контролируют особенно тщательно, так как его качество существенно колеблется в процессе добычи и поставки потребителю. Поставщик обязан выслать предприятию удостоверение о качестве отгруженного топлива, в котором указываются марка и группа угля, выход летучих веществ, зольность, размер кусков, содержание влаги, теплотворность топлива.
От каждой поступающей на предприятие партии твердого топлива берется средняя проба, которая подвергается анализу с определением влажности, зольности, сортности и теплотворности топлива.
Влажность топлива определяют таким же способом, как и влажность сырья.
Зольность топлива определяют следующим образом. 5—10 г из средней пробы помещают в тигель и прокаливают при постепенном повышении температуры до полного сгорания органической части. Зольность топлива А, %, вычисляют по формуле

где — количество топлива, г; — количество золы, г.
Сортность твердого топлива устанавливают рассевом средней пробы топлива на грохоте или контрольных ситах с размерами отверстий, соответствующими гранулометрическому составу топлива по технологической карте.
Теплотворность топлива определяют в калориметрической бомбе по ГОСТ 147—54.
Влажность и зольность твердого топлива, идущего в производство извести, определяют один раз в сутки, а сортность (гранулометрический состав) —один раз в смену.
Кроме того, необходимо периодически контролировать правильность хранения твердого топлива в штабелях.
Жидкое топливо контролируют как по паспорту поставщика, так и отбором проб от полученной партии. В паспорте поставщика указывается марка мазута, содержание серы и теплотворность.
Среднюю пробу отбирают в чистый металлический сосуд во время слива мазута в хранилище из напорной части мазутопровода между расходным баком и печью. На каждые 10 т для пробы берут 1 л. Для получения лабораторной пробы первичную пробу при температуре не выше 25°С сильно взбалтывают в течение 5—10 мин и затем быстро отливают из нее 1 л в чистую сухую бутылку с пробкой.
Теплотворность мазута определяют, как и для твердого топлива.
Качество мазута, идущего в производство, контролируют 2—4 раза в месяц.
Газообразное топливо проверяют в лабораториях специализированных организаций. Среднюю пробу газа в объеме 20 л отбирают 1 раз в месяц в стальной баллон через газоотводные трубки из газопровода распределительной станции. На основании анализа газа определяют теплотворность и плотность газообразного топлива при нормальных условиях.
Все данные по качеству топлива заносят в специальный журнал по контролю топлива.
Не нашли, что искали? Воспользуйтесь поиском по сайту:
©2015 - 2025 stydopedia.ru Все материалы защищены законодательством РФ.
|