Пошаговый расчет поточной линии
1. Расчет программы запуска ведущей детали на год.
2. Расчет эффективного фонда времени работы оборудования за год.
3. Расчет такта работы поточной линии.
4. Расчет потребности в оборудовании (рабочих местах) на каждой операции.
5. Расчет коэффициента загрузки оборудования.
6. Расчет общего коэффициента загрузки оборудования на поточной линии.
7. Разработка аналоговой модели (календарного графика) работы поточной линии в период укрупненного ритма.
8. Организация (проектирование) поточного производства в пространстве (физическая модель).
9. Выбор транспортных средств для межоперационной транспортировки ведущей детали на поточной линии.
10. Организация оперативного учета и контроля за ходом производства.
1.Расчет программы запуска деталей на поточной линии Nзап:
, (2.1)
где Nзап и Nвып–годовая (месячная)программы запуска и выпуска деталей, шт;
α–технологические потери детали в процессе обработки, 0,3 %.
2. Расчет эффективного фонда времени работы оборудования за год Фоб.эф с учетом потерь времени по техническим и организационным причинам (простой в планово-предупредительном ремонте), мин:
, (2.2)
где ДкалиДвых– количество календарных, выходных и праздничных дней в году;
Дп/пр– количество предпраздничных дней в году;
s –число смен на участке;
tсм – номинальная продолжительность смены, 8 ч;
tсокр – сокращение продолжительности смены предпраздничного дня, 1 ч;
Кзаг.об– коэффициент загрузки оборудования во времени, (при отсутствии фактических данных по предприятию в дипломном проекте рекомендуемые значения для металлорежущих станков при двухсменном режиме работы:Кзаг.об = 0,95, для уникальных станков свыше 30-й категории сложности Кзаг.об= 0,92, для автоматических линий Кзаг.об = 0,9, для верстаков и монтажных столов Кзаг.об= 0,98).
3. Расчет такта выпуска/запуска. Под тактом понимается период времени между запуском (выпуском) двух смежных изделий. Он должен быть согласован с производственной программой участка (линии) и определяется по формуле:
а) такт выпуска деталей, мин/шт:
, (2.3)
гдеФэф–эффективный фонд времени работы оборудования за год, мин;
б) такт запуска деталей, мин/шт
. (2.4)
4.Расчет потребного количества рабочих мест (расчетное) для непрерывно-поточной линиипо каждой операции, шт:
, (2.5)
гдеtшт-кi–норма штучного времени на i-ю операцию, мин.
Норма штучного времени определяется в технологической части проекта методом технического нормирования:
, (2.6)
гдеα–процент потерь времени от оперативного времениton = (tо + tв), учитывающий остальные составляющие штучного времени.Величину αпринимают равной в зависимости от сложности наладки станков в пределах 6–10 %, для автоматических линий – до 18 % оперативного времени.
Для переменно-поточных и групповых поточных линий число станков на каждую операцию рассчитывают по штучно-калькуляционному времени и программе выпуска каждой закрепленной за линией детали:
, (2.7)
гдеtш-кi– штучно-калькуляционное время операции изготовления i-й детали на станке, мин.;
Ni– программа выпускаi-й детали;
п–количество разных деталей, изготовляемых на переменно-поточной линии.
Полученное значение Срiокругляют до ближайшего большего целого числа, получая при этом расчетное число станков Спрi для данной операции.
В случае если число станков превышает целое число не более чем на 0,05-0,1, рекомендуется пересмотреть содержание данной операции в отношении изменения режима резания, структуры операции, применяемых инструментальных материалов и оснастки с целью повышения производительности обработки.
5. Расчет коэффициента загрузки рабочих мест на операциях:
, (2.8)
гдеСпрi–число принятых рабочих мест на i-й операции.
Для дальнейшей работы следует сверить расчетные показатели с рекомендуемыми значениями перечисленных коэффициентов для отдельных станков и групп оборудования, приведенных в таблице2.1.
Таблица 2.1. Допустимые значения коэффициентов загрузки и использования оборудования[3]
Группа оборудования
| Коэффициент загрузки
оборудования Кзаг
| Коэффициент
использования
оборудования Ки
| максимальный
| средний
по группе
| Универсальные станки
| 0,95–1,0
| 0,80
| 0,90
| Автоматы и полуавтоматы одношпиндельные
| 0,95–1,0
| 0,85
| 0,85
| То же многошпиндельные
| 0,90
| 0,90
| 0,80
| Специальные и агрегатные станки
| 0,90
| 0,90
| 0,80
| Автоматические линии с жесткими связями
| 0,95–1,0
| 0,90
| 0,75
| Станки с ЧПУ
| 0,95
| 0,90
| 0,85
| В случаеесли коэффициент загрузки при расчете получается меньше рекомендованных значений, то в качестве принятого следует взять расчетное число станков, а коэффициент использования принимают равным единице.
Уточненные расчетные показатели необходимо внести в соответствующую таблицу 2.2.
Таблица 2.2. Нормы времени и потребность в технологическом оборудовании
Наименование и номер
операции
| Норма штучного времени, мин
| Количество станков (рабочих мест), ед.
| Такт
линии,
r,
мин. /шт
| Коэф-т загрузки оборудования (фактический), Кз.ф.
| Количество операций выполняемых на рабочем месте, m
| штучное,tшт.-к i
| машинное,tмашi
| ручное,
tручi
| расчетное,Ср
| принятое,Спр
|
|
|
|
|
|
|
|
|
|
|
|
|
|
|
|
|
|
|
|
|
|
|
|
|
|
|
|
|
|
|
|
|
|
|
|
| и т.д.
|
|
|
|
|
|
|
|
| Итого
|
|
|
| ΣСрi =
| ΣСпрi =
|
|
|
| 6. Общий коэффициент загрузки рабочих мест на поточной линии:
, (2.9)
где m– число операций.
7. Количество операций miвыполняемых на i-м рабочем месте:
, (2.10)
гдеКз.н – нормативный коэффициент загрузки оборудования;
Кз.ф – фактический коэффициент загрузки оборудования.
Разработка аналоговой модели (календарного графика) работы поточной линии в период укрупненного ритма.
Организация (проектирование) поточного производства в пространстве (физическая модель).
Выбор транспортных средств для межоперационной транспортировки ведущей детали на поточной линии.
Организация оперативного учета и контроля за ходом производства.
7. Построение календарного графика работы поточной линии в период укрупненного ритма:
а) расчет выработки на период обслуживания:
, (2.11)
где B– выработка на период обслуживания, шт;
R–период обслуживания, R = 0,5 смены
б) время работы недогруженного оборудования:
, (2.12)
где Кзi - коэффициент загрузки оборудования на i-й операции.
Коэффициент загрузки рабочего во время многостаночного цикла:
, (2.13)
где tр – ручное время, мин;
tм.с. – машинное время, мин;
tсв – свободное время, мин.
г) выработка по каждой операции за время работы оборудования на i-ой операции:
, (2.14)
д) расчет величины цикловых заделов:
1) величина технологического задела:
, (2.15)
где Спрi – количество мест-дублеров на i-й операции;
ni– количество одновременно обрабатываемых деталей на одном рабочем месте;
m– количество операций в технологическом процессе.
2) величина межоперационного оборотного задела определяется между двумя смежными операциями:
, (2.16)
гдеТ – период времени одновременной работы оборудования на смежных операциях;
Сi, Сi+1 – количество работающего оборудования на смежных операциях в периодТ;
tштi, tштi+1 – норма штучного времени на смежных операциях.
Полученные расчетные величины заделовиспользуются при построении графиков работы оборудования и эпюрымежоперационных заделов за период ритма R.
Модели и методы расчета оборотного задела и правила построения эпюр[4]:
1. Эпюра представляет собой кусочно-линейную непрерывную функцию.
2. Величина оборотного задела изменяется от нуля до некоторого максимального значения; это максимальный задел .
3. Оборотный задел в начале периода оборота равен заделу в конце периода; это переходящий задел . Построение эпюры и расчет параметров задела для произвольной пары смежных операций iи (i +1) включает следующие шаги.
1) Период оборота линии разбивается на интервалы, в пределах которых состояния операций неизменны.
2) Для каждого интервала решается вопрос о характере изменения задела:
а) он увеличивается, если пополняющая задел операция более производительна, чем берущая из задела, с учетом числа работающих в этом интервале рабочих мест;
б) он уменьшается, если пополняющая операция менее производительна;
в) он неизменен, если обе операции в паре равнопроизводительны (в том числе – обе не выполняются).
3) Линейные функции на всех интервалах связываются в единую эпюру на основании приведенных ранее правил построения эпюр.
4) Для каждого интервала рассчитывается изменение величины задела по формуле:
,(2.17)
гдеТf–продолжительность f-го интервала;
–количество рабочих мест на i-й и (i + 1)-й операциях, выполняемых наf-м интервале.
5) Начиная с нулевой точки, цепным методом рассчитываются величины задела во всех переломных точках эпюры (на границах интервалов) с использованием полученных ранее значений ; при этом часть расчетов может оказаться избыточной, если искомые величины уже найдены.
6) Рассчитывается величина среднего задела как высота прямоугольника, равновеликого фигуре, образованной эпюрой задела.
Таблица 2.4. График работы поточной линии за период ритма R (пример выполнения)
№ операции
| tшт, мин
| Ср i
| Спр i
| № станка
| Загрузка станка, %
| № рабочего
| Загр.рабочего.,%
| График работы оборудования и рабочих за период ритма R
Эпюры межоперационных заделов за период ритма R
|
| 9,61
| 0,84
|
| 14 период ритма
|
|
| 0,82
| 84 %
| Zм.о.1 – 2
|
1 1
|
| 9,33
| 0,82
|
|
|
|
| 0,82
| 82 %
| Zм.о.2 – 3
|
|
| 9,33
| 0,82
|
|
|
|
| 0,82
| 82 %
| Zм.о.3 – 4
|
2 2
|
| 8,51
| 0,74
|
|
|
|
| 0,8
| 74 %
| Zм.о.4 – 5
|
6 ujNpLzoFcbRKGOUm5spAHC/XII4K0mQNssjl9QfFLwAAAP//AwBQSwECLQAUAAYACAAAACEAtoM4 kv4AAADhAQAAEwAAAAAAAAAAAAAAAAAAAAAAW0NvbnRlbnRfVHlwZXNdLnhtbFBLAQItABQABgAI AAAAIQA4/SH/1gAAAJQBAAALAAAAAAAAAAAAAAAAAC8BAABfcmVscy8ucmVsc1BLAQItABQABgAI AAAAIQCu2ey7GQIAADAEAAAOAAAAAAAAAAAAAAAAAC4CAABkcnMvZTJvRG9jLnhtbFBLAQItABQA BgAIAAAAIQBfFEqT3gAAAAkBAAAPAAAAAAAAAAAAAAAAAHMEAABkcnMvZG93bnJldi54bWxQSwUG AAAAAAQABADzAAAAfgUAAAAA " strokeweight="1.5pt"/> 2
|
| 9,16
| 0,8
|
|
|
|
| 0,81
| 80 %
| Zм.о.5 – 6
| 9 9
|
| 5,51
| 0,48
|
|
|
|
| S abHjeKHFnrYt1d/V0UbK+iN73mG2n2dTfT7cbd93I1ulrq+mp0cQgaZwLsOvflSHMjod3JG1F0ZB mqxiU8EqS0HEfJmu70Ec/hayLOT/B8ofAAAA//8DAFBLAQItABQABgAIAAAAIQC2gziS/gAAAOEB AAATAAAAAAAAAAAAAAAAAAAAAABbQ29udGVudF9UeXBlc10ueG1sUEsBAi0AFAAGAAgAAAAhADj9 If/WAAAAlAEAAAsAAAAAAAAAAAAAAAAALwEAAF9yZWxzLy5yZWxzUEsBAi0AFAAGAAgAAAAhAOgq su4UAgAALAQAAA4AAAAAAAAAAAAAAAAALgIAAGRycy9lMm9Eb2MueG1sUEsBAi0AFAAGAAgAAAAh AMp9gX/cAAAACAEAAA8AAAAAAAAAAAAAAAAAbgQAAGRycy9kb3ducmV2LnhtbFBLBQYAAAAABAAE APMAAAB3BQAAAAA= " strokeweight="1.5pt"/>0,81
| 48 %
| Zм.о.6 – 7
|
3 3
|
| 4,83
| 9,42
|
|
|
|
| 0,81
| 42 %
| Zм.о.7 – 8
| 10 10
|
| 2,67
| 0,23
|
|
|
|
| 0,8
| 23 %
| Zм.о.8 – 9
| 18
|
| 16,25
| 1,42
|
|
|
| 3 и 4
| 0,81
0,95
|
24 % 47 %
71 %
| Zм.о.9 – 10
|
8 8
|
| 7,89
| 0,69
|
|
|
|
| 0,91
| 69 %
| Zм.о.10 – 11
|
|
| 5,4
| 0,47
|
|
|
| 5 и 6
| 0,91
| 25 % 22 %
| Zм.о.11 – 12
|
3 3
|
| 7,59
| 0,66
|
|
|
|
| 0,91
| 66 %
| Суммарный межоперационный задел на начало и конец смены:
Zм.о= (2.18)
3) страховой задел берется в размере технологического задела
Кроме того на операции N 025 организуется дополнительный задел в размере двух деталей, который дает возможность организовать параллельное многостаночное обслуживание.
Суммарный цикловой задел определяется:
Zц = Zm +Zм.о + Zстр + Zд(2.19)
Расчет среднесписочной численности рабочих на поточной линии)
,(2.20)
гдеαдоб– добавочный процент числа рабочих-операторов на случай невыхода на работу (очередные и ученические отпуска, болезни, рекомендуемое значение 10-12%;
Нобс – норма обслуживания рабочих мест на i-й операции.
Таблица 2.5. Численность работающих на поточной линии
Категории работающих
| Количество, чел.
| Производственные рабочие, в том числе:
а) основные
б) вспомогательные
|
| Итого
|
| 2.2. Организация предметно-замкнутых участков (ПЗУ) по изготовлению комплекта деталей.
Теоретические основы формирования ПЗУ изложены в разделе 1. Процесс формирования ПЗУ начинается с определения производственной программа выпуска деталей каждого наименования (Nj), типа производства, разработки технологического процесса и расчета норм времени на обработку деталей каждого наименования по конкретной операции (tшт.ij), подготовительно-заключительного времени (tn-з.ij),допустимых потерь времени на переналадку и плановые ремонты оборудования (tно), определения баланса рабочего времени в плановом периоде (Фэф) и установления режима работы участка (sсм).
Пошаговый расчет календарно-плановых нормативов участка серийной сборки. К числу основных календарно-плановых нормативов участка серийной сборки относятся:
- размер партии изделий (n):
- ритм (К) партии;
- стандарт-план участка серийной сборки;
- длительность производственного цикла (tц);
- заделы (Z);
- незавершенное производство (Нср).
Партия – это заранее установленное количество одноименных предметов труда, изготовленных при одной наладке оборудования (рабочих мест) и, следовательно, при однократных затратах подготовительно-заключительного времени.
Размер партии – очень важный календарно-плановый норматив, оказывающий существенное влияние на производительность труда рабочих, себестоимость изготовления продукции, длительность производственного цикла и объем незавершенного производства.
Размер партии зависит от многих экономических и организационно-производственных факторов, причем действующих в противоположных направлениях. Так, например, увеличение размера партии ведет, с одной стороны, к снижению подготовительно-заключительного времени на единицу продукции, а следовательно, к росту производительности труда и снижению себестоимости продукции, а с другой – к увеличению длительности производственного цикла, величины заделов, незавершенного производства, а следовательно, и величины оборотных средств. Поэтому правильное определение размера партии имеет важное экономическое значение.
Размер партии на практике, как правило, устанавливают в два этапа.
На первом этапе устанавливают минимальный размер партии (nmin). Он определяется по допустимому проценту потерь на подготовительно-заключительное время по следующим формулам:
а) для одной операции:
;
б) для совокупности операций (например, участка):
,
где η– допустимые потери рабочего времени на текущий ремонт и подналадку рабочих мест, принимаются в пределах 2-5%;
tп-з.i– подготовительно-заключительное время на выполнение i-й операции, мин;
tшт.i– штучное время на выполнение i-й операции, мин;
т– количество операций, выполняемых на рабочих местах участка.
В проекте в качестве максимального размера партии (птах) следует принять месячную программу собираемых изделий.
На втором этапе осуществляют корректировку полученных значений nminи птахпо всем факторам, не учтенным в расчетах. К числу таких факторов относят:
- необходимость согласованности размера партии изделий и программы их выпуска;
- необходимость согласованности размеров партий на участке, в цехе, между цехами.
Таким образом, в результате проведения первого этапа будут получены пределы нормального размера партии:
.
Корректирование же предельных размеров партии всегда начинается с установления удобопланируемых ритмов. Удобопланируемый ритм – это такая его величина, которая укладывается целое число раз в планируемый период. Ряд удобопланируемых ритмов (R) в течение месяца в рабочих днях, например, при 20 рабочих днях составляют 20, 10, 5, 4, 2, 1; при 21 рабочем дне – 21, 7, 3, 1; при 22 рабочих днях – 22,11,2,1. Неучтенные в рядах (R) один-два рабочих дня в течение месяца являются резервными на случай ликвидации отклонений от плана. Ритм (периодичность чередования) партии определяют по формуле:
,
где Тпл – продолжительность планового периода, в днях;
пmin– минимальный размер партии изделий, шт.
Nмес– заданная программа выпуска (запуска) изделий в планируемом периоде, шт.
Если при расчете получилось дробное число, например 2,49 дня при Тпл= 21, следует выбрать из ряда удобопланируемых ритмов ближайшее целое число. В данном случае надо принять Rnp= 3. Далее в соответствии с принятым Rпркорректируют размер партии по формуле:
.
При наличии брака на отдельных операциях размер партии изделий устанавливают следующим образом:
- исходя из месячной программы выпуска Nвыпопределяют программу запуска (Nзап) (формула (2.30));
- рассчитывают количество партий изделий за плановый период.
Количество партий изделий рассчитывают по формуле:
(парт).
Размер партии для каждой операции определяют по формуле:
(шт.).
Определив размер партии изделий (пн), устанавливают длительность операционного цикла партии изделий по операциям (ton) и по сборочным единицам (tсб.ед). Расчет ведется по формулам:
,
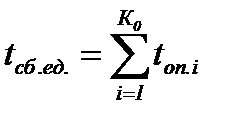
где – штучное время на каждой i-й операции с учетом коэффициента выполнения норм времени, мин;
Ко– количество операций определенной сборочной единицы (например, сборочная единица АБ включает шесть операций).
Результаты расчетов заносят в таблицу (графы 9 и 10 табл. 1 в примере 2.5).
Исходя из длительности циклов операций и сборочных единиц строят цикловой график сборки партии изделий в порядке, обратном ходу технологического процесса, но без учета загрузки рабочих мест (рис. 2а к примеру 2.5).
Для достижения равномерности загрузки рабочих мест и рабочих-сборщиков исходя из общей трудоемкости изготовления партии изделий и принятого ритма определяют необходимое количество рабочих мест. Расчет ведется по формуле:
,
где т – общее количество сборочных операций.
После определения количества рабочих мест операции закрепляют за рабочими местами (табл. 2а в примере 2.5), строят цикловой график с учетом загрузки рабочих мест и составляют стандарт-план работы сборочного участка (рис. 2б к примеру 2.5).
Затем строят уточненный цикловой график сборочного процесса (рис. 2в к примеру 2.5) и определяют опережение запуска-выпуска всех сборочных единиц и окончательную длительность производственного цикла.
Длительность производственного цикла применительно к участку серийной сборки (tц) – это промежуток времени от начала работы по выполнению первой по времени операции над партией предметов труда до окончания работы по выполнению последней операции над этой же партией.
Определяется tцисходя из графика стандарт-плана (см. рис. 2в к примеру 2.5; в рассматриваемом примере tц = 96 ч).
Заделы на участке серийной сборки – это детали, мелкие сборочные единицы, узлы, подузлы, блоки, запущенные в производство и находящиеся на рабочих местах, но не законченные изготовлением на той или иной технологической стадии. Среднюю величину задела на участке серийной сборки определяют по следующим формулам:
а) в штуках:
;
Б) в партиях:
,
где tц– длительность производственного цикла сборки партии предметов труда, дн.
Незавершенное производство – это выраженная в трудоемкости или в стоимостном выражении, а следовательно в сопоставимом виде, величина заделов.
Средняя величина незавершенного производства в нормо-часах может быть рассчитана следующим образом:
а) без учета затрат труда на предыдущих операциях производства по формуле:
, (нормо-ч);
б) с учетом затрат труда на предыдущих стадиях производства по формуле:
, (нормо-ч).
Среднее значение незавершенного производства в денежном выражении может быть выражено без учета и с учетом затрат на предыдущих стадиях производства. Расчет можно выполнить с использованием следующих формул:
а) без учета затрат на предыдущих стадиях производства:
;
б) с учетом затрат на предыдущих стадиях производства:
,
где Сц– цеховая себестоимость предмета труда;
Спред– затраты на предшествующих стадиях обработки.
Для сборочных цехов Сцможно установить на уровне 85% полной себестоимости изделий, тогда Нсрс учетом затрат на предыдущих стадиях производства примет вид:
.
Вид и необходимое количество транспортных средств определяют так же, как и для ОППЛ.
Пошаговый расчет ПЗУ. Чтобы организовать работу ПЗУ, необходимо рассчитывать следующие календарно-плановые нормативы (КПН)[5]:
1) размеры партии деталей (пj);
2) периодичность чередования партий деталей (Rnp.j);
3) число партий по каждомуj-му наименованию деталей (Хj);
4) количество единиц оборудования по каждой операции (Спр.i)и коэффициента его загрузки (Кз.i);
5) пооперационно-подетальный стандарт-план;
6) продолжительность производственного цикла обработки партиидеталей каждогоj-го наименования (Тцj);
7) нормативы заделов (Zj);
8) нормативы незавершенного производства (Нсрj).
1) Размер партии деталей по каждому j-му наименованию определяют, как правило, в два этапа:
Этап 1 - расчет (минимальной) величины размера партии деталей j-гoнаименования поформуле:
,(2.21)
гдеηно– допустимый процент потерь времени на текущий ремонт и переналадку оборудования (в пределах 2-5 %);
m– число операций на детали j-го наименования.
Потери времени на переналадку оборудования можно определить по формуле:
,
где Тнал – трудоемкость одной наладки;
nзап –число запусков в год;
N – годовая программа выпуска данных деталей.
За максимальный размер партии деталейj-го наименованияследует принять месячную программу выпуска Nмi.
Этап 2– корректировка полученных размеров партии деталей, т.е. nminjи nmaxj. Нормальный (оптимальный) размер партии nнjограничен неравенством:
.(2.22)
Корректировка предельных размеров партии деталей j-го наименования начинается с установления удобопланируемых ритмов. Их величина зависит от количества рабочих дней в месяце: при 22 рабочих днях–удобопланируемыми ритмами являются – 22,11,2,1 день; при 21 рабочем дне – 21,7,3, 1; при 20 рабочих днях – 20, 10,5,4,2, 1.
2) Период чередования партий деталейj-го наименования (Rnpj) рассчитывают по формуле:
.(2.23)
Если по расчету получаются дробные числа, из ряда удобопланируемых ритмов выбирают ближайшие целые числа.
Далее для деталей ПЗУ всех j-х наименований принимают общий (максимальный из всех принятых) период чередования. После этого корректируют размеры партий деталей каждого j-гoнаименования по формуле:
.(2.24)
3) Число партий по каждомуj-му наименованию деталей (Xj) определяют по формуле:
.(2.25)
4) Число единиц оборудования по каждой i-й операции рассчитывается по формуле:
.(2.26)
Потребное количество оборудования затем сопоставляется с фактическим количеством оборудования по данной группе(Сфj). Из сопоставления можно получить средний коэффициент загрузки оборудования:
(2.27)
и коэффициент соответствия имеющегося количества оборудования потребному его числу:
.(2.28)
В случае построения производственного процесса по принципу концентрации операций необходимое количество оборудования для обработки изделий i-гo наименования Cjопределяется по формуле:
,(2.29)
гдеkn – коэффициент, учитывающий потери времени по организационно-техническим причинам;
qne– часовая (цикловая) производительность оборудования, шт/ч:
,(2.30)
гдеnцi– количество изделий, обрабатываемых за цикл;
Tц i– цикл изготовления изделия i-гo наименования, час.
Коэффициент загрузки единицы j-го оборудования:
,(2.31)
гдеТу – время работы оборудования по управляющей программе за плановый период, ч;
Тв – время вспомогательных работ, ч;
Тоб – время организационно-технического обслуживания оборудования, ч.
5) Построение стандарт-плана ПЗУ.Пооперационный подетальный стандарт-план устанавливает повторяющиеся стандартные сроки запуска и выпуска партий деталей каждого наименования по каждой операции. Стандарт план строится на определенный период времени (ритм чередования партий деталей принимается Rпр) и работа по нему повторяется из периода в период без изменений до тех пор, пока действует данная производственная программа.
Для всех наименований деталей ПЗУ принимается общий ритм (наибольший из всех принятых).
При построении стандарт-плана разрабатываются три календарных графика.
Порядок построения первого графика. Исходя из установленного срока изготовления партии деталей j-го наименования, на календарный план наносят время циклов обработки каждой партии деталей j-го наименования по операциям производственного процесса, начиная с последней и кончая первой (в порядке, обратном ходу технологического процесса), без учета загрузки рабочих мест.
Продолжительность операционного цикла (Тц.оп.ij, ч) рассчитывается по формуле:
. (2.32)
Расчет продолжительности операционных циклов по всем деталям и операциям производится в табличной форме (табл. 7.3).
На этом же графике строится собственно стандарт-план, где представлены стандартные повторяющиеся сроки выполнения всех операций обработки партий деталей каждого наименования.
После построения графика 2 строится уточненный график 3 технологического цикла обработки партий деталей каждого наименования с учетом загрузки рабочих мест. При этом необходимо стремиться к тому, чтобы время циклов отдельных операций графика 2 являлось проекциями на графике 3. По этому графику определяются продолжительность технологического цикла партий каждого наименования, опережение запуска, выпуска, время пролеживания партий деталей в ожидании высвобождения оборудования от обработки предыдущей партии и общая продолжительность производственного цикла комплекта партий деталей (Тцк), изготавливаемых на ПЗУ.
6)Расчет продолжительности производственного цикла. Проводится по каждой партии деталей каждого наименования по стандарт-плану (графический метод) и по формулам (аналитический метод).
При расчете по графику с учетом загрузки рабочих мест и времени пролеживания деталей, продолжительность производственного цикла составляет соответственно: ТцА=7,5 смены, ТцБ = 9 смен, Тцв = 9 смен, а общая продолжительность производственного цикла комплекта партий деталей Тцк =11,5 смены. Время опережения запуска-выпуска с учетом пролеживания составляет 2,5 смены (см. рис. 7.1, в).
Аналитическим методом продолжительность производственного цикла определяется по формуле (приблизительное значение, так как в формуле не учитывается время пролеживания деталей и принимается среднеарифметическое значение числа единиц оборудования):
,(2.33)
гдеtзах– время на одну заходку деталей в другие цехи, мин;
ωз– число заходов партии деталей в другие цехи;
te– время, затрачиваемое на естественные процессы (сушка, остывание и др.), мин.
7)Определение среднего размера заделов.Размер задела по j-му наименованию деталей определяется по формуле:
(2.34)
8)Определение незавершенного производства.Величина незавершенного производства без учета затрат труда на предыдущих стадиях обработки деталей рассчитывается по формуле:
.(2.35)
Пример расчета ПЗУ. Исходные данные
На ПЗУ обрабатывают комплект корпусных деталей, перечень которых, виды заготовок, марки, нормы расхода, оптовые цены материала и реализуемых отходов приведены в табл. 2.6.
Таблица 2.6 - Исходные данные
Наименование
детали
| Месячная программа выпуска, шт.
| Вид
заготовки
| Материал (марка)
| Норма
расхода, кг
| Чистый вес
детали, кг
| *Оптовая цена 1 кг, руб.
| материала
| отходов
| 1. Корпус1К(А)
|
| Литье
| Сталь 45л
| 35,0
| 30,0
| Уточнить!
| Уточнить!
| 2. Корпус 2К(Б)
|
| Литье
| Сталь 45л
| 42,0
| 35,0
|
|
| 3. Корпус 3К(В)
|
| Литье
| Сталь 45л
| 55,0
| 45,0
|
|
| Примечание.*Уточнить цены на момент выполнения проекта
Количество рабочих дней в месяце (Др) –22.
Режим работы ПЗУ (Ксм) – двухсменный.
Продолжительность рабочей смены – 8 ч.
Не нашли, что искали? Воспользуйтесь поиском по сайту:
©2015 - 2025 stydopedia.ru Все материалы защищены законодательством РФ.
|