Ножницы для резки металлолома
Резание длинномерного металлолома на ножницах относится к высокопроизводительному и экономичному способу разделки, имеющему тенденцию к дальнейшему развитию. На ножницах режут металлолом из сортового проката (швеллеры, уголки, двутавры и т. д.), трубы, штанги, обрезь толстого листового металла, различного рода балки и т. д. На предприятиях и в цехах по переработке металлолома используют ножницы двух типов — аллигаторные и гидравлические, отличающиеся по устройству и принципу работы.
Отечественная промышленность выпускает три типоразмера аллигаторных ножниц (Н-2228, Н-2230 и Н-2231), одинаковых по устройству, но отличающихся по мощности. Эти ножницы позволяют производить резку металла с допускаемой площадью поперечного сечения соответственного, 80 и 145 см3 при пределе прочности материала до 500 МПа.
Устройство аллигаторных ножниц Н-2230 приведено на рис.2. Основными узлами ножниц являются режущий механизм, привод, станина и упор. Литая станина 9 ножниц выполнена с двумя массивными стойками, в которых расположены опоры 2 качающейся челюсти 4, подшипниковые узлы 10 коленчатого вала и зубчатых передач. В передней части станины закреплен нижний нож 14 (рис. 3).
Режущий механизм состоит из качающейся челюсти с закрепленным на ней ножом 15,шатуна и коленчатого, вала и по кинематической схеме представляет собой шарнирный четырехзвенный механизм. (рис. 3)
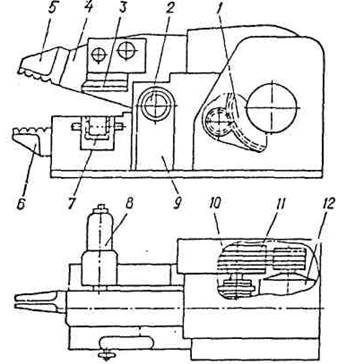
Рис. 2. Аллигаторные ножницы Н-2230
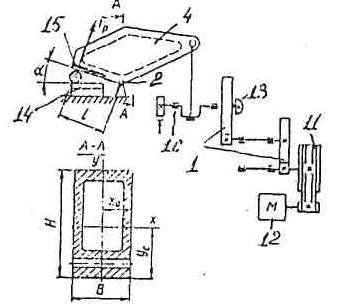
Рис. 3. Кинематическая схема аллигаторных ножниц
Коленчатый вал (рис.2) вращается от электродвигателя 12 через клиноременную 11 и две понижающие зубчатые 1 передачи. Для предохранения ножниц от поломок при перегрузках установлена фрикционная муфта предельного момента. Большой шкив клиноременной передачи выполняет в приводе роль маховика. Включение и выключение ножниц производят муфтой включения с поворотной шпонкой 13 (рис. 3) вмонтированной в ступицу зубчатого колеса последней передачи. Муфтой управляют ножной педалью через рычажную систему. Предусмотрена возможность управления ножницами переносной электрической педалью. Для остановки челюсти в крайнем верхнем положении на коленчатом валу установлен тормоз периодического действия с эксцентрично закрепленным шкивом. Подвижная 5 и неподвижная 6 губки позволяют производить обжатие труб перед резкой. Щека 3 осуществляет прижатие металлолома, а упор 8 препятствует его перекосу в процессе резки. Ролик 7 станины облегчает ручную подачу металлолома в зев ножниц.
Наиболее мощные аллигаторные ножницы Н-2231 снабжены электродвигателем мощностью 39,9 кВт; число ходов подвижной челюсти в минуту — 16; масса ножниц — 23 т.
Преимущества аллигаторных ножниц состоят в простоте устройства, в надежности работы и малых габаритах, недостатки — в недостаточной мощности для резки металлолома крупного сечения, в больших затратах ручного труда при подаче металла в зев, повышенной опасности для обслуживания.
Гидравлические ножницы
Для резания металлического лома больших сечений применяются гидравлические ножницы, отличающиеся высокой производительностью при полной механизации процессов. Техническая характеристика ножниц приведена в табл. 1.
Таблица 1. Технические характеристики гидравлических ножниц
Параметры
| Модель ножниц
|
| Н-2335
| Н-2338
| Н-302
| НО-340
| Н-1600
| Максимальное усилие реза-
ния, 10 кН 315 630 1000 1000 1600
Усилие смятия и прижима,
10 кН 120 3X80 400 400 400
Усилие боковой подпрес-
совки, 10 кН — — — 200 —
Усилие толкателя подающего
механизма, 10 кН 10 20 32 32 —
Длина ножей, мм 1400 1650 2000 2100 2200
Наибольший ход ножа, мм 650 950 1200 1250 1400
Ход механизма подачи, мм 5000 7000 12 000 12 000 12 000
Число резов в 1 мин 6 3 3 1,5 3
Производительность, т/ч 5 до 10 10-20 10—20 —
Размеры сечении разрезаемо-
го металлолома:
диаметр круга, мм 90 140 190 190 220
размеры полосы, мм 50X750 50X1200 70X1850 70X1850 70X2000
Установочная мощность элек- тродвигателей, кВт 250 658 708,8 600 900 Масса ножниц с гидроприво- дом, т 70 175 207 390 600
Современные ножницы оборудуются механизмами резания, подпрессовки и прижима, а также комплексом вспомогательных механизмов, обеспечивающих подачу и уборку лома.
Гидравлические ножницы (рис. 4, а)типа НО-340 состоят из следующих основных узлов и механизмов: корпуса ножниц 1 с механизмами резания 3 и прижима 4; механизма боковой подпрессовки 5; механизма загрузки с коробом 6; загрузочного желоба 13 и крышки желоба 7 с механизмом поворота; механизма подачи 9; механизма отвода толкателя 11.
Механизмы резания и прижима (рис. 4, б)находятся в сборной литой станине 1, выполненной в виде отдельных элементов коробчатого сечения (на рисунке условно заштрихованы), скрепленных колодами и стяжками.
Механизм резания состоит из подвижного верхнего суппорта 3 с шевронным ножом 14, неподвижного суппорта 15 с нижним прямым ножом, тяг 17, двух плунжерных гидроцилиндров 16 и траверсы 19. Суппорт 3 перемещается в клиновидных V-образных направляющих стоек станины и соединен с нижней траверсой тягами. Усилие при резании создается гидроцилиндрами 16, опирающимися плунжерами через сферические подпятники 18 на нижнюю траверсу. Возврат подвижного суппорта производится гидроцилиндром" обратного хода (на рисунке не показан), соединенного плунжером с траверсой 19.
В процессе резания, кроме усилия резания Fр, возникают горизонтальные силы Т, которые взаимоуравновешиваются.
Механизм прижима обеспечивает подпрессовку и фиксацию лома по вертикали во время резания. Механизм прижима по схеме расположения аналогичен механизму резания, но имеет один рабочий гидроцилиндр.
Механизм боковой подпрессовки (рис 4 , в)служит для смятия лома в горизонтальном направлении и ориентирования его при подаче к ножам. Он представляет собой открытую с торцов камеру 22, внутри которой навстречу друг другу перемещаются два штемпеля 21, приводящихся в движение от гидроцилиндров 20.
Механизм загрузки (рис. 4 , г)состоит из короба 6, который поворачивается с помощью двух качающихся гидроцилиндров 23, обеспечивая сброс лома в желоб.
Механизм поворота крышки 7 желоба (рис. 4, г)осуществляет частичное сминание лома перед подачей в камеру боковой подпрессовки, а также удерживает лом от выпучивания при проталкивании в зону резания. Поворот производится качающимся гидроцилиндром 24,. развивающим усилие до 800 кН.
Механизм подачи периодически проталкивает лом вдоль желоба к ножницам. Он состоит из толкателя 8 со штангой 10, которая на.верхней поверхности имеет рейку со скошенными зубьями, а на нижней поверхности — рейку с модульными зубьями. Штанга продвигается штоком гидроцилиндра 9 и поддерживается роликами 12.
Механизм отвода толкателя (рис. 4, д) имеет электромеханический редукторный привод, соединенный через управляемую кулачковую муфту с зубчатой шестерней 11. Последняя находится в зацеплении с зубчатой рейкой штанги 10. При работе толкателя электродвигатель выключают, а муфту 25 с помощью электромагнита размыкают. Ножницы работают в следующей последовательности (рис. 4, а). Металлолом загружается магнитом или многочелюстным грейфером в короб 6, при повороте лом ссыпается в желоб 13. Далее толкатель 8 механизма подачи периодически продвигает лом вдоль желоба в камеру боковой подпрессовки 5 и в пресс-камеру. После уплотнения лом 2 режется на мерные куски и по склизу падает в приемный короб. В это время короб 6 заполняется новой порцией лома.
Машинный зал гидравлических ножниц расположен ниже уровня пола. В зале установлены два горизонтальных плунжерных насоса, создающих рабочее давление 32 МПа, электродвигатели мощностью 320 кВт и частотой вращения ротора 375 об/мин, а также гидроаппаратура.
Рис.4 . Гидравлические ножницы НО-340:
а — принципиальная схема; б — механизм резания; в — механизм боковойподпрессовки; г — механизм загрузки и поворота крышки желоба; д — механизм отвода толкателя.
Стальная стружка, используемая при плавке в сталеплавильных агрегатах в насыпном виде, должна иметь длину не более 100 мм, а подготовленная к брикетированию на прессах — не более 50 мм. Дробление стружки на машиностроительных заводах и предприятиях Вторчермета производят валковыми, молотковыми и конусными стружкодробплкамп, а также стружкодробильнымп агрегатами, созданными на основе валковых стружкодробилок.
Конусные, валковые и фрезерные стружкодробилки работают в основном на принципе измельчения стружки резанием между неподвижными и вращающимися ножами.
Фрезерные стружкодробилки. Стружкодробилки предназначены для резания витой стружки углеродистых сталей. Основные технические данные стружкодробилки СК-2М: производительность — 1,6 – 2 т/ч; частота вращения вертикального ножевого вала — 32,5 об/мин; диаметр воронки — 1125 мм; мощность электродвигателя — 28 кВт; средняя длина измельченной стружки — 75 мм; масса — 5,4 т.
Фрезерная стружкодробилка (рис. 5) состоит из корпуса, конической воронки 2 с неподвижными фигурными ножами 3, вертикального вала 6 с конической 4 и цилиндрической 5 ножевыми головками, конической зубчатой пары 9, клиноременной передачи 7 и электродвигателя 8. Стружка загружается в воронку и последовательно проходит верхнюю и среднюю зоны дробления коническими ножами и нижнюю зону дробления цилиндрическими ножами. Их недостаток – невысокая степень дробления и отсутствие механизации загрузки.
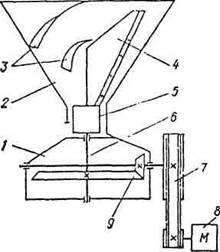
Рис. 5 . Кинематическая схема фрезерной стружкодробилки МИКСЕРЫ
Не нашли, что искали? Воспользуйтесь поиском по сайту:
©2015 - 2024 stydopedia.ru Все материалы защищены законодательством РФ.
|