ТЕМА 5. СТРОИТЕЛЬНЫЕ КОНСТРУКЦИИ ИЗ АЛЮМИНИЕВЫХ СПЛАВОВ
ОБЩАЯ ХАРАКТЕРИСТИКА АЛЮМИНИЕВЫХ КОНСТРУКЦИЙ.
ОСОБЕННОСТИ КОНСТРУКЦИЙ ИЗ АЛЮМИНИЕВЫХ СПЛАВОВ
Конструкции из алюминиевых сплавов обладают общими для металлических конструкций достоинствами: индустриальностью изготовления, транспортабельностью, сборностью, возможностью осуществления монтажа крупными блоками, разборностью, долговечностью и надежностью в эксплуатации.
Алюминиевые конструкции наиболее легки, даже по сравнению со стальными, поскольку отношение расчетного сопротивления к плотности при одинаковой прочности сопоставляемых материалов у алюминия примерно в 3 раза выше, чем у стали. Снижение собственного веса конструкции в свою очередь:
уменьшает усилия в элементах конструкций, особенно большепролетных, а также подвергающихся сейсмическим воздействиям;
снижает транспортные расходы, объемы и сроки монтажа;
сокращает расход энергии при эксплуатации подвижных конструкций.
Благодаря значительной антикоррозионной стойкости алюминия, которая к тому же может быть повышена оксидированием, эмалированием и другими способами, снижаются эксплуатационные расходы и возрастает долговечность конструкций, что особенно важно при наличии агрессивной среды. Отличительной особенностью алюминиевых конструкций по сравнению со стальными является также возможность обеспечения особых эксплуатационных требований благодаря таким свойствам материала, как высокая отражательная способность полированной поверхности, антимагнитность, петоксичность, а также неспособность к образованию искр при ударах.
Немаловажное значение для строительных конструкций имеет их внешний вид, который при применении алюминия может быть улучшен благодаря фактуре самого материала, а также возможности использования архитектурных деталей, разнообразных форм и рисунка, изготовляемых в заводских условиях.
МАТЕРИАЛЫ АЛЮМИНИЕВЫХ КОНСТРУКЦИЙ
Алюминий — серебристо-белый металл, растворимый в некоторых кислотах и едких щелочах. На воздухе алюминий быстро покрывается плотной окисной пленкой, предохраняющей поверхность изделия от дальнейшего окисления. Показатели основных физических свойств алюминия следующие:
плотность (среднее значение) р, кг/м3
модуль продольной упругости Е, МПа 70 х103
модуль сдвига G, МПа 26,5х103
коэффициент поперечной деформации
(Пуассона) в стадии упругой работы материала v 0,3 коэффициент продольной температурной деформации аt,1/°С 23х10-6
температура плавления алюминия технической чистоты tпл, °С 658
Алюминий обладает хорошей теплопроводностью: и электропроводностью, малым захватом нейтронов, он не магнитен и не способен к ценообразованию при ударе, в полированном виде обладает высокой отражательной способностью. По плотности алюминий уступает только двум металлам — магнию (1,74 т/м3) и бериллию (1,85 т/м3). Технически чистый алюминий имеет: низкую прочность (qб =60...70 МПа; Q0.2=20...30 МПа) и высокую пластичность (∑>30 %). Значительное увеличение прочности алюминия достигается легированием его магнием, марганцем, кремнием, медью, цинком и некоторыми другими элементами. Временное сопротивление легированного алюминия (алюминиевых сплавов) в зависимости от состава легирующих добавок в 2—5 раз выше, чем у технически чистого, однако относительное удлинение при этом снижается в 2—3 раза.
Наряду с отмеченными положительными свойствами для алюминия характерны и такие свойства, которые нередко приводят к снижению эффективности его применения в строительных конструкциях.
К ним относятся: почти в 3 раза меньшие, чем у стали, значения модуля упругости и модуля сдвига; более низкий, чем у стали, предел выносливости; незрительное понижение показателей прочности при температуре выше 100—150 °С.
Производство алюминия слагается из двух основных процессов: получение глинозема (оксида алюминия А12Оз) из алюминиевых руд и электролизного выделения металлического алюминия из глинозема, растворенного в расплавленном криолите Na3AlF6.
К числу алюминиевых руд с достаточно высоким процентным содержанием оксида алюминия относятся: бокситы (36—65), нефелины (32—36), алуниты (35—37) каолины (38—42) и некоторые др.
По способу производства полуфабрикатов алюминиевые сплавы разделяют на литейные и деформируемые. В строительстве в основном используют деформируемые сплавы, полуфабрикаты из которых получают способом деформации в горячем или холодном состоянии: прессованием (профили, прутки, трубы, панели), прокаткой (листы, ленты), волочением (тонкостенные трубы), ковкой и штамповкой (фасонные детали). Литейные сплавы вследствие их низкой пластичности в строительных конструкциях применяются чрезвычайно редко (так же, как и стальное литье).
По составу основных легирующих компонентов отечественные деформируемые сплавы делятся на группы, каждая из которых включает в себя несколько марок, имеющих свое обозначение. В первые три из рассматриваемых групп входят технически чистый алюминий и сплавы двойных композиций: Аl—Мn и Al—Mg. Термическая обработка этих сплавов не приводит к упрочнению, поэтому сплавы, относящиеся к этим группам, получили название термически неупрочняемых сплавов.
1-я группа. Технически чистым алюминием называют алюминий, общее содержание примесей в котором не превышает 1,2%. По коррозионной стойкости и высокой пластичности технически чистый алюминий близок к химически чистому. Установлены следующие марки технически чистого алюминия: АДО, АД1 и АД с содержанием примесей соответственно до 0,5, 0,7 и 1,2%.
2-я группа. Сплавы системы А1—Мn. Характерным представителем этой группы является сплав АМц, содержащий 1 —1,6 % марганца. Этот сплав обладает высокой коррозионной стойкостью, хорошо сваривается, легко полируется, однако прочность его невелика.
3-я группа. Сплавы системы Al—Mg, называемые магналиями, обозначаются буквами АМг с добавлением цифры, указывающей примерное содержание магния в процентах (АМг2, АМгЗ и т. д.). Эти сплавы содержат также небольшое количество марганца (0,2—0,8%). Сплавы этой группы обладают высокой стойкостью против коррозии, хорошо свариваются. С увеличением содержания магния прочностные показатели повышаются; однако при содержании магния более 3,5 % пластичность и коррозионная стойкость сплавов заметно снижаются. Для улучшения свойств в качестве добавок используют титан (0,02—0,1%), бериллий (0,002—0,005%) и хром (0,05-0,35 %).
4-я группа. Сплавы системы Al—Mg—Si, легированные кремнием (0,3—1,2%) и магнием (0,4—1,4%), называются силуминами. Обозначаются они буквами АД с добавлением порядкового номера (АД31, АДЗЗ, АД35, и т. д.). Сплавы этой группы пластичны, хорошо свариваются, обладают высокой стойкостью против коррозии, хорошо полируются и легко анодируются. К этой же группе относится сплав, дополнительно содержащий до 0,5 % меди. Этот сплав, широко применявшийся ранее в авиастроении и названный поэтому авиалем, обозначается буквами АВ.
5-я группа. Сплавы системы А1—Си—Mg называются дуралюминами. Они обозначаются буквой Д с добавлением порядкового номера (Д1, Дб, Д16, Д18 и т. д.). Свое название дуралюмины получили от латинского слова durus (твердый). Наличие в сплавах этой группы меди в количестве 3,8—4,9%, способствующей увеличению твердости и прочности его после термической обработки, отрицательно сказывается на его пластичности и коррозионной стойкости. Дуралгомин был первым из сплавов, обладающих высокой прочностью.
6-я группа. Сплавы системы Al—Mg—Zn стали применяться сравнительно недавно (с начала 50-х гг.). Отличительной особенностью сплавов, содержащих 3—7 % цинка и около 2 % магния, является их способность к самоупрочнению после прессования полуфабрикатов в горячем виде. Небольшими добавлениями циркония, меди и хрома можно получать более высокопрочные из всех известных алюминиевых сплавов.
Цифровая система обозначения марок построена следующим образом: первая цифра определяет основу сплава: 1 .— алюминий, вторая цифра обозначает композицию легирования (систему) сплава:
0 — технически чистый алюминий;
1 — Al—Cu—Mg; 3 — Al—Mg—Si; 4 — Al—Mn; 5 — Al—Mg; 9 — Al—Mg—Zn.
Последними двумя цифрами обозначается порядковый номер сплава в своей системе.
Полуфабрикаты (листы, профили, трубы, ленты, плиты и т. п.) поставляются заводами-изготовителями при различном состоянии материала: без какой-либо дополнительной обработки (после горячего прессования или проката), в состаренном (после закалки), отожженном, нагартованном или в других возможных состояниях. Поэтому к обозначению марки сплава добавляется обозначение, указывающее состояние материала в полуфабрикатах, подвергнутых той или иной обработке: М — мягкое (отожженное); Н — нагартованное; Н2 — полуна-гартованное; Т — закаленное и естественно состаренное; Т1 — закаленное и искусственно состаренное; Т4 — естественно состаренное после неполной закалки; Т5 — искусственно состаренное после неполной закалки.
Профили, не подвергавшиеся термической обработке (горячепрессованные), после марки сплава дополнительного обозначения не имеют.
Для плакированных листов (покрытых при прокатке тонким слоем чистого алюминия) используют дополнительные обозначения: ПЛАК — плакированные или А — нормальная двусторонняя плакировка; У — утолщенная двусторонняя плакировка. Буквой п (малое) обозначаются прутки. Данные о состояниях материала, в котором заводы производят поставку основных видов полуфабрикатов, приведены в таблице.
ОСОБЕННОСТИ КОНСТРУИРОВАНИЯ И РАСЧЕТА
ЭЛЕМЕНТОВ АЛЮМИНИЕВЫХ КОНСТРУКЦИЙ
Введенные в действие с января 1987 г. нормы проектирования алюминиевых конструкций СНиП 2.03.06—85 являются четвертым по счету нормативным документом, разработанным в нашей стране. По структуре они близки к нормам проектирования стальных конструкций СНиП 11-23-81*.
Из большого числа сплавов различных композиций, производимых отечественной промышленностью, к использованию в строительстве нормы рекомендуют шесть марок деформируемого алюминия и один литейный. В числе деформируемых сплавов три марки термически неупрочняемого алюминия (АД1М, АМц, АМгМ) и три марки термически упрочняемого (АД31, 1915, 1935). Литейный сплав (АМ8) относится к числу термически не-упрочняемых (табл. 10.1). Некоторые из сплавов применяются в различных состояниях поставки. Например, сплав марки АД31 — в четырех различных состояниях (Т, Т1, Т4, Т5). Ограниченное число марок сплавов продиктовано производственными соображениями.
В нормах приведены рекомендации по использованию марок алюминия и полуфабрикатов из них в зависимости от назначения конструкций, которые разбиты на четыре группы применения: группа I — ограждающие и другие конструкции типа оконных и дверных заполнений, подвесных потолков, перегородок, витражей и т. п.; группа II — конструкции, выполняющие одновременно несущие и ограждающие функции:' блоки покрытий, кровельные и стеновые панели и т. п.; группа III — несущие сварные конструкции: фермы, колонны, прогоны, пространственные решетчатые покрытия, сборно-разборные конструкции каркасов зданий, покрытия больших пролетов и др.; группа IV — клепаные конструкции, а также элементы конструкций, не имеющие сварных соединений.
Основное расчетное сопротивление алюминия R, принятое единым при расчетах на растяжение, сжатие и изгиб, установлено делением нормативного сопротивления Rn на коэффициент надежности по материалу γт. При этом за нормативное сопротивление принимают либо условный предел текучести, либо временное сопротивление разрыву, значения которых установлены ГОСТом и ТУ. Диаграмма q—e алюминия не имеет выраженной площадки текучести, поэтому за предел текучести принято напряжение, соответствующее остаточному удлинению, равному 0,2 %. Численные значения коэффициентов надежности по материалу при нахождении расчетного сопротивления по пределу текучести приняты γm=l,l, при вычислении расчетного сопротивления по временному сопротивлению разрыву γт = 1,45.
За расчетное сопротивление принимается меньшее из двух значений, определенных по σо и σв.
Для конструкций, эксплуатируемых при расчетной температуре наружного воздуха 51 — 100 СС, расчетные сопротивления понижаются умножением основного расчетного сопротивления на коэффициент γt. Значение этого коэффициента для алюминия марок АМг2, АД31, 1915, 1935 и АЛ8 вне зависимости от состояния поставки γt —0,9 и для алюминия марок АД1 и АМц — γt = 0,85.
Расчетные сопротивления алюминия на срез Rs, смятие торцевой поверхности Rv и смятие местное при полном касании Riv установлены умножением основного расчетного сопротивления R на соответствующие коэффициенты перехода: γs —0,6; γр=1,б и γt р=0,75.
На прочность конструкции рассчитывают по упругой стадии работы материала. Исключение составляют некоторые виды листовых конструкций, эксплуатация которых допускается в стадии развития пластических деформаций. В этих случаях расчетное сопротивление алюминия марки АМг2М на растяжение принимается увеличенным против основного на 20 %, а для марок АД1Ми АМцМ — на 40 %.
Значения коэффициентов условий работы ус для элементов алюминиевых конструкций приняты немного сниженными по сравнению с коэффициентами для стальных конструкций. Например, для сжатых элементов решетки плоских ферм γс = 0,75 при λ>50 и γс = 0,9 при λ >=50, вместо γс = 0,8 при λ >=60 для стальных элементов; в пространственных конструкциях для раскосов из одиночных уголков при креплении их к поясам одной заклепкой или болтом γс =0,6 вместо γс = 0,75.
В связи с пониженным значением модуля упругости предельные значения гибкостей для сжатых и для растянутых элементов алюминиевых конструкций установлены на 20—30 % ниже, чем для стальных. На 25 % снижена предельная гибкость для отдельных ветвей составных центрально-сжатых стержней ([>v]=30, против. [>.]=40 для стального стержня). По тем же соображениям предельное расстояние между соединениями (прокладками, шайбами и т. п.) составных сжатых элементов, рассчитываемых как сплошностенчатые, уменьшено до 30% (против 40%).
РАСЧЕТ ЭЛЕМЕНТОВ КОНСТРУКЦИЙ
Центрально-растянутые и центрально-сжатые элементы. При расчете на прочность стержней, работающих на осевую силу, должно удовлетворяться условие N<=AnRyc. Использование алюминия взамен стали в центрально-растянутых стержнях позволяет существенно снизить их массу. Получаемый при этом эффект можно выразить значением Km.t, определяемым как отношение массы алюминиевого стержня к массе стального
Km.t = mal/mst=palRst/pstRal
При использовании163 МП алюминия с расчетным сопротивлением выше значение Km.t <0,5, а следовательно, масса стержня снижается в 2 раза и более. Применение алюминия меньшей прочности не дает значительного эффекта, а при Ral =80 МПа масса алюминиевого стержня оказывается даже больше стального (Km.t >1).
Расчет на устойчивость сплошностенчатых стержней, подверженных сжатию осевой силой, выполняются по формуле
N<=AφRγc, где φ=σcr / R
В стадии упругой работы материала (точнее до предела пропорциональности) критическое напряжение потери устойчивости стержня определяется уравнением Эйлера σэ = π2Е/λ2. На значение критического напряжении существенно влияет модуль упругости, который для алюминия почти в 3 раза меньше, чем у стали. Нижняя граница применимости уравнения Эйлера для алюминия марки 1915Т (σpr =180 МПа) соответствует гибкости λэ = 3,14 1/70 000/180 = 62 (рис. 10.2). Для стали марки ВСтЗпсб—1 (σpr =190МПа) λэ =3,14/206 000/190= 104.
Значения коэффициентов f, установлены с учетом наличия возможных начального искривления оси стержня и случайного эксцентриситета действия сжимающей силы, а также влияния формы сечения. На устойчивость алюминиевого стержня перечисленные факторы влияют несколько больше, чем на устойчивость стального стержня.
Потеря устойчивости сжатого стержня, поперечное сечение которого имеет только одну ось симметрии (тавр, швеллер и др.), происходит в изгибно-крутильной форме. При этом значения критического напряжения и, следовательно, коэффициента f оказываются несколько меньшими, чем для стержня, имеющего в сечении две оси симметрии.
Вследствие относительно низких значений коэффициента φ использование алюминия в сжатых стержнях большой и даже средней гибкости оказывается нецелесообразным.
Зависимости,
Km.с= mal/mst= palRst
выражающие отношение погонных масс центрально сжатых стержней,которые обладают равной несущей способностью при
одинаковых расчетных длинах, форме и высоте сечения (а, следовательно, и близких по гибкости), позволяют в первом приближении оценить возможности снижения массы стержня при замене стали марки ВСтЗпсб—1 на алюминий соответствующей марки.
Следует отметить, что использование сплавов высокой прочности в сжатых стержнях мало эффективно даже при малых гибкостях. Так, при λ = 30 замена сплава АД31Т1 сплавом 1915Т с расчетным сопротивлением на 33 % выше, чем у первого, позволяет улучшить показатель массы всего на 10 %. С увеличением гибкости этот процент постепенно снижается и при λ=110 значение коэффициента К т.с для всех сплавов приближается к единице. В этом случае алюминиевый стержень имеет такую же погонную массу, как и стержень из стали марки ВСтЗпсб—1, а площадь сечения алюминиевого стержня
Aal=Ast pst / pal
должна быть почти в 3 раза больше, чем стального.
Увеличение радиуса инерции за счет высоты сечения позволяет снизить гибкость стержня и, следовательно, улучшить показатель Кт.с.
Элементы, работающие на поперечный изгиб (балки). Алюминиевые балки рассчитывают на прочность по тем же формулам, что и стальные. Учет пластических деформаций при этом не допускается. Это связано с более ограниченной, чем у стали, зоной упругопластической стадии работы материала, а также с недостаточной изученностью действительной работы изгибаемых элементов из алюминия в стадии развития пластических деформаций материала.
Эффективность использования алюминия взамен стали в балках, несущая способность которых определяется расчетом на прочность (M<=Wn Ryc), может быть охарактеризована отношением масс алюминиевой и стальном балок mal/mst. При одинаковых характеристиках сечении (Wat=W st; Aal=Ast) значение Кт.б.=mа1/т st имеет тот же закон изменения, как Km.t.
Общую устойчивость балки двутаврового сечения, изгибаемой в плоскости стенки, проверяют по формуле
M= WcφbR γc,
где φb= σcr.b /R
Выражение критического напряжения потери устойчивости изгибаемого стержня имеет сложную зависимость
σcr.b=ks/2 l0/h*Jy/Jx*(h/l0)2 
Поскольку значения модуля продольной упругости и модуля сдвига алюминия примерно в 3 раза меньше соответствующих значений для стали, то и критические напряжения при всех остальных равных параметрах находятся в соответствии
σcr.b.al =1/3 σcr.b.st
Общая устойчивость балок обычно обеспечивается конструктивными мероприятиями, например постановкой связей в уровне сжатого пояса. Поскольку критическое напряжение потерн устойчивости изгибаемого стержня из алюминия значительно меньше, чем из стали, расстояния между точками раскрепления алюминиевых балок связями должны быть существенно меньшими, чем при раскреплении стальных балок.
При расчете изгибаемых элементов на деформативность наибольший относительный прогиб от нормативных нагрузок не должен превышать предельного, установленного нормами,
f/l = A/EJ<=[f/l]
где A—параметр, зависящий от расчетной схемы балки, размеров пролета и нагрузок.
Предельные прогибы отражают эксплуатационные требования к конструктивным элементам различных видов.
Внецентренно - растянутые и внецентренно - сжатые элементы. Прочность алюминиевых стержней, работающих на одновременное действие осевой силы и изгибающего момента, проверяется по упругой стадии работы материала. Для алюминиевых конструкций часто решающее— расчет на устойчивость в плоскости действия момента N<=φeARyc. Коэффициент φе для сплошностенчатых стержней определяется в функции условной гибкости λ = λ и приведенного эксцентриситета mеf/ηm.
Зависимости
Km.с= mal/mst= pal/*Rst*φe,st Rst/ φe,al Ral ,
выражающие отношение погонных масс внецентренно-сжатых стержней, обладающих равной несущей способностью при одинаковых расчетной длине, эксцентриситете, форме и высоте сечения, позволяют в первом приближении оценить возможности снижения массы стержня при замене стали марки на алюминий. При этом можно видеть, что при больших гибкостях стержней эффективность применения алюминия возрастает с увеличением приведенного эксцентриситета.
СОЕДИНЕНИЯ АЛЮМИНИЕВЫХ КОНСТРУКЦИЙ
В конструкциях из алюминия применяют сварные, заклепочные, болтовые, паяные, клеевые, а также комбинированные (клеесварные, клееболтовые и т. п.) соединения. Выбор вида соединения зависит как от типа конструкции, так и от марки и состояния сплава. Применение соединений, в которых часть усилий воспринимается сварными швами, а часть заклепками или болтами, не допускается.
СВАРНЫЕ СОЕДИНЕНИЯ
Способы сварки. Алюминиевые конструкции можно сваривать практически всеми известными способами сварки: газовой, электродуговой, электроконтактной и др. Тепловое воздействие при сварке приводит к изменению механических свойств алюминия в околошовной зоне, нередко более значительному, чем при сварке стали. В полуфабрикатах, упрочненных холодной деформацией (нагартованных или полунагартованных), прочность при сварке снижается в результате отжига.
Прочность сварных соединений конструкций из термически упрочненных сплавов находится в зависимости от состава легирующих компонентов и состояния сплава (естественное или искусственное старение).
Значительное влияние на качество металла шва оказывают оксиды алюминия. Следует заметить, что сварка возможна лишь при условии чистоты свариваемых поверхностей. Изделия должны быть тщательно очищены от грязи, жира и непосредственно перед сваркой от оксидной пленки, поскольку образование ее происходит очень быстро.
В процессе сварки под действием высоких температур окисление происходит особенно интенсивно, поэтому очень важно обеспечить защиту металла от кислорода воздуха. Наибольшее распространение получил способ электродуговой сварки в среде защитного газа. Этот способ обеспечивает более высокое качество сварных соединений. Защитным газом служит аргон (аргонно-дуговая сварка).
Аргонно-дуговая сварка может осуществляться с помощью неплавящегося (обычно вольфрамового) электрода или плавящимся голым (без обмазки) электродом.
При первом способе сварку можно выполнять с присадкой или без нее (соединяется расплавленным металлом изделия). Присадочный материал обычно вводится в процессе сварки расплавлением проволоки подобно тому, как это делается при газовой (кислородно-ацетиленовой) сварке. Сварку с помощью неплавящегося электрода применяют при соединении изделий малой толщины (до 6—10 мм).
Для сварки изделий средней и большой толщины более удобным и дающим лучшие результаты оказывается способ сварки плавящимся электродом. Автоматическая сварка в среде защитного газа может выполняться на скоростях, в 1,5 раза превышающих скорость автоматической сварки по слою флюса. При сварке элементов малой толщины (1—2 мм) внахлестку применяют контактную электросварку (точечную пли роликовую). Роликовая сварка в заводских условиях обеспечивает получение прочных и водонепроницаемых соединений.
Газовая сварка, электродуговая сварка электродами с обмазкой, а также сварка под слоем флюса (широко применяемая при сварке стальных конструкций) редко применяются при изготовлении алюминиевых конструкций, как не имеющие преимуществ перед аргонно-дуговой и контактной.
Расчет сварных соединений. Расчет соединений стыковыми швами производится по формулам расчета для целого сечения. При этом значения расчетных сопротивлений стыковых швов, работающих на растяжение, качество которых не контролируется физическими методами, принимаются пониженными на 20 %.
Стыковые соединения, работающие одновременно на изгиб и срез, следует проверять по формуле
σw/2 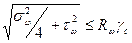
В соединениях угловыми швами расчет производится по тем же формулам, что и соединении конструкций из стали на срез (условный), но только по одному сечению — по металлу шва
τ wmax <= Rwf
В качестве расчетных характеристик принимаются: lw — расчетная длина шва, равная его полной длине за вычетом 3t (при сварке встык) или 3kf (при сварке угловыми швами); при выводе стыкового шва за пределы соединения (на подкладки и т. п.) — принимается полная длина шва;
t — наименьшая толщина соединяемых элементов; kf — катет углового шва, равный катету вписанного равнобедренного треугольника; βf — коэффициент при автоматической одно- и двухпроходной сварке, равный 0,9, во всех других случаях — 0,7.
ЗАКЛЕПОЧНЫЕ И БОЛТОВЫЕ СОЕДИНЕНИЯ
Соединения на болтах или заклепках хотя и связаны с некоторым ослаблением сечения элементов конструкций, тем не менее они имеют некоторые преимущества перед сварными соединениями, так как не вызывают структурных изменении материала.
Заклепочные соединения. Чтобы исключить вредное влияние местного нагрева при клепке, заклепки из алюминиевых сплавов ставят в холодном состоянии. Материалом для заклепок служат сплавы повышенной пластичности.
Перед постановкой в конструкцию заклепки из термоупрочняемых сплавов подвергают закаливанию при температуре около 500 °С. Наибольшее время с момента термической обработки заклепки до клепки определяется скоростью процесса старения материала. Для дуралюмина это время невелико. Например, для сплава Д16п оно составляет всего 20 мин. Срок между термообработкой и постановкой заклепок может быть увеличен хранением заклепок в холодильнике. Так, тот же сплав Д16п, находящийся при t = 0°С, сохраняет свежезакаленное состояние 20 ч. Поскольку упрочнение материала протекает в заклепках, поставленных в конструкцию, возможность загружения конструкции определяется временем, необходимым для достижения материалом заклепок требуемой прочности (обычно 5—10 дней). При применении заклепок из алюминия типа магналии, не подвергающихся упрочнению термообработкой, эти трудности отпадают. Работа заклепки, поставленной в холодном состоянии, отличается от работы заклепки, поставленной после нагрева до соответствующей температуры. Как известно, стержень заклепки, поставленной в горячем состоянии, при остывании, сокращаясь в длине, стягивает соединяемые элементы, что и определяет работу заклепочного соединения в первой стадии вследствие сил трения. При холодной клепке такого стягивания листов не происходит и соединение сразу работает в стадии упругопластических деформаций — смятия и среза. Такая работа заклепок, установленных в холодном состоянии, аналогична второй стадии работы соединения на заклепках, поставленных в горячем состоянии. Чтобы заклепка, поставленная в холодном состоянии, хорошо работала, необходимо полное заполнение отверстия се стержнем. Заклепки ставят в отверстия, рассверленные в пакете. В продавленные отверстия заклепки ставить не допускается. При клепке соединяемые элементы должны быть хорошо прижаты друг к другу, что обеспечивается более частой постановкой сборочных болтов. После снятия этих болтов в заклепочных стержнях возникают растягивающие напряжения; они, однако, значительно меньше растягивающих напряжений, возникающих при остывании заклепки, поставленной в горячем состоянии. Вследствие этого усилие, передаваемое за заклепочную головку, оказывается сравнительно небольшим, и, следовательно, размеры головки могут быть приняты меньшими по сравнению с применяемыми в стальных заклепках. В то же время образование замыкающей головки заклепок больших диаметров (16—20 мм) при холодном способе клепки даже из мягкого (неупрочненного) алюминия требует больших усилий. Стремление уменьшить это усилие привело к изысканию новых форм замыкающих головок.
Сжимающее усилие, необходимое для образования замыкающей головки заклепки диаметром 20 мм из дуралюмина марки Д18, при обычной полукруглой форме — 690, при плоскоконической — 430, при конусообразной — 350 кН. При постановке заклепок того же диаметра из сплава Д1 усилия, необходимые для формирования головок, по сравнению с приведенными, возрастают в 1,3—1,4 раза.
Клепка конструкций в заводских условиях осуществляется на скобах большой мощности. В монтажных условиях, когда клепка ведется пневматическими молотками, форма замыкающей головки имеет особое значение.
Болтовые соединения. В монтажных соединениях алюминиевых конструкций используют как алюминиевые, так и стальные болты. Алюминиевые болты, так же как и стальные, изготовляют нормальной и повышенной точности. Во избежание электрохимической коррозии стальные болты и шайбы оцинковывают или кадмируют. Кроме обычных болтов достаточно широко используются самонарезающие болты и винты, а также болты с обжимными кольцами, служащие для крепления тонколистовых элементов на монтаже. Самонарезающие болты изготовляют из калиброванной стали марки 30 с фосфатированным покрытием. Эти болты выпускают с диаметром резьбы М6, длиной 20 и 25 мм и шестигранной головкой. Воронежский ЗСАК изготовляет стальные самонарезающие винты, которые имеют потайную и полукруглую форму головки с крестообразной формой шлица, диаметр резьбы 4, 5 и 6 мм, длина 15, 25, 30 и 40 мм.
Болты с обжимными кольцами, так называемые локболты, установка которых в соединениях производится специальным пневматическим инструментом, повышают производительность труда на монтаже в 1,5—2 раза.
Расчет заклепочных и болтовых соединений. Заклепки и болты в конструкциях из алюминиевых сплавов рассчитывают по тем же формулам, что и в стальных конструкциях. Расчетные сопротивления срезу в заклепочных соединениях Rrs из алюминия марок АД1Н, АМг2Н соответственно равны 35 и 70 МПа, а из алюминия марок АМг5пМ и АВТ — 100 МПа. Для заклепок с потайными или полупотайными головками расчетные сопротивления снижаются на 20 %.
Диаметр односрезных заклепок обычно назначается несколько большим удвоенной толщины склепываемого пакета: d=2∑t+ (1 ...3), а при двухсрезных d = ∑t+(1...3). Диаметр отверстий под заклепки должен быть немного больше заклепок. Так, при стандартном диаметре заклепок 3—8, 10, 12, 14, 16, 18 мм диаметр отверстий должен соответственно составлять 3,1; 4,1; 5,1; 6,2; 7,2; 8,2; 10,2: 12,35; 14,4; 16,55 и 18,6 мм.
В алюминиевых конструкциях максимальные расстояния между центрами заклепок и болтов несколько уменьшены по сравнению с расстояниями в стальных конструкциях, а минимальные расстояния от центра заклепки (болта) до края элемента увеличены.
Коэффициенты трения щ при расчете соединений на высокопрочных болтах вне зависимости от марки алюминия принимаются: при пескоструйной очистке — 0,45; при химической обработке (травление) — 0,4. При отсутствии обработки соединяемых поверхностей коэффициент трения столь незначителен (|и=0,15), что использование высокопрочных болтов оказывается нецелесообразным. Чтобы увеличить прочность заклепочных и болтовых соединений, соединяемые поверхности целесообразно намазывать клеем (см. п.Ч 1.3.2). В соединениях на высокопрочных болтах, вследствие того что материал конструкции (алюминий) и болтов (сталь) имеет разные коэффициенты линейного расширения, при изменении температуры в стержне болта могут возникать дополнительные температурные напряжения. Их необходимо учитывать при назначении предварительного натяжения болта.
ПРОЧИЕ ВИДЫ СОЕДИНЕНИЙ
Паяные соединения тонкостенных элементов конструкций имеют определенные преимущества по сравнению со сварными: при пайке расходуется меньше тепла, этот процесс не вызывает существенных изменений химического состава и механических свойств основного металла, остаточные деформации в паяных соединениях значительно меньше, чем в сварных. Однако при пайке необходимо особенно тщательно удалять оклееную пленку с поверхности соединяемых изделий. В связи с этим пайка имеет весьма ограниченное применение в строительных конструкциях из алюминия.
Клеевые и клееметаллические соединения. Клеевые соединения имеют определенные преимущества по сравнению с клепаными и сварными соединениями: основной металл не нагревается и не ослабляется отверстиями, благодаря склеиванию большой площади поверхности отсутствуют места концентрации напряжений. Все алюминиевые сплавы, в том числе высокопрочные, можно склеивать. Используя клеи, можно осуществлять соединения алюминия с другими материалами (деревом, сталью, бетоном и т. п.); клеевой слой одновременно предохраняет от вредного контакта с ними.
Недостатком клеевых соединений являются их малая сопротивляемость отрыву, особенно при сосредоточенном действии силы), отсутствие надежных методов контроля за качеством склеивания, а также снижение прочности во времени.
Чтобы повысить надежность клеевых соединений, применяют комбинированные соединения: клеесварные, клеезаклепочные, клеевинтовые или клееболтовые. Наиболее прогрессивные клеесварные соединения алюминия с применением контактной точечной сварки, что позволяет механизировать процесс изготовления конструкций. Для клеезаклепочных и клеевинтовых соединений не нужно сложное оборудование, их можно применять в разнообразных конструктивных решениях (в том числе в соединениях с неметаллическими материалами).
Для склеивания алюминиевых конструкции применяют клен на основе эпоксидных смол, полиуретановые, каучуковые и некоторые другие.
ОСОБЕННОСТИ ПРОЕКТИРОВАНИЯ АЛЮМИНИЕВЫХ КОНСТРУКЦИЙ
Использование алюминия в строительстве вследствие высокой стоимости и дефицитности материала в каждом отдельном случае должно быть соответствующим образом обосновано.
При проектировании конструкций из алюминия не следует копировать решения, характерные для конструкций из стали.
На конструктивные формы алюминиевых конструкций большое влияние оказывают модуль упругости, коэффициент температурной продольной деформации, коррозионная стойкость материала. Большое значение имеет и возможность использования в конструкциях прессованных профилем со сложной формой поперечного сечения.
Не нашли, что искали? Воспользуйтесь поиском по сайту:
©2015 - 2025 stydopedia.ru Все материалы защищены законодательством РФ.
|