Расчет шпиндельных узлов на виброустойчивость. Особенности проектирования высокоскоростных шпиндельных узлов.
Расчет на виброустойчивость, который предусматривает определение собственной частоты шпинделя с целью избежания резонансных колебаний,
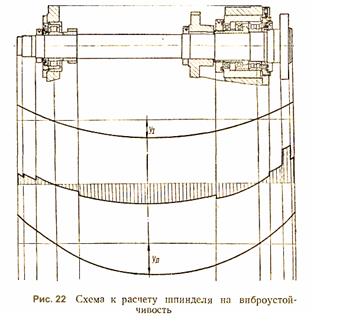
рекомендуется производить для быстроходных шпинделей.
Собственную частоту колебаний можно определять любым из методов, рассматриваемых в курсах теоретической механики. При отсутствии значительных масс, расположенных на консоли, целесообразно применять графический способ (рис. 22 — для шпинделя токарно-револьверного станка).
Последовательность расчета при этом сводится к следующему. Строят упругую линию оси шпинделя под действием собственного веса. Затем задаются произвольной угловой скоростью вращения шпинделя ω0 и строят новую упругую линию под действием центробежных сил, возникающих в каждом сечении шпинделя:
Ax = Fxρ ω02yx, (1.6)
где Fx — площадь сечения шпинделя;
ρ— плотность материала;
ух—прогиб в данном сечении;
Этот способ основан на том, что построенные упругие линии с достаточной точностью геометрически подобны, т. е. уІ = const уІІ (см. фиг. V, 53), и критическая угловая скорость определяется при этом выражением
. (2.6)
Для устранения опасности резонанса обычно ставят условие
(3.6)
где ω— наибольшая угловая скорость вращения шпинделя.
В последнее время на современных металлорежущих станках резко увеличилась скорость резания, а с ней и частота вращения шпинделей.
Частота вращений шпинделей на фрезерно – сверлильно - расточных станках достигает до 1000 об/ мин, частота шпинделей во внутришлифовальных станках достигает до 150000 об / мин и более.
В станкостроении наиболее распространены опоры в виде подшипников качения. В настоящее время около 95% роторов машин и приборов вращаются в подшипниках качения. Если шпиндель станка сконструирован достаточно жестким, то с увеличением частоты вращения шпинделя реакции между шпинделем и подшипниками качения резко возрастают. Сила трения, возникающая между шариками и дорожками качения подшипника, повышается пропорционально нормальному давлению, в результате подшипники качения нагреваются и преждевременно выходят из строя.
Частота вращения шпинделя ограничивается, прежде всего, динамикой системой шпиндель – подшипники – станина станка. Если раньше шпиндели вращались, как правило, с частотой меньшей первой критической скорости, то в современных станках применяются все чаще закритические шпиндели, вращающиеся с частотой большей первой критической скорости, а иногда и больше второй и третей.
Здесь надо понимать, под критическими скоростями, явление резонанса собственной частоты колебаний и вынужденной частоты.
В зоне критических скоростей возникают повышенные давления на опоры шпинделя.
При использовании жестких шпинделей, вращающиеся в подшипниках качения, установленных массивном корпусе шпиндельной бабки, реакция между шпинделем и подшипником возрастает согласно выражению
(4.6)
где N – реакция, приходящаяся на каждую опору двухопорного симметричного шпинделя; m- масса шпинделя; ω – угловая скорость шпинделя; а0- коэффициент определяемый из формулы Герца – P =a0δ⅔, дающий зависимость реакции Р от деформации δ при точечном контакте шарика с дорожкой качения, при этом а0 = 104 кГс/ см3/2.
Из этого выражения видно, что с увеличением угловой скорости шпинделей резко возрастают динамические давления на опоры.
С увеличением частоты вращения шпинделя с 10000 об/мин до 100000 об/мин, нагрузки на опору возрастают в 108 – 1010 степени раз. Очевидно, подшипники такой нагрузки не выдержат и сломаются. При больших частотах вращения шпиндель изгибается в процессе эксплуатации. Его ось вращения смещается от оси шпинделя. Это приводит к увеличению амплитуды колебаний, ухудшению качества обработки и повышению реакции между шпинделем и опорами.
Для высокоскоростных шпинделей выполняется очень точная динамическая балансировка и требуется подбор подшипников высокой точности с биением, измеряемым в долях микронов. Но при высоких скоростях выше второй критической и это не дает положительного результата.
В СССР и за рубежом много посвящено много работ изучению поведения шпинделя в критических зонах при прохождении этих зон на рабочую частоту. Было предложено дать возможность занять положение динамической оси шпинделя, к которой она стремится и этим уменьшить нагрузку на опоры. Для этого опоры шпинделя поставили в упругие опоры расчетной жесткости. Расчетами и экспериментами подтверждено, что жесткий шпиндель, вращающийся в упругих опорах, после перехода через две критические скорости самоцентрируются, т.е. автоматически выбираются статическая и моментная неуравновешенности, а главное центральная ось инерции шпинделя совмещается с осью вращения, при этом давление на опоры снижается до допустимых значений.
При применении подшипников жидкостной или газовой смазкой, могут возникнуть автоколебания, вызванные особыми свойствами масленой пленки или газовой смазки.
При изгибе шпинделя на больших частотах вращения может возникнуть вибрация, вызванная внутренним трением в материале шпинделя. Применение упругих опор позволяет устранить или уменьшить эти опасные явления. Упругие опоры по конструкции представляют собой замкнутые рессорные упругие кольца, материал и конструкция которых определяют необходимую расчетную жесткость.
Пример одной из конструкций упругих опор
Рис. 23
Высокоскоростные шпиндели для фрезерных работ работают с частотой до 10000 об/мин. В настоящее время широко используют встроенные мотор – шпиндели с диапазоном регулирования ДСТ≥ 10000. Для устранения нагрева шпинделя применяют активное водяное охлаждение и проходное воздушное, с локальным подводом к опорам смазки туманом.
В качестве привода для внутришлифовальных шпинделей применяют ременный привод, встроенный электропривод – мотор - шпиндель и воздушные турбины.
Ременный привод применяют до n < 30000 об/мин. Встроенный электропривод применяют с n=12000 об/мин до 15000 об/мин. Дальнейшему повышению n препятствует недостаточная прочность шихтованного ротора, который начинает течь.
Применение в качестве привода воздушной турбины сопорами на газовой смазке позволяет получать более высокие частоты шпинделя до 300000 об/мин.
Итак:
Известно, что повышение точности обработки и производительности станочного оборудования достигается, в том числе, и за счет увеличения скорости резания.
При проектировании высокоскоростных шпинделей необходимо
1. Применять высокоточную динамическую балансировку
2. Использовать в опорах подшипники с минимальным радиальным биением
3. Использовать конструкции опор в зависимости от скоростной характеристики dшп• nmax .
4. Использовать упругие опоры расчетной жесткости
5. Добиваться высокой точности формы опорных поверхностей шпинделя и их взаимного расположения
Применение упругих опор расчетной жесткости позволяет повысить ресурс подшипников шпиндельных опор, снизить вибрацию, увеличить частоту вращения на рабочих режимах, уменьшить мощности холостого хода, снизить давление между шпинделем и подшипниками. При снижении давления между шпинделем и подшипниками увеличивается толщина масленого слоя, а следовательно высокочастотная вибрация подшипников, вызываемая дефектами их изготовления исчезает. Это приводит к увеличению качества обрабатываемой поверхности и ресурса подшипников.
В шпинделях станка могут возникать продольные, поперечные, осевые и крутильные колебания. По виду их подразделяют на собственные, вынужденные и автоколебания. Так как шпиндель имеет сложную конструкцию и в процессе работы станка на него действует большое количество различных факторов как систематического, так и случайного характера, в том числе от смежных технологических систем, то расчет колебаний представляет определенную трудность.
Основная характеристика шпинделя для оценки его виброустойчивости— частота собственных колебаний fc. Обычно чем ниже частота колебаний, тем меньше виброустойчивость, так как для возбуждения колебаний на низкой частоте нужна меньшая энергия. Расчетная схема для определения fc приведена на рис. 24, а формула имеет вид (5.6):
(5.6)
где Wi — силы тяжести элементов, на которые разбита колеблющая система, Н; yi — прогибы под действием силы тяжести всей системы в точке приложения силы, включая деформации опор, м; g —ускорение свободного падения, м/с2.
Расчет шпинделя на виброустойчивость заключается в сравнении частот собственных колебаний fc с вынужденными колебаниями fв- При применении подшипников качения источником колебания может явиться переменная жесткость опор. В этом случае частота будет равна числу шариков или роликов, проходящих в 1 с в направлении действующей силы:
(6.6)
где п — частота вращения шпинделя, об/с; D — диаметр беговой дорожки внутреннего кольца, м; d — диаметр тела качения, м; z— число тел качения. Если источником вынужденных колебаний является дисбаланс шпинделя, то частота fв равна частоте вращения шпинделя (fв = n). Во избежание резонанса необходимо, чтобы fc и fв различались в 1,3...2,0 раза.
Точность вращения, жесткость и виброустойчивость шпинделей во многом зависят от типа опор. В качестве опор применяют прецизионные подшипники качения и подшипники скольжения с жидкостным трением, к которым предъявляют следующие требования:
1. Высокая точность вращения. Биение шпинделя станков нормальной точности находится в пределах 0,01...0,03 мм, а для прецизионных станков достигает нескольких микрометров. Эту точность могут обеспечить подшипники качения и скольжения. Однако в последнем случае при изменении нагрузки или скорости ось вращения шпинделя будет смещаться, так как изменяется толщина масляной пленки.
2. Опоры шпинделей должны быть долговечны. Подшипники качения имеют ограниченный срок службы, зависящий от частоты вращения шпинделя и нагрузки. Подшипники скольжения изнашиваются, в основном, в период пуска, остановки или реверса шпинделя станка. Поэтому при редких включениях они могут работать длительное время.
3. Виброустойчивость опор — важное условие для работы высокооборотных шпинделей. Современные прецизионные подшипники качения отвечают требованиям виброустойчивости. Подшипники скольжения обладают способностью гасить колебания за счет демпфирующего действия масляного слоя.
Для универсальных станков необходимо, чтобы подшипники работали одинаково надежно во всем диапазоне применяемых скоростей и нагрузок. В этом отношении существенное преимущество имеют подшипники качения,
Эксплуатационными преимуществами (легкость замены, простота эксплуатации и др.) обладают подшипники качения, вследствие чего они получили наибольшее применение в современных станках. В тех случаях, когда режим работы постоянный и требуется высокая виброустойчивость, применяют подшипники скольжения.
Итак, чтобы избежать явление резонанса, необходимо, чтобы частота собственных колебаний шпинделя fШ. и частота возмущающей силы fВ отличались на ± (25 + 30)% . Однако точность определения fВ невелика, и поэтому для надежности расчета желательно, чтобы частоты fШ и fВ отличались в несколько раз, а частота собственных колебаний шпинделя была выше частоты вынужденных колебаний. Тогда при пусках и остановках станка нет прохождения через зону резонанса и, кроме того, амплитуда колебаний меньше. Но в высокоскоростных шпинделях это не всегда возможно, и шпиндель может работать с числом оборотов выше критического значения, то есть выше числа оборотов, соответствующего резонансу.
Такая картина может наблюдаться при работе внутришлифовальных шпинделей, число оборотов которых достигает 200000 б/мин. В этом случае наступает динамическое центрирование шпинделя и работа в зарезонансной зоне протекает спокойно
Для удаления от зоны резонанса выгоднее делать быстроходный шпиндель более податливым. Однако, так как при пуске и останове шпинделя имеется проход через критические числа оборотов, необходима тщательная балансировка шпиндельного узла.
Крутильные колебания шпинделей для работы шпиндельной группы обычно имеют меньшие значения. Однако для станков с прерывистым резанием (фрезерные, зуборезные и другие), крутильные колебания шпинделя и всего привода могут вызвать неравномерность вращения шпинделя и дополнительные динамические нагрузки
Не нашли, что искали? Воспользуйтесь поиском по сайту:
©2015 - 2024 stydopedia.ru Все материалы защищены законодательством РФ.
|