Литиевые аккумуляторы с полимерным электролитом.
Литий-полимерные (Li-pol) аккумуляторы отличаются от литий-ионных видом используемого полимерного электролита (ПЭ), являющегося одновременно пористым сепаратором и обладающего ионной проводимостью. Все полимерные электролиты делят на 3 типа: сухие, гель-полимерные, содержащие пластификаторы (пропиленкарбонат, этиленкарбонат, диметилкарбонат и др.) и микропористые (например, на основе сополимера винилиденфторида с гексафторпропиленом, в порах которого находится неводный раствор соли). В таблице 1 приведены характеристики аккумуляторов с ПЭ.
Недостатками сухого и микропористого электролита являются их плохая проводимость и высокое внутреннее сопротивление. Однако они хорошо работают при температурах выше 40°С. Литиевый аккумулятор с гель-полимерным электролитом имеет более высокую проводимость, является гибридным и его называют Li-ионным полимерным аккумулятором.
Таблица 1.
Характеристики Li-аккумуляторов с ПЭ
Тип ПЭ
| Состав и характеристика ПЭ
| Электрическая проводимость, См/м
| Характеристики аккумулятора
| Сухой ПЭ
| полиэтиленоксид + соль лития (LiClO4 LiBF4, LiAsF6)
| 10–5–10–2;
с добавкой при 60°С до 0,1
| металлический литиевый анод; безопасны, низкий саморазряд; высокое омическое сопротивление границы раздела электрод/электролит;
>100 Вт·ч/кг
| Гель-полимерный
| полиакрилонитрил/ поливинилхлорид + соль лития + пластификатор-растворитель
| до 5 при 25°С
| металлический литиевый анод; 155–160 Вт·ч/кг и 175–270 Вт·ч/л; до 500 циклов
| поливинилиденфторид + полиалкилен-гликольдиакрилаты + соль лития
| до 10,5
| углеродистый анод; до 500 циклов с сохранением 70% нормируемой емкости. Токи разряда и заряда от 1C до 25C [25].
| Микропористый ПЭ
| пористая матрица с порами 0,1–1 мкм (поливинилденфторид) + неводный раствор соли лития
| до 0,1
| 100–125 Вт·ч/кг; 200–250 Вт·ч/л; 500–1000 циклов
|
Li-полимерные и Li-ионные полимерные аккумуляторы имеют следующие преимущества: малую толщину (до 1 мм), гибкий форм-фактор, простую конфигурацию корпуса, лучшую безопасность при эксплуатации. Однако Li-ионные полимерные аккумуляторы имеют более низкую энергетическую плотность и меньший ресурс по сравнению с Li-ионными, а также их производство дороже.
Процесс заряда литий-полимерных аккумуляторов подобен заряду литий-ионных.
Утилизация литиевых аккумуляторов
Большие масштабы производства литиевых ХИТ с учетом используемых в них материалов делают приоритетной проблему утилизации литиевых аккумуляторов после выработки их ресурса, а также отбракованных изделий и технологических отходов производства.
Необходимость утилизации литиевых ХИТ обусловлена как экологическими (литий, его соединения, электролит, катодные материалы являются экологически опасными и могут привести к значительному загрязнению окружающей среды), так и экономическими факторами.
Экологические факторы подробно рассмотрены в вопросе утилизации первичных ЛХИТ (лаб. раб. №3, с. 109).
Экономические факторы. В состав литиевых вторичных ХИТ входит большое количество ценных материалов: металлический литий и его соединения, содержащие дорогостоящие компоненты – кобальт, никель, и др., а также органические вещества.
Известно несколько схем утилизации литий-ионных аккумуляторов, которые используют операции вскрытия источников (механическим, электролитическим способами или с применением лазерного пучка), извлечения и нейтрализации электролита, обработки катодного материала с выделением Co, перевод лития в раствор и т. д. [26, 27].
Большой интерес представляет схема процесса утилизации использованных Li-ионных аккумуляторов с положительным электродом на основе кобальтата лития и электролитом LiPF6 в смеси пропиленкарбоната с диэтилкарбонатом (рис. 8).
Отсутствие металлического лития в литий-ионных аккумуляторах позволяет упростить разборку источников тока и процесс дальнейшей переработки отходов.
Из полученного осадка Co(OH)2 в течение 3 ч при 450°С получают Co3O4, который затем смешивают со стехиометрическим количеством Li2CO3, получающимся в процессе утилизации первичных литиевых источников тока. В результате 5-часового прогрева при 400°С, гомогенизации и последующего 20-часового отжига при 700°С получается кобальтат лития необходимого качества для использования в аккумуляторах. Таким образом, сочетая утилизацию первичных литиевых источников тока и литий-ионных аккумуляторов, удалось создать удачную технологию комплексной рекуперации литиевых источников тока. Считается целесообразным утилизацию литиевых ХИТ проводить на предприятиях, где их изготавливают.
Массовое применение литий-ионных аккумуляторов значительно упрощает проблему их сбора после выработки ресурса. Актуальность вопроса сбора и утилизации отработанных ЛХИТ приобретает все большее значение и для Республики Беларусь.
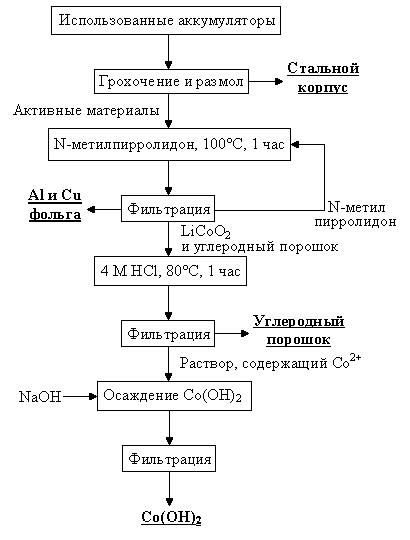
Рис. 8. Технологическая схема процесса переработки использованных
литий-ионных аккумуляторов
Варианты заданий к лабораторной работе
Вариант 1. Определите электрические характеристики (НРЦ, U, Rвнутр) литий-ионного аккумулятора. Определите внутреннее сопротивление аккумулятора путем снятия вольт-амперной кривой. Не разряжайте литий-ионный аккумулятор ниже 3,2 В.
Снимите зарядную характеристику аккумулятора. Вначале заряжайте при постоянном токе 0,7С до напряжения 4,1 В. Затем заряд продолжайте вести при постоянном напряжении, ток при этом снижается до 3% от начального. Первая стадия заряда может длиться около 40 мин, вторая стадия до 2 часов.
Вариант 2. Изучите влияние токовой нагрузки на разрядные кривые литий-ионного аккумулятора. Разряд осуществляйте током 0,2C; 0,5C; 1С в течение 0,5–1 ч. Не разряжайте литий-ионный аккумулятор ниже 3,2 В.
Снимите зарядную характеристику аккумулятора способом, описанным в варианте 1.
Лабораторная работа №8
ТОПЛИВНЫЕ ЭЛЕМЕНТЫ
Топливный элемент (ТЭ) – это химический источник тока, в котором осуществляется прямое превращение химической энергии топлива и окислителя, непрерывно подводимых к электродам, непосредственно в электрическую энергию посредством электрохимических реакций, минуя малоэффективные процессы горения (рис. 1). Поэтому энергетический КПД топливного элемента значительно выше (50–80%), чем у традиционных энергоустановок и может достигаеть 90% [29]. Теоретически ТЭ может работать неограниченно долго.
Особенности ТЭ
Активными веществами топливного элемента являются, как правило, газообразные или жидкие восстановители (топливо) и окислители. Электроды являются катализаторами токообразующих реакций, в реакциях не участвуют и выполняют функцию токоотвода. Разрядное напряжение ТЭ отличаются стабильностью, а электроды малой поляризуемостью.
ТЭ обладают высокой удельной энергией со значительной мощностью при непрерывном разряде от 5000 ч.
Электрохимические системы, применяемые в топливных элементах, отличаются высоким термодинамическим КПД, для некоторых из них он больше 1 (формула 1.11, с. 6). Например, для электрохимических систем гидразин/пероксид водорода и метанол/азотная кислота термодинамический КПД составляет 1,05 и 1,83, соответственно.
Рис. 1. Ступени преобразования химической энергии традиционным и
электрохимическим способом
Фактический КПД (формула 1.12, с. 6) значительно ниже и для лучших образцов ТЭ лежит в пределах 50–70%.
ТЭ являются частью электрохимических генераторов (ЭХГ), в которые входят батарея ТЭ, системы автоматического контроля и регулирования температуры, напряжения. ЭХГ вместе с устройствами для хранения и подвода топлива и окислителя, отвода тепла и продуктов реакции входят в состав энергетической установки (ЭУ). Упрощенная схема ЭУ приведена на рис.2.
Рис. 2. Упрощенная схема ЭУ.
Особое значение ЭХГ и ЭУ приобрели как источники питания для космических и подводных аппаратов. Возможные области применения ТЭ показаны на рис. 3.
Разработаны гибридные ЭУ, в которых электрическая энергия генерируется двумя или более устройствами, например ЭУ и газотурбинной установкой, или ЭУ и батареей электроаккумуляторов.
Теория и конструкция топливных элементов
Выбор топлива и окислителя, подаваемых в ТЭ, определяется, в первую очередь, их электрохимической активностью (то есть скоростью реакции на электродах), стоимостью, возможностью легкого подвода исходных веществ и отвода продуктов реакции.
В таблице 1 приведены теоретические значения ЭДС и напряжения разомкнутой цепи (Uрц) ТЭ, работающих на газообразном, жидком и твердом топливе и кислороде, а также электролит и материалы электродов.
В качестве газообразного топлива используется водород, синтез газ (СО и Н2) и смеси углеводородов. Жидкие виды топлива представлены водными растворами сильных восстановителей: гидразин, аммиак, метанол, этанол и др. Твердым видом топлива является уголь, спрессованная сажа.
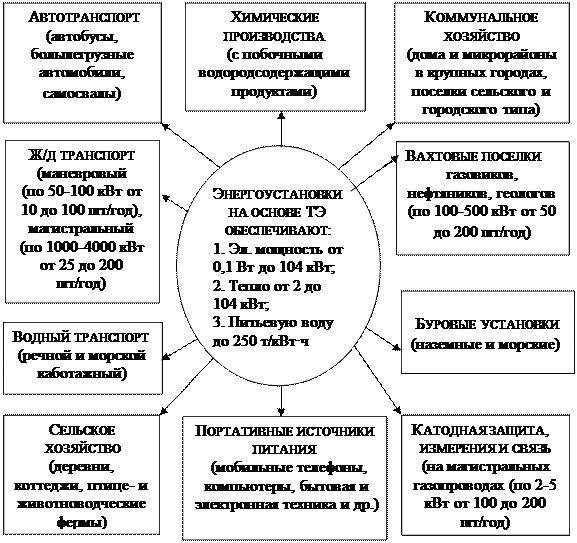
Рис. 3. Области применения топливных элементов.
.
Примеры анодного окисления топлива:
СН3ОН + Н2О → СО2 + 6Н+ + 6e–, (1)
С2Н5ОН + ЗН2О → 2СО2 + 12Н++ 12e–, (2)
N2H4 + 4OH– → N2 + 4H2O + 4e–, (3)
NH3 + 3OH– → 0,5N2 + 3H2O + 3e–, (4)
Водород считается основным источником топлива для ТЭ. Процесс преобразования топлива позволяет извлекать водород и из метанола, природного газа, нефти и др.
Таблица 1
Характеристики электрохимических систем топливных элементов
Топливо
| Суммарная токообразующая реакция
| ∆G, кДж/моль
| ЭДС298КВ
| Материал электрода
| Электролит
| Uрц, В
| анод
| катод
| Водород (г)1
| H2 + Cl2 = 2HCl
| -262,51
| 1,37
| Pt
| Pt
| 5 % HCl
| 1,37
| H2 + 1/2O2 = H2O
| -237,35
| 1,23
| 5 % H2SO4
| 1,15
| Пропан (г)
| C3H8 +5O2= 3CO2 + 4H2O
| -2,106
| 1,085
| 0,65
| Метан (г)
| CH4 + 2O2 = CO2 + 2H2O
| -818,52
| 1,06
| 0,58
| Муравьиная кислота (ж)2
| HCOOH + 1/2O2 = CO2 + H2O
| -285,54
| 1,48
| 1,14
| Аммиак (ж)
| NH3 + 3/4O2 = 3/2H2O + 1/2N2
| -338,29
| 1,17
| 30 % KOH
| 0,62
| Оксид углерода (II) (г)
| CO + 1/2O2 = CO2
| -257,28
| 1,33
| Cu
| Ag
| 1,22
| Метанол (ж)
| CH3OH + 3/2O2 = CO2 + 2H2O
| -698,36
| 1,21
| Pt
| C
| 0,98
| Формальдегид (ж)
| CH2O + O2 = CO2 + H2O
| -522,09
| 1,35
| 1,15
| Натрий (ж)
| Na + 1/2H2O + 1/4O2 = NaOH
| -300,78
| 3,12
| Na (Hg)
| Ag/C
| 2,10
| Гидразин (ж)
| N2H4 + O2 = N2 + 2H2O
| -602,48
| 1,56
| Ni
| C
| 1,28
| Уголь (тв)3
| C + O2 = CO2
| -334,78
| 1,02
| C
| CuO/C
| Na2CO3рас
| 1,034
| | | | | | | | | |
1 газ; 2 жидкость; 3 твердое вещество; 4 измерено при 1023 К.
Известно, что процесс электрохимического окисления водорода состоит из нескольких стадий:
1) растворение газообразного водорода в электролите;
2) диффузия растворенного водорода к поверхности электрода;
3) адсорбция водорода на поверхности электрода;
4) диссоциация молекулы водорода на атомы, их частичное растворение в материале электрода с образованием твердого раствора внедрения и диффузия атомов к активному центру электрокатализатора:
Н2 = 2 Надс; (5)
5) электрохимические стадии переноса заряда, ионизация:
Надс + Н2О = Н3О+ + е–. (6)
Надс + ОН– = Н2О + е–. (7)
6) десорбция продуктов электрохимической реакции.
Следует отметить, что стадии диссоциации (5) и переноса заряда (6, 7) для ряда материалов заменяются стадией электрохимической десорбции, которая в кислой среде выражается следующим образом:
Н2 + Н2О = Н3О+ + Надс + е–. (8)
Материал электродов, на которых осуществляется процесс окисления, должен быть устойчив в реакционной среде, обладать высокой электропроводностью, обеспечивать высокую скорость химических и электрохимических реакций и быть устойчивым к каталитическим ядам (СО2, СО, соединения мышьяка и серы). Высокая электрохимическая активность электродов достигается введением в них катализаторов, в качестве которых используются металлы платиновой группы (Pt, Pd, Ir), Ag, специально обработанные Ni, Co, активированный уголь, WC, [2, 3, 29].
Наиболее распространены катализаторы на основе платины и ее сплавов. Известно [1], что на платине окисление водорода происходит со скоростью в 100–1000 раз большей, чем на других металлах и сплавах. Механизм окисления водорода на платине в кислых электролитах включает скоростьопределяющую стадию адсорбции молекулярного водорода:
Н2 + 2 Pt = 2 Pt-Hадс, (9)
и, последующий быстрый, перенос электрона:
2 Pt-Hадс = 2 Pt + 2H+ + 2e–. (10)
Даже незначительная примесь СО и СО2 приводит к блокировке большинства активных центров, делая поверхность катализатора недоступной для адсорбции водорода. Отравление платины приводит к резкому падению напряжения топливного элемента. Эффективным путем повышения устойчивости катализатора к отравляющему действию СО и СО2 является замена чистой платины на Pt-Ru сплав [29].
В качестве катодного вещества-окислителя ТЭ используется воздух, кислород, раствор пероксида водорода или азотной кислоты. Наиболее распространены ТЭ с газодиффузионным воздушным катодом, на поверхности которого восстанавливается кислород. Суммарные уравнения полуреакций для кислой и щелочных сред записываются следующим образом:
О2 + 4Н+ + 4е– = 2Н2О, (11)
О2 + 2Н2О + 4е– = 4ОН–. (12)
Однако механизм восстановления кислорода включает протекание большого числа последовательных и параллельных стадий с образованием мало устойчивых промежуточных продуктов, например, оксидов металла-катализатора, пероксида водорода. Традиционно катализатором в этих процессах является платина и ее сплавы с золотом и иридием. Кроме того, для реакции катодного восстановления кислорода перспективны катализаторы на основе сплавов палладия.
Увеличение каталитической активности платины в реакции восстановления кислорода может быть достигнуто путем ее легирования никелем, кобальтом, хромом, железом, медью, ванадием, вольфрамом и др. Примером такого легирования являются синтезированные на саже наноразмерные системы Pt-Co и Pt-Fe с электрокаталитической активностью, сопоставимой с Pt-катализатором и приемлемой коррозионной стойкостью [29, 30]. Позитивное влияние легирующего компонента обусловлено следующими эффектами кристаллической решетки получаемого сплава:
· уменьшение межатомного расстояния Pt-Pt, способствующее диссоциативной адсорбции молекул кислорода;
· увеличение доли вакантных d-орбиталей металла-катализатора и понижение их энергии взаимодействия с кислородом;
· уменьшение среднего размера частиц катализатора и увеличение площади поверхности катализатора под влиянием легирующего компонента;
· увеличение доли благоприятно ориентированных граней кристалла;
· выщелачивание второго металла в процессе работы, вследствие чего происходит развитие поверхности катализатора и формирование новых активных центров;
· уменьшение агломерации наночастиц в процессе функционирования ТЭ вследствие усиления их адгезии к основе;
· изменение состава поверхностных оксидов путем включения в поверхностный слой оксидов металлов-каталиаторов [30].
В последние годы в ТЭ начинают использовать электродные носители из углеродных наноразмерных материалов (УНМ), которые представлены углеродными нанотрубками, наноониксами, нановолокнами с характерным размером от 4 нм до десятков микрометров [30].

Рис. 4. Электронно-микроскопические фотографии платиноуглеродного наноструктурного катализатора ТЭ[29].
Каталитический слой, состоящий из наночастиц углерода (рис. 4), покрытого металлом-катализатором, обладает пористостью и проницаемостью достаточной для обеспечения доступа реагентов или отвода продуктов. Углерод обладает высокой электропроводностью, а также достаточной коррозионной стойкостью в условиях эксплуатации ТЭ. Кроме того, частицы металлов, склонные к агрегатированию, закрепляются на поверхности наноразмерного носителя, образуя наструктурированный катализатор (рис. 4). Удельная площадь поверхности наночастиц углерода в каталитическом слое может достигать 60–90 м2/г. Однако распространение таких материалов сдерживается существующими дорогостоящими технологиями синтеза УНМ, которые реализуются в условиях высокого вакуума, дугового разряда, лазерного нагрева и, как правило, требуют использования специального оборудования. Кроме того, получаемые неоднородные УНМ, чаще всего, нуждаются в дополнительной активации, направленной на создание дефектов структуры, удаление аморфного углерода и разрушение крупных агломератов УНМ, внедрение каталитически активных групп и гетероатомов. Поэтому в настоящее время интенсивно развиваются новые мало затратные методы получения УНМ, одним из которых является гальваноплазменный синтез УНМ. Преимуществом этого метода является то, что он реализуется при атмосферном давлении путем электродугового испарения графитовых электродов, погруженных в жидкость с использованием типового электротехнического оборудования. Полученные таким образом УНМ, по данным сканирующей электронной микроскопии, представлены вытянутыми сфероидными структурами с размером меньше 200 нм [31, 32].
Тем не менее, УНМ являются наиболее приемлемой основой пористых электродов ТЭ, основное отличие которых выражается в поляризационной характеристике [29]. На рис. 5 видно, что пористый электрод при малых токах i работает по всему объему – внутрикинетический режим. В этой области токов (отрезок АВ на кривой 2) расстояние между кривыми постоянно и равно логарифму фактора шероховатости поверхности электрода (lg σs). По мере увеличения тока из-за возрастающего влияния омических факторов кривые сближаются (участок BC). При дальнейшем увеличении тока процесс вытесняется на внешнюю поверхность и пористый электрод теряет свои преимущества перед гладким, наблюдается внешнекинетический режим (отрезок CD) и внешнедиффузионный режим в слое электролита (отрезок DE) [29].
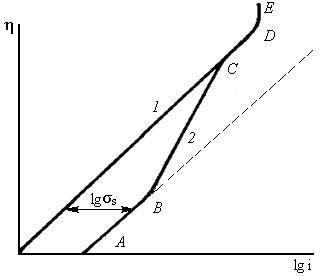
Рис. 5. Тафелевские поляризационные кривые гладкого (1) и пористого (2) электродов; σs – фактор шероховатости.
При разработке электродов ТЭ, работающих на газообразном топливе, необходимо создавать развитую границу раздела фаз газ – электролит – электрод. Эффективность работы таких ТЭ зависит от того, насколько кинетически благоприятны и стабильны условия для протекания каждой из последовательных стадий токогенерующего процесса. Практическое применение в этой области получили газожидкостные и газодиффузионные электроды.
Модель газожидкостного электрода представляет собой гомопористую пластинку, обладающую электронной проводимостью, одна сторона которой граничит с электролитом, другая – с газом. Разряд адсорбированных молекул газа проходит в объеме электрода на границе трех фаз. Стабильность реакционной поверхности и сама возможность электрохимической реакции зависят от соотношения давления газа Ргаз и суммы капиллярного Рк и гидростатического Рг давления электролита. При Ргаз > Рк+Рг газ будет вытеснять электролит из пор и барботировать в раствор, при Ргаз < Рк+Рг электролит заполнит поры, произойдет промокание электрода. В обоих случаях разрядный ток будет минимальным. Трехфазная граница раздела окажется максимальной в том случае, сели для каждой из сквозных пор будет соблюдаться равенство Ргаз = Рк+Рг. Однако реальный газодиффузионный электрод не является гомопористым и, соответственно, капиллярное давление как величина, зависящая от радиуса поры, будет различным в разных точках электрода. В результате одни поры будут заполнены электролитом частично, другие – полностью, через третьи газ будет проходить сквозь электрод. Существуют различные способы стабилизации трехфазной границы раздела на уровне максимально достижимой либо номинальной плотности тока.
Первый способ реализован в конструкции гидрофильного электрода (рис. 6) и заключается в применении двойной пористости. Электрод состоит из двух слоев, имеющих различную структуру: газозапорного слоя, обращенного к электролиту, и активного слоя, обращенного к газовой камере (рис. 6). Запорный слой имеет мелкозернистую структуру и электрохимически неактивен, его задача – быть заполненным электролитом при любом допустимом давлении газа.
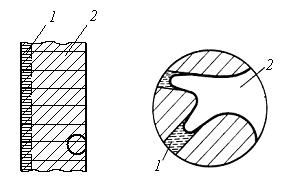
Рис. 6. Схема двухслойного гидрофильного газожидкостного электрода
1 - газозапорный спой, 2 - активиый спой;
1 - жидкостная пора, 2-газовая пора
Активный слой состоит из порошков наполнителя и катализатора. Его структура более крупнопориста и неоднородна, что определяется характером дисперсности наполнителя. В результате при некотором перепаде давления более крупные поры заполняются газом; их называют газовыми в отличие от жидкостных пор, заполненных электролитом. Все жидкостные поры должны быть равномерно распределены в объеме активного слоя и соединены с электролитом вне электрода.
Электрохимическая реакция протекает преимущественно в зоне мениска жидкости в поре. Там электролит образует тонкую кольцевую пленку, сквозь которую растворенный газ быстро диффундирует к электродной поверхности. Максимальная поверхность тонкопленочной части электролита обеспечивается оптимальным соотношением газовых и жидкостных пор активного слоя электрода. При этом избыточное давление обычно не превышает 0,1 МПа.
По другому способу стабильная граница раздела фаз достигается гидрофобизацией активного слоя. Такой электрод готовят из смеси катализатора с гидрофобным веществом, например с фторопластом или полиэтиленом. Соотношение жидкостных и газовых пор зависит от соотношения дисперсности и массы компонентов смеси. Чтобы избежать просачивания электролита на газовую сторону электрода, ее покрывают тонким мелкопористым гидрофобным слоем.
Достоинство газожидкостного гидрофобизированного электрода заключается в его работоспособности при атмосферном давлении. Это позволяет использовать его в качестве положительного электрода воздушно-водородного элемента. Кроме того, активный слой такого электрода может иметь толщину на порядок меньше, чем толщина гидрофильных электродов с газозапорным слоем. Однако наличие гидрофобизатора в структуре электрода снижает его электрическую проводимость, а при длительном разряде из-за постепенного ухудшения гидрофобных свойств газовые поры активного слоя постепенно заполняются электролитом, что уменьшает скорость токообразующей реакции. Чтобы избежать затопление пор, применяют комбинированный трехслойный электрод, состоящий из активного гидрофобизированного слоя и двух тонких запорных слоев: газозапорного со стороны электролита и гидрозапорного со стороны газа. Такой электрод рассчитан на работу при повышенном давлении газа и при длительном разряде сохраняет хорошую работоспособность [2].
Наибольшее распространение в ТЭ получили высокоэффективные тонкие многослойные газодиффузионные электроды гидрофильно-гидрофобного типа (рис. 7). Их каталитически активный мелкопористый слой состоит из активированного угля, к которому добавлены окисные катализаторы (шпинели) для кислородного электрода и малые количества платины (менее 10 г/м2) для водородного электрода. К этому слою примыкают крупнопористые слои из смеси углеродного материала и фторопласта, гидрофобность которых нарастает по мере приближения к тыльной (газовой) поверхности электрода.
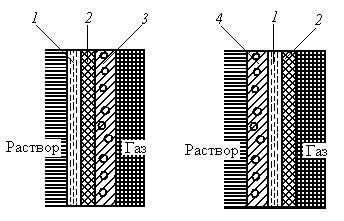
а б
Рис. 7. Схема устройства воздушных (кислородных) электродов. 1 – слой активированного угля; 2 – угольный слой переменной гидрофобности; 3 – никелевая сетка; 4 – гидрофильная пористая никелевая основа.
Механической основой электрода служит армированный сеткой тонкопористый слой из спеченного никелевого порошка. Этот слой выполняет одновременно функции запорного слоя. В первых вариантах запорный слой был гидрофобным (за счет обработки пористого никеля фторопластом) и располагался с газовой стороны (рис. 7, а). В более поздних вариантах использовался гидрофильный запорный слой со стороны электролита (рис. 7, б). Общая толщина электрода – 0,5–2 мм. Благодаря переменной по толщине гидрофобности реакционная зона в таком электроде четко фиксирована [3].
Существует еще один способ стабилизации соотношения жидкостных и газовых пор, который сводится к применению матричного электролита. В этом случае строго ограниченный объем электролита распределяется между пористым сепаратором-матрицей и активным гидрофильным слоем, оставляя часть пор электрода незаполненной.
Составной частью ТЭ, как правило, является мембранно-электродный блок (МЭБ), который представляет собой мембрану, на одну сторону которой нанесен катодный, а на другую - анодный катализаторы. Токосъем с катодной и анодной сторон, подвод исходных реагентов и отвод продуктов реакции производится через пористые газодиффузионные электроды. МЭБ, газодиффузионные электроды и токоподводы могут быть соединены в монополярные и биполярные батареи ТЭ. Пример конструкций ТЭ представлен на рис. 8 [33].
Типы топливных элементов
Существуют различные типы ТЭ. Их обычно классифицируют по используемому топливу, рабочему давлению и температуре, а также по характеру применения.
В зависимости от температуры применяемого электролита топливные элементы делят на высокотемпературные, среднетемпературные и низкотемпературные.
Высокотемпературные элементы работают при температурах 400–1000°C на расплавленных карбонатах или твердых электролитах. Среднетемпературные элементы работают при температурах 180–250°C на водных щелочных электролитах (30–45% KOH) или на концентрированной H3PO4. Низкотемпературные ТЭ работают при температурах ниже 100 °C со щелочными и кислотными электролитами.

Рис. 8. Составные части и внешний вид твердополимерного (а)
и твердооксидного (б) топливного элемента
В низкотемпературных элементах не удается использовать природные виды топлива: нефть, продукты ее переработки, природный газ (метан). Проблема использования этих видов топлива решается по двум направлениям: применением высокотемпературных элементов и
предварительной химической обработкой топлива для получения электрохимически активных веществ.
Наибольшее распространение получила классификация топливных элементов по типу электролита как среды для внутреннего переноса ионов. В таблице 2 приведены технические характеристики ТЭ.
ТЭ со щелочным электролитом ЩТЭ (AFC). Электролит состоит из жидкого KOH, который циркулирует в пространстве между электродами. ЩТЭ использовались с середины 1960-х годов в космических программах, обеспечивая питанием электрические системы космических кораблей "Буран", "Шаттл" и др. КПД достигает 70%. Примером такого ТЭ является щелочной кислородно-водородный ТЭ:
(Ni-сетка, Pt-Pd)Н2 | КОН (30% масс.) | О2(Pt-Au, Ni-сетка).
Рабочее напряжение U = 0,95 В при 100°С, плотность тока i = 0,1–0,3 А/см2, удельная мощность – 500 Вт/л, ресурс работы – 10000 ч.
Наземное применение ЩТЭ ограничено из-за высокой стоимости, т. к. они должны работать с чистым водородом и кислородом (либо с кислородом воздуха, из которого удален углекислый газ).
ТЭ с фосфорнокислым электролитом ФКТЭ (PAFC). Электролитом является бумажная матрица, насыщаемая фосфорной кислотой, также проводящей протоны. Рабочая температура 150–220оС. Это наиболее коммерчески разработанные ТЭ. Они могут применяться в стационарных электрогенераторных устройствах в зданиях, гостиницах, больницах, аэропортах и электростанциях.
ТЭ на фосфорной кислоте вырабатывают электричество с КПД более 40% или около 85%, если пар, который производит этот ТЭ, используется для совместного производства тепла и электричества. Примером такого ТЭ может быть кислородно-водородный элемент:
(Pt, уголь)Н2 | Н3РО4 (98% масс.), | О2(Pt, уголь) .
Рабочее напряжение U = 0,7 В при 200°С, плотность тока i = 0,25 А/см2. Ресурс – 50000 часов.
ТЭ с твердополимерным электролитом ТПТЭ (PEMFC). В качестве электролита используется твердая полимерная мембрана (пленка), которая проводит водородные ионы (протоны) с анода на катод. Они обеспечивают высокую плотность тока, что позволяет уменьшать их вес, стоимость, объем и улучшать качество работы. Неподвижный твердый электролит упрощает герметизацию в процессе производства, уменьшает коррозию, и обеспечивает более долгий срок службы. Такие ТЭ могут работать при низких температурах (ниже 100°С). Основным недостатком ТПТЭ является необходимость подачи увлажненных газов для предотвращения высыхания тведополимерного электролита. В качестве такого электролита используются тведополимерные мембраны из перфторированного сульфокатионитного полимера (Nafion, МФ4-СК) или полибензимитазола, допированного ортофосфорной кислотой [30].
ТПТЭ идеально подходят для транспорта и стационарных установок небольшого размера. Принципиальная схема работы ТЭ представлена на рис. 9.
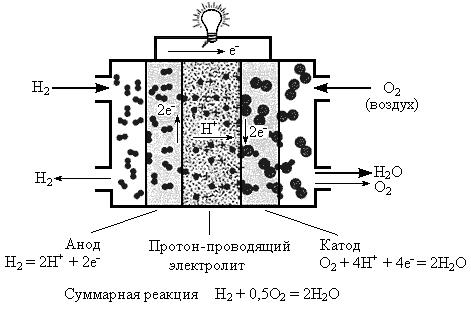
Рис. 9. Схема работы топливного элемента с
твердополимерным электролитом
Разновидностью ТПТЭ является метанольный топливный элемент МЭТ (MFC):
(С, Pt- Ru)CH3OH | Протонпроводящая мембрана | О2(Pt, С).
Состав и структура катодов МТЭ отличается от состава и структуры катодов ТПТЭ более высоким содержанием платины в катализаторе (до 4 мг/см2). Удельное содержание платины – 1 мг/см2 [29].
Стандартная ЭДС при температуре 298 К равна 1,18 В и с увеличением температуры снижается. При температуре 25оС МТЭ способны поддерживать плотность тока 5–10 мА/см2 и мощность 1–4 мВт/см2, которые возрастают с увеличении температуры. При температуре 90оС и концентрации метанола 2 моль/л можно получить в ТЭ плотность тока 200–300 мА/см2. Повышение давления воздуха на 400 кПа увеличивает удельную мощность примерно на порядок [29].
ТЭ с расплавленным карбонатом РКТЭ(MCFC) использует расплавленную смесь лития/калия (или лития/натрия) для проведения ионов карбоната от катода к аноду. Рабочая температура – около 650°C, что позволяет использовать топливо напрямую, без какой-либо дополнительной его подготовки, и никель в качестве катализатора. Конструкция более сложна, чем конструкция ТЭ на фосфорной кислоте, из-за более высокой рабочей температуры и использования расплава электролита.РКТЭ требуется существенное количество времени для достижения рабочей температуры и реагирования на изменения потребности в электричестве. Поэтому лучше всего РКТЭ подходят для условий, где необходима постоянная подача больших количеств электроэнергии.
Распространенным ТЭ с электролитом в виде расплавленной эвтектической смеси карбонатов лития и натрия является следующая система:
(LiNiO2)Н2+СО | Li2CO3 + Na2CO3 (расплав), | воздух(Ni пористый).
Рабочее напряжение U = 0,7 В при 650°С, плотность тока i = 0,16 А/см2, ресурс – 10000 часов
Анодная реакция может быть представлена:
Н2 + СО32- → Н2О + СО2+2е–, (13)
СО+СО32-→ 2СО2+2е–. (14)
Катодная реакция:
О2 + 2СО2 + 4е–→ СО32-. (15)
Суммарная реакция:
Н2 + СО + О2 → Н2О + СО2. (16)
Наибольшее количество подобных установок построено в Японии и США (демонстрационная опытная электростанция мощностью 1,8 МВт).
ТЭ с твердооксидным электролитом ТОТЭ (SOFC). В ТОТЭ в качестве электролита используют стабилизированный оксидами иттрия или скандия оксид циркония с ионной проводимостью по кислороду. При температуре 1273 К удельная проводимость электролита находится в пределах 14–30 См/м.
Достоинствами ТОТЭ являются использование не платиновых катализаторов, меньшая чувствительность к каталитическим ядам, возможное электроокисление СО, относительно низкие электродные поляризации и, соответственно, высокие плотности тока, отсутствии жидких компонентов, миграции электролита, проблем затопления и смачивания электродов, толерантность к перегрузкам и недогрузкамкам. В ТОТЭ наряду с электроэнергией генерируется высокопотенциальная теплота, которую можно использовать в газовой турбине [29].
Наиболее распространен твердооксидный ТЭ с топливом в виде углеводородной смеси, содержащей СО + Н2. Электролитом является оксидная керамика 0,9 ZrO2 + 0,1 Y2O3. Рабочая температура 800 – 1000°С. Ресурс работы – 10000 ч. В качестве катодных материалов используются оксидные полупроводниковые соединения (перовскиты) – манганит или кобальтит лантана, дозированные стронцием La(1-x)SrxMnO3 и La(1-x)SrxCoO3, где х = 0,1–0,25. Материалом анода служит кермет на основе Ni-ZrO2 толщиной 0,1–0,2 мм, имеющий малое электрическое сопротивление, высокую стабильность и температурный коэффициент расширения близкий к температурному коэффициенту расширения твердооксидного электролита и характеризуемый высокой электрохимической активностью к реакциям анодного окисления водорода и диоксида углерода.
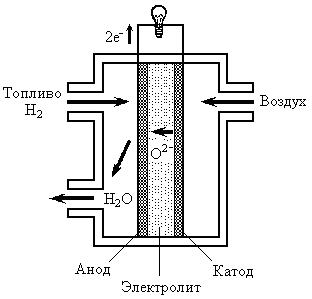
Рис. 10. Схематическое изображение топливного элемента с твердым электролитом
На катодной стороне твердооксидного электролита (рис. 10) происходит восстановление O2 с образованием иона кислорода по реакции:
O2 + 4e–→ 2 O2-. (17)
Не нашли, что искали? Воспользуйтесь поиском по сайту:
©2015 - 2025 stydopedia.ru Все материалы защищены законодательством РФ.
|