Детали машин и основы конструирования
Тема 1. Общие сведения о деталях машин
Основные понятия.Машины состоят из деталей. Детали машин– это составные части машин, каждая из которых изготовлена без применения сборочных операций, например, вал.
Число деталей в сложных машинах может измеряться десятками и сотнями тысяч, например, в автомобиле содержится более 15 тыс. деталей, в автоматизированных комплексах прокатного оборудования – более миллиона.
Совокупности совместно работающих деталей, представляющих собой конструктивно обособленные единицы и обычно объединяемые одним назначением, называются узлами или сборочными единицами. Узлы одной машины можно изготовлять на разных заводах. Характерными примерами узлов являются редукторы, коробки передач, муфты, подшипники в собственных корпусах.
Выполнение машины из деталей, в первую очередь, связано с необходимостью определенных относительных движений ее частей. Как свидетельствует одно из дошедших до нас определений, под термином «машина» понималось «орудие, имеющее внутреннее движение частей».
Неподвижные и взаимно неподвижные скрепленные между собой детали называют звеньями. Выполнение звеньев не из одной, а из нескольких соединенных между собой деталей обеспечивает возможность:
- изготовления деталей из разных материалов, например, вкладышей подшипников из бронзы или другого антифрикционного материала, а корпуса подшипника из чугуна;
- удобной замены быстроизнашивающихся деталей;
- сборки (например, установка коленчатого вала в коренные подшипники двигателя выполнима лишь при съемных крышках) и облегчения сборки машины;
- облегчения изготовления деталей ввиду упрощения их формы и уменьшения размеров;
- большей нормализации, стандартизации и централизованного изготовления деталей.
Различают детали общего и специального назначений.
Детали общего назначения –детали, которые встречаются почти во всех машинах (болты, валы, зубчатые колеса и т.д.). Они составляют подавляющее большинство и изучаются в курсе «Детали машин».
Детали специального назначения– детали, которые встречаются только в специальных типах машин (гребные винты, поршни, коленчатые валы, шпиндели станков, клапаны, шатуны и т.п.); их изучают в специальных курсах («Металлорежущие станки», «Швейное оборудование» и т.п.)
Работоспособность машин.Общие требования к машинам:
- увеличение мощности при тех же габаритных размерах;
- повышение скорости и производительности;
- повышение коэффициента полезного действия;
- автоматизация работы машин;
- использование стандартных деталей и типовых узлов;
- минимальная масса и низкая стоимость изготовления.
Детали машин должны удовлетворять условию работоспособности, т. е. способности, сохраняя свои эксплуатационные показатели, выполнять заданные функции в течение заданного срока службы, и условию экономичности, т. е. иметь минимально необходимую стоимость изготовления и эксплуатации.
Поэтому необходимо применять наиболее подходящие материалы с учетом их стоимости и дефицитности, а также рассчитывать детали с минимальными коэффициентами безопасности.
Работоспособность деталей машин характеризуется определенными условиями или критериями. По одному или по нескольким из этик критериев ведут расчет, цель которого – определение размеров и материалов деталей машин. Часть критериев удовлетворяется заведомо и не требует проверки или вообще относится не ко всем деталям.
Основные критерии работоспособности:
1. Прочность – способность детали выдерживать нагрузки без разрушения.
2. Жесткость – способность деталей, сборочных единиц сопротивляться изменению формы под действием нагрузок.
3. Износостойкость – способность материала рабочих поверхностей деталей сопротивляться изнашиванию.
Изнашивание – процесс разрушения поверхностных слоев при трении, приводящий к постепенному изменению размеров, формы, массы и состояния поверхности деталей. Износ – результат изнашивания.
Износостойкость – важный критерий работоспособности, т.к. около 90 % деталей, имеющих подвижные сопряжения, выходят из строя именно из-за износа.
4. Теплостойкость – способность конструкции работать в пределах заданных температур в течение заданного срока службы.
5. Виброустойчивость – способность машины сопротивляться появлению вредных вынужденных колебаний.
Соблюдение данных критериев обеспечивает надежность конструкции в течение заданного срока службы.
Надежность (общая) – свойство изделий выполнять в течение заданного времени или заданной наработки свои функции, сохраняя в заданных пределах эксплуатационные показатели. Надежность изделий обуславливается их безотказностью, долговечностью, ремонтопригодностью и сохраняемостью.
Безотказность – свойство сохранять работоспособность в течение заданной наработки без вынужденных перерывов. Это свойство особенно важно для машин, отказы которых связаны с опасностью для жизни людей (например, ВС) или с перерывом в работе большого комплекса машин.
Долговечность – свойство изделия сохранять работоспособность до предельного состояния с необходимыми перерывами для ремонтов и технического обслуживания.
Ремонтопригодность – приспособленность изделия к предупреждению, обнаружению и устранению отказов и неисправностей путем проведения технического обслуживания и ремонтов.
Сохраняемость – свойство изделия сохранять требуемые эксплуатационные показатели после установленного срока хранения и транспортирования.
Надежность деталей машин сильно зависит от того, насколько близок режим работы деталей но напряжениям, скоростям и температурам к предельным, т. е. от запасов по основным критериям работоспособности.
Надежность в значительной степени определяется качеством изготовления, которое может изменять ресурс в несколько раз.
Надежность статически определимых механизмов при одинаковых номинальных напряжениях выше, чем статически неопределимых, что связано с меньшим влиянием технологических погрешностей, а также температурных и силовых деформаций. Например, самоустанавливающиеся конструкции, как правило, более надежны, чем несамоустанавливающиеся.
Утрата работоспособности изделий (полная или частичная) называется отказом. Отказы по своей природе могут быть связаны с разрушением деталей или их поверхностей (поломки, выкрашивание, износ, коррозия) или не связаны с разрушением (засорение каналов, ослабление соединений). Различают полные и частичные отказы; внезапные (например, поломки) и постепенные (изнашивание, коррозия и др.); опасные для жизни человека, тяжелые и легкие; устранимые и неустранимые. По времени возникновения отказы делятся на приработочные (возникающие в первый период эксплуатации и связанные с отсутствием приработки и с попаданием в сборку дефектных элементов); отказы при нормальной эксплуатации (до проявления износовых отказов) и износовые отказы, к которым в теории надежности относят также отказы по усталости и старению.
Основным показателем безотказности является вероятность безотказной работы в течение заданного времени или заданной наработки Р(t). Экспериментально этот показатель может быть оценен как отношение числа образцов, сохранивших работоспособность, к общему числу испытанных образцов, если последнее достаточно велико.
В связи с тем, что отказ и безотказная работа – взаимно противоположные события,
,
где – вероятность отказа за время t;
f(t) – плотность вероятности отказов.
Основные показатели долговечности деталей: средний ресурс, т. е. средняя наработка до предельного состояния, и ресурс, который обеспечивается у заданного числа процентов (например, 90 %) изделий, так называемый гамма-процентный ресурс.
Вероятность безотказной работы системы равна по теореме умножения вероятностей произведению вероятностей безотказной работы элементов:
.
Поэтому надежность сложных систем получается низкой, например, при числе элементов п = 10 с одинаковой вероятностью безотказной работы 0,9 общая вероятность безотказной работы равна 0,910 = 0,35.
В период нормальной эксплуатации машин износовые отказы еще не проявляются и надежность характеризуется внезапными отказами. Эти отказы вызываются неблагоприятным стечением многих обстоятельств и имеют постоянную интенсивность, не зависящую от продолжительности предшествующей эксплуатации изделия.
Вероятность безотказной работы определяется по формуле
,
где – постоянная интенсивность отказов;
tср – средняя наработка на отказ.
Если, как обычно, lt £0,1, то Р(t)» 1 – lt.
Для износовых отказов справедлив закон распределения, который дает вначале низкую плотность вероятности отказов, затем максимум и далее падение, связанное с уменьшением числа элементов, оставшихся работоспособными. Наиболее универсальным, удобным и широко применяемым для практических расчетов является нормальное распределение. Плотность вероятности отказов определяется по формуле
.
Распределение имеет два независимых параметра: средняя наработка на отказ ( ) и среднее квадратическое отклонение ( ), где NQ – общее число объектов испытаний или наблюдений.
Вероятность отказов и безотказной работы определяют по таблицам для нормального распределения, приводимым во всех математических справочниках.
Несколько лучше, чем нормальное, описывает результаты усталостных испытаний логарифмически-нормальное распределение, в котором по нормальному закону распределяется логарифм наработки. Однако оперирование этим распределением сложнее.
Выбор материала.При выборе материала следует учитывать следующие факторы:
1. Габаритные размеры, конфигурацию и массу детали.
2. Соответствие материала основным критериям работоспособности и сроку службы.
3. Условия эксплуатации (пыль, агрессивная среда).
4. Применение ресурсосберегающих технологий.
5. Стоимость и дефицитность материала.
6. Возможность унификации (один и тот же материал использовать в разных узлах машины).
Тема 2. Механические передачи
Для приведения в движение машин-орудий необходима механическая энергия, которая получается в электрических, тепловых и др. машинах-двигателях. Чаще всего это энергия вращательного движения вала двигателя.
Как правило, вал двигателя имеет иную, обычно большую, угловую скорость, чем вал приводимой машины. Поэтому между двигателем и орудием вводят промежуточные устройства, которые называют передачами.
Механическими передачами называют устройства, применяемые для передачи и распределения механической энергии от двигателя к рабочему органу (рис. 3.4.1).
В качестве примера покажем схему привода транспортера. От электродвигателя 1 с помощью ременной передачи 2 движение передается на вал зубчатой передачи, заключенной в пылевлагонепроницаемом корпусе 3 (такую передачу называют редуктором); выходной (ведомый) вал зубчатой передачи соединен цепной передачей 4 с валом ленточного транспортера 5.
Причины введения передач между двигателем и орудием:
1. Двигатели работают, как правило, в режиме высоких угловых скоростей, обеспечивающих им наибольшую мощность, КПД и малые габариты; угловые же скорости валов производственных машин обычно отличаются от угловой скорости вала двигателя.
2. Изменение скорости производственной машины (например, автомобиля, токарного станка), а, следовательно, и значения вращающего момента выгоднее осуществлять с помощью передачи, а не путем изменения угловой скорости вала двигателя.
3. Двигатели обычно передают вращательное движение, а рабочие органы машины иногда требуют возвратно-поступательного, качательного, винтового и других видов движения.
4. Часто возникает необходимость передачи энергии от одного двигателя к нескольким механизмам с различными скоростями.
В механических передачах различают ведущие звенья (передающие движения) и ведомые звенья (получающие движение). Принято обозначать параметры ведущих звеньев индексом 1 (нечетные цифры при многоступенчатых передачах), а ведомых – индексом 2 (четные цифры).
У ведущего элемента направления угловой скорости и вращающего момента совпадают; у ведомого – противоположны.
Классификация механических перпедач представлена на рис. 3.4.2.
Рис. 3.4.2. Классификация механических передач
Зубчатые передачи. Зубчатая передача – механизм для передачи вращательного движения между валами и изменения частоты вращения, состоящий из зубчатых колес (или зубчатого колеса и рейки) или из червяка и червячного колеса.
Простейшая одноступенчатая зубчатая передача состоит из двух колес с зубьями, посредством которых они сцепляются между собой. Многоступенчатая зубчатая передача образуется последовательным соединением нескольких одноступенчатых.
Меньшее зубчатое колесо передачи называется шестерней, большее – колесом. Колесо, радиус которого равен бесконечности, называют зубчатой рейкой.
Основными преимуществами зубчатых передач являются постоянство передаточного числа (отсутствие проскальзывания), компактность по сравнению с фрикционными и ременными передачами, высокий кпд (до 0,97…0,98 в одной ступени), большая долговечность и надежность в работе (например, для редукторов общего применения установлен ресурс ~ 30 000 ч), возможность применения в широком диапазоне скоростей (до 200 м/с), мощностей (до десятков тысяч кВт).
К недостаткам зубчатых передач относятся: шум при высоких скоростях, невозможность бесступенчатого изменения передаточного числа, необходимость высокой точности изготовления и монтажа, незащищенность от перегрузок, наличие вибраций, которые возникают в результате неточного изготовления и неточной сборки передач.
По расположению осей валов различают зубчатые передачи с параллельными (рис. 3.4.3, а – в, з), с пересекающимися (рис. 3.4.3, г, д) и перекрещивающимися (рис. 3.4.3, е, ж) геометрическими осями.
Рис. 3.4.3. Зубчатые передачи
По форме различают цилиндрические (рис. 3.4.3, а – в, з), конические (рис. 3.4.3, г, д, ж), эллиптические, фигурные зубчатые колеса и колеса с неполным числом зубьев (секторные).
По форме профилей зубьев различают эвольвентные и круговые передачи, а по форме и расположению зубьев – прямые (рис. 3.4.3, а, г, е, з), косые (рис. 3.4.3, б), шевронные (рис. 3.4.3, в) и круговые (рис. 3.4.3, д, ж).
В зависимости от относительного расположения зубчатых колес передачи могут быть с внешним (рис. 3.4.3, а) или внутренним (рис. 3.4.3, з) их зацеплением. Для преобразования вращательного движения в возвратно поступательное и наоборот служит реечная передача (рис. 3.4.3, е).
Зубчатые передачи эвольвентного профиля широко распространены во всех отраслях машиностроения и приборостроения. Они применяются в исключительно широком диапазоне условий работы. Мощности, передаваемые зубчатыми передачами, изменяются от ничтожно малых (приборы, часовые механизмы) до многих тысяч кВт (редукторы авиационных двигателей). Наибольшее распространение имеют передачи с цилиндрическими колесами, как наиболее простые в изготовлении и эксплуатации, надежные и малогабаритные. Конические, винтовые и червячные передачи применяют лишь в тех случаях, когда это необходимо по условиям компоновки машины.
Планетарными называются передачи, содержащие зубчатые колеса с перемещающимися осями.
Волновая передача основана на принципе преобразования параметров движения за счет волнового деформирования гибкого звена механизма. Впервые такая передача была запатентована в США инженером И.В. Массером.
Передачи, работа которых основана на использовании сил трения, возникающих между рабочими поверхностями двух прижатых друг к другу тел вращения, называют фрикционными передачами.
Червячные передачи. Червячная передача применяется для передачи вращения от одного вала к другому, когда оси валов перекрещиваются. Угол перекрещивания в большинстве случаев равен 90º. Наиболее распространенная червячная передача состоит из так называемого архимедова червяка, т.е. винта, имеющего трапецеидальную резьбу с углом профиля в осевом сечении, равным двойному углу зацепления (2α = 40°), и червячного колеса.
Ременные передачи. Ременная передача состоит из двух шкивов, закрепленных на валах, и охватывающего их ремня. Ремень надет на шкивы с определенным натяжением, обеспечивающим трение между ремнем и шкивами, достаточное для передачи мощности от ведущего шкива к ведомому.
В зависимости от формы поперечного сечения ремня различают плоскоременную (рис. 3.4.4, а), клиноременную (рис. 3.4.4, б) и круглоременную (рис. 3.4.4, в) передачи.
Сравнивая ременную передачу с зубчатой можно отметить следующие преимущества: возможность передачи движения на значительное расстояние (до 15 м и более); плавность и бесшумность работы, обусловленные эластичностью ремня и позволяющие работать при высоких скоростях; способность выдерживать перегрузки (до 300 %) благодаря увеличению скольжения ремня; невысокая стоимость, простота обслуживания и ремонта.
Основными недостатками ременной передачи являются непостоянство передаточного отношения из-за скольжения ремня на шкивах, значительные габаритные размеры при больших мощностях (для одинаковых условий диаметры шкивов примерно в пять раз больше диаметров зубчатых колес), большое давление на шкивы в результате натяжения ремня, низкая долговечность ремней (от 1000 до 5000 ч).
Ременные передачи применяют преимущественно в тех случаях, когда по условиям конструкции валы расположены на значительных расстояниях. Мощность современных передач не превышает 50 кВт.
В многоступенчатых приводах ременную передачу применяют обычно в качестве быстроходной ступени, устанавливая ведущий шкив на валу двигателя. В таком случае габариты и масса передачи будут наименьшими.
Цепные передачи. Цепная передачасостоит из двух колес с зубьями (звездочек) и охватывающей их цепи. Наиболее распространены передачи с втулочно-роликовой цепью (рис. 3.4.5, а) и зубчатой цепью (рис. 3.4.5, б). Цепные передачи применяются для передачи средних мощностей (не более 150 кВт) между параллельными валами в случаях, когда межосевые расстояния велики для зубчатых передач.
Преимуществами цепных передач являются отсутствие проскальзывания, достаточная быстроходность (20…30 м/с), сравнительно большое передаточное число (7 и более), высокий КПД, возможность передачи движения от одной цепи нескольким звездочкам, небольшая нагрузка на валы, так как цепная передача не нуждается в предварительном натяжении цепи необходимом для ременной передачи.
Недостатками цепных передач являются вытяжка цепей вследствие износа шарниров, более высокая стоимость передачи по сравнению с ременной, необходимость регулярной смазки, значительный шум.
По назначению цепи подразделяют на приводные передачи, используемые в приводах машин, тяговые (рис. 3.4.6) – передачи, применяемые в качестве тягового органа, и грузовые – передачи, используемые в грузоподъемных машинах дл подъема грузов.
Передачи «винт – гайка». «Передача винт – гайка»служит для преобразования вращательного движения в поступательное. Широкое применение таких передач определяется тем, что при простой и компактной конструкции удается осуществить медленные и точные перемещения.
В авиастроении передача «винт – гайка» используется в механизмах управления ВС: для перемещения взлетно-посадочных закрылков, для управления триммерами, поворотными стабилизаторами и др.
К преимуществам передачи относятся простота и компактность конструкции, большой выигрыш в силе, точность перемещений.
Недостатком передачи является большая потеря на трение и связанный с этим малый КПД.
В качестве примера рассмотрим конструкцию винтового механизма, используемого на самолетах Ту-154 в качестве подъемников предкрылков, которая включает в себя головку подъемника – редуктор, винтовую пару и узлы крепления к предкрылку и крылу.
В подъемнике внутреннего предкрылка (рис. 3.4.7) конические колеса установлены в корпусе 1. Шестерня 2 вращается вместе с валом трансмиссии. Колесо 3 соединено с винтом 4 шарнирно-винтовой парой.
Шарики заполняют в гайке две секции, каждая из которых образует отдельную замкнутую цепочку шариков. При вращении винта шарики перемещаются по каналам, образуемым резьбой винта и гайки, а гайка при этом совершает поступательное движение.
На гайке 8 закреплена вильчатая труба 7 с карданным узлом 6, связанным с предкрылком. Ход гайки ограничен упорами 5. Серьга 9 крепится на лонжероне крыла.
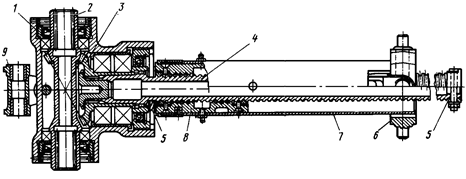
Рис. 3.4.7. Подъемник внутреннего предкрылка
Рычажные механизмы. Механизмы, в которые входят жесткие звенья, соединенные между собой кинематическими парами пятого класса, называют рычажными механизмами.
В кинематических парах таких механизмов давление и интенсивность изнашивания звеньев меньше, чем в высших кинематических парах.
Среди разнообразных рычажных механизмов наиболее распространенными являются плоские четырехзвенные механизмы. Они могут иметь четыре шарнира (шарнирные четырехзвенники), три шарнира и одну поступательную пару или два шарнира и две поступательные пары. Их используют для воспроизведения заданной траектории выходных звеньев механизмов, преобразования движения, передачи движения с переменным передаточным отношением.
Под передаточным отношением рычажного механизма понимают отношение угловых скоростей основных звеньев, если они совершают вращательные движения, или отношение линейных скоростей центра пальца кривошипа и выходного звена, если оно совершает поступательное движение.
Примеры применения рычажных механизмов в авиационной технике.
На рис. 3.4.8 представленрычажный механизм управления посадочными щитками самолета.
Рукоятка 6 входит во вращательные пары В и С со звеном 5, вращающимся вокруг неподвижной оси А, и штоком а поршня 8, движущегося в неподвижном цилиндре 7. Со штоком b поршня 3, движущегося в неподвижном цилиндре 2, соединен ролик 9, скользящий в кулисе d щитка 1, вращающегося вокруг неподвижной оси D. При качании рукоятки 6 поршень 8 перекачивает жидкость в рабочий цилиндр 4. Шток b поршня 3 при своем движении поворачивает посадочные щитки 6 ВС. Обратный ход поршня 3 осуществляется пружиной.
Кулачковые механизмы. Кулачковые механизмы (рис. 3.4.9) по широте применения уступают только зубчатым передачам. Их используют в станках и прессах, двигателях внутреннего сгорания, машинах текстильной, пищевой и полиграфической промышленности. В этих машинах они выполняют функции подвода и отвода инструмента, подачи и зажима материала в станках, выталкивания, поворота, перемещения изделий и др.
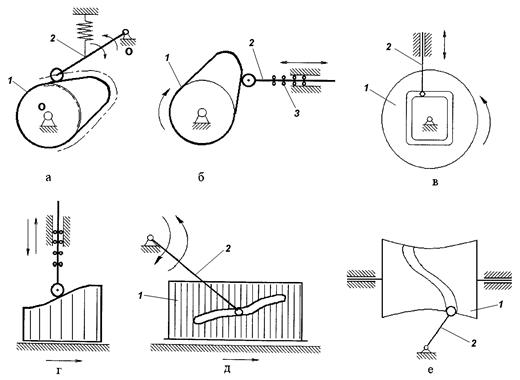
Рис. 3.4.9. Кулачковые механизмы:
а, б, в – дисковые; г, д – плоские с поступательным перемещением кулачка; е – гиперболоидные
Кулачковые механизмы имеют ряд преимуществ: возможность воспроизведения почти любого закона движения ведомого звена, простота согласования работы нескольких механизмов в машинах-автоматах, надежность в работе и компактность.
К недостаткам этих механизмов следует отнести относительно быстрое изнашивание соприкасающихся поверхностей, которое обусловлено ускоренным движением толкателя, отсутствием смазки, а также наличием вибрации, которая возрастает с увеличением частоты вращения кулачка.
В зависимости от вида движения кулачка механизмы подразделяют на поступательные (рис. 3.4.9, г, д), вращательные (рис. 3.4.9, а, б, в) и качающиеся. По взаимному расположению кулачка и толкателя механизмы называют центральными и дезаксиальными (нецентральными). По типу замыкания высшей кинематической пары их подразделяют на пары с кинематическим и силовым замыканием.
Силовое замыкание происходит под действием пружины, силы тяжести груза либо реализуется гидравлическим или пневматическим способом. Оно характерно преимущественно для механизмов, работающих с небольшими скоростями звеньев.
Анализ кулачковых механизмов. Основной задачей анализа движения звеньев кулачковых механизмов является определение перемещений (S), скоростей (V), ускорений (а) точек ведомого звена по заданному очертанию профиля кулачка и функции движения ведущего звена.
Для проведения анализа должны быть заданы кинематическая схема механизма, профиль кулачка и закон движения ведомого звена (толкателя).
В общем случае за время одного оборота кулачка толкатель проходит следующие фазы движения:
1. Фазу удаления (толкатель перемещается на максимальное расстояние от центра вращения кулачка).
2. Фазу дальнего стояния (толкатель находится в покое в верхнем положении).
3. Фазу возвращения (толкатель возвращается в исходное положение).
4. Фазу ближнего стояния (толкатель находится в покое в нижнем положении).
В течение этих фаз соответственно за время ty, tд, tв, … tб кулачок поворачивается на угол φу, φд, φв, φб (рис. 3.4.10, а). Сумму φу + φд + φв = φр называют рабочим углом кулачка.
Закон движения толкателя обычно задают в виде функции его ускорения от времени, представленной в аналитической форме или в виде графика, т.е. должен удовлетворять кинематическому и динамическому условиям. Если в некоторый момент времени ускорение выходного звена стремится к бесконечности (рис. 3.4.10, б), то звено осуществляет движение с жестким ударом; если ускорение мгновенно изменяется на конечную величину (рис. 3.4.10, в) – движение с мягким ударом. При плавном изменении ускорения от минимального значения до максимального, называется безударным (рис. 3.4.10, г).
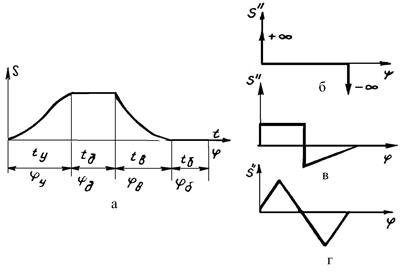
Рис. 3.4.10. Законы движения толкателя
Основные кинематические и силовые соотношения в передачах:
1.Окружная скорость (V) – линейная скорость точек вращающегося тела, отстоящих от оси вращения на расстоянии , определяется по формуле
, т.к. .
где V – окружная скорость, м/с;
– угловая скорость, рад/с;
n – частотавращения, мин-1.
2. Окружная сила( ) – сила, вызывающая вращение тел или сопротивление вращению и направленная по касательной к траектории точки ее приложения.
Из известного соотношения:
;
,
где – мощность, Вт;
,
где Т – крутящий момент, Н×м.
Þ .
3. Передаточное число– отношение угловых скоростей двух валов – ведущего к ведомому:
,
где и – угловая скорость и частота вращения ведущего вала;
и – угловая скорость и частота вращения ведомого вала.
Знак: «+» – при одинаковом направлении вращения, «–» – при противоположном.
Передаточное отношение – отношение угловых скоростей любых валов независимо от направления силового потока:
, а .
Если известны другие параметры передачи:
, .
Для зубчатых передач:
,
где и – число зубьев ведомого и ведущего колеса.
Таким образом, передаточное число находится по формуле
(обратите внимание на индексы букв).
Если , передачу называют понижающей, если – повышающей.
В многоступенчатых передачах, общее передаточное число равно произведению передаточных чисел каждой ступени передачи, т.е.
.
Элементы зубчатого зацепления.У зубчатого колеса условно различают тело или основание (диск со ступицей) и зубчатый венец, отделяемый от тела соосной поверхностью впадин.
Геометрические параметры цилиндрических зубчатых колес. Зацепление зубчатых колес эквивалентно качению без скольжения окружностей с диаметрами и , называемых начальными окружностями (рис. 3.4.11). Заметим, что у пары сопряженных зубчатых колес может быть бесчисленное множество начальных окружностей.
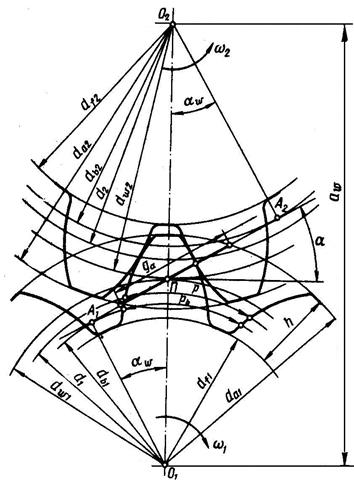
Рис. 3.4.11
Если заменить одно из колес зубчатой рейкой, то для каждого зубчатого колеса найдется только одна окружность, катящаяся по начальной прямой без скольжения. Эта окружность называется делительной окружностью ( ), единственной для каждого колеса.
В большинстве случаев начальные и делительные окружности совпадают. В дальнейшем рассматривается только такой случай зацепления.
Полюс зацепления называется точка касания начальных окружностей.
Окружность вершин( ) – окружность, ограничивающая высоту зубьев.
Окружность впадин ( ) – окружность, ограничивающая впадины зубьев.
Головка зуба – часть зуба, расположенная между делительной окружностью цилиндрического зубчатого колеса и окружностью вершин зубьев.
Ножка зуба – часть зуба, расположенная между делительной окружностью и окружностью впадин.
Высота зуба (h) – радиальное расстояние между окружностями вершин и впадин зубчатого колеса. Высота зуба рассчитывается по формуле
,
где ha – высота головки;
hf – высота ножки зуба
Радиальный зазор(с)– расстояние между поверхностями вершин зубьев и впадин шестерни и колеса. Радиальный зазор рассчитывается по формуле
.
Окружная толщина зуба (st) – расстояние между разноименными профилями зуба по дуге делительной окружности зубчатого колеса.
Шаг зацепления– кратчайшее расстояние между одноименными профильными поверхностями. Шаг зацепления по делительной окружности рассчитывается по формуле
.
Ширина венца (b)– наибольшее расстояние между торцами зубьев цилиндрического зубчатого колеса по линии, параллельной его оси.
Межосевое расстояние ( ) – расстояние между осями зубчатых колес передачи.
Модуль зубьев (т) – часть диаметра делительной окружности, приходящаяся на один зуб
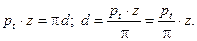
Обозначим – окружной модуль зубьев, тогда
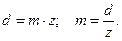
Модуль является основной стандартизированной характеристикой размеров зубьев (табл. 1). Для пары зацепляющихся колес модуль должен быть одинаковым.
Таблица 1
Ряды
| Модуль, мм
| 1-й
| 1; 1,25; 1,5; 2; 2,5; 3; 4; 5; 6; 8; 10; 12; 16; 20; 25
| 2-й
| 1,125; 1,375; 1,75; 2,25; 2,75; 3,5; 4,5; 5,5; 7; 9; 11; 14; 18; 22
| Примечание. Предпочтение следует отдавать 1-му ряду.
Силы, действующие в зацеплении. Цилиндрическая прямозубая передача
Распределенную нагрузку на площадке контакта принято представлять в виде сосредоточенной силы (рис. 3.4.12).
Нормальная сила между парой контактирующих зубьев определяется по формуле:
,
где – контактное напряжение;
– площадь поверхности контакта.
Для упрощения принимают, что сила приложена в точке зацепления.
Для расчетов силу раскладывают на окружную и радиальную составляющие:
.
; .
Основные критерии работоспособности зубчатых передач. При передаче крутящего момента в зацеплении кроме нормальной силы (Fn) действует сила трения (Fтр = Fnf), связанная со скольжением. Под действием этих сил зуб находится в сложном напряженном состоянии. Решающее влияние на его работоспособность оказывают два основных напряжения: контактные напряжения (σН) и напряжения изгиба (σF). Для каждого зуба σН и σF не являются постоянно действующими. Они изменяются во времени по некоторому прерывистому отнулевому циклу (рис. 3.4.13). Время действия σF за один оборот колеса (t1) равно продолжительности зацепления одного зуба (t2). Напряжения σН действуют еще меньшее время.
Не нашли, что искали? Воспользуйтесь поиском по сайту:
©2015 - 2025 stydopedia.ru Все материалы защищены законодательством РФ.
|