Технология изготовления конструкционных элементов для жилищного строительства.
При использовании разных технологий используются свои типовые конструкционные элементы, рассмотрим технологии их производства.
Деревянные технологии
В деревянной технологии основными элементами являются брус и цилиндрованное бревно.
Клееный брус изготавливается из пиломатериалов сосны или ели, Вологодской, Пермской, Омской, Иркутской, Новосибирской областей и республики Коми.
Сушка материалов осуществляется до 10% влажности (как для производства мебели) в сушильных камерах.
Затем на специальной технологической линии вырезаются нездоровые сучки, производится сращивание досок до длины 12м (ламели).
После чего ламели, в специальном прессе под давлением 10кг/см2, склеиваются экологически чистым клеем
Окончательная фаза производства клееного бруса - профилирование заготовок и нарезание узловых соединений, позволяющих изготавливать продукцию в жёстких допусках.
Каждая деталь конструкции деревянного дома из клееного бруса проходит индивидуальный контроль и маркируется.
Затем из готовых деталей формируются пакеты. Их упаковывают в многослойную полиэтиленовую пленку и отправляют по месту назначения.
Типовая технология изготовления сруба оцилиндрованного бревна представляет собой последовательность операций:
1. Изготовление заготовок.

Рис. 1.8.
Оцилиндровка и профилирование бревна. Полный цикл изготовления бревна 15-30 минут.

Рис. 1.9.
Оцилиндровка и профилирование бревна. В комплексе смонтирована высокопроизводительная ленточнопильная часть, позволяющая изготавливать доски, брус, бруски и рейки.

Рис. 1.10.
Оцилиндровочный комплекс проходного типа для крупных домостроительных производств. Переработка кругляка, максимальный диаметр Ø320 мм с целью изготовления оцилиндрованных и срубовых бревен, бруса и обрезной доски.
2. Торцевание бревен в размер по длине
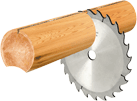
Рис. 1.11.
Оцилиндрованное бревно подается на торцовочный станок для задания базы, от которой ведется разметка для зарезки чаши.
3. Фрезерование чашек в бревне
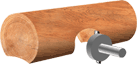
Рис. 1.12.
После установки в заданной точке и выставления необходимого угла происходит механический или пневматический прижим и зарезка поперечного паза (чашки) соответствующего диаметра.
Строительство из камня
В большинстве случаев для производства пенобетона используют одну из двух технологий - баротехнологию или классическую технологию.
Мобильные установки без пеногенератора, работающие по принципу баротехнологии. Данные установки позволяют получать пенобетон без пеногенератора. Производительность установок 20 и 40 куб.м. пенобетона в сутки, соответственно. Плюсами данных установок являются дешевизна и простота получения пенобетона. Минусами повышенный расход пенообразователя, сравнительно небольшая производительность и меньшая прочность получаемого пенобетона, по сравнению с оборудованием на базе пеногенераторов.
Установки для пенобетона с пеногенератором работают по классической технологии пенобетона. Установки смонтированы как единый комплекс и позволяют получать до 100 куб.м. пенобетона в сутки. Плюсами данных установок являются высокая производительность, небольшой расход пенообразователя, легкая встраиваемость в технологические линии производства, получение пенобетона с большей прочностью и более низкой себестоимостью. Минус - более высокая цена по сравнению с мобильными установками.
Вне зависимости от типа установки и вида технологии производства пенобетона, в ней получается пенобетон. Если заливать этот пенобетон на стройке в опалубку, то кроме одной из этих установок и компрессора к ней, более ничего не нужно. Если производить пенобетонные блоки, то понадобится заливать выходящий из установок пенобетон в формы для получения блоков.
Способов получения блоков три:
Заливка пенобетона в кассетные металлические формы. Залитый пенобетон застывает в течение 10 часов, после этого форма разбирается, и из нее достаются готовые блоки. Одну форму можно использовать 2 раза за сутки. Соответственно, если производить 20 куб.м. пенобетона в день, то нужно 10 форм и 2-х сменная работа.
При изготовлении формы применяется лазерная резка и фрезеровка, что позволяет производить высокоточные формы для пенобетона с отклонением размеров на блок не более 1 мм. Формы универсальные, т.е. в одной и той же форме можно производить и перегородочные блоки толщиной 100 мм и стеновые толщиной 200 мм. Типоразмеры форм - 500х300х100(200), 600х300х100(200), 400х200х200. Возможно и изготовление форм других типоразмеров.
При объемах производства до 40 куб.м. блоков в день технология разливки по формам экономически более целесообразна. Плюсы: сравнительно небольшие вложения и простота производства. Минусы: трудно производить большие объемы, привязанность к типоразмерам.
Резка пенобетонных массивов на резательных установках. Сначала пенобетон заливается в формы без перегородок, где получается большой массив объемом 2-3 куб.м. Примерно через 14 часов пенобетон подается на резку, где из него пилами автоматически выпиливаются блоки нужного размера.
Данный метод отличается высокой производительностью и высокой технологичностью. Причем, при резке пенобетона можно получать блоки любых типоразмеров. Минусы: высокая стоимость и отход 0,5% в виде крошки от пиления. Посмотреть оборудование для резки пенобетона.
Разливка пенобетона в специальные формы и их последующая автоматическая распалубка. Сначала пенобетон заливается в специальные формы с перегородоками, где при застывании получаются готовые блоки. Примерно через 14 часов формы подаются в установку автоматической распалубки, где блоки выдавливаются на европоддон, а формы при этом автоматически смазываются.
Данный метод прост и производителен. Большой недостаток: привязанность к одному типоразмеру выпускаемых блоков. Установку автоматической распалубки невозможно перенастроить на производство блоков других типоразмеров.
Способы производства кирпича изменялись с течением времени от столетия к столетию. До ХIX века эта процедура была весьма трудоемкой, так как кирпич формовался вручную. Его сушка возможна была только в летнее время, а формовка производилась в больших напольных печах, выложенных из высушенного кирпича-сырца. Примерно двести лет назад были изобретены кольцевая обжиговая печь и ленточный пресс, что весьма облегчило процесс производства. Также в XIX веке стали выпускаться и глинообрабатывающие машины.
На сегодняшний день больше всего кирпича производится круглогодично на крупных заводах. Эти предприятия выпускают более 200 миллионов кирпичей в год. В производстве кирпича обычно применяются легкосплавные песчанистые и мергелистые глины.
На сегодняшний день существуют две основные технологии производства этого стройматериала. Первая основана на обжиге глины, а вторая осуществляется без него.
Технология обжигового кирпича. Подготовка материала для будущего кирпича может быть произведена следующим способом. Глина, извлеченная из карьера, помещается в бетонированные творильные ямы, в которых ее разравнивают и заливают водой. В таком состоянии материал оставляют на 3-4 дня. Только после этого глина доставляется на завод для произведения машинной переработки.
Для удаления из глинистой массы камней обычно применяются специальные камневыделительные вальцы. После проведения этой процедуры глина поступает в ящичный питатель. У выходного отверстия этой машины размещаются подвижные грабли, которые частично разбивают куски и выталкивают глину на бегуны. Здесь глина хорошо размалывается. Затем материал проходит через одну или две пары гибких вальцов и поступает в ленточный пресс, соединенный с резательным аппаратом. Кирпич отрезается от глиняной ленты и попадает на подкладочные деревянные рамы. После такой расфасовки материал помещается в сушильную камеру. Когда камера полностью заполняется, ее запирают и разогревают.
Сушка кирпича чаще всего производится искусственным способом, так как она не требует большого складского пространства и не зависит от погодных условий. Для такой сушки используют тепло отработанного пара. В результате постепенного подъема температуры в сушильной камере образуются водяные испарения без движения воздушных потоков. Это благоприятно влияет на сушку кирпича. Кирпич во влажном воздухе нагревается, что обеспечивает равномерное высыхание всей массы. Высушенный кирпич поступает в кольцевую или туннельную печь для обжига. Эта операция происходит при температуре около 1000 градусов. Обжиг длится до начала спекания.
Хороший кирпич должен иметь матовую поверхность, и при ударе давать звонкий звук. Требуется, чтобы на изломе он был однородным пористым и легким. Кирпич считается бракованным, если в нем есть внутренние пустоты и трещины на внешней стороне.
Технология безобжигового кирпича. В данном случае применяется гипер- или трибо-прессование. Это технология сварки минеральных сыпучих материалов под воздействием высокого давления в присутствии вяжущих компонентов и воды, завершающаяся выдержкой на складе в течение 3-5 суток до созревания. На первой стадии исходное сырье дробится до фракции 3-5 мм, после чего поступает в приемный бункер. Затем, пройдя по ленточному транспортеру через расходный бункер и питательный дозатор, материал попадает в бетоносмеситель. Там происходит его смешивание с цементом до получения однородной массы. На второй стадии осуществляется поставка готового материала по ленточному конвейеру через двухрукавную течку на установку формования. После прессования кирпич можно сразу помещать на технологические поддоны. На них он и размещается на складе, где происходит естественная выдержка в течение 3-7 суток. После этого производится отгрузка готового кирпича потребителю.
Каркасное домостроение.
Деревянные сборные дома возводятся по архитектурному проекту, «скелетом» здания являются деревянные заготовки – балки, стропильные фермы (системы), фермы перекрытия, стеновые панели. Стропильные конструкции, составляющие основу каркасно-панельных сборных домов, изготавливаются в соответствии со всеми строительными нормами. Параллельно идет процесс возведения фундамента.
После того, как каркасно-панельные дома будут укомплектованы основными конструкциями, они отправляются на объект. Далее проводится монтаж деревянного быстросборного панельно каркасного дома согласно чертежам. Такие постройки имеют самый высокий уровень заводской готовности, все элементы дома и его комплектование происходит в заводских условиях и прибывают на строительную площадку полностью подготовленные к сборке.

Рис 1.14. Структура панели.
Панели состоят из двух ориентированных стружечных плит OSB (ОСП), между которыми под давлением приклеивается слой пенополистирола в качестве утеплителя. Толщина панелей в готовом виде составляет от 160 мм до 220 мм. Стандартный размер панели 1,25 метра на 2,5 метра.
Исходным сырьем для ОСП-плит (OSB) сосновые деревья небольшого диаметра, так называемая тонкомерная древесина. При этом, что очень важно, древесные отходы не используются. Это гарантирует однородность структуры плиты и соблюдение главного правила: толщина каждой стружки должна составлять 0,4 мм. Таким образом, около 90 % бревна, очищенного от коры, лущится на щепу для ОСП-плиты (OSB).
Краткое описание технологического процесса позволяет лучше понять особенности ОСП-плиты (OSB). Бревна сортируют, затем проводят специальную обработку, окоривают и строгают на щепу. Средняя длина щепы составляет 150 мм, а ширина вирируется в зависимости от части ствола. Щепу сушат в специальных центрифугах. Далее, пропитывая водостойкими смолами и воском, укладывают конвейерным способом в двух направлениях, создавая так называемый ковер. Затем щепу подвергают воздействию высоких температур и давления. В заключение полотно ОСП-плиты (OSB) разрезают по размерам заказчика. Произведенные плиты подвергаются постоянно физическим тестам основанным на специальных методах контроля и тестах стандартизации.
Различают 4 вида плит OSB — в зависимости от влагостойкости и прочности. Наибольшим спросом на рынке сегодня пользуются плиты OSB-3, благодаря своей универсальности и более низкой стоимости, в сравнении с плитами OSB-4.
OSB-1 -предназначена для использования в условиях пониженной влажности (мебель, обшивка, упаковка);
OSB-2 - используется при изготовлении несущих конструкций в сухих помещениях;
OSB-3 - материал, выдерживающий более тяжелые режимы эксплуатации при изготовлении несущих конструкций в условиях повышенной влажности.
Не нашли, что искали? Воспользуйтесь поиском по сайту:
©2015 - 2024 stydopedia.ru Все материалы защищены законодательством РФ.
|