Термическая обработка. Определение оптимального режима закалки углеродистой стали
Закалка – термическая обработка, заключающаяся в нагреве стальных изделий до температуры выше критических точек, выдержке при этой температуре до сквозного прогрева и быстрое охлаждение в воде, масле или какой-либо другой закалочной среде.
Простую углеродистую сталь подвергают закалке исключительно, чтобы повысить твердость и прочность закаленных изделий, а легированную сталь, помимо этого, чтобы улучшить ее служебные физико-химические свойства, например, магнитную проницаемость, коррозионную стойкость и т.п.
Режим закалки различных марок стали устанавливают в зависимости от содержания углерода в стали, от размеров и массы изделий, от их назначения, от формы деталей, от количества обыкновенных и случайных примесей, от способа укладки изделий в печи, от количества одновременно закаливаемых изделий. Иногда сталь одной и той же марки, но разных плавок при закалке ведет себя поразному. Чтобы не было брака из-за низкой твердости, перегрева, трещин перед обработкой больших партий изделий для корректировки режима закалки проводят пробную закалку, а затем уже обрабатывают всю партию.
Температуру закалки для углеродистых сталей выбирают по диаграмме состояния Fe – C.
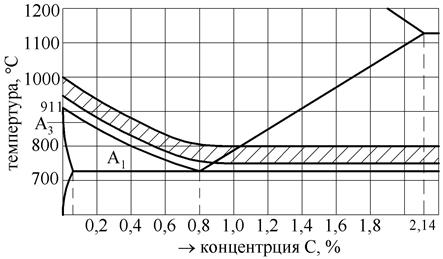
Рис. 23. График нагрева под закалку с различным содержанием углерода
Для доэвтектоидных сталей температура закалки лежит на 30-50 °C выше линии Ас3, для заэвтектоидных сталей – на 30-50 °C выше Ас1.
При введении в сталь легирующих элементов диаграмма изотермического превращения очень часто резко изменяется, появляются перегибы и смещения по горизонтали и вертикали.
Время закалки складывается из времени нагрева tн и времени выдержки в печи tв:
.
Теоретически tн можно приблизительно определить по следующей формуле:

где Д – минимальный размер максимального сечения, мм;
к1 – коэффициент среды (для газа к1 =2; соли к1 =1; металла к1 =0,5);
к2 – коэффициент формы (для шара к2 =1, цилиндра к2 =2, параллелепипеда к2 =2,5, для пластины к2 =4);
к3 – коэффициент равномерности нагрева (для всестороннего нагрева к3 =1, для одностороннего к3 =4).
Время выдержки tвпринимают для углеродистых сталей равным приблизительно одной минуте, для легированных – 2 минуты.
Закалка стали сопровождается существенным увеличением объема, что вызывает появление значительных внутренних напряжений. Закалочные напряжения могут привести к короблению изделий и образованию трещин в процессе закалки. Кроме того, оставшиеся внутренние напряжения могут вызвать деформацию изделий с течением времени в условиях эксплуатации. Поэтому закаленные детали всегда подвергают отпуску.
Отпуск – вид термической обработки стали, в результате которой неустойчивые структуры закалки переходят в более устойчивые. Отпуск осуществляется путем нагрева закаленной стали до температур, меньших Ас1, выдержки при этих температурах и охлаждении. Режим отпуска определяет конечные свойства закаленного изделия.
Практическими целями отпуска являются: уменьшение закалочных напряжений, снижение твердости до требуемого уровня, получения нужного комплекта механических свойств (прочности, пластичности и вязкости).
В зависимости от температуры различают три практические разновидности отпуска: низкий, средний и высокий.
Низкий отпуск – нагрев закаленной стали до температур 180–250 °С. Твердость понижается на 2–3 HRC. Структура – отпущенный мартенсит – пересыщенный твердый раствор углерода в a-железе такой же концентрации, как у исходного аустенита. Такой отпуск применяется для инструментальных, подшипниковых сталей, малоуглеродистых после цементации для изготовления деталей и инструментов, работающих на износ, от которых требуется высокая твердость.
Средний отпуск – нагрев закаленной стали до температур 350–500 °С. Твердость понижается примерно на 15–20 HRC. Структура ‑ зернистый троостит отпуска ‑ высокодисперсная разновидность перлита, состоящий из равновесного феррита и дисперсных включений цементита. Этот вид отпуска рекомендуется при термической обработке рессор и пружин.
Высокий отпуск – нагрев закаленной стали до температур 500–680 °С. Твердость понижается на 22–25 HRC. Структура – сорбит отпуска - дисперсная разновидность перлита, ферритокарбидная смесь. Высокий отпуск рекомендуется для среднеуглеродистых конструкционных сталей.
ЗАДАЧА № 12
1 Нарисовать часть диаграммы Fe – C и указать на ней температуры нагрева под закалку данных сталей.
2 Назначить режим закалки и отпуска, следующих изделий:
- пруток d=3, =200, сталь У12;
- шар d=26 сталь 40;
- цилиндр d=80, h=60, сталь У7;
- 6´8´15, сталь 65.
3 Проанализировать табл. 5 твердостей закаленных углеродистых сталей и определить более и менее твердые материалы.
4 Построить график изменения твердости HRC после закалки от содержания углерода в стали по табл. 5.
Таблица 5
Не нашли, что искали? Воспользуйтесь поиском по сайту:
©2015 - 2025 stydopedia.ru Все материалы защищены законодательством РФ.
|