Быстрорежущие стали нормальной и повышенной производительности.
Быстрорежущие стали применяют для режущих инструментов, работающих в условиях значительного нагружения и нагрева рабочих кромок. Инструмент из быстрорежущих сталей обладает высокой стабильностью свойств.
Они маркируются Р18, Р6М5 и др. В марках стали буквы и цифры обозначают Р – быстрорежущая, цифра, следующая за буквой – среднюю массовую долю вольфрама, М – молибден, Ф – ванадий, К – кобальт, А – азот; цифры, следующие за буквами, означают соответственно массовую долю молибдена, ванадия, кобальта; Ш – электрошлаковый переплав.
Быстрорежущие стали сочетают высокую теплостойкость (600-650 С в зависимости от состава и обработки) с высокими твердостью до 68–79 HRC, износостойкостью при повышенных температурах и повышенным сопротивлением пластической деформации.
Для обеспечения красностойкости сталь легируют большим количеством вольфрама в сочетании с молибденом и ванадием. Кроме этих элементов все быстрорежущие стали легированы хромом, а некоторые кобальтом.
Применяемые быстрорежущие стали делят на три группы: стали нормальной производительности, повышенной и высокой производительности.
Стали нормальной производительности характеризуются пониженной теплостойкостью (615–620 С). К ним относятся: вольфрамовые стали (Р9, Р12, Р18), вольфрамомолибденовые (Р6М5, Р6М3, Р8М3 и др.), безвольфрамовые (9Х6М3Ф3АГСТ, 9Х4М3Ф2АГСТ и др.).
Стали повышенной производительности дополнительно легированы кобальтом и ванадием. К ним относятся стали с повышенной теплостойкостью 625-640 С: вольфрамокобальтовые (Р9Ф5, Р9К10 и др.); вольфрамованадиевые (Р9Ф5, Р12Ф3 и др.), вольфрамованадиевые с кобальтом (Р10Ф5К5, Р12Ф4К5 и др.); вольфрамованадиевые с кобальтом и молибденом (Р12Ф3К10М3, Р12Ф2К5М3 и др.).
К группе быстрорежущих сталей повышенной производительности следует отнести и быстрорежущие дисперсионно-твердеющие сплавы с интерметаллидным упрочнением. Их высокая теплостойкость и режущие свойства обеспечиваются высокими температурами превращения и упрочнением вследствие выделения при отпуске интерметаллидов, имеющих более высокую устойчивость, к коагуляции при нагреве, чем карбиды. Наибольшее распространение получил сплав В11М7К23 (ЭП831).
Быстрорежущие стали относятся к ледебуритному (карбидному) классу.
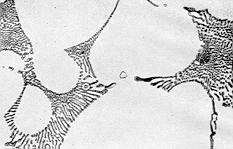
Их фазовый состав в отожженном состоянии представляет собой легированный феррит и карбиды. В феррите растворена большая часть хрома; почти весь вольфрам (молибден) и ванадий находятся в карбидах.
Для снижения твердости, улучшения обработки резанием и подготовки структуры стали к закалке быстрорежущую сталь после ковки подвергают отжигу при 860–880 С.
Для придания стали теплостойкости инструменты подвергают закалке и многократному отпуску
Окончательная термическая обработка – закалка и высокий отпуск. Микроструктура закаленной стали состоит из легированного мартенсита, остаточного аустенита (до 30%) и карбидов. После трехкратного отпуска при температуре 560 С количество остаточного аустенита уменьшается до 2–3%, твердость увеличивается. Для снижения количества остаточного аустенита применяется обработка холодом.
Для придания стали теплостойкости инструмент подвергают закалке и многократному отпуску. 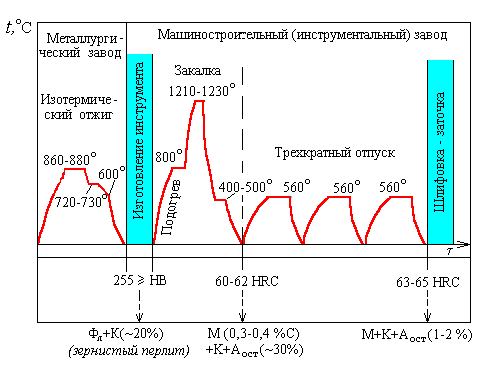
Схема термической обработки быстрорежущей стали P6M5. Фл - легированный феррит; К - карбид; М - мартенсит; Аост - остаточный аустенит. В скобках показано количество углерода в мартенсите и количество остаточного аустенита в структуре стали, %
| Высокие температуры закалки необходимы для более полного растворения вторичных карбидов и получения высоколегированного аустенита. Это обеспечивает обеспечивает получение после закалки мартенсита, обладающего высокой устойчивостью против отпуска, т.е. теплостойкостью. Во избежание образования трещин в инструменте при нагреве до температуры закалки его подогревают. Выдержка при температуре закалки должна быть непродолжительной -от 8 до 9 с на каждый миллиметр диаметра или наименьшей длины инструмента при нагреве в расплавленной соли (чаще в BaCl2) и 12–14 с при нагреве в печи. Охлаждающей средой при закалке чаще является масло. Для уменьшения деформации инструментов применяют ступенчатую закалку в расплавленных солях (KN03) при 400–500 °C. После закалки следует трехкратный отпуск, вызывающий превращение остаточного аустенита в мартенсит и дисперсное твердение за счет выделения карбидов. Режущие свойства инструмента, не подвергающегося переточке по всем граням (сверла, развертки, метчики, фрезы), можно повысить азотированием при 550–560 °С.
Билет 8
Не нашли, что искали? Воспользуйтесь поиском по сайту:
©2015 - 2025 stydopedia.ru Все материалы защищены законодательством РФ.
|