Перекристаллизационный отжиг и нормализация.
1)Конструкционные стали чаще всего содержат углерод в количестве
до 0,7%. т.е. являются доэвтектоидньши сталями.
Перекристаллизационный отжиг проводит для снижения твердости, повышения пластичности и получения однородной мелкозернистой структуры. Одновременно при отжиге полностью снимаются остаточные напряжения.
Полуфабрикаты из конструкционных сталей после литья или горячего деформирования из-за ускоренного охлаждения с высоких температур могут иметь повышенную твердость, что затруднит их обработку резанием и приведет к понижению пластичности. Кроме того, отливки и горячедеформированнаи сталь часто приобретают структурные дефекты, ухудшающие юс свойства.
Характерный структурный дефект стальных отливок — крупнозернистость.
При ускоренном охлаждении крупнозернистого аустенита создаются условия для образования видманштеттовой структуры. При ее образовании выполняется принцип размерного и структурного соответствия, в результате чего кристаллы доэвтектоидного феррита ориентированно прорастают относительно кристаллической решетки аустенита и имеют форму пластин.
Размер зерна аустенита, образующегося после обработки давлением определяется температурой окончания обработки.
При обработке давлением включения вытягиваются. Феррит, зарождаясь на вытянутых включениях, образует вытянутые скопления. Строчечность структуры, вызванная неметаллическими включениями, не исправляется отжигом.
Горячекатаная сталь со строчечной структурой имеет худшие механические свойства (прочность, пластичность и вязкость) в поперечном и высотном направлениях по сравнению с основным направлением деформации.
Для полной перекристаллизации структуры конструкционные стал нагревают до температуры, превышающей температуру Ас3 на 30 - 50% При более высоком нагреве произойдет укрупнение аустенитных зерен. После сквозного прогрева изделия следует медленно охлаждать, чтобы обеспечить в результате распада аустенита равновесную ферритно-перлитную структуру и соответственно низкую твердость и высокую пластичность.
Скорость охлаждения при отжиге выбирают в зависимости от степени легированности стали. Углеродистые стали получаются достаточно мягкими при скорости охлаждения 100 — 200°С/ч. Легированные стал с более высокой устойчивостью переохлажденного аустенита нужно охлаждать медленнее — со скоростью 20 — 70 °С/ч. Высоколегированные стали экономичнее подвергать изотермическому отжигу, т.е. дать выдержку при температуре немного меньше Аr1,чтобы получить продукты распада аустенита с низкой твёрдотью.
2) Нормализации, как и перекристаллизационному отжигу, чаще всего подвергают конструкционные стали после горячей обработки давлением и фасонного литья. Нормализация отличается от отжига в основном условиями охлаждения; после нагрева до температуры на 50 — 70 °С выше Асз сталь охлаждают на спокойном воздухе.
Нормализация — более экономичная термическая операция, чем отжиг, так как меньше времени затрачивается на охлаждение стали. Кроме того, нормализация, обеспечивая полную перекристаллизацию структуры, приводит к получению более высокой прочности стали, так как при ускорении охлаждения распад аустенита происходит при более низких температурах.
Легированные конструкционные стали с повышенной устойчивостью переохлажденного аустенита после нормализации приобретают высокую твердость, затрудняющую последующую обработку резанием. В связи с этим после нормализации проводят отпуск при температурах, обеспечивающих получение требуемой твердости (650 — 750°С в зависимостям состава стали).
После нормализации углеродистых и низколегированных сталей, так же как и после отжига, образуется ферритно-перлитная структура, однако имеются и существенные структурные отличия .При ускоренном охлаждении, характерном для нормализации, доэвтектоидный феррит при прохождении температурного интервала Аr3-Ar1 выделяется на гра ницах зерен аустенита; поэтому кристаллы феррита образуют сплошные или разорванные оболочки вокруг зерен аустенита — ферритиую сетку.
Нормализация позволяет несколько уменьшить анизотропию свойств, вызванную наличием в горячедеформнрованной стали вытянутых неметаллических включений. При ускоренном охлаждении(по сравнению с отжигом) возникает больше самороизвольно образующихся центров кристаллизации,поэтому строчечность структуры менее резко выражена.
Чем меньше сечение, тем быстрее произойдёт охлаждение на спокойном воздухе и тем выше будет прочность стали.
3 вопрос. Усталость.

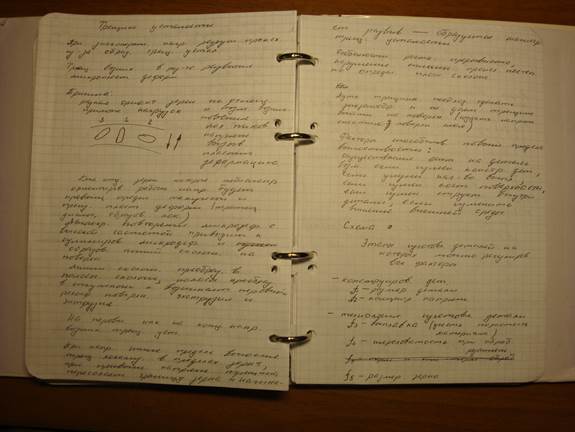
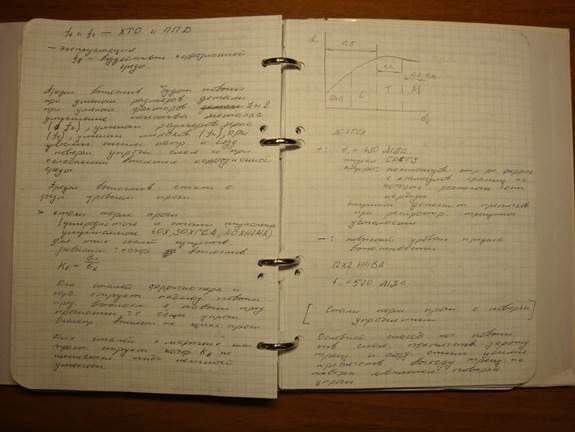
3 билет
1. Строение и свойства сложных фаз в сплавах: твёрдые растворы и промежуточные фазы. Примеры химических соединений, фаз внедрения, электронных соединений, фаз Лавеса.
1. Сплав – вещество, содержащее в своем составе два или более компонентов, по крайней мере один из которых – металл.
Фаза – пространственно ограниченная и отличная от других часть системы, имеющая свою кристаллическую решётку и свои свойства. Гомогенные вещества имеют одну фазу, а гетерогенные – несколько фаз.
Структура – строение металла, в котором можно различать отдельные фазы, их форму, размеры и взаимное расположение. Структура влияет на свойства.
Равновесное состояние – когда в сплаве все фазы, присущие этой системе оформлены. Это состояние обеспечивается при медленном охлаждении, можно различать размеры и формы фаз.
Неравновесное состояние – процесс образования и обособления фаз не закончился, образуется при быстром охлаждении.
Компонент – химическое вещество, входящее в состав сплава.
В дальнейшем будем рассматривать двойные сплавы.
Различные типы кристаллических сплавов.
1. Твердые растворы – фаза сплава, крист. решетка, которой не отличается от решетки металлоосновы, а концентрация легирующих компонентов изменяется в широких пределах.Твердые растворы классифицируются по 3 признакам:
1)по типу легирующего элемента : металл или металлоид(С,N,O)
2)по протяженности области существования на диаграммах состояния(ограниченная и неограниченная)
3)по степени регулярности расположения атома(неупорядочення и упорядоченая)
Выделяют твердые растворы внедрения и твердые растворы замещения.
В твердых растворах внедрения(легирующий компонент Ме) – атомы растворенного вещества находятся в межатомных промежутках растворителя.
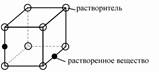
Особенности:
-растворенные вещества должны иметь малый атомный радиус (обычно это неметалл);
-ограниченная растворимость;
В твердых растворах замещения(легирующий компонент металлоид) – атомы растворенного вещества замещают атомы растворителя в узлах кристаллической решетки.
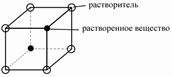
Особенности
-растворенное вещество такого же типа, как и растворитель (атомы близки по размеру);
-часто имеют неограниченную растворимость;
2.Промежуточные фазы – фазы,которые имеют кристаллическую решетку личную или отличающаяся от решеток составляющих ее компонентов .ПФ-это химические соединения, которые образованны компонентами сплава. ПФ отличается от ТР крист. решеткой и типом связи, поэтому ПФ имеют более высокую твердость, чем ТР. Реакция образования ПФ:
1) Ж-->ПФ - эвтектика
2) Ж-->[Ф+ПФ] – по эвтектической реакции
3)Ф -->[Ф+ПФ] – эвтектоидное превращение
ПФ различаются по хим. составу :
1)для общего обозначения соединения типа МеМе
2)типа Ме - металлоид: МеХ, где Х-С,N,О и т.д.
Химические соединения Ме+ :
1) Ме-интерметаллиды МеМе
2) Азот –нитриды : МеN
3) Углерод – карбиды : МеС
4) Кислород – оксиды : МеО
Интерметаллиды:
1) сплавы непереходных Ме
а)электронные соединения
б)Фазы Лавеса
2) сплавы переходных Ме
а) сигмафазы
б)гаммафазы типа Ni3Al
Примеры:
Электронное соединение-CuZn, FeAl, CoAl
Фаза Лавеса – МоFe, NbFe2
Вопрос 2 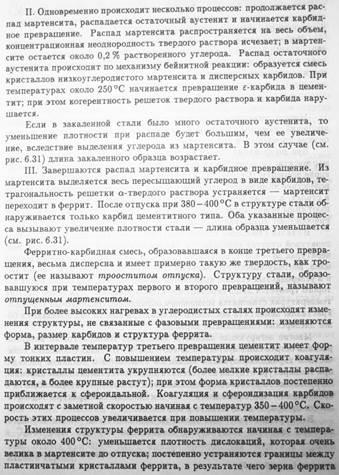
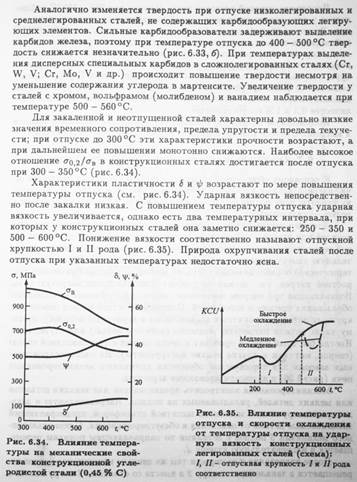
Отпуск – термическая обработка стали, заключающаяся в нагреве закаленной на мартенсит стали до температуры ниже критической, выдержки при этой температуре и охлаждении на воздухе.
Цель отпуска: Улучшение механических свойств закаленной стали, снижение хрупкости, повышение пластичности, некоторое снижение твердости и прочности.
вопрос 3
Легированной называется сталь, содержащая в своем составе один или несколько специально введенных легирующих элементов в количестве, заметно изменяющем свойства стали.
Принципы маркировки стали:
Марка легированной стали – буквенно-цифровой код ее химического состава. Каждый элемент обозначается заглавной буквой русского алфавита:
а) по одной из букв русского названия Н – Ni; В – W; Т – Ti; Х – Cr; М – Mo; Г – Mn; Д – Cu; Ю – Al; А – N; Б – Nb;
б) по первой букве латинского названия С – Si;
в) просто условное обозначение Ф – V;
Марка легированной стали: 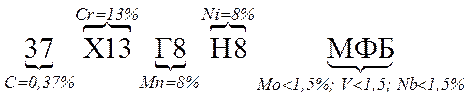
Если число соответствующее содержанию углерода двухзначное, то это содержание углерода в сотых долях процента, если в единицах, то это содержание углерода в десятых долях процента.
– низколегированные 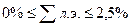
– среднелегированные 
– высоколегированные 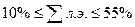
Влияние некоторых основных легирующих элементов на свойства сталей.
1. Никель. Никель образует твердые растворы внутри легированных сталей, повышается прочность стали, ее устойчивость к высоким температурам (никель – сильный аустенизатор).
2. Хром. Если содержание в стали хрома больше 12%, то сталь – нержавеющая (при условии растворения хрома в кристаллической решетке железа). Хром – сильно карбидообразующий элемент. Из-за образования карбидов коррозионная стойкость стали может уменьшаться. В стали 12Х18Н10Т предотвращено образование карбидов хрома на зернах.
3. Вольфрам. Вольфрам повышает твердость и прочность стали. Сильно карбидообразующий элемент. Карбиды вольфрама устойчивы и действуют при температуре выше температуры применения. Вольфрам используют для изготовления инструментальных сталей.
4. Ванадий. Ванадий повышает устойчивость к циклическим нагружениям и высоким температурам.
5. Марганец. Марганец способствует повышению твердости и прочности, обеспечивает высокую вязкость сталей.
6. Кремний. Кремний – ферритизатор – повышает устойчивость феррита при высоких температурах, то есть такая сталь обладает хорошими электро-магнитными свойствами (феррит – сильный ферромагнетик). Стали с высоким содержанием кремния используются для изготовления сердечников для электроприборов.
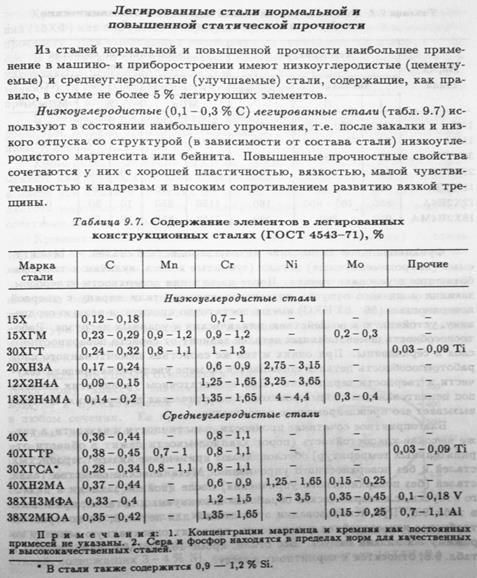
Билет № 4
1.Атомно-кристаллическая структура. Влияние типа связи на структуру и свойства. Анизотропия. Строение реальных кристаллов. Дефекты. Влияние структурных дефектов на свойства.
Кристаллическое тело характеризуется правильным расположением атомов в пространстве. У аморфных веществ расположение атомов случайно. Кристаллические вещества образуют кристаллическую решётку. 14 типов кристаллических решёток. Крист. решётка характеризуется элементарной ячейкой. Эл. ячейка – кристаллич. решётка наименьшего объёма, воспроизведение которой в пространстве множество раз создаёт пространственную крист. решётку. Атомы в пространстве располагаются упорядоченно, образуя кристаллическую решётку. Основные типы:
1. Простая кубическая решётка: в узлах кубика атомы касаются друг друга. Параметры: Период решётки (расстояние между атомами a =d), d – диаметр атома. 1/8·8 =1 атом на элемент, ячейку. Для химического соединения данный тип решётки.
2. Кубическая объёмно-центрированная решётка характерна для тугоплавких металлов. a =1,21·d. 1/8·8 +1 =2. Feα, Ti, W, Nb.
3. Кубическая гранецентрированная решётка . 1/8·8 +1/2·6 =4. Характерна для пластичных металлов. Cu, Feγ, Au.
Анизотропия
Анизотропия – это различие свойств в разных направлениях в кристалле. В монокристалле – анизотропия. Поликристаллические вещества – где много кристаллов. В поликристаллическом теле – изотропия (одинаковые свойства по разным направлениям).
Неоднородный химический состав и внешние условия вызывают дефекты кристаллической решетки. Выделяют дефекты трех типов:
1) точечные (вакансии, внедренные атомы);
2) линейные (краевые и винтовые дислокации);
3) объемные (микропоры, трещины, газовые пузырьки).
Точечные дефекты:
Вакансия – отсутствие атома в узле кристаллической решетки.
Внедренные атомы: а) чужеродный атом в узле кристаллической решетки; б) атом вне узла, в межузельном пространстве.
Линейные дефекты:
Дислокации: краевые – оборванный край атомной плоскости внутри кристаллической решетки; винтовые – условная ось внутри кристалл, относительно которой закручиваются атомные плоскости в процессе кристаллизации.
Объемные дефекты:
Возникают из-за влияния внешних условий кристаллизации или под действием внешних нагрузок. В результате несколько вакансий дают пору; несколько линейных дислокаций – трещину.
Влияние дислокаций на процесс деформирования кристалла.
Наличие дислокаций значительно облегчают движение атомных плоскостей друг относительно друга и способствует уменьшению предела прочности. В результате деформирования дислокации могут выходить за грани кристалла. Под действием значительных усилий в кристалле могут возникать новые дислокации, облегчающие деформирование кристалла (площадка текучести). Дислокации переплетаются.
n – плотность дислокаций;
| |
Если дислокаций нет, то требуется значительное усилие, чтобы деформировать материал. Чем больше дислокаций, тем меньше усилие необходимое для деформации образца. Начиная с некоторой концентрации дислокаций деформация затрудняется, дислокации мешают движению друг друга. Возникает эффект упрочнения. Структура, возникающая при большом количестве мешающих друг другу дислокаций.
Реальные кристаллы имеют много дефектов, от которых зависят свойства материала
Влияние типа связи.
1)Кристаллы, в которых вреобдадает молекулярная связь, возникающая между любыми частицами(ионами,атомами, молекулами), называют молекулярными. Для многих она мала по сравнению с другими, болле прочными связями.
В кристаллах инертных газов эта связь единственная, а следовательно, она определяет структуру и свойства кристаллов.
Атомы инертных газов жмеют полностью достроенные энергетические уровни, поэтому при сближении атомов обмен электронами невозможен Возникновение сил притяжения между атомами объясняют их взаимной поляризацией при сближении (рис. 1.9).
Силы Ван-дер-Ваальса между частицами не имеюь направленного характера, так как мгновенный диполь образуется с каждым из соседних атомов. В результате атомы, стремясь увеличяггь число соседей кристаллической решетке, укладываясь наиболее компактным образом( ГПК – типичная решётка)
Энергия связи сил Ван-тер-Ваадьса невелика, поэтому молекулярные
кристаллы имеют низкие температуры плавления и легко возгоняются. Молекулярные кристаллы — диэлектрики, так как кристалл построен из электрически нейтральных атомов (молекул), у которых энергетические
зоны полностъю достроены.
2)Кристаллы, в которых преобладает ковалентный тип связи, называютют ковалентными. Их образуют элементы 4,5,6 подгруппы В Периодической системы Д.И. Менделеева: углерод, кремний, германий, сурьма, висмут и др. При взаимодействии атомы обобществляют свои валентные электроны с соседними атомами, достраивая таким образом валентную зону. Ковалентная связь характеризуется направленностью. Вследствие этого атомы в ковалентных кристаллах укладываются некомпактно и образуют кристаллические структуры с небольшим координационным числом. Так. ГПК решетка алмаза имеет координационное число 4 (К4).Вследствие большой энергии связи ковалентные кристаллы характеризуются высокими температурами плавления.Образование заполненных валентных зон при такой связи превращает ковалентные кристаллы в полупроводники и даже диэлектрики. Температурный коэффициент электрического сопротивления у ковалентных кристаллов имеет отрицательное значение, т.е. при нагреве электрическое сопротивление снижается. К ковалентным кристаллам относятся многие сложные кристаллические вещества, состоящие из разнородных атомов, например карбид кремния, нитрид алюминия и др.
3) Это кристаллы, в которых преобладает металлический тки связи. Их образуют элементы всех подгрупп А и I — Ш подгрупп В Периодической системы элементов. В металлическом кристалле при взаимодейства с элементами других групп атомы легко отдают свои валентные электроны и превращаются в положительные ионы.
При взаимодействии валентные энергетические зоны атомов перекрываются, образуя общую зону со свободными подуровнями. Это дает возможность валентным электронам свободно перемещаться в пределах этой зоны.
2.Причины возникновения остаточных напряжений при закалке. Различные виды закалки.
Конструкционные стали подвергают закалке и отпуску для повышения прочности и твердости, получения высокой пластичности, вязкости и высокой износостойкости, а инструментальные – для повышения твердости и износостойкости.
Основными параметрами являются температура нагрева и скорость охлаждения. Продолжительность нагрева зависит от нагревательного устройства, по опытным данным на 1 мм сечения затрачивается: в электрической печи – 1,5…2 мин.; в пламенной печи – 1 мин.; в соляной ванне – 0,5 мин.; в свинцовой ванне – 0,1…0,15 мин.
По температуре нагрева различают виды закалки:
– полная, с температурой нагрева на 30…50oС выше критической температуры А3
.
Применяют ее для доэвтектоидных сталей. Изменения структуры стали при нагреве и охлаждении происходят по схеме:
.
Неполная закалка доэвтектоидных сталей недопустима, так как в структуре остается мягкий феррит. Изменения структуры стали при нагреве и охлаждении происходят по схеме:

– неполная с температурой нагрева на 30…50 oС выше критической температуры А1

Применяется для заэвтектоидных сталей. Изменения структуры стали при нагреве и охлаждении происходят по схеме:
.
После полной закалки заэвтектоидных сталей получают дефектную структуру грубоигольчатого мартенсита.
Заэвтектоидные стали перед закалкой обязательно подвергают отжигу – сфероидизации, чтобы цементит имел зернистую форму.
Охлаждение при закалке.
Для получения требуемой структуры изделия охлаждают с различной скоростью, которая в большой степени определяется охлаждающей средой, формой изделия и теплопроводностью стали.
Режим охлаждения должен исключить возникновение больших закалочных напряжений. При высоких скоростях охлаждения при закалке возникают внутренние напряжения, которые могут привести к короблению и растрескиванию.
3.Серые, высокопрочные, ковкие чугуны. Особенности их получения. Классификация чугунов по структуре металлической основы, их свойства. Принцип маркировки. Применение.
Из рассмотрения структур чугунов можно заключить, что их металлическая основа похожа на структуру эвтектоидной или доэвтектоидной стали или технического железа. Отличаются от стали только наличием графитовых включений, определяющих специальные свойства чугунов.
В зависимости от формы графита и условий его образования различают следующие группы чугунов: серый – с пластинчатым графитом; высокопрочный – с шаровидным графитом; ковкий – с хлопьевидным графитом.
Наиболее широкое распространение получили чугуны с содержанием углерода 2,4…3,8%. Чем выше содержание углерода, тем больше образуется графита и тем ниже его механические свойства, следовательно, количество углерода не должно превышать 3,8 %. В то же время для обеспечения высоких литейных свойств (хорошей жидкотекучести) углерода должно быть не менее 2,4 %.
Влияние состава чугуна на процесс графитизации.
Углерод и кремний способствуют графитизации, марганец затрудняет графитизацию и способствует отбеливанию чугуна. Сера способствует отбеливанию чугуна и ухудшает литейные свойства, ее содержание ограничено – 0,08…0,12 %. Фосфор на процесс графитизации не влияет, но улучшает жидкотекучесть, Фосфор является в чугунах полезной примесью, его содержание – 0,3…0,8 %.
Влияние графита на механические свойства отливок.
Графитовые включения можно рассматривать как соответствующей формы пустоты в структуре чугуна. Около таких дефектов при нагружении концентрируются напряжения, значение которых тем больше, чем острее дефект. Отсюда следует, что графитовые включения пластинчатой формы в максимальной мере разупрочняют металл. Более благоприятна хлопьевидная форма, а оптимальной является шаровидная форма графита. Пластичность зависит от формы таким же образом. Относительное удлинение ( ) дпя серых чугунов составляет 0,5 %, для ковких – до 10 %, для высокопрочных – до 15%.
Наличие графита наиболее резко снижает сопротивление при жестких способах нагружения: удар; разрыв. Сопротивление сжатию снижается мало.
Положительные стороны наличия графита.
· графит улучшает обрабатываемость резанием, так как образуется ломкая стружка;
· чугун имеет лучшие антифрикционные свойства, по сравнению со сталью, так как наличие графита обеспечивает дополнительную смазку поверхностей трения;
· из-за микропустот, заполненных графитом, чугун хорошо гасит вибрации и имеет повышенную циклическую вязкость;
· детали из чугуна не чувствительны к внешним концентраторам напряжений (выточки, отверстия, переходы в сечениях);
· чугун значительно дешевле стали;
· производство изделий из чугуна литьем дешевле изготовления изделий из стальных заготовок обработкой резанием, а также литьем и обработкой давлением с последующей механической обработкой.
Серый чугун.
Структура не оказывает влияние на пластичность, она остается чрезвычайно низкой. Но оказывает влияние на твердость. Механическая прочность в основном определяется количеством, формой и размерами включений графита. Мелкие, завихренной формы чешуйки графита меньше снижают прочность. Такая форма достигается путем модифицирования. В качестве модификаторов применяют алюминий, силикокальций, ферросилиций.
Серый чугун широко применяется в машиностроении, так как легко обрабатывается и обладает хорошими свойствами.
В зависимости от прочности серый чугун подразделяют на 10 марок (ГОСТ 1412).
Серые чугуны при малом сопротивлении растяжению имеют достаточно высокое сопротивление сжатию.
Серые чугуны содержат углерода – 3,2…3,5 %; кремния – 1,9…2,5 %; марганца –0,5…0,8 %; фосфора – 0,1…0,3 %; серы – < 0,12 %.
Структура металлической основы зависит от количества углерода и кремния. С увеличением содержания углерода и кремния увеличивается степень графитизации и склонность к образованию ферритвой структуры металлической основы. Это ведет к разупрочнению чугуна без повышения пластичности. Лучшими прочностными свойствами и износостойкостью обладают перлитные серые чугуны.
Учитывая малое сопротивление отливок из серого чугуна растягивающим и ударным нагрузкам, следует использовать этот материал для деталей, которые подвергаются сжимающим или изгибающим нагрузкам. В станкостроении это – базовые, корпусные детали, кронштейны, зубчатые колеса, направляющие; в автостроении - блоки цилиндров, поршневые кольца, распределительные валы, диски сцепления. Отливки из серого чугуна также используются в электромашиностроении, для изготовления товаров народного потребления.
Обозначаются индексом СЧ (серый чугун) и числом, которое показывает значение предела прочности, умноженное на СЧ 15.
Высокопрочный чугун с шаровидным графитом.
Высокопрочные чугуны (ГОСТ 7293) могут иметь ферритную (ВЧ 35), феррито-перлитную (ВЧ45) и перлитную (ВЧ 80) металлическую основу. Получают эти чугуны из серых, в результате модифицирования магнием или церием (добавляется 0,03…0,07% от массы отливки). По сравнению с серыми чугунами, механические свойства повышаются, это вызвано отсутствием неравномерности в распределении напряжений из-за шаровидной формы графита.
Чугуны с перлитной металлической основой имеют высокие показатели прочности при меньшем значении пластичности. Соотношение пластичности и прочности ферритных чугунов - обратное.
Высокопрочные чугуны содержат: углерода – 3,2…3,8 %, кремния – 1,9…2,6 %, марганца – 0,6…0,8 %, фосфора – до 0,12 %, серы – до 0,3 %.
Эти чугуны обладают высокой жидкотекучестью, линейная усадка – около 1%. Литейные напряжения в отливках несколько выше, чем для серого чугуна. Из-за высокого модуля упругости достаточно высокая обрабатываемость резанием. Обладают удовлетворительной свариваемостью.
Из высокопрочного чугуна изготовляют тонкостенные отливки (поршневые кольца), шаботы ковочных молотов, станины и рамы прессов и прокатных станов, изложницы, резцедержатели, планшайбы.
Отливки коленчатых валов массой до 2..3 т, взамен кованых валов из стали, обладают более высокой циклической вязкостью, малочувствительны к внешним концентраторам напряжения, обладают лучшими антифрикционными свойствами и значительно дешевле.
Обозначаются индексом ВЧ (высокопрочный чугун) и числом, которое показывает значение предела прочности, умноженное на ВЧ 100.
Ковкий чугун
Получают отжигом белого доэвтектического чугуна.
Хорошие свойства у отливок обеспечиваются, если в процессе кристаллизации и охлаждения отливок в форме не происходит процесс графитизации. Чтобы предотвратить графитизацию, чугуны должны иметь пониженное содержание углерода и кремния.
Ковкие чугуны содержат: углерода – 2,4…3,0 %, кремния – 0,8…1,4 %, марганца – 0,3…1,0 %, фосфора – до 0,2 %, серы – до 0,1 %.
Формирование окончательной структуры и свойств отливок происходит в процессе отжига, схема которого представлена на рис. 11.4.
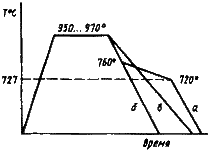
Рис. 11.4. Отжиг ковкого чугуна.
Отливки выдерживаются в печи при температуре 950…1000 С в течении 15…20 часов. Происходит разложение цементита: .
Структура после выдержки состоит из аустенита и графита (углерод отжига).При медленном охлаждении в интервале 760…720oС, происходит разложение цементита, входящего в состав перлита, и структура после отжига состоит из феррита и углерода отжига (получается ферритный ковкий чугун).
При относительно быстром охлаждении (режим б, рис. 11.3) вторая стадия полностью устраняется, и получается перлитный ковкий чугун.
Структура чугуна, отожженного по режиму в, состоит из перлита, феррита и графита отжига (получается феррито-перлитный ковкий чугун)
Отжиг является длительной 70…80 часов и дорогостоящей операцией. В последнее время, в результате усовершенствований, длительность сократилась до 40 часов.
Различают 7 марок ковкого чугуна: три с ферритной (КЧ 30 – 6) и четыре с перлитной (КЧ 65 – 3) основой (ГОСТ 1215).
По механическим и технологическим свойствам ковкий чугун занимает промежуточное положение между серым чугуном и сталью. Недостатком ковкого чугуна по сравнению с высокопрочным является ограничение толщины стенок для отливки и необходимость отжига.
Отливки из ковкого чугуна применяют для деталей, работающих при ударных и вибрационных нагрузках.
Из ферритных чугунов изготавливают картеры редукторов, ступицы, крюки, скобы, хомутики, муфты, фланцы.
Из перлитных чугунов, характеризующихся высокой прочностью, достаточной пластичностью, изготавливают вилки карданных валов, звенья и ролики цепей конвейера, тормозные колодки.
Обозначаются индексом КЧ (высокопрочный чугун) и двумя числми, первое из которых показывает значение предела прочности, умноженное на , а второе – относительное удлинение - КЧ 30 - 6.
Билет
Не нашли, что искали? Воспользуйтесь поиском по сайту:
©2015 - 2025 stydopedia.ru Все материалы защищены законодательством РФ.
|