Жаропрочность. Критерии оценки. Способы повышения. Жаропрочные стали перлитного, аустенитного и мартенситного класса.
Жаропрочностью называется способность материала длительное время сопротивляться деформированию и разрушению, когда рабочие температуры деталей превышают 0,3tПл.
Решающее значение при выборе материала имеют температура, длительность работы под нагрузкой и действующие напряжения.
Нагрев ослабляет межатомные связи, при высоких температурах уменьшаются модули упругости, временное сопротивление, предел текучести, твердость. Чем ниже tПл основы сплава, тем ниже оказываются его допустимые рабочие температуры (рис. 15.6).
При длительном нагружении при высоких температурах поведение материала определяется диффузионными процессами. Для этих условий характерны процессы ползучести и релаксация напряжений.
Ползучесть - медленное нарастание пластической деформации под действием напряжений, меньших предела текучести. Типичная зависимость деформации от времени нагружения представлена на рис. 15.7.
Кривая ползучести состоит из трех участков. Стадия I так называемой неустановившейся ползучести отличается постепенным затуханием скорости деформации до определенного постоянного значения. Стадия II - установившейся ползучести - характеризуется постоянной скоростью деформации. На стадии III - стадии разрушения - скорость деформации нарастает до момента разрушения. Как правило, она непродолжительна и для деталей недопустима, так как в этом случае неминуемо быстрое разрушение.
Относительное развитие каждой стадия зависит от температуры и напряжения. При одном и том же напряжении повышение температуры испытания сокращает продолжительность стадии 2 и ускоряет разрушение (рис. 15.8, а). Аналогично влияет повышение напряжения при неизменной температуре испытания (рис. 15.8,6)-
Критериями жаропрочности являются: предел ползучести, предел длительной прочности, сопротивление релаксации.
Предел ползучести - напряжение, под действием которого материал деформируется на определенную величину за определенное время при заданной температуре. В обозначении предела ползучести указывают температуру, деформацию и время, за которое она возникает.
Ползучесть металлов вызывает релаксацию напряжений в предварительно нагруженных деталях. Критерием сопротивления релаксации является падение напряжения за время τ при заданной температуре.
Большинство жаропрочных материалов поликристаллические. Деформация ползучести в таких материалах развивается благодаря перемещению дислокаций в зернах, эериограничному скольжению и диффузионному переносу.
Для обеспечения жаропрочности требуется ограничить подвижность дислокаций и замедлить диффузию. Это достигается повышением прочности межатомных связей, созданием препятствий для перемещения дислокаций внутри зерен и на их границах, увеличением размеров зерен.
Прочность межатомной связи увеличивают легированием, Изменением типа кристаллической решетки, переходом от металлической связи к более прочной ковалеятной.
Наиболее целесообразным является легирование твердого раствора более тугоплавкими металлами, чем металл-основа этого раствора.
Подвижность дислокаций существенно снижается в многофазной структуре с мелкими частицами упрочняющих фаз. Материалы с многофазной структурой, получаемой термической обработкой, называются дисперсионно-упрочненными.
Эффективность упрочнения определяется свойствами частиц и их распределением. Чем они мельче и чем ближе находятся друг от друга, тем выше жаропрочность.
Многофазная структура с мелкими частицами упрочняющих фаз в сталях получается при помощи закалки и отпуска, а во многих жаропрочных сплавах — после закалки и старения. Упрочняющими фазами служат карбиды и карбонитриды в жаропрочных сталях, γ-фаза с ГЦК решеткой в никелевых сплавах, фазы Лавеса.
Материалы с упрочняющими частицами, инертными по отношению к металлической основе, называются дисперсно-упрочненными. Преимуществом дисперсно-упрочненных материалов является устойчивость структуры при продолжительном нагреве. Частицы этого порошка имеют однородную структуру с равномерным распределением тонких оксидных частиц.
Способы уменьшения зернограничного скольжения: создание крупнозернистой структуры, образование дисперсных частиц вторых фаз на границах зерен, нейтрализация вредных легкоплавких примесей на границах зерен.
Крупнозернистость — характерная особенность структуры жаропрочных материалов. Чем крупнее зерна, тем меньше протяженность межзеренных границ и слабее зернограничное скольжение и диффузионный перенос. Идеальными в этом отношении являются монокристаллы, у которых совсем нет границ зерен. Для упрочнения границ зерен в жаропрочные стали и сплавы вводят малые добавки (ОД - 0,01 %) легирующих элементов, которые концентрируются на границах. Эти элементы замедляют зернограничное скольжение и нейтрализуют действие вредных примесей. Особенно часто используют бор, церий и другие редкоземельные металлы. Границы зерен в никелевых жаропрочных сплавах упрочняют карбидами, добавляя с этой целью в сплавы около О.1 % С.
К дополнительным мерам повышения жаропрочности относят: термомеханическую обработку для получения структуры полигонизации; упорядочение твердого раствора металла-основы н создание анизотропной структуры.
Полигонизация повышает сопротивление ползучести, так как малоугловые границы в зернах мешают передвижению дислокаций. Однако такая обработка эффективна лишь в изделиях простой формы (например, в трубах), когда деформация во всем изделии одинакова.
Применение упорядочения ограничено, не всякий твердый раствор упорядочивается.
Анизотропную структуру в изделиях из жаропрочных сплавов получают направленной кристаллизацией или теми же способами, какими получают КМ.
Классификация жаропрочных сталей и сплавов
В качестве современных жаропрочных материалов можно отметить перлитные, мартенситные и аустенитные жаропрочные стали, никелевые и кобальтоавые жаропрочные сплавы, тугоплавкие металлы.
При температурах до 300oC обычные конструкционные стали имеют высокую прочность, нет необходимости использовать высоколегированные стали.
Для работы в интервале температур 350…500oC применяют легированные стали перлитного, ферритного и мартенситного классов.
Перлитные жаропрочные стали. К этой группе относятся котельные стали и сильхромы. Эти стали применяются для изготовления деталей котельных агрегатов, паровых турбин, двигателей внутреннего сгорания. Стали содержат относительно мало углерода. Легирование сталей хромом, молибденом и ванадием производится для повышения температуры рекристаллизации (марки 12Х1МФ, 20Х3МФ). Используются в закаленном и высокоотпущенном состоянии. Иногда закалку заменяют нормализацией. В результате этого образуются пластинчатые продукты превращения аустенита, которые обеспечивают более высокую жаропрочность. Предел ползучести этих сталей должен обеспечить остаточную деформацию в пределах 1 % за время 10000…100000 ч работы.
Перлитные стали обладают удовлетворительной свариваемостью, поэтому используются для сварных конструкций (например, трубы пароперегревателей).
Для деталей газовых турбин применяют сложнолегированные стали мартенситного класса 12Х2МФСР, 12Х2МФБ, 15Х12ВНМФ. Увеличение содержания хрома повышает жаростойкость сталей. Хром, вольфрам, молибден и ванадий повышают температуру рекристаллизации, образуются карбиды, повышающие прочность после термической обработки. Термическая обработка состоит из закалки от температур выше 1000oС в масле или на воздухе и высокого отпуска при температурах выше температуры эксплуатации.
Для изготовления жаропрочных деталей, не требующих сварки (клапаны двигателей внутреннего сгорания), применяются хромокремнистые стали – сильхромы: 40Х10С2М, 40Х9С2, Х6С.
Жаролрочные свойства растут с увеличением степени легированности. Сильхромы подвергаются закалке от температуры около 1000oС и отпуску при температуре 720…780oС.
При рабочих температурах 500…700oC применяются стали аустенитного класса. Из этих сталей изготавливают клапаны двигателей, лопатки газовых турбин,сопловые аппараты реактивных двигателей и т.д.
Основными жаропрочными аустенитными сталями являются хромоникелевые стали, дополнительно легированные вольфрамом, молибденом, ванадием и другими элементами. Стали содержат 15…20 % хрома и 10…20 % никеля. Обладают жаропрочностью и жаростойкостью, пластичны, хорошо свариваются, но затруднена обработка резанием и давлением, охрупчиваются в интервале температур около 600oС, из-за выделения по границам различных фаз.
Билет № 2.
1. Диаграмма состояния для сплавов с переменной растворимостью.
Диаграмма состояния представлена на рис. 5.7.
По внешнему виду диаграмма похожа на диаграмму состояния сплавов с ограниченной растворимостью компонентов в твердом состоянии. Отличие в том, что линии предельной растворимости компонентов не перпендикулярны оси концентрации. Появляются области, в которых из однородных твердых растворов при понижении температуры выделяются вторичные фазы.
На диаграмме:
df – линия переменной предельной растворимости компонента В в компоненте А;
ek – линия переменной предельной растворимости компонента А в компоненте В.
Кривая охлаждения сплава I представлена на рис. 5.7 б.
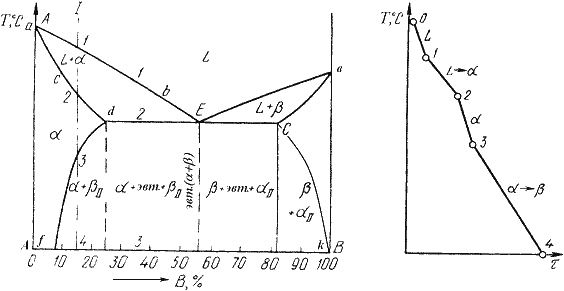
Рис. 5.7. Диаграмма состояния сплавов, испытывающих фазовые превращения в твердом состоянии (а) и кривая охлаждения сплава (б)
Процесс кристаллизации сплава I: до точки 1 охлаждается сплав в жидком состоянии. При температуре, соответствующей точке 1, начинают образовываться центры кристаллизации твердого раствора . На участке 1–2 идет процесс кристаллизации, протекающий при понижающейся температуре. При достижении температуры соответствующей точке 2, сплав затвердевает, при дальнейшем понижении температуры охлаждается сплав в твердом состоянии, состоящий из однородных кристаллов твердого раствора . При достижении температуры, соответствующей точке 3, твердый раствор оказывается насыщенным компонентом В, при более низких температурах растворимость второго компонента уменьшается, поэтому из -раствора начинает выделяться избыточный компонент в виде кристаллов . За точкой 3 сплав состоит из двух фаз: кристаллов твердого раствора и вторичных кристаллов твердого раствора .
Не нашли, что искали? Воспользуйтесь поиском по сайту:
©2015 - 2025 stydopedia.ru Все материалы защищены законодательством РФ.
|