Технология изготовления дисков
автомобиль диск колесо кованный
Кованые диски изготовленные методом горячей объемной штамповки в закрытых матрицах (горячая объемная штамповка это технологическая операция при которой заготовка деформируется в специальном инструменте — штампе).
Для дисков используется сплав типа АВ на основе алюминия с легирующими добавками магния, меди, кремния и марганца. Он не только высокопрочен, но и пластичен. За рубежом аналог этого сплава обычно называют «авиационный алюминий 6061» (aircraft grade Al 6061). Готовую отливку — цилиндр диаметром примерно 20 см — режут на куски нужной длины (в зависимости от размера будущих колес) и отправляют в кузнечно-прессовый цех. Там эти заготовки, пока даже отдаленно не напоминающие колесные диски, разогревают и с помощью пресса «осаживают» — сплющивают, превращая в заготовки толщиной сантиметров двадцать и диаметром около полуметра. Процесс дальнейшего превращения в колеса происходит в несколько этапов. Сначала заготовки разогревают до 430°C и с помощью предварительного штампа (разогретого примерно до 350°C) предают нужную форму — предварительные заготовки для автомобильных колес. Загатовки вновь отправляются в печь для разогрева, а затем специальный конвейер подает их к прессу с другим установленным штампом — окончательным. Пауза между выходом заготовки из печи и собственно штамповкой не должна быть больше 11 секунд, иначе заготовка остынет ниже критической температуры. Разогретый штамп смазывают специальной смазкой, заготовку переносят на пресс-форму. Верхняя часть пресса опускается, поднимается и вот из-под пресса достают готовое, если не считать облоя (излишков материала, выдавленных при штамповке), диск. Первые четыре отштампованных диска после освоения нового штампа идут на контроль геометрии — только после этого дается разрешение на использование штампа для серийного производства дисков.
При производстве колёс используются гидравлические вертикальные прессы усилием 4,7, 10, 30.тонн. На фотографиях один из рабочих с помощью кисти смазывает штамповую оснастку специальной смазкой, чтобы готовая деталь не прилипала к пресс-форме. Секторный штамп (справа). При горячей объемной штамповке используются вот такие штампы, состоящие из нескольких секторов. При окончательном формировании диска верхняя часть штампа опускается, и сектора сходятся. Излишки металла при этом выдавливаются через щели, образуя облой.
Несмотря на уже проступившее внешнее сходство, механические свойства колес пока еще далеки от тех чудных качеств, которыми славится горячая объемная штамповка. А славится она высокой прочностью (превышает прочность литых дисков при существенно меньшей массе), пластичностью (в отличие от литых дисков, кованые при высоких нагрузках деформируются, а не разрушаются) и упругостью (при умеренных нагрузках они деформируются упруго). Для получения всего этого как раз и нужна термообработка. Сначала колеса подвергают закалке — равномерно прогревают в течение нескольких часов в печи до 515°C, а затем быстро охлаждают, погружая в воду. После закалки сплав уже имеет нужную мелкозернисто-волокнистую структуру, но для того, чтобы колеса приобрели нужные механические свойства, их нужно «состарить» — подождать, пока структура выровняется, и убрать внутренние механические напряжения. В обычных условиях на это может уйти пара месяцев, но, чтобы не терять время, заготовки искусственно состаривают: выдерживают в печи при температуре 150 — 160°C примерно 12 — 14 часов, после чего медленно охлаждают.
После термообработки не менее 10 % заготовок из каждой партии подвергаются контролю. Их поверхность протравливают: на светлой травленой поверхности хорошо заметны дефекты штамповки и складки. А один диск из партии распиливают, вырезая из него специальный фрагмент — так называемый шаблон. Шаблон шлифуют и протравливают, а затем тщательно изучают в лаборатории на наличие дефектов деформации, термообработки и однородности сплава. Чаще всего дефекты встречаются в ступичной части, там наиболее сложный с металлургической точки зрения характер деформаций и термических нагрузок. На этом этапе также проводится контроль механических свойств сплава — образцы закрепляются в специальной разрывной машине, с помощью которой определяется предел прочности, предел текучести, относительное удлинение и твердость. Если дефекты и значения характеристик материала не укладываются в допуски, изучению подвергается еще один диск из партии. Если же и повторная проверка подтверждает эти выводы, значит, имело место нарушение технологической цепочки — и вся партия бракуется. Если же все параметры в норме — партия колес уходит на механическую обработку.
Виды повреждений
Диски являются важной деталью автомобиля, непосредственно воспринимая удары и тряску, возникающие от неровности дороги. Современные литые и штампованные диски могут иметь высокую цену и при повреждении выгоднее их починить, чем покупать новые. Основные повреждения колесных дисков могут возникать по четырем причинам:
— воздействие ударов. Сильный удар, например, при наезде на бордюр или при проваливании колеса в выемку, могут деформировать диск или привести к локальному разрушению. На рисунке 3.5 изображен диск поврежденный в следствии удара;

Рисунок 3.5 — Повреждение в следствии удара
— повреждения при замене диска. Возникают при небрежной или неуме-лой смене пробитой шины, от воздействия бортировки, кувалды или другого инструмента;
— воздействие грязи, пыли, воды. Диск подвержен абразивному воздействию загрязняющих веществ из-за своего расположения, что через некоторое время приводит к потере внешнего вида, локальному повреждению окраски, возникновению очагов коррозии.
Восстановление дисков
3.6.1 Аргонно-дуговая сварка дисков
Аргонно-дуговая сварка, применяется при соединении цветных металлов и легированных сталей. При сварке высоколегированных сталей в инертном газе обеспечивается минимальный угар легирующих элементов. Для этого также применяется присадочная проволока того же состава, что и металл изделия. Режим сварочного процесса легированных сталей различных толщин подбирают опытным путём. На рисунке 3.6 изображен метод восстановления диска аргонно-дуговой сваркой.
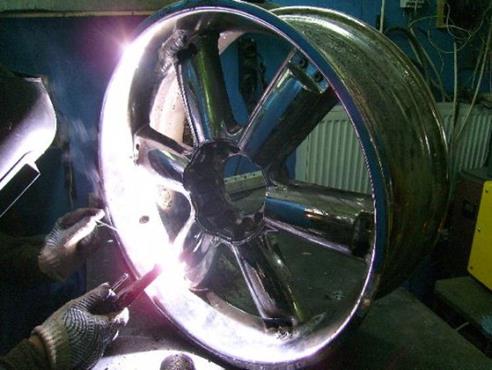
Рисунок 3.6 — Аргонно-дуговая сварка диска
Тщательная подготовка поверхности алюминиевых деталей к сварке — залог высокого качества сварной конструкции.
Легирование алюминия увеличивает в первую очередь его прочность. Алюминий легируют в основном магнием, марганцем, медью, кремнием, цинком. Алюминиевые сплавы классифицируют по технологии изготовления (деформируемые и литейные), а также по способности к термической обработке (неупрочняемые и упрочняемые термической обработкой). Сварные конструкции изготавливают из деформируемых сплавов, сведения о которых приведены в ГОСТ4784-74. Важнейшим показателем свариваемости алюминиевых сплавов является способность не образовывать при сварке «горячих трещин». Сплавы, крайне чувствительные к горячему трещинообразованию, считаются несвариваемыми. Применение их в сварных конструкциях не рекомендуется. Сплавы, не упрочняемые термической обработкой, имеют низкий уровень легирования. Механическая их прочность относительно невысока, но они хорошо свариваются и являются коррозионно-стойкими. Это сплавы алюминий-марганец (отечественное обозначение АМц), алюминий-магний (АМг); к ним же можно отнести и технический алюминий. Заготовки из этих сплавов выпускаются в отожженном и холоднодеформированном (нагартованном) состоянии. Сплавы, упрочняемые термической обработкой (закалка с последующим старением), имеют обычно более высокую степень легирования. Прочность их выше, но они хуже свариваются (некоторые совсем не свариваются) и часто имеют низкую коррозионную стойкость. Это сплавы алюминий-магний-кремний (авиали, отечественное обозначение АД), алюминий-медь (большинство относятся к дюралюминам, отечественное обозначение Д), алюминий-цинк (с добавками других элементов).
Авиали свариваются хорошо, однако с использованием присадочного материала; сваривать их сплавлением кромок не рекомендуется.
Дюралюмины относятся к несвариваемым сплавам. Единственный свариваемый алюминиево-медный сплав (сплав 1201) и его зарубежные аналоги.
Тройные сплавы алюминия с цинком и магнием свариваются хорошо только в том случае, если содержание этих легируемых элементов в сумме не превышает 7 — 7,5 %. К свариваемым относится отечественный сплав 1915 и его зарубежные аналоги.
Применительно к литейным сплавам сварка применяется только в ремонтных целях, а также для исправления дефектов литья. Из всех литейных сплавов наибольшее распространение получили сплавы алюминия с кремнием (силумины). Практически все они свариваются хорошо.
Для ручной дуговой сварки технического алюминия применяются отечественные электроды ОЗА-1 и ОЗАНА-1, а для заварки дефектов литья в силуминах ОЗА-2 и ОЗАНА-2. В этих электродах в обмазке находятся хлоридные и фторидные соли, разрушающие оксидную пленку и способствующие устойчивому горению дуги. В других видах сварки алюминия и его сплавов (аргонно-дуговом и полуавтоматическом) для предотвращения окисления используется защитный газ аргон или его смесь с гелием. Гелий повышает температуру дуги и увеличивает проплавление. Для аргоно-дуговой сварки,используются вольфрамовые электроды. Для сварки алюминия используются электроды большего диаметра, чем для сварки стали. Присадочным материалом чаще всего служит сварочная проволока. Отечественная сварочная проволока в соответствии с ГОСТ 7871-75 состоит из:
— чистого технического алюминия (СвА99, СвА97, СвА85Т, СвА5);
— сплава алюминий-марганец (СвАМц);
— сплавов алюминия с магнием (СвАМг3, СвАМг5, Св1557, СвАМг6, СвАМг63, СвАМг61);
— сплавов алюминия с кремнием (СвАК5, СвАК10);
— сплава алюминия с медью (Св1201).
Кроме того, по ТУ выпускают проволоку 1437 (алюминий, легированный хромом) и АВч (сплав алюминия с кремнием и магнием). За рубежом наиболее широко используется проволока марки 4043 (отечественный аналог СвАК5).
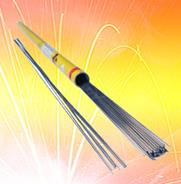
Рисунок 3.7 — Проволока марки СвАК5
Общим правилом при сварке алюминиевых сплавов является то, что металл сварочной проволоки должен примерно соответствовать по химическому составу металлу детали. Исключением являются сплавы алюминия с магнием, для сварки которых (из-за интенсивного испарения магния) следует использовать проволоку с содержанием магния большим, чем в детали.
Рассмотрим широко применяемую проволоку СвАК5. Она предназначена для сварки авиалей, а также для ремонта и исправления дефектов отливок из низколегированного силумина. Металл проволоки имеет относительно низкую температуру плавления, хорошую жидкотекучесть. По сравнению с проволоками из алюминиево-магниевых сплавов она при сварке дает меньше дыма и поэтому облегчает визуальное наблюдение за сварочной ванной. Следует иметь в виду, что сварной шов этой проволоки имеет низкую пластичность.
Другая часто применяемая проволока СвАМг5. Она предназначена в первую очередь для сварки алюминиево-магниевых сплавов, авиалей, а также для сваривающихся тройных сплавов алюминий-цинк-магний. Ограничением в ее применении является то, что сварной шов не должен при эксплуатации подвергаться действию температур, превышающих 80°C.
Не нашли, что искали? Воспользуйтесь поиском по сайту:
©2015 - 2025 stydopedia.ru Все материалы защищены законодательством РФ.
|