Общие понятия процесса волочения
Сущность процесса волочения заключается в протаскивании обрабатываемой заготовки через отверстие, размеры которого меньше размеров сечения исходной заготовки (рис. 123, а). При волочении площадь поперечного сечения заготовки уменьшается, приобретая постоянное сечение по всей длине, а длина увеличивается. Отношение полученной длины lк первоначальной l0называется вытяжкой.
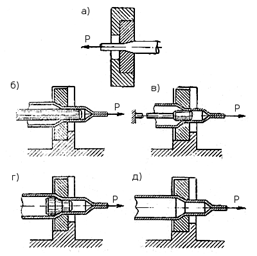
Рис. 123. Схема волочения: а — прутка; б — трубы на длинной оправке; в — трубы на несмещающейся оправке; г — трубы на плавающей оправке; д — трубы без оправки
Коэффициент вытяжки μ = l / l0 = F0 / F, величина которого в первых и последних проходах составляет 1,15 ÷ 1,25, при промежуточном волочении допускают 1,30 ÷ 1,45, а обжатие (обжатие определяется формулой φ = F0 — F / F0ּ100%, где F0 — исходное сечение, F — полученное сечение. При калибровке оно бывает 8—12%.) до 30—35%. При волочении труб на длинной оправке (рис. 123, б) коэффициент вытяжки можно довести до 1,8.
Усилие Р, потребное при волочении, называется усилием волочения. ОтношениеР к площади поперечного сечения, получаемого после волочения, называется напряжением волочения, которое должно быть меньше предела текучести обрабатываемого металла, иначе выходящий из отверстия волоки пруток будет утрачивать форму и размеры, полученные в отверстии волоки.
Волочение осуществляется в холодном состоянии, поэтому оно вызывает физическое упрочнение (наклеп) металла. Для восстановления первоначальных свойств применяют термообработку (отжиг), которая необходима при волочении в несколько переходов, а также в окончательной продукции.
Волочильный инструмент изготовляют из инструментальной стали, твердых сплавов, а для получения проволоки размером меньше 0,5 мм иногда применяют волоки из естественного алмаза.
Основная часть волоки называется волочильным глазком, или матрицей, и представляет собой рабочее отверстие постепенно уменьшающегося сечения, через которое протягивается металл. Волока с одним отверстием называется фильером, с несколькими — волочильной доской.
Для уменьшения трения при волочении применяют обильную смазку, различные предварительные покрытия, например, омеднение, которое снижает коэффициент трения, а следовательно, и усилие волочения, а также предохраняет поверхность от задира волочильным инструментом; для снижения усилия волочения применяют также роликовую матрицу (рис. 124, а).
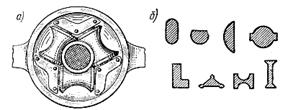
Рис. 124. Роликовая матрица и фасонные профили.
Передний конец исходной заготовкиперед волочением вытягивается (заостряется) с тем, чтобы он прошел через отверстие полоки и его можно было захватить тянущим устройством. Для волочения применяют декапированный металл — отожженный и протравленный.
Обычно волочение применяют при изготовлении проволоки размером меньше 5 мм; при получении тонкостенных труб (рис. 123, б — д), при калибровке и получении высокого качества поверхностей горячекатанных прутков размером до 150 мм (круг, квадрат); при производстве сложных фасонных профилей (рис. 124, б) для изготовления деталей, которые раньше обрабатывались резанием на станках.
Волочильное оборудование
Оборудование, на котором осуществляют волочение, называют волочильными станами. Волочильные станы по принципу работы тянущих устройств подразделяются на две группы: с прямолинейным движением тянущих устройств — цепные, реечным винтовые и с наматыванием обрабатываемого металла на барабан барабанные.
Прессование
Сущность процесса прессования заключается в выдавливании металла, заключенного в замкнутую полость, через отверстие меньшего сечения, чем площадь сечения исходного металла. Прессованиеприменяют для изготовления прутков, труб и изделий сложных профилей. Наружные размеры и форма каждого профиля определяются размерами и формой отверстия матрицы (рис. 127), а внутренняя — формой и наружными размерами иглы 4.
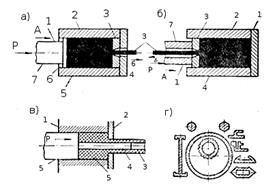
Рис. 127. Схема прессования: а — по прямому методу; б — по обратному; в — трубы; г — профиля, полученные прессованием.
При прессовании заготовку помещают в контейнер 2, с одной стороны которого установлена матрица 5, через отверстие матрицы с помощью пуансона 1 выдавливается металл заготовки. Профиль получаемой продукции при работе на данной матрице будет постоянным на всей длине.
При движении пуансона с некоторой скоростью, называемой скоростью прессования, металл из матрицы будет выходить со скоростью истечения во столько раз большей, во сколько площадь поперечного сечения контейнера будет больше площади отверстия в матрице.
Прессованию подвергают алюминий, медь и их сплавы, а также цинк, олово, свинец и др. Для прессования стальных профилей исходным металлом служат специально подготовленные заготовки. Процесс прессования осуществляется при температурах горячей обработки. Прессование осуществляется почти исключительно на гидравлических, горизонтальных прессах. Усилие применяемых для прессования прессов достигает 15 000 Т.
Применяют два метода прессования — прямой (рис. 127, а) и обратный (рис. 127, б). При прямом методе прессования течение металла совпадает с направлением движения пуансона; при обратном методе прессования металл течет навстречу направлению движения пуансона.При прессовании по прямому методу затрачивается большее усилие, чем при прессовании по обратному методу, так как в этом случае оно расходуется на выдавливание металла и на преодоление трения металла о внутренние стенки контейнера. При обратном методе прессования смещение исходного металла относительно внутренних Стенок контейнера не происходит, а потому усилие расходуется только на выдавливание металла через отверстие матрицы.
При обоих методах прессования имеет место отход металла на прессование: при прямом методе 12 — 15%, при обратном 5 — 6% от веса слитка, получающийся вследствие того, что полностью выдавить из контейнера заложенный в него металл невозможно. Пресс-остаток при обратном методе прессования всегда меньше пресс-остатка, получакщегося при прямом методе. Однако обратный метод получил ограниченное применение из-за сложности конструкции пуансона, который оказывает влияние на конструкцию пресса.
При прессовании труб (рис. 127, в) заготовка должна иметь сквозное отверстие. Это отверстие может быть получено на другом прессе, но также может быть прошито и на том же прессе, на котором осуществляется сам процесс прессования.
Особое внимание при прессовании уделяют нагреву металла и очистке его от окалины, так как заготовки с окалиной резко снижают стойкость матриц. Прессованием можно получить трубы, прутки простых профилей, а также разнообразные профили (рис. 127, г).
К достоинствам метода прессования можно отнести:
- более высокую точность профилей, по сравнению с аналогичными профилями, получаемыми при прокатке;
- возможность избежать малопроизводительных отделочных операций;
- высокую производительность;
- возможность получения сложных профилей.
Наряду с достоинствами у прессования есть и существенные недостатки: значительный износ инструмента, большой отход металла, особенно припрессовании труб большого диаметра.
Не нашли, что искали? Воспользуйтесь поиском по сайту:
©2015 - 2025 stydopedia.ru Все материалы защищены законодательством РФ.
|