Способы получения чёрного глинозёма
Чистый глинозем А12О3 получают многими способами, которые можно разделить на три характерные группы:
- чисто химические методы, когда алюминиевую руду обрабатывают химическими веществами с целью образования растворимых соединений алюминия;
- спекание руд с последующей химической обработкой (спекание ускоряет растворение алюминия);
- металлургическая обработка руды с восстановлением примесей и образованием глиноземистых шлаков, которые дают растворимые в воде соединения алюминия.
Все способы преследуют одну цель — отделить от руды посторонние примеси и получить растворимые соединения алюминия в воде. Для этого руда выщелачивается раствором Na2CО3 с образованием алюмината натрия Al2O3 • Na2О, из которого затем осаждается гидрат окиси алюминия при помощи углекислоты:
3 Н2О + А12О3·Na2О + СО2 →2 Al (ОН)3 + Na2 СО3.
Гидрат окиси алюминия выпадает в осадок, его отфильтровывают, сушат и прокаливают, в результате чего получается чистая окись алюминия:
2А1 (ОН)3→А12О8 + 3 Н2О
Чистая окись алюминия имеет высокую температуру плавания (до 2000°). Для электролиза окись алюминия растворяют и солях — электролите. В качестве электролита используют криолит — фторид алюминия и натрия Na3AlF6; расплавленный криолит хорошо растворяет окись алюминия.
ля электролиза окиси алюминия применяют электролизные ванны — электролизеры. На рис. 34 приведена схема ванны для мектролиза алюминия с непрерывным самообжигающимся анодом. Анод 1 снабжен кожухом 3 из алюминиевых листов толщиной 7 мм. Кожух постепенно наращивают коробами 2 высотой 1 м,которые вставляют один в другой.
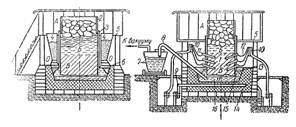
Рис. 34. Схема электролизной алюминиевой ванны с непрерывным самообжигающимся анодом: 1 — анод; 1 — коробка; 3 — кожух; 4— бункеры; 5 — площадка; 5 — окись алюминия; 7 — вакуумный ковш; 8 — труба; 9 — шина катода; 10 — шина анода; 11 — стальные штыри; 12 — медные ленты; 13 — корка электролита; 14 — углеродистые блоки; 15 — расплавленный электролит; 16 — расплавленный алюминий
Подвод тока к аноду в современных ваннах может быть осуществлен сверху и сбоку. На рис. 34 показан подвод тока сбоку. В анод забивают стальные штыри 11 диаметром 60 мм и длиной 700—800 мм под углом 15—20º по отношению к горизонтальной плоскости. Штыри при помощи гибких медных лент 12 соединяют с шиной анода 10. Анод укрепляется на жесткой раме из швеллеров, которая снабжена механизмом для опускания и подъема анода. Закрепляется анод с подъемной рамой при помощи забиваемых штырей. Горизонтальная площадка 5 предназначена для обслуживания анода, наращивания коробок 2, загрузки анодной массы, засыпки порошка окиси алюминия в бункеры 4. Ванна закрывается шторным кожухом. Газы улавливают для извлечения HF.
В кожух анода загружают анодную массу в виде брикетов А; по мере опускания и нагрева эта масса расплавляется, переходит в полутвердое состояние Б. В нижней части, где развиваются высокие температуры, анодная масса спекается в прочный монолит В.
Ваннуэлектролизера 14 выкладывают обожженными углеродистыми блоками, к которым подведены катодные шины 9. На дне ванны собирается жидкий алюминий 16. По мере накопления алюминий из ванны удаляют вакуумными котлами 7 через трубу 8, опускаемую в расплавленный алюминий. Часть электролита затвердевает и образует корку 13. На корку периодически засыпают из бункеров 4 окись алюминия 6.
Напряжение при электролизе составляет 4,5—5 в, сила тока на одну ванну достигает 100 000 а. Необходимая температура ванны (950—1000°) поддерживается сопротивлением электролита, общий расход материалов не 1 т алюминия составляет 1,92—1,98 т глинозема и 0,08—0,09 т криолита. Механизм электролиза глиноземистых расплавов является очень сложным физико-химическим процессом, в результате которого на катоде происходит разряд ионов алюминия, и он собирается на дне электролизной ванны, а ионы кислорода отдают электроны аноду и соединяются с углеродом, образуя углекислый газ.
Когда весь глинозем, находящийся в расплаве, восстановится, напряжение в ванне повышается. Это явление называют анодным эффектом. Его обнаруживают по накаливанию лампочки. В этот момент пробивают корку 13 и опускают глинозем 6 в расплавленный электролит 15 (рис. 34).
Электролизная ванна, сила тока в которой 50 000 а, дает около 350 кг алюминия в сутки. В современной практике расход электроэнергии на 1 т алюминия достигает 17 500—18 500 квт-ч.
Полученный алюминий электролитически рафинируют, разливают в изложницы на чушки и классифицируют по содержанию алюминия на марки согласно ГОСТу. Содержание алюминия в них колеблется от 98 до 99,9 %.ри получении алюминия электролизом и рафинировании его затрачивается большое количество электрической энергии. Поэтому для промышленности представляет большой интерес электротермический способ получения алюминиевых сплавов в дуговых электрических печахс проводящим подом (рис. 35). В этих печах между угольным электродом 5 и токопроводящим подом 1 возбуждается электродуга.
Шихта — смесь руды с восстановителем 3 — загружается аппаратами 4 вокруг электрода. Зависание шихты устраняется аппаратами 6. Жидкий сплав 2 восстановленных элементов собирается на поду.
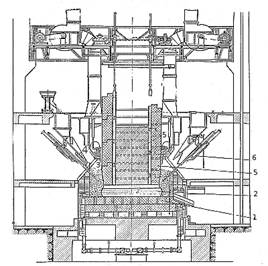
Рис. 35. Конструкция рудотермическои печи: 1 — токопроводящий под; 2 — жидкий сплав; 3 — загруженная шихта; 4 — загрузочный аппарат; 5 —угольный электрод; 6 — аппарат для шуровки
Этим методом выплавляют силикоалюминий с содержанием 30—60% Si и 40—70% А1. Исходным материалом при электротермическом способе служит руды, чистые от железных окислов, с высоким содержанием глинозема и кремнезема. В качестве восстановителей используют древесный уголь и торфяной кокс:
SiО2 + 2C→Si+2СО Si + 2СО→2А1 + 3СО.
Силикоалюминий периодически выпускают через летку и разливают в изложницы. Полученный таким способом сплав добавляют в расплавленный алюминий и получают алюминиево-кремнистые сплавы — силумины.
Расход энергии на 1 т силикоалюминия составляет 10 000 — 12 000 квтч. Из полученных алюминиевых сплавов можно выделить алюминий. Для выделения алюминия применяют метод возгонки алюминия с легкокипящими металлами: ртутью, цинком, магнием и др.
Не нашли, что искали? Воспользуйтесь поиском по сайту:
©2015 - 2025 stydopedia.ru Все материалы защищены законодательством РФ.
|