Пути повышения эффективности работы склада
Дальновидные руководители торговых или производственных компаний всегда нацелены на расширение своей деятельности и увеличение товарных объемов. А для этого надо ответить на вопрос: удастся ли справиться с планируемым товарным потоком без ввода в строй новых складских площадей? Можно ли обработать большую товарную массу, не располагая средствами для расширения имеющихся мощностей?
Анализ финансовых результатов деятельности компании за отчетные периоды поможет понять, является ли склад «узким» местом в системе поставок или может стать таковым, почему в системе распределения постоянные сбои и процент материальных потерь не уменьшается, а с ростом объемов увеличивается. И если в период роста и становления компании закладывался определенный процент на убытки в области обработки товаров, то без сокращения логистических издержек выжить в современных условиях не удастся.
Обычно к предложениям со стороны по совершенствованию логистических операций руководство компании относится без должного внимания или же просто их игнорирует. В итоге руководители логистических и складских подразделений, устав биться со «стенкой - руководством компании», перестают разрабатывать меры по оптимизации складских и транспортных операций. Практика общения с руководителями логистических подразделений показывает, что они большей частью способны разработать и предложить способы оптимизации операций при обслуживании товарного потока. Однако эти предложения не находят поддержки у руководителей компании по следующим причинам (см. Схему 2):
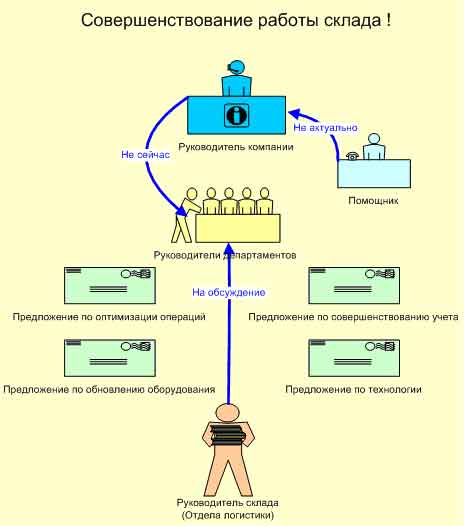
Ø Проведение руководством политики экономии во всем.
Ø Отсутствие концепции (стратегии) развития компании и мероприятий по ее реализации.
Ø Мнение помощника руководителя или руководителя другого отдела, имеющего влияние на руководство и не являющегося специалистом в логистике.
Ø Отведенная руководителю по логистике роль в управлении компании.
Многие руководители компаний не понимают, что большинство решений по оптимизации складских операций напрямую зависит от комплексных мер по развитию коммерческого, транспортного, финансового и других подразделений компании.
Так как работе склада практически во всех компаниях раньше не уделялось достаточного внимания, то она строилась на основании имеющихся возможностей. Под склады отводились бывшие производственные помещения или складские объекты, но старой постройки. Система зонирования в таких складах не проработана, а стеллажное оборудование установлено не оптимально. Технология работы с товарами настолько несовершенна, что позволяет осуществлять только самые основные операции с ними.
Для обработки товаров на складе есть только минимум технических средств. И никакой возможности повышения квалификации для сотрудников склада. Все вопросы о совершенствовании складских операций решаются в последнюю очередь, и любые попытки руководителя склада сделать это пресекаются руководством компании.
Как же определить имеющийся потенциал склада?
Прежде всего необходимо провести аудит товародвижения на складе с применением АВС анализа по ряду характеристик товаров. Такой аудит позволит оценить существующие возможности склада и выявить факторы, влияющие на складскую переработку товаров.
Затем провести аудит существующей складской технологии, системы зонирования и размещения стеллажного оборудования. С помощью такого аудита можно выявить «узкие» места в работе с товарами и оценить потенциал имеющихся площадей с точки зрения возможной обработки товарных объемов и условий, при которых это осуществимо.
Далее необходимо разработать модель склада «как должно быть» с учетом обработки планируемых товарных объемов. Если ставится задача создать модель склада без значительных финансовых затрат, то основным решением будет совершенствование складской технологии, оптимизация операций и использование имеющихся площадей. В завершение определяются потребности в дополнительном складском оборудовании.
Но, как уже говорилось выше, разрабатываются окончательные решения, которые могут быть реализованы только после согласования их с другими подразделениями компании с учетом их возможностей.
Некоторые примеры увеличения пропускной способности склада на имеющихся площадях:
А. Сокращение срока товарного запаса.
По результатам аудита товародвижения выявляются товарные группы или товары с определенными сроками хранения, скорость их реализации (ухода со склада), реальный срок товарного запаса по всем товарным группам и/или артикулам. Эти данные позволяют увидеть реальную работу сотрудников отдела закупок и продаж, деятельность которых напрямую влияет на работу склада.
Для разработки и утверждения срока хранения товарного запаса необходимо учитывать следующие основные факторы:
Ø Сроки и объемы поставок.
Ø Планируемые сроки продаж и маркетинговые данные на будущие периоды.
Ø Мощность склада по хранению товарных запасов.
Решение вопроса о количестве товарного запаса на складе (двухнедельный, месячный и т.д.) позволяет рассчитать потребность в зоне хранения и в максимальном товарном объеме, который может находиться на складе. Принятое решение должны реализовывать все задействованные подразделения, в первую очередь отделы закупок и продаж, а также подразделения логистики по транспортировке товаров.
Следует ежемесячно выявлять на складе залежалые товары (неликвиды), по которым необходимы оперативные решения (уценка, списание, уничтожение). У некоторых компаний товары на складах лежат от нескольких месяцев до 1 года и более. Это приводит к снижению эффективности использования складских площадей и прямым убыткам компании.
По результатам аудита складской технологии, исходя из величины товарного запаса, используемого стеллажного и подъемно-транспортного оборудования, определяется потребность в площади зоны хранения. В зависимости от результатов АВС анализа определяются участки хранения для каждой категории товаров по скорости их реализации, объемно-весовым характеристикам и принятому порядку их отбора.
Реализация разработанной технологии требует наличия соответствующих возможностей (применение метода штрих-кодирования товаров, адресной системы хранения, формирование необходимых отчетов и др.). Применяемый программный продукт должен позволять проводить ежемесячный АВС анализ по обрабатываемым товарам, чтобы можно было корректировать участки хранения для наиболее востребованных товаров и порядок их размещения на хранение.
Б. Увеличение скорости обработки товаров при их приемке и отгрузке.
На постоянно работающем складе средняя величина объемов поступлений и отгрузок примерно одинаковая. Она напрямую зависит от ежедневных объемов продаж, которые могут меняться в силу сезонности и других факторов.
По результатам аудита товародвижения определяются:
- величина входящего и выходящего товарного потока;
- количество и виды транспортных средств, перевозящих товары;
- объемы партий поставок и отгрузок и другие величины.
Полученные данные позволяют проанализировать процессы выполнения операций с товарами при приемке и отгрузке и выявить реальную пропускную возможность склада по этим потокам.
Если количество входных и выходных ворот ограничено и недостаточно площадей для обработки планируемых товарных объемов, то потребуется более детальное изучение всех операций, входящих в процесс приемки и отгрузки. Такое изучение в рамках аудита складской технологии позволяет определить:
- какое количество и в какие временные периоды (в течение суток) автомобили прибывают на склад для разгрузки и погрузки;
- каким образом загружены автомобили (товар на паллетах или в навал);
- какие объемы товаров прибывают на разных видах автомобилей;
- сколько времени уходит на разгрузку/погрузку автомобиля вручную и при помощи транспортных тележек или погрузчиков;
- другие вопросы.
Способы решения, которые требуют согласования с другими подразделениями компании, участвующими в организации движения товаров, могут быть, например, такими:
- Увеличение или переход на доставку всех товаров на европаллетах, что сокращает процесс разгрузки/загрузки автомобиля в 1,5-2 раза.
- Приемка всех товаров по состоянию внешней упаковки без пересчета вложений, что сокращает время приемки в несколько раз.
- Заблаговременная передача данных от поставщика о поступающих товарах для внесения в базу данных склада, что позволяет ускорить процесс приемки товаров.
- Возможность использования одинаковых штрих-кодов для поставщиков, склада и получателей, что экономит время на распечатку и наклейку складских этикеток со штрих-кодом и ускоряет процесс приема товаров.
Решение этих вопросов выходит за рамки деятельности склада и зависит от возможностей, имеющихся у других подразделений компании и у поставщиков. Если хотя бы часть этих вопросов будет реализована, то площадь зоны приемки сократится, так как потребуется меньше времени на приемку товара. Следовательно, на одной площади можно будет обслужить большее количество товаров.
В. Рациональное использование объема склада
Как правило, возможности объема складского помещения (независимо от вида склада) максимально используются только в зоне хранения, где установлены высотные стеллажи. В остальных зонах (разгрузки, приемки, комплектации, экспедиции и загрузки) высота склада обычно не используется. Конечно, для разных складов, выполняющих разные задачи и имеющих разные операции с товарами, трудно предложить единое унифицированное решение. Но сам принцип использования высоты склада должен быть рассмотрен при оптимизации складских площадей. При жесткой ограниченности площади склада обработку больших товарных объемов можно осуществлять следующим способом:
- Установить в зоне комплектации стеллажи для хранения собранных заказов. Такая система может быть актуальна для складов, формирующих и отгружающих многочисленные заказы в течение суток и на следующий день.
- Установить в зоне экспедирования стеллажи для хранения партий товаров, подготовленных к отправке. Эта система актуальна для складов, которые готовят заказы в течение длительного времени, а отгружают в течение ограниченного времени.
При использовании стеллажей для хранения заказов в зоне комплектации или экспедирования следует иметь в виду, что могут появиться дополнительные операции по размещению и изъятию паллет с мест хранения в этих зонах. Поэтому необходимо все взвесить и решить, какой способ будет более рациональным.
Выполнение на складе различных дополнительных операций (стикерование, антикражирование и др.) требует складских площадей. Так как подобные операции производятся вручную с каждой товарной единицей, то это требует штучного отбора товаров с мест хранения. Для этого подойдет мезонин, на котором можно установить полочные стеллажи для ручного отбора товаров. На мезонине можно разместить и рабочие места сотрудников, выполняющих данные операции.
Таким образом, мезонины - это дополнительные складские площади, но на их покупку и установку нужны средства.
Сделаем выводы. Возможности по оптимизации работы склада, более рациональному использованию складских площадей не могут быть реализованы без проработанного плана развития всей компании и изучения возможностей в других подразделениях и у партнеров, так как склад является только средством, обеспечивающим движение товаров, а условия и параметры товарных потоков задаются другими подразделениями компании.
Существует два основных способа увеличения пропускной способности склада:
Совершенствование объемно-планировочных решений в имеющихся складских помещениях.
Ускорение выполнения операций с товарами на всех участках склада.
АВС-АНАЛИЗ ДЛЯ ПОВЫШЕНИЯ ЭФФЕКТИВНОСТИ РАБОТЫ СКЛАДА
Задача анализа товарного запаса на складах регулярно возникает практически во всех компаниях. Одним из наиболее известных методов его проведения является АВС-анализ. Несмотря на это ответы на вопросы «с чего начать?» и «как провести АВС-анализ?» не перестают быть насущными для многих логистов.
Прежде чем проанализировать запас, необходимо определиться с тем, что же хранится на складе. Весь хранимый товар можно разделить на три основные части - основной, временный и вынужденный запас. Очевидно, что формирование каждой из трех составляющих запаса происходит с разной целью и обусловлено разными причинами.
• Основной товарный запас служит для обеспечения текущей отгрузки в соответствии с планом.
• Временный запас создается для получения дополнительных конкурентных преимуществ.
• Вынужденный запас возникает сам по себе в процессе работы любой компании.
Итак, чтобы проанализировать товарный запас, его следует разделить на эти три группы.
Зачем анализировать товарный запас? Ответ очевиден: чтобы оптимизировать остатки и не платить за хранение лишних товаров. Но стандартные подходы, которые используют компании, очень часто не дают ответа на вопрос, что же такое оптимальный запас товара на складе. Почему так происходит? Дело в том, что имеющийся запас товара - это по сути показатель и результат деятельности всей логистической системы компании и ее окружения. В каком-то смысле он не может быть большим или маленьким. Его состояние определяется ассортиментом, товарным наполнением, клиентами, менеджментом и квалификацией персонала компании, размерами склада, географическим положением и т. д.
Существующий размер товарного запаса -это характеристика того, как эффективно компания умеет работать на определенном рынке, с определенными поставщиками и клиентами. Для того чтобы приблизить свой товарный запас к оптимальному, необходимо научиться выделять самые значимые причины, влияющие на текущее состояние товарного запаса компании.
Почему надо использовать АВС-анализ?
Идея ABC-анализа строится на основе принципа Парето, который формулируется следующим образом: «За большинство возможных результатов отвечает относительно небольшое число причин». В настоящее время принцип широко известен как «правило, 20 на 80».
Самая простая разновидность ABC-анализа - это отсортированный по убыванию список параметров. Если номенклатурный перечень не превышает 100 наименований, такой сортировки бывает достаточно. Сложнее выделить значимые позиции, если на складе хранится несколько десятков тысяч наименований товара. Именно в таких случаях и используется развернутый АВС – анализ.
Таблица 1
Исходные данные

С чего начать?
Проведение анализа необходимо начинать с выбора объектов, значимость которых мы хотим определить, и актуальных параметров объектов, по которым мы будем проводить анализ. Проведение анализа начинают с выбора объектов и определения их актуальных параметров.
Объектом может быть товар, товарная группа, поставщик, клиент, заказ и т. д. В качестве параметра можно выбрать: средний или текущий товарный запас в рублях; штуках, коробках или паллетах; объем продаж за период, доходность товара, количество заказов клиентов и т. п..
Для примера рассмотрим отчет о среднем товарном запасе за месяц в паллетах. Объектом анализа являются товары; параметром, по которому проводится анализ, - средний товарный запас за месяц в паллетах (см. таблицу 1).
Как выполнять АВС - анализ?
Для проведения анализа очень удобно использовать MS Excel или любой другой аналогичный редактор. Порядок действий следующий.
1. Отсортировать объекты анализа в порядке убывания значения параметра.
2. Рассчитать долю параметра от общей суммы параметров выбранных объектов (это делается для того, чтобы оценить «вклад» каждого объекта в общий результат).
3. Рассчитать эту долю с накопительным итогом (эта операция носит технический характер и служит для удобства дальнейшего определения границ для групп ABC).
4. Присвоить значения групп выбранным объектам.
Наибольшее число вопросов вызывает определение границ при проведении АВС-анализа. Автор в своей практике изначально использовал деление на три группы по показателю «доля с накопительным итогом»: А - до 50%, В - 50-80% и С - 80-100%. Данное распределение полностью отвечает задачам склада оптовой компании или розничной сети.
Товар – взаимозаменяемый, и соответственно в группу С попадает весь «ассортиментный хвост». Но в случае анализа запаса на складе производственной компании или сети магазинов - дискаунтеров, в которых взаимозаменяемость товаров может отсутствовать, появилась необходимость разделить группу С, куда попадает 80% всего ассортимента, на две менее крупные группы. Поэтому во многих случаях рекомендую производить деление товара на четыре группы:
· группа А - объекты, сумма долей с накопительным итогом которых составляет первые 50% от общей суммы параметров;
· группа В - следующие за группой А объекты - от 50 до 80%;
· группа С - от 80 до 95%;
· группа D - оставшиеся объекты, сумма долей с накопительным итогом которых составляет от 95% до 100% от общей суммы параметров.
В результате проведенного анализа мы получили четыре группы объектов (таблица 2):
группа А - составляет 20% ассортимента и 49% товарного запаса;
группа В - 30% ассортимента и 30% товарного запаса;
группа С - 20% ассортимента и 13% товарного запаса;
группа D - 30% ассортимента и 8% товарного запаса.
Несколько практических рекомендаций.
Допустим, перед компанией стоит задача снизить средний товарный запас. В этом случае необходимо разобраться, по какой причине товары группы А находятся на складе в таком большом количестве. Даже незначительное снижение запаса только по двум товарам из этой группы заметно скажется на общем объеме товарного запаса.
Основной запас
· Рабочий товарный запас, необходимый для обеспечения отгрузки в соответствии с планом продаж на текущий период.
· Страховой товарный запас, который позволяет компенсировать незапланированный рост отгрузки и непредвиденные задержки в доставке, связанные с перебоями в производстве или наличии товара у поставщика.
Временный запас
· Сезонный товарный запас. Избыточный запас, создаваемый до начала сезонного роста продаж.
· Маркетинговый товарный запас. Дополнительный запас, формируемый на время проведения маркетинговых акций, рекламных кампаний и т. д.
· Конъюнктурный товарный запас. Избыточный запас, создаваемый под воздействием конкурентной ситуации на рынке.
Причинами создания конъюнктурного запаса могут: разовые скидки поставщиков, прогнозируемый или искусственно создаваемый дефицит товара у поставщиков и т. п.
Вынужденный запас
Брак. Товар, который потерял потребительские свойства и не может быть в дальнейшем использован по назначению.
Неликвидный или труднореализуемый запас. Часто этот товар появляется в результате «творческого взаимодействия» отдела продаж и отдела закупок: запланировали отгружать одно количество, а фактический спрос оказался в 10 раз меньше; заменили одного поставщика на другого, а реализовать остатки «забыли» и т. д.
Таблица 2
Распределение товаров по группам на основе АВС-анализа.
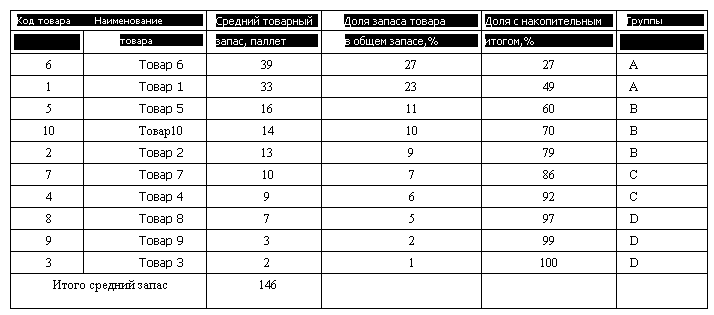
Таблица 3 Сопоставление объемов отгрузки на некий период с суммой брака на этот же период.
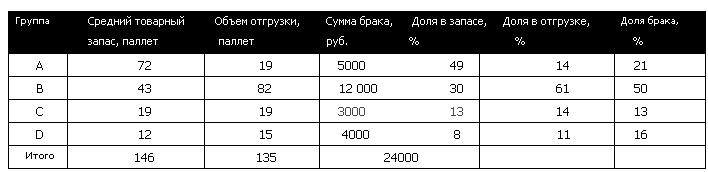
Результаты АВС-анализа следует использовать разносторонне. Много дополнительной информации можно получить, если сопоставить результаты анализа по одному параметру с другими параметрами одного и того же объекта, например отгрузку товара за некий период и сумму брака по товару за этот же период (Таблица 3).
Два товара группы А, на которые приходятся 14% отгрузки, составляют 49% товарного запаса. При этом на два товара группы С приходятся те же 14% отгрузки, но они составляют только 13% запаса. Значит, если по товарам группы С удается обеспечить отгрузку со средним товарным запасом в 19 паллет, то не исключено, что и в отношении товаров группы А существует такая же возможность.
Сгруппировав товар по одному параметру, сопоставьте полученный результат с другими параметрами. Группа D может приносить 5% дохода, составлять 50% товарного запаса и занимать 70% площади склада.
ABC-анализ товаров по доходу покажет, на чем зарабатываются деньги, аналогичный анализ по затратам позволит понять, на что они тратятся.
Если в оптовой компании или розничном магазине провести ABC-анализ товаров по объему продаж, а потом оценить, из каких товаров состоят ассортиментные группы, то можно определить, какие из этих групп требуют расширения, а какие - сокращения.
Можно проанализировать товары по количеству отгруженных единиц (или количеству заказов по ним) и в результате получить 20% товаров, покупаемых 80% клиентов, определив привлекательность товара для клиента. Этот же результат можно использовать при планировании размещения товара в «горячих» и «холодных» зонах на складе.
В одной очень известной оптовой компании информационная система настроена таким образом, что менеджер по закупке при формировании заказа сначала открывает список поставщиков группы А. При этом товары отсортированы и выделены разным цветом не по алфавиту или коду, как обычно, а по результатам ABC-анализа товаров по доходу за последний квартал. В первой половине дня формируются заказы на наиболее значимые товары, а в конце дня, когда сотрудник устает и совершает больше ошибок, оформляются наименее важные заказы.
Первый шаг
Даже на рассмотренном простейшем примере из 10 товаров видно, что АВС - анализ позволяет не только разбить весь набор данных на группы в зависимости от степени влияния на конечный результат, но и значительно облегчить работу с большим ассортиментом. Сначала весь ассортимент делится на группы, а затем более подробно рассматривается каждый товар в группах А и В и менее подробно - в группах С и D. Это дает возможность более эффективно распределить усилия и рабочее время, которые требуются для контроля и управление наиболее важными с точки зрения конечного результата объектами.
Важно помнить, что АВС - анализ является одним из способов математической обработки данных. Если провести анализ по сумме дохода от продаж, а потом сократить группы С и D как приносящие всего 20% дохода, но занимающие 60% площади склада, то через некоторое время оставшиеся товары распределятся по тому же закону, но общий результат деятельности компании может снизиться на 50%. Ценность в глазах клиентов имеют не только товары основного ассортимента, но и «ассортиментный хвост», который отличает компанию от конкурентов.
Таким образом, АВС - анализ позволяет сделать первый эффективный шаг в оптимизации товарного запаса на складе.
Посменная работа: компромиссный вариант
Для чего и на сколько необходимо увеличивать время работы склада? Как распределить работу между сменами и выбрать оптимальное для конкретного склада соотношение время/трудовые ресурсы?
Чаще всего обработка товаропотока на складе включает в себя:
1. Погрузочно-разгрузочные работы:
- разгрузка паллетированного груза;
- разгрузка навального груза;
- загрузка отобранных заказов.
2. Комплектацию заказов:
- формирование пакета документов под заказы.
3. Внутрискладские работы:
- инвентаризация;
- работа с браком;
- работа с документами.
На функционирование складского комплекса оказывают влияние и такие факторы, как пропускная способность погрузочно-разгрузочных доков, размеры зоны комплектации и т. п., но мы рассматриваем время и трудовые ресурсы, затрачиваемые на операцию. Теоретически, если предположить, что все операции строго последовательно выполняет один человек, мы получим минимальные затраты на ресурсы и максимальный период времени на весь процесс. Если же на складе одновременно трудится такое количество человек, что большинство операций можно делать параллельно, то затраты на ресурсы значительно увеличатся, а время на выполнение всего объема работ сократится.
Выбор компромисса между количеством сотрудников и объемом времени на выполнение всех операций - одна из основных проблем, которые должен решать менеджер складского комплекса.
Исходные данные
Перевод затрат на каждый вид складских работ в человеко-часы - лучший способ приведения потребностей в ресурсах и времени к одному параметру. В этом случае мы получаем общий объем затрат, которые можем распределить либо в пользу человека, либо в пользу часов.
Рассмотрим складской комплекс, предназначенный для обработки продукции, хранящейся в коробах и на паллетах (в среднем на паллете здесь умещается 80 коробов). На складе проводится разгрузка и так называемых паллетных машин (товар размещается на паллетах), и сборных (товар в навал).
Во втором случае требуется дальнейшая укладка товара на паллеты, поэтому затраты на разгрузку таких машин больше. Заказы на отгрузку имеют разную структуру и объем. Они поступают от оптовых клиентов, торговых представителей, а также из филиалов. Объем ежедневных работ приведен в столбцах 1-4 табл. 1 и в столбце 1 табл. 2.
Таблица 1.
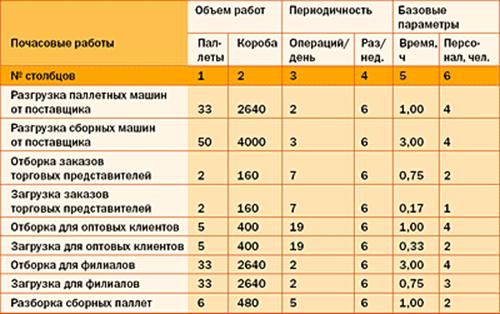
Таблица 2.
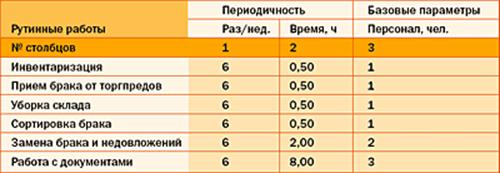
Каждодневная инвентаризация - это выборочные пересчеты продукции, которые делает кладовщик в течение дня для контроля качества работы персонала склада. Работа с браком включает в себя прием, сортировку, документальное оформление. Поскольку все работы планируются непосредственно на складе, необходимо ввести в расчеты работу операторов и кладовщиков с документами.
Затраты по времени и ресурсам приведены в столбцах 5-6 табл. 1 и в столбцах 2-3 табл. 2. Затраты (в человеко-часах) на каждую операцию в отдельности и на все операции вместе находятся путем несложных подсчетов. Они представлены в табл. 3.
Человеко-часы рассчитываются как произведение "затраты на операцию по времени" (табл. 2, столбец "Время") х "количество персонала, задействованного в данной операции" (табл. 2, столбец "Персонал") х "количество операций в день" (табл. 1, столбец "Операции в день"). Как видно, общая потребность в ресурсах по данному складскому комплексу составляет 213 человеко-часов в сутки.
Таблица 3.
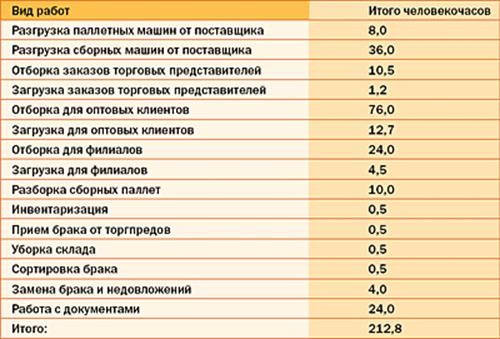
Теория
Распределение работ по времени должно преследовать конкретные цели: оптимизировать использование зоны погрузки/разгрузки, "привязать" основные процессы к оптимальному времени выполнения работ и обеспечить максимально равномерное распределение затрат по времени.
Для начала, чтобы достаточно быстро уменьшить возросшую потребность в площадях и складской технике, а также снизить риски возникновения конфликтов между операциями, необходимо разделить по времени процессы разгрузки и погрузки. Отборка и загрузка заказов торговых представителей должна осуществляться до начала работы торговых точек. Отборку и загрузку заказов оптовых клиентов необходимо производить в таком порядке, чтобы заказы доставлялись в день отборки. Распределение загруженности склада по часам позволит сформировать равномерные по персоналу смены.
Затем необходимо, варьируя людские и временные характеристики склада, привести полученную потребность человеко-часов к тому количеству рабочих часов или смен, которые мы хотим видеть на данном складском комплексе.
Решение
Для того чтобы определить пиковые нагрузки на склад и количество сотрудников, необходимо составить график, опираясь на исходные данные. Распределив все работы склада по времени, составим несколько вариантов организации работы смен и количества персонала в них.
Предположим, что мы планируем ввести односменный восьмичасовой график, и работы распределены следующим образом (табл. 4.1 и табл. 4.2).
Таблица 4.1.
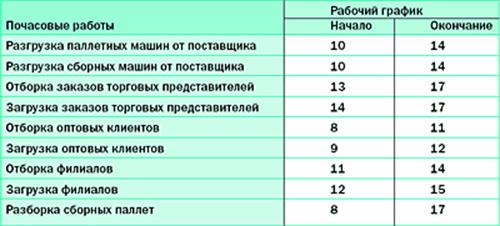
Таблица 4.2.
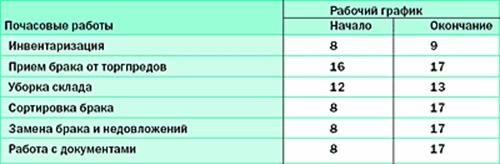
После того как мы получили затраты на каждую операцию в человеко-часах и определили период времени, когда данные виды работ выполняются, мы можем составить график загруженности для склада. Для этого мы должны суммировать все затраты в человеко-часах по всем операциям на каждый час рабочего времени склада и представить это в виде графика (см. график 1).
Не нашли, что искали? Воспользуйтесь поиском по сайту:
©2015 - 2025 stydopedia.ru Все материалы защищены законодательством РФ.
|