ОСНОВНЫЕ СИЛЫ, ДЕЙСТВУЮЩИЕ НА ГОЛОВКУ БАЛАНСИРА
Все нагрузки, действующие на головку балансира или ТПШ можно разделить на 2 большие группы:
- статические: вес самой штанговой колонны, вес столба жидкости (при ходе вверх)
- динамические: силы инерции движущихся масс возникающие при движении с ускорением штанговой колонны и столба жидкости при ходе вверх, вибрационные нагрузки, обусловленные колебательными явлениями штанговой колонны
На практике часто приходится учитывать и другие виды динамических нагрузок, например, силы трения штанговой колонны о жидкость (при откачке вязких нефтей, высоковязких эмульсий).В этих случаях силы трения становятся соизмеримы с весом самой колонны.
Максимальная нагрузка будет при ходе вверх, а минимальная при ходе вниз.
,
где Р¢шт – вес штанговой колонны в жидкости с учетом выталкивающей силы
Р¢ж – усилие от веса столба жидкости высотой от динамического уровня до устья
где a,а1 – кинематические коэффициенты Вирновского, зависят от типа СК
D – диаметр плунжера
d – диаметр штанг
w - угловая скорость вращения кривошипа
s0 – длина хода ТПШ
lшт – удлинение штанг

где fшт и fтр – площадь поперечного сечения трубы и штанг по телу.
Для практики применение этой формулы неудобно, Поэтому они были упрощены Адониным. Было выведено 2 режима: статический и динамический.
Их различают по параметру 
w - угловая скорость вращения кривошипа
L – длина штанговой колонны
а – скорость звука в стали 5100 м/с.
Формула Адонина менее точна, чем Вирновского. Их различие +-100кг, что в пределах погрешности динамографа гидравлического типа.
НАСОСНЫЕ ШТАНГИ И МУФТЫ
Штанговая колонна (ШК) предназначена для передачи движения от привода к плунжеру насоса. ШК собирается из отдельных штанг, соединяемых муфтой. Штанги выпускаются диаметром: 12, 16, 19, 22, 25 мм. Длина штанги 8м±.
Стандартом предусмотрен выпуск укороченных штанг для регулировки длины колонны, длиной 1,3; 1,5; 2; 3м.
Резьба – метрическая специальная Ш19 ГОСТ 13877-80
Муфты выполняются в двух исполнениях: без лысок, с лысками под ключ.
Колонна насосных штанг является наиболее слабым элементом насосной установки, поэтому она работает в очень тяжелых условиях: испытывает переменные нагрузки которые имеют пульсирующий характер, т.е. одного знака, но в нижней части под плунжером может быть знакопеременной; колонна погружена в коррозионно-активную жидкость – смесь нефти и минерализованной воды, в которой зачастую присутствуют агрессивные СО2 и H2S; штанга интенсивно изнашивается вследствие трения об НКТ, особенно на участках набора кривизны наклонно-направленных скважин.
Исходя из этого очень важна технология производства штанги. Применяются методы упрочнения – все штанги выполняются методом формирования. Резьба не нарезается а накатывается, что позволяет получить волокнистую структуру металла.
Штанги изготавливаются из следующих сталей:
- для легких условий работы – сталь 40, нормализация
- для средних и среднетяжелых условий работы – 20Н2М, 20НМ, нормализация
- для тяжелых условий работы – сталь 40 с последующим упрочнением ТВЧ или из стали 30ХМА или нормализованная с упрочнением ТВЧ
- для особотяжелых условий – 15НВМА закалка.
Может применяться дробеструйная обработка для создания поверхностного наклепа.
Наиболее частые причины выхода из строя штанговых колонн является: обрыв штанговой колонны; отворот.
Обрыв штанг вызывается усталостью металла вследствие переменности нагружения, концентрация напряжений около концентраторов и агрессивного воздействия среды. Усталостное разрушение начинается с появления микротрещин на поверхности, обычно формируются на участках у головки штанг. Далее микротрещины развиваются вглубь штанги, пока не произойдет обрыв штанг.
Другой причиной наиболее частых обрывов штанг на участках, прилегающих к головке является несоосность тела штанги и головки, приводящая к появлению Мизг.
На работу штанговой колонны сильно влияет момент свинчивания. Мкр должен быть таким, чтобы после затяжки обеспечить такое усилие прижатия торца муфты к уборному бурту так, чтобы после запуска штанги в колонну данный стык не раскрылся. Поэтому штанги собираются с помощью механических ключей с моментомером.
Расчет колонны штанг сводится к допускаемому напряжению обуславливающую длительную надежную работу штанговых колонн.
За время двойного хода нагрузка на штанги переменна. Так в ТПШ усилие при ходе вверх определяется весом штанг, весом столба жидкости, силами трения, инерционными нагрузками, а при ходе вниз только усилиями от веса штанг, т.е. в верхней части колонны действует усилие одного знака (переменное), пульсирующая.
Характер нагружения в нижней части колонны иной – при ходе плунжера вниз усилие трения плунжера о цилиндр, усилие обусловленное гидравлическим клапаном и приводит к появлению усилий, сжимающих штанговую колонну, т.е. в нижней части колонны могут возникнуть знакопеременные нагрузки. В России за критерий нагружения штанг (ШК) принято приведенное напряжение sпр , учитывающее циклический характер нагрузки, рассчитываемое по формуле:
,
где sмах – максимальное напряжение цикла
sамп – амплитуда напряжений цикла
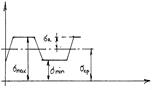

Полученное значение sпр сравнивается с допускаемым. Под допускаемыми напряжениями понимаются такие предельные напряжения в опасном сечении, при которых ШК выполняет свои функции в заданное время без разрушения. В нефтепромысловой практике в качестве допускаемых напряжений понимаются такие напряжения пр которых число обрывов не превысит 1-3 раза в год.
Допускаемое напряжение определяется опытным путем, путем статистической обработки результатов работы штанг в конкретных скважинных условиях. На основе полученных статистических данных строится зависимость среднего числа обрыва штанг от напряжений в конкретных скважинных условиях.
В большинстве случаев для уменьшения веса ШК применяют ступенчатые колонны. Их подбирают из следующего условия:
sпр1=sпр2=sпр3. (1)
Длина и диаметры подбираются из условия (1).
Опыт эксплуатации штанг показал, что основными причинами разрушения колонны является:
- обрыв тела штанги – 60%
- обрыв ниппельной части – 17%
- обрыв муфты – 13%
- обрыв резьбовых соединений – 10%
При увеличении глубины подвески насоса число обрывов штанг по телу растет и достигает 90%.
ШТАНГОВЫЕ НАСОСЫ
Штанговые насосы (ШН) работают в тяжелых условиях: перекачиваемая жидкость содержит минерализованную воду, абразив, химически активные вещества, газы; температура окружающей среды до 100 0С.
Стандарт ОСТ предусматривает выпуск следующих типов насосов:
НВ1, вставной с замком наверху
НВ2, вставной с замком внизу
НН1, невставной с захватами штоком
НН2, невставной с ловителем
Предусмотрены следующие исполнения насосов, различающиеся:
1) по конструкции цилиндра: Б – безвтулочный цилиндр (толстостенный) С – составной втулочный цилиндр
2) по конструктивным особенностям определяемым функциональным назначением
Т – с полым трубчатым штоком, обеспечивающим подъем жидкости по полым штангам
А – со сцепляющимся устройством для сцепления КШ с плунжером
D1 – одноступенчатые двухплунжерные обеспечивающие откачку высоковязкой жидкости.
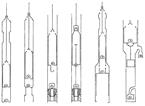
НВ1, НВ2, НН2, НН1, НВ1D1, ННD1
5) – одноступенчатый, двухплунжерный для работы с вязкими жидкостями, позволяет бороться с изгибом(продольным) нижней части ШК, путем создания растягивающей нагрузки, приложенной к низу ШК при ходе вниз.
6) – насос с вакуумным гидроутяжелителем, позволяет бороться с продольным изгибом низа ШК при работе с вязкими жидкостями.
3) по стойкости к среде
« » - (без обозначения) нормальные насосы с содержанием примеси 1,3г/литр
и – абразивно-, износостойкий, стойкий к среде с мех примесями больше 1,3г/литр
4) По зазорам насосы делятся на группы посадки
Цилиндры. Стандарт API предусматривает выпуск цилиндров:
Толстостенные, тонкостенные.
Стандарт ОСТ предусматривает выпуск только толстостенных цилиндров. Толщина стенки цилиндра 7-8мм (толстостенные), 3-3,5мм (тонкостенные).
Тонкостенные применяются во вставных насосах. Толстостенные, как правило в невставных.
По степени обработки внутренней поверхности цилиндра их различают:
прецизионно-хопингованный цилиндр, хопингованный цилиндр.
ПХ цилиндр предназначен при работе с металлическими плунжерами, т.е. герметизация пары плунжер-цилиндр осуществляется за счет выполнения минимально возможных зазоров.
Х цилиндр предназначен для работы с мягкими плунжерами, т.е. герметизация осуществляется за счет уплотнительных эластомеров.
Плунжеры насосов. Плунжеры по типу уплотнения могут быть: уплотнения металл по металлу (металлический плунжер); плунжер с мягким уплотнением или с уплотнением эластомера; цельный; сборный.
Плунжеры могут быть гладкими и с канавками.
Стандарт предусматривает строго заданный номинальный диаметр плунжера. По стандарту ОСТ необходимый зазор между цилиндром и плунжером набирается, обеспечивается путем селективной сборки. Стандарт API обеспечивает и требует обеспечение фактических диаметров плунжера и цилиндра с точностью до сотых долей мм. Это позволяет обеспечивать при массовом производстве необходимый зазор между плунжером и цилиндром. Данная особенность существенно облегчает ремонт насоса.
Клапанные узлы. Основным конструктивным отличием клапанных узлов выполненных по API является отсутствие клетки. Стандарт предусматривает использование различных покрытий внутренней поверхности корпуса клапана для уменьшения износа шарика (в виде резины)
Замковые опоры. Стандарт предусматривает 2 типа крепления вставных насосов:
механическое крепление; манжетное крепление.
Крепление может быть в верхней части насоса и в нижней части насоса. Крепление вставного насоса осуществляется путем взаимодействия замка насоса с замковой опорой.
Требования к замковым опорам:
- крепление насоса должно обеспечивать его фиксацию в начальный момент работы установки, т.е. когда уровень жидкости в затрубе и в трубах одинаков
- крепление должно обеспечивать фиксацию насоса в случае действия динамических нагрузок, обусловленных силами трения плунжера о цилиндр и т.д.
- крепление должно обеспечивать герметичность соединения замка с замковой опорой
- крепление должно обеспечивать срыв насоса с опоры без осложнений в момент ПРС.
Преимущества и недостатки верхнего и нижнего крепления.
Нижнее крепление обеспечивает более выгодную форму нагружения цилиндра насоса, что позволяет использовать на больших глубинах. Недостатком является возможность прихвата насоса особенно при периодической откачке.
Достоинством верхнего крепления является меньшая вероятность прихвата насоса, однако этот тип крепления нельзя применять при больших подвесках.
УЭЦН
УЭЦН предназначен для откачки из нефтяных скважин пластовой жидкости, содержащей воду, нефть, газ и мех примеси. УЭЦН имеют исполнения: обычное, повышенной коррозионной стойкости, повышенной износостойкости.
УЭЦН состоит из: погружного насосного агрегата (ЭД, система гидрозащиты, насос); кабельные линии; оборудование устья скважины; колонна НКТ; наземное электрооборудование.
Погружной насосный агрегат спускается в скважину на колонне НКТ, кабель крепится к НКТ хомутами и обеспечивает подвод электроэнергии к агрегату. Над насосом устанавливаются обратный и сливной клапаны.
Обратный клапан позволяет предотвратить обратный переток жидкости при остановке агрегата, а также обеспечить запуск насоса на закрытую задвижку. Сливной клапан устанавливается выше обратного и обеспечивает опорожнение колонны НКТ перед подъемом агрегата в процессе ПРС.
Оборудование устья скважины обеспечивает подвеску колонны с агрегатом и кабелем, герметизацию труб и кабеля и отвод жидкости в манифольд.
Трансформатор обеспечивает подачу необходимого напряжения к погружному ЭД. Станция управления предназначена для управления погружным ЭД.
Оборудование устья унифицировано с оборудованием устья фонтанирующей скважины, с тем отличием что выполнен в колонной головке узел ввода кабеля.
компенсатор + протектор = гидрозащита ПЭД
Конструкция погружного насосного агрегата (ПНА) и его особенности.
ЭЦН – являются многоступенчатыми и секционными.
Рабочие колеса и направляющий аппарат размещены в корпусе и собраны в пакет на валу. Рабочие колеса насажены на вал с зазором и соединены с ним посредством призматической шпонки и могут свободно перемещаться вдоль вала. В осевом направлении каждое рабочее колесо опирается на направляющий аппарат через шайбу. Таким образом, осевые нагрузки от рабочих колес передаются на корпус насоса и вал разгружается.
Порядок выбора установки подразумевает выбор узлов агрегата и режимных факторов и производится в следующей последовательности:
1. Определяют потребный напор насоса для конкретной скважины
2. Задается проектный объемный дебит скважины по жидкости
3. Производят подбор установки из числа имеющихся
4. Определяют глубину подвески насоса
5. проверяют возможность работы установки при откачке тяжелых жидкостей
6. Проверяют диаметр погружного агрегата, труб и кабеля, чтобы обеспечить необходимый зазор в обсадной колонне.
Определение необходимого напора.
Давление создаваемое насосом расходуется на преодоление давления создаваемого столбом жидкости в трубах НКТ над динамическим уровнем, а также на преодоление гидравлических сопротивлений в лифте при движении газожидкостной смеси в НКТ. Необходимое давление уменьшается на величину работы газа в НКТ.
Давление нагнетания насоса: 
,
где rghдин – давление создаваемое весом столба жидкости над динамическим уровнем
Рсопр – давление необходимое на преодоление гидросопротивлений
rghг – давление за счет работы расширения газа.
В свою очередь, давление создаваемое столбом жидкости в трубах НКТ над динамическим уровнем определяется как разность между давлением создаваемым столбом жидкости в трубах в скважине находящихся в покое (статическим уровнем) и забойным давлением устанавливающееся в скважине в процессе ее эксплуатации.
Глубина погружения выбирается исходя из минимально возможного газосодержания на приеме насоса (до 35%)


Вопросы выбора насоса. В промысловой практике необходимый напор и производительность редко соответствует паспортному, поэтому приходится производить подгонку к конкретным условиями способы:
- снятие необходимого числа ступеней (не более 20%) (установка втулок)
- установка дросселя на устье в котором расходуется излишек энергии (напора)
- применение регулируемого привода
1 способ более предпочтителен, т.к. позволяет эксплуатировать установку с большим КПД. С другой стороны 2 способ позволяет изменять производительность установки не извлекая ее на поверхность, т.к. имеется излишек мощности на устье в дросселе, путем замены дросселя. Это особенно важно, т.к. в процессе длительной эксплуатации могут возникнуть отложения в НКТ, увеличивающие гидросопротивляемость. Поэтому в промысловой практике применяют первые 2 способа одновременно – снимают часть рабочих колес оставляя давление на дроссель.
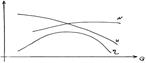
1. Способ установки проставки
2. Стравливается в дроссель
3. Меняют частоту вращения.
Диаметральный габарит погружного оборудования должен обеспечить спуск и подъем без осложнений и повреждений на большую глубину наклонно-направленных скважин.
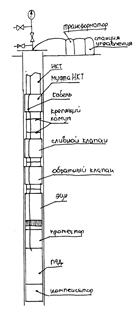
ВИНТОВЫЕ НАСОСЫ
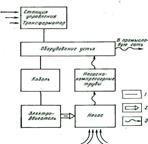
Рисунок 1. Структурная схема установки УЭВН:
1—передача электроэнергии, 2—передача механической энергии; 3—течение жидкости
УЭВН (рис.2) состоит из погружного агрегата, включающего специальный погружной маслозаполненный электродвигатель 1, протектор 2 и винтовой электронасос 3, специальный кабель 4, прикрепленный к колонне НКТ 5 хомутами 6. С помощью устьевого оборудования 8, установленного на колонной головке эксплуатационной колонны 7, подвешена колонна НКТ. На поверхности рядом со скважиной устанавливается кабельный барабан 9 и автотрансформатор 10 со станцией управления 11. Выше насоса устанавливается обратный клапан, облегчающий пуск установки после ее простоя, а над обратным клапаном— спускной клапан для слива жидкости из внутренней полости НКТ при их подъеме.
Винтовые электронасосы
Существенным недостатком центробежных насосов является его низкая эффективность при работе в скважинах с дебитами ниже 60 мУсут и с малыми диаметрами эксплуатационных колонн. Это явление обусловлено свойствами центробежного насоса—степенной зависимостью развиваемого напора от диаметра колеса, т. е. в конечном счете от диаметрального габарита насоса.
С другой стороны, высокая единичная мощность агрегата обусловлена рациональным принципом его компоновки—расположением первичного двигателя в непосредственной близости от насоса.
Электровинтовые насосы скомпонованы аналогично УЦЭН, но вместо гидродинамического центробежного насоса используется объемный — винтовой насос. Это решение позволяет использовать все преимущества объемного насоса и преимущества компоновки агрегата ЦЭН.
Принцип действия винтовых насосов заключается в том, что винт или винты насоса и его обойма образуют по своей длине ряд замкнутых полостей, которые при вращении винтов передвигаются от приема насоса к его выкиду. В начальный момент каждая полость сообщается с областью приема насоса, при продвижении вдоль оси насоса ее объем увеличивается, заполняясь перекачиваемой жидкостью, после чего становится полностью замкнутым. У выкида объем полости сообщается с полостью нагнетания, постепенно уменьшается, а жидкость выталкивается в трубопровод.
Винтовые насосы могут быть с несколькими или с одним винтом. Для перекачивания нефти используются одновинтовые насосы. У одновинтового насоса замкнутая полость образуется одним металлическим винтом и резиновой обоймой. Винт имеет однозаходную плавную нарезку с весьма большим отношением длины витка к глубине нарезки (15—30). Обойма насоса имеет внутреннюю поверхность, соответствующую двухзаходному винту, у которого шаг винтовой поверхности равен удвоенному шагу винта насоса. Винт вращается вокруг своей оси и по окружности с радиусом, равным ее эксцентриситету.
Для увеличения долговечности насоса и прежде всего его основных деталей — винты и обоймы, работающих в условиях абразивного изнашивания, сочетающегося с коррозионным воздействием перекачиваемой жидкости, их изготавливают следующими: винт из стали с покрытием хромом, обойму — из маслотермостойкой резины с высоким сопротивлением абразивному изнашиванию.
Винтовой насос подвешивается в скважине на насосно-компрессорных трубах вместе с протектором, электродвигателем и токоподводящим кабелем. Все элементы электропривода у одновинтового насоса такие же, как у центробежного насоса.
На рис. показан общий вид винтового насоса. Он имеет два рабочих винта 4 и 7 и две обоймы 3 и 6. Прием жидкости из скважины ведется через две фильтровых сетки 2. Нагнетаемая жидкость поступает в полость между винтами и за обоймой 3 проходит к предохранительному клапану / и далее в насосно-компрессорные трубы. Привод насоса идет от двигателя через протектор 10, пусковую муфту 9 и вал 8. Шарнирные муфты 5 позволяют осям винтов вращаться по окружности с радиусом, равным эксцентриситету. Осевые усилия от двух винтов приложены к муфте, расположенной между ними, и взаимно компенсируются.
Одновинтовые насосы для добычи нефти рассчитаны на подачи 40, 80, 100 м^суг жидкости и напоры 800 и 1400 м для применения в 146 и !68 мм колоннах. К. п. д. насосов находился в пределах 0,4—0,7. При этом увеличение вязкости перекачиваемой жидкости не уменьшав к. п. д. насоса так, у центробежных насосов.
Насосы работают от двигателей с 2800—3000 оборотами вала в минуту.
В погружных винтовых насосах применяется ряд специфических узлов и деталей —пусковая и эксцентриковая муфты, предохранительный клапан, шламовая труба." Пусковая муфта служит для соединения вала протектора с валом насоса при вращении двигателя с рабочим числом оборотов и разъединения их в момент запуска электродвигателя. Таким образом обеспечивается максимальный крутящий момент по валу насоса при его пуске.
Помимо этого пусковая муфта не позволяет при обесточи-вании двигателя вращаться валу насоса в противоположную сторону.
При аварийном выходе из строя насоса пусковая муфта отключает вал протектора от вала насоса.
Необходимость установки эксцентриковой муфты обусловлена особенностями кинематики насоса. При работе его помимо того, что винт вращается вокруг собственной оси, одновременно происходит вращение оси винта, причем направления этих движений противоположны. Эксцентриковые муфты устанавливаются между валом протектора и винтом и между винтами.
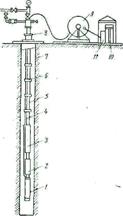
ДИАФРАГМЕННЫЕ НАСОСЫ
Диафрагменные насосы рассчитаны на откачку жидкости с высоким содержанием механических примесей. Температура откачиваемой жидкости не должна превышать 80° С, а вязкость — 300 сст. Эффективно применение насосов для откачки агрессивных жидкостей. Для насосов этого вида характерны небольшие подачи и напоры. Характеристика одного типоразмера насоса (по данным фирмы Плойгер) приведена на рис.23.
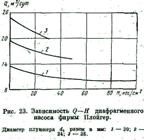
Наиболее важной особенностью глубинных диафрагменных насосов является расположение всех рабочих органов насоса, кроме всасывающего и нагнетательного клапанов, в маслозаполненной герметичной камере. Эта камера отделена от добываемой жидкости гибкой диафрагмой. Таким образом, воздействию добываемой жидкости подвергается минимально возможное количество деталей глубинного насоса.
Схема диафрагменного насоса (рис. 24) конструктивно объединяет насосные узлы с маслозаполненным асинхронным электродвигателем. С ротором электродвигателя жестко связана ведущая шестерня конического редуктора. На ведомой шестеренке смонтирован эксцентрик, создающий поступательное движение плунжеру наcoca.
Возвратное движение плунжера осуществляется с помощью цилиндрической пружины. Все камеры электродвигателя и насоса, вплоть до диафрагмы, заполнены жидким маслом. Для компенсации изменения объема масла при нагреве в нижней части двигателя имеется резиновый мешок-сильфон. Количество масла, закачиваемого рабочим поршнем под диафрагму, должно обеспечивать необходимую величину перемещения диафрагмы, зависящую от условий эксплуатации. Специальное клапанное устройство, связанное с движением диафрагмы насоса, автоматически регулирует объем закачиваемого масла. При лишнем количестве масла толкатель диафрагмы открывает клапан сброса масла, при недостаточном — клапан поступления масла. Шариковые всасывающий и нагнетательный клапаны, диафрагменного насоса смонтированы в его головке. В этой же головке закреплены всасывающий и нагнетательный патрубки с пескоотделителем. Добываемая жидкость поступает к всасывающему патрубку через фильтр. Электродвигатель оснащен кабельным вводом для подсоединения специального кабеля. Система разборных уплотнений герметизирует основные узлы агрегата, упрощая его ремонт.
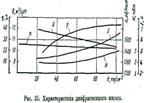
Конструкция диафрагмы, ее закрепление, состав материала тщательно экспериментально отрабатывались. Диафрагма изготовляется из резины на основе нитрильных каучуков, минимальная толщина ее стенки около 2 мм. Ход диафрагмы — около 2,5 мм. Расчетное число циклов работы диафрагмы—400×106. Незначительный перепад давления, воспринимаемый диафрагмой, создает условия для ее длительной непрерывной работы. Величина хода диафрагмы около 2,5 мм определяется величиной перемещения плунжера, равной 16 мм при диаметре 29 мм. Шариковые клапаны насоса работают в тяжелых условиях (большое число ходов, высокое содержание абразивных частиц в перекачиваемой жидкости). Характеристика испытанного насоса приведена на рис. 25.
Высокая долговечность глубинного диафрагменного насоса, связанная с герметизацией его рабочих органов, а также его рабочие характеристики определяют возможность применения оборудования в скважинах с высоким содержанием мехпримесей в добываемой жидкости с небольшими отборами и высокими уровнями. Видимо, также целесообразно будет применение диафрагменных насосов для откачки высоко агрессивных жидкостей.
Одновременно установками диафрагменных насосов эксплуатировалось не более трех скважин.
В результате отработки конструкции узлов насоса в настоящее время максимальный межремонтный период установок диафрагменного насоса достиг 220 сут.
Имелись зарегистрированные межремонтные периоды порядка 150—180 сут. Основной причиной подъема насосов являлся износ их клапанных узлов.
По сравнению с межремонтными периодами работы установок глубинных штанговых насосов в этих же скважинах достигнуто в отдельных случаях десятикратное и более увеличение величины межремонтного периода.
Положительные итоги испытаний создают возможность промышленного применения отечественных диафрагменных насосов.
Не нашли, что искали? Воспользуйтесь поиском по сайту:
©2015 - 2025 stydopedia.ru Все материалы защищены законодательством РФ.
|