Результаты измерений удельного сопротивления слитка четырехзондовым методом
Торец 1 слитка
| Торец 2 слитка
|
|
|
|
|
|
|
|
|
|
|
|
| Ом·см
| Ом·см
|
|
|
|
|
|
|
|
|
|
|
|
| =
| =
| =
| =
| =
| =
| =
| =
|
2.9. При обработке результатов измерений в измерительном блоке установки применяется цифровая фильтрация сигналов. Это уменьшает влияние внешних электромагнитных помех, кратковременного ухудшения контакта зондов с образцом и т.д. Но, с другой стороны, это увеличивает время установления правильных результатов измерения. Поэтому, чем дольше зонды контактируют с образцом, тем точнее производятся измерения.
2.10. При переходе установки в режим ожидания, режимы измерений (тип головки, тип электропроводности и последний используемый диапазон тока) запоминаются и сохраняются после выключения питания установки.
ВНИМАНИЕ! При проведении измерений УЭС четырехзондовым методом, образец должен находиться на диэлектрической поверхности! Не использовать металлический столик!
2.11. Для образцов кремния определить концентрацию примесных атомов. Воспользоваться графиком зависимости ρ(Nпр) (рис. 7), построенным на основе большого числа измерений проводимости образцов кремния, и широко используемым в полупроводниковой промышленности.
Сформулировать выводы по работе.
Подготовить отчет по работе.
Контрольные вопросы.
1. Какие параметры полупроводника называют фундаментальными? Приведите примеры таких параметров.
2. Какие параметры полупроводников называют характеристическими?
3. Что указывается в методических инструкциях, которыми руководствуются ОТК заводов, при контроле качества выпускаемых промышленностью полупроводниковых материалов?
4. В чем состоит принцип четырехзондового метода измерения удельного сопротивления?
5. Каким образом учитывается краевой эффект при измерении удельного сопротивления четырехзондовым методом?
6. Из каких материалов изготавливают зонды при использовании зондовых методов измерения удельного сопротивления?
7. Чем обусловлена наибольшая погрешность четырехзондового метода?
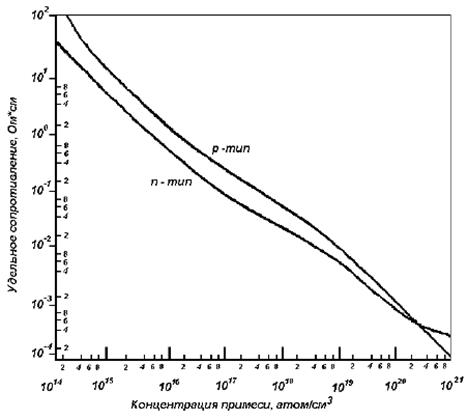
Рис. 7. Зависимость удельного сопротивления кремния при комнатной температуре от концентрации примеси доноров и акцепторов.
Литература.
1. Батавин В.В. Измерение параметров полупроводниковых материалов и структур / В.В. Батавин, Ю. А.Концевой, Ю. В. Федорович - М.: Радио и связь, 1985. - С. 5 - 34.
2. Павлов Л.П. Методы измерения параметров полупроводниковых материалов / Л.П. Павлов. - М.: Высшая школа, 1987. - С. 10 - 32.
3. Зеегер К. Физика полупроводников / К. Зеегер -М.: Мир, 1977. -616 с.
4. Фистуль В.И. Введение в физику полупроводников / В.И. Фистуль. М.: Высшая школа, 1984. – 352 с.
Лабораторная работа №4
Изучение установки для напыления пленок методом термического вакуумного испарения
Целью данной работы является изучение метода термического вакуумного испарения и вакуумной установки типа УВР для осаждения тонких пленок, ее подготовка к процессам вакуумного напыления.
Теоретическая часть.
Метод получения пленок путем испарения вещества в вакууме и последующей его конденсации на подложке, который сокращенно называют методом термического вакуумного испарения (ТВИ), является одним из универсальных методов получения тонких пленок. Он пригоден для получения проводниковых, резистивных, диэлектрических и полупроводниковых пленок испарением неорганических веществ. Процесс происходит в условиях глубокого вакуума, чем обусловлена высокая чистота наносимых пленок.
Возможность контроля и управления как процессом, так и вакуумными условиями обеспечивает воспроизводимость пленок при большой скорости их нанесения. Сущность метода ТВИ поясняет рис. 1.
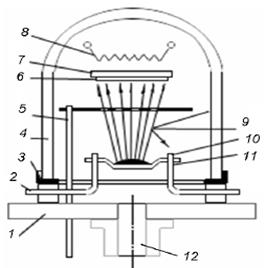
Рис. 1. Схема установки термического вакуумного испарения:
1 – базовая плита; 2 – токопровод; 3 – герметизация колпака; 4 – колпак; 5 – подвижный экран; 6 – подложка; 7 – держатель подложки; 8 – подогреватель; 9 – соударение с молекулой остаточного газа; 10 – испаряемое вещество; 11 – испаритель (тигель, лодочка); 12 – присоединение к вакуумному насосу.
Сущность процесса состоит в переводе осаждаемого материала с помощью нагрева в парогазовую фазу. Образующийся при этом парогазовый поток в высоком вакууме распространяется прямолинейно, так как отсутствует соударение с молекулами остаточного газа – длина свободного пробега молекул в остаточном газе на порядок превышает расстояние от источника до подложки; газ попадает на подложку, поверхность которой холоднее источника пара, При этом происходит конденсация и образование плёнки. Давление остаточных газов составляет 10−8−10−4 Па.
Адгезионную прочность и структурную стабильность обеспечивают чистота и подогрев подложки до 300−600 °С. Адгезионную прочность увеличивают путём нанесения промежуточного слоя с хорошей адгезией к материалу подложки и плёнки. Так, для нанесения плёнки золота на стекло адгезионным подслоем является хром.
Метод ТВИ имеет разновидности, которые различают главным образом по способу нагрева испаренного вещества (резистивное, высокочастотное, электронно-лучевое).
Процесс испарения и качество получаемых плёнок в значительной мере определяются типом и конструкцией испарителей. Существующие испарители можно разбить на две группы: с прямым и косвенным подогревом.
Испарители с прямым нагревом, в которых ток пропускается непосредственно через испаряемый материал. Такой метод испарения имеет основное достоинство – получение особо чистых плёнок, отсутствие загрязнения примесями нагревателя.
Испарители с косвенным подогревом подразделяются на:
– резистивные, в которых тепло выделяется при пропускании тока через нагреватель;
– индукционные, в которых испаряемый материал нагревается вихревыми токами;
– электронно-лучевые, в которых для испарения материала используется энергия электронного луча;
– дуговые, в которых для испарения вещества используется дуговой разряд.
Резистивные испарители косвенного подогрева более универсальны, так как позволяют испарять проводящие и непроводящие материалы в различном виде (гранулы, ленты, проволоки). Однако при этом получаются менее чистые плёнки из-за испарения материала нагревателя.
В качестве материалов нагревателей применяются тугоплавкие металлы: W, Mo, Ta. В зависимости от вида испаряемого материала испарителям придают форму лодочек или неглубоких тиглей. Для испарения порошкообразных материалов применяют испарители в виде лодочек с сетчаток крышкой, которая предотвращает разбрасывание материала вследствие образования повышенного давления пара в месте контакта испаряемого материала и нагревателя. Для нанесения плёнок Ti, Ni, Fe такие испарители малопригодны, так как эти металлы вступают в химическое взаимодействие с материалом испарителя.
Параметрами процесса являются температура испарителя и определяемая ею плотность потока пара, скорость напыления, зависящая как от температуры испарителя, так и от взаимного расположения испарителя и подложки, температура подложки, давление остаточных газов в камере. Распределение испаряемых частиц по скорости и по энергии описывается функцией Максвелла-Больцмана. При этом средняя скорость частиц равна:
(1)
а средняя кинетическая энергия частиц:
(2)
где k - постоянная Больцмана, T - температура вещества в испарителе, m - масса частицы.
Вакуумные условия в рабочей камере должны обеспечивать формирование чистых пленок испаряемого вещества. Для этого достаточно, в первом приближении, чтобы в пролетном пространстве испаритель-подложка отсутствовало столкновение атомов (молекул) вещества с молекулами остаточного газа. Средняя длина свободного пробега частиц зависит от давления следующим образом:
(3)
где pг - давление газа, dч - эффективный диаметр частиц, примерно равный сумме радиусов двух сталкивающихся частиц, T - температура газа, равная температуре стенок камеры.
Вероятность для молекулы вещества преодолеть расстояние r0 от испарителя до подложки без столкновения с молекулами воздуха:
(4)
Реальный размер r0 в установках вакуумного напыления не превышает 30 см. Исходя из требования отсутствия столкновений в пролетном пространстве, что соответствует величине P - 0,95, достаточно, чтобы давление в камере было pг – 10-3 Па.
Следует учесть также постоянную бомбардировку подложки и растущей пленки молекулами остаточных газов. Остаточные газы вступают в химическое взаимодействие с атомами вещества или адсорбируются, ухудшая адгезию, образуя поры в пленке.
Для подавления мешающего действия остаточных газов следует уменьшить давление в камере и увеличивать скорость напыления. Важными при выборе степени разряжения в рабочей камере являются экономические соображения. Для производственных условий приемлемым является вакуум 1,3*10-4…7*10-5 Па, который достигается относительно простыми откачными средствами; время откачки составляет 1…1,5 часа. Переход к более высокому вакууму потребует недопустимого увеличения длительности откачки или использования более производительных, но и значительно более дорогих средств откачки.
Кроме остаточной атмосферы загрязнения возможны за счет молекул летучих соединений, имеющихся в вакуумной камере. Газ выделяется при прогреве деталей внутрикамерного устройства, при прогреве испаряемого материала; летучие углеводороды поступают из вакуумных насосов. Для уменьшения их влияния используется прогрев и обезгаживание внутрикамерного устройства и испарителей, предварительное испарение вещества; насосы и камера снабжаются ловушками паров масел, поглотителями активных газов. Стабилизация вакуумных условий при напылении является необходимым фактором достижения воспроизводимых свойств пленок.
К основным достоинствам метода следует отнести:
– возможность получения плёночных структур на подложках и ранее нанесенных слоях, изготовленных из самых различных металлов, диэлектриков и полупроводников;
– хорошую адгезию напыляемых плёнок;
– разнообразие методов контроля толщины и скорости нанесения плёнок;
– наличие соответствующей контрольно-измерительной и регулирующей аппаратуры;
– малый уровень загрязнений при проведении технологического процесса;
– наличие достаточно простых методов получения рисунка плёночных структур.
К основным недостаткам метода термического вакуумного испарения следует отнести:
– недостаточную однородность и равномерность осаждаемых плёнок;
– малую адгезию плёнки к подложке.
Краткое описание установки типа УВР и вспомогательных приборов.
Рассмотрим основные характеристики термовакуумной установки типа УВР (УВР-2; УВР-3; УВН-2М2; УРМ.3.279.017; УВН-75Р1), смотри рис. 2. Данные установки периодического действия имеют рабочую камеру, в которой проводятся все стадии технологического процесса. Такие установки еще используются в промышленном производстве, так как они просты по конструкции, легко переналаживаются и довольно дешевы. Тонкие пленки, наносимые на таких установках, обеспечивают необходимое качество и воспроизводимость технических параметров. Производительность установки периодического действия невелика, так как перед каждой очередной загрузкой партии подложек в рабочую камеру напускают атмосферный воздух.
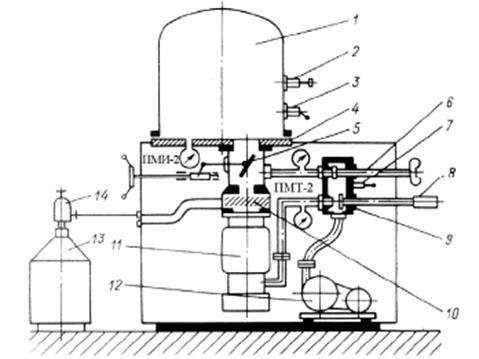
Рис. 2. Схема вакуумной системы установки УВН-2М: 1 – рабочая камера; 2, 7 – вентиль-натекатель; 3 – натекатель; 4 – базовая плита; 5 – затвор; 6, 8 – клапаны; 9 – клапанная коробка; 10 – азотная ловушка; 11 – дифнасос; 12 – форнасос; 13 – сосуд Дьюара; 14 – азотный питатель
В качестве основного средства откачки используется паромасляный диффузионный насос (11) типа Н-2Т. Для предварительной откачки вакуумной системы служит механический вращательный насос (12) типа ВН-7Г. Для предотвращения попадания в рабочую камеру (1) паров масла из диффузионного насоса на впускной фланец последнего устанавливается азотная ловушка (10), питаемая, в данном случае, от выносного сосуда Дьюара (13) с азотным питателем (14). Различные переключения в вакуумной системе осуществляются с помощью клапанной коробки (9) с клапанами (6, 8), а также высоковакуумным затвором (5). Игольчатый вентиль-натекатель (2) служит для дозированной подачи какого-либо газа в рабочую камеру, а натекатель (3) – для напуска воздуха под колпак перед его подъемом. Вентиль-натекатель (7) с электромагнитным приводом предназначен для напуска атмосферного воздуха в механический насос после его остановки и при закрытых клапанах (6, 8). Для измерения давления в различных участках вакуумной системы установлены манометрические лампы: две термопарные – на трубопроводах, соединяющих клапанную коробку с диффузионным насосом и с рабочей камерой, ионизационная – на базовой плите (4) непосредственно под колпаком. Контроль вакуума может осуществляется с помощью прибора ВИТ-2 (ВИТ-1, ВИТ-3), к которому подключены манометрические лампы. При работе всех средств откачки, включая азотную ловушку, под колпаком рабочей камеры установки может быть достигнут предельный вакуум 6,65*10–5 Па. Время достижения предельного вакуума не более 90 мин. Управление подачей тока на испарители, нагреватели осуществляется с помощью ручного управления с блока управления. Контроль толщины слоя металлизации может осуществляется с помощью переносного прибора КИТ-1 при помощи кварцевого резонатора, помещенного внутри установки.
После того, как вакуумная установка подготовлена к работе, внутри камеры (1) сначала создают предварительный низкий вакуум порядка 1,33 Па. Для этого включается форвакуумный насос (12), открывается вентиль (6), а затвор (5) находится в положении (Н) - «низкий вакуум». Величина вакуума контролируется с помощью термопарного вакуумметра ПМТ-2. После достижения необходимого предварительного вакуума, Вентиль (6) закрывается, при этом открывается вентиль (8) затвор (5) устанавливается в положение (В) «высокий вакуум». При этом включается высоковакуумный паромасляный диффузионный насос (11). Давление в системе понижается до высокого вакуума порядка 6*10-5 Па. Величина высокого вакуума контролируется ионизационным вакуумметром ПМИ-2, при этом форвакуумный насос продолжает работать. В форбаллоне поддерживается постоянно пониженное давление порядка 1,33 Па. Это необходимо для уменьшения перепада давления на входе и выходе высоковакуумного насоса, что способствует снижению коэффициента сжатия газа и, следовательно, уменьшению или предотвращению его конденсации. По достижении необходимого рабочего вакуума (6*10-5 Па) в системе можно приступать к напылению.
Величина достигнутого вакуума контролируется с помощью вакуумметра ВИТ-2, состоящего из двух частей: термопарного вакуумметра (для контроля низкого вакуума) и ионизационного вакуумметра (для контроля высокого вакуума).
При работе с термопарными преобразователями чаще всего используется режим постоянства тока накала. На рис. 3 показано устройство преобразователя ПМТ-2. В стеклянной колбе (1) преобразователя на никелевых вводах закреплен платиновый нагреватель (2), к средней точке которого подсоединена хромель-копелевая термопара (3). Постоянство тока накала легко реализуется при питании нагревателя относительно большим напряжением, ограниченным балластным резистором. При изменении давления меняется температура нагревателя, а следовательно, и термо-э.д.с. термопары, по величине которой оценивается давление. На рис. 4 показаны градуировочные кривые преобразователя ПМТ-2 по воздуху и некоторым газам.
Точность измерения давления термопарными преобразователями существенно зависит от правильного подбора тока накала нагревателя. Ток накала нагревателя преобразователя ПМТ-2 можно определить до вскрытия новой лампы, поскольку давление в запаянном манометрическом преобразователе ниже 10–2 Па. При этом теплоотвод по газу от нагревателя пренебрежимо мал, и вся подводимая мощность расходуется на излучение (примерно 63 %) и теплоотвод по вводу (примерно 37 %). Ток нагревателя подбирают таким, чтобы стрелка милливольтметра точно совпадала с сотым делением шкалы; при этом показание миллиамперметра (шкала «ток накала») будет соответствовать рабочему току нагревателя. Рабочий ток различных преобразователей находится в пределах 90–150 мА.
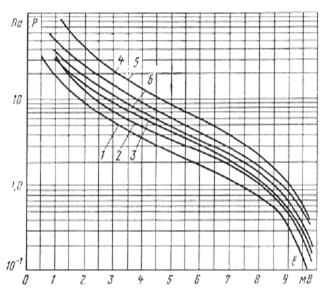
Рис. 3. Термопарный манометрический преобразователь ПМТ-2: 1 – стеклянная колба; 2 – нагреватель; 3 – термопара
| Рис. 4. Градуировочные кривые преобразователя ПМТ-2 по воздуху и некоторым газам: 1 – водород; 2 – воздух; 3 – гелий; 4 – криптон; 5 – аргон; 6 – неон
|
Конструкция наиболее распространенного отечественного электронного ионизационного манометрического преобразователя ПМИ-2 показана на рис. 5. В стеклянном баллоне преобразователя (1) смонтирована трехэлектродная система, состоящая из коллектора ионов (2), анодной сетки (5) и прямонакального катода (4). На анодную сетку относительно катода подается напряжение +200 В, а на цилиндрический коллектор ионов – 50 В. Анодная сетка преобразователя выполнена из вольфрамовой проволоки диаметром 0,2 мм в виде бифилярной спирали. При прогреве преобразователя для обезгаживания по спирали пропускается ток 3 А. Ионизационный преобразователь ПМИ-2 имеет линейную зависимость ионного тока от давления в диапазоне 5*10–6 до 1 Па. Его чувствительность по воздуху составляет 0,173 Па–1. В режиме вакуумметров ВИТ-2 и ВИТ-3 «токовая» чувствительность равна 8,6*10–5 А/Па. В указанном выше рабочем диапазоне давлений ионный ток в цепи коллектора изменяется от 4*10–10 до 10–4 А.
На рис. 6 приведена упрощенная схема ионизационного манометра, входящего в состав измерительного блока ВИТ-3. Катод (1) манометрической лампы ПМИ-2 питается от накального трансформатора Тр1. Электронный стабилизатор тока эмиссии СТЭ, подключенный через трансформатор Тр2 к катоду, автоматически поддерживает постоянным электронный ток лампы ПМИ-2. В цепь коллектора ионов (3) включен усилитель ионного тока УИТ. Усиленный ионный ток, пропорциональный давлению газов в баллоне манометрической лампы, измеряется миллиамперметром mA, для чего переключатель П2 устанавливается в положение «Измерение». Шкала миллиамперметра проградуирована в единицах давления (мм. рт. ст.). Этот же прибор используется для измерения тока эмиссии, часть которого проходит по калиброванному резистору R2. Переключатель П2 при этом устанавливается в положение «Ток эмиссии».
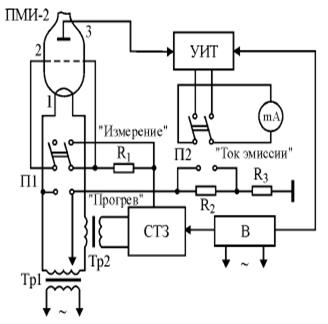
Рис. 5. Электронный ионизационный манометрический преобразователь ПМИ-2
| Рис. 6. Упрощенная схема ионизационного манометра
|
Аноды электронных ламп стабилизатора СТЭ и усилителя УИТ питаются от выпрямителя В. Ионизационный манометр следует включать при давлении в системе, к которой подсоединена лампа ПМИ-2, не выше 0,13 Па. Перед началом измерений в течение 15 мин производится прогрев анода 2 манометрической лампы с целью ее обезгаживания, для чего переключатель П1 устанавливается в положение «Прогрев», и на анод лампы ПМИ-2 подается напряжение от половины обмотки трансформатора Тр1. Ионизационный вакуумметр ВИТ-3 с манометрической лампой ПМИ-2 позволяет измерять давление от 1,3*10–1 до 10–5 Па. Нижний предел давлений, измеряемых лампой ПМИ-2, ограничен фоновым электронным током, не зависящим от давления. Возникновение этого тока обусловлено мягким рентгеновским излучением, испускаемым анодом под действием бомбардировки его электронами, эмитируемыми катодом. Рентгеновское излучение, в свою очередь, выбивает из коллектора электроны, которые и создают фоновый электронный ток в цепи коллектора, имеющий обратное по отношению к ионному току направление. При давлениях 10–5–5*10–6 Па фоновый ток становится сравнимым по величине с ионным током, поэтому величина 10–5 Па является нижним пределом давлений, измеряемых манометрической лампой ПМИ-2.
Подколпачное устройство, рабочий объем установки типа УВР позволяет производить финишную ионную очистку подложек. Для этого имеются необходимые электроды, между которыми возбуждается тлеющий разряд. После очистки производят напыление пленок.
Технологические возможности установки в основном заключаются в напылении элементов одного слоя через трафареты или в напылении двух сплошных слоев (например: резистивного и проводящего с последующей двойной фотолитографией).
Внутрикамерное устройство может включать в себя датчики контроля сопротивления и толщины пленки.
Контроль сопротивления осуществляется с помощью «свидетеля» - контрольной подложки с заранее нанесенными на нее пленочными контактами. Свидетель устанавливается рядом с подложкой и с помощью прижимных контактов подключается к измерительному прибору (рис. 7).
В процессе осаждения резистивного материала на рабочие подложки происходит рост пленки и на «свидетеле». По мере роста пленки сопротивление квадрата уменьшается, соответственно уменьшается сопротивление «свидетеля» Rсв. При достижении некоторого, заранее рассчитанного, Rсв напыление прекращается. Сопротивление рассчитывается по следующей формуле:
(5)
где: Lсв и Bсв - расстояние между контактами и ширина свидетеля; R0- заданное расчетное значение удельного поверхностного сопротивления (сопротивление квадрата из конструкторских расчетов резисторов микросхемы), Ом; d - температурный коэффициент сопротивления резистивного материала, 1/град; DТ - разность значений температуры подложки при напылении и комнатной температурой, град.
Прибор КС-2 измеряет сопротивление в диапазоне до 1 МОм с погрешностью до 5% и одновременно фиксирует время напыления.
Толщину осаждаемой пленки можно контролировать с помощью кварцевого измерителя толщины. Кварцевый измеритель толщины (КИТ) контролирует определенную толщину как металлических, так и диэлектрических материалов косвенным способом. Принцип его работы основан на зависимости резонансной частоты кварцевого резонатора от массы, осаждённой на кристалл пленки.
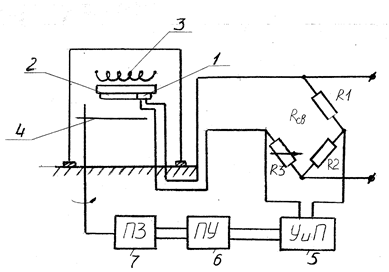
Рис. 7. Функциональная схема контроля пленок методом свидетеля
Кварцевый датчик-резонатор представляет собой определенный срез монокристалла кварца в виде пластины, заключенной между металлическими контактами (рис.8, а).
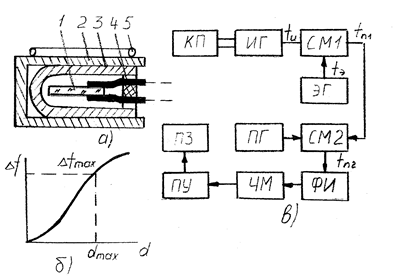
Рис. 8. Кварцевый измеритель толщины: а) - кварцевый резонатор;
б) - градуировочный график; в) - блок - схема прибора КИТ-1
При толщине пленки не более 1% от толщины кварцевой пластины справедливо равенство:
(6)
где: f0- резонансная частота кварца, Гц; Df - изменение частоты кварца, вызванное накоплением материала осажденного слоя на грани кварца, Гц; К - плотность кварцевого кристалла, кг-м ; dк- начальная толщина кварцевой пластины, м; γпл - плотность осажденного материала пленки, толщина осажденной пленки, м.
Выражение (1) перепишем в следующем виде:
(7)
где - постоянная данного прибора, характеризующая чувствительность, Гц ´ м 2 /кг.
Известно, что толщина пленки при осаждении в вакууме обратно пропорциональна квадрату расстояния от испарителя до приемной поверхности. Поэтому, задавая по шкале прибора частотный сдвиг, нужно учесть, что расстояние от испарителя до подложки Lп не равно расстоянию от испарителя до кварцевой пластины Lк
Поэтому:
(8)
Если массовая плотность пленки γпл постоянная величина, то имеет место линейная зависимость Df = j(dпл).
При вакуумном осаждении плотность пленки зависит от условий осаждения и не поддается предварительному расчету. Поэтому на практике обычно используют тарировочный график Df = j(dпл) (рис. 8б), который строят экспериментально для каждого вида напыляемого материала и конкретных условий напыления с применением оптических средств измерения. Наиболее крутой участок графика соответствует наивысшей чувствительности прибора и определяет максимальную суммарную толщину пленки d max после которой нанесенная пленка должна быть удалена с кварца с помощью избирательного травителя. Чувствительность прибора можно измерять в (нм/Гц) и определять по графику.
Для таких приборов, как КИТ-1, КИТ-2 Cf = 106 Гц*м2/кг. Структурная схема прибора КИТ-2 приведена на рис. 8 в. Кварцевый датчик размещается в вакуумной камере над испарителем и входит в состав измерительного генератора. Частота измерительного генератора, снижающаяся по мере напыления пленки, сравнивается с частотой эталонного генератора. Путем последовательных преобразований по мере достижения ее частоты, соответствующей заданной толщине пленки (в соответствии с тарировочным графиком), срабатывает привод заслонки. Напыление прекращается.
Частотный метод контроля можно применять в процессе термического вакуумного напыления, когда в рабочем объеме отсутствуют заряженные частицы, способные создавать помехи. Более универсальным является бесконтактный фотометрический метод контроля толщины пленки. Он основан на зондировании растущей пленки лучом лазера, анализе интерференционной картины света, отраженного от системы «подложка – пленка» и от системы «рабочая среда – пленка». Коэффициент отражения линейно поляризованного света в такой системе зависит от толщины пленки и изменяется периодически. Количество всплесков для данной длины волны света будет пропорционально толщине пленки. Оно определяется по калибровочной кривой и заранее предусматривается. По достижении нужной толщины сигнал подается на исполнительное устройство, прерывающее процесс осаждения.
Не нашли, что искали? Воспользуйтесь поиском по сайту:
©2015 - 2025 stydopedia.ru Все материалы защищены законодательством РФ.
|