И расчет допускаемых напряжений
Расчет зубчатых передач редуктора
Выбор материала зубчатых колес
и расчет допускаемых напряжений
2.1.1 Зубчатые колеса изготовляют из термически обработанных сталей различных марок, которые по критерию прирабатываемости делят на две группы: с поверхностной твердостью по Бринеллю до 350НВ и выше 350НВ.
Заготовки из сталей первой группы (<350НВ) подвергаются объемной термообработке в виде нормализации или улучшения. Зубья таких колес хорошо прирабатываются со временем. Для более равномерного изнашивания твердость зубьев шестерни назначают на 20 ... 50 НВ выше твердости зубьев колеса.
Твердость сталей второй группы (>350НВ) принято измерять в единицах Роквелла, HRC (1 HRC » 10 НВ). Ввиду высокой твердости нарезание зубьев из сталей этой группы производят до процедуры поверхностной термообработки, а после нее зубья дополнительно шлифуют.
Материал зубчатых колес выбирают по табл. 3, исходя из доступности и стоимости той или иной марки стали, условий прирабатываемости, принятого варианта термической обработки (т.о.) и других соображений.
В практике машиностроения можно выделить пять типовых вариантов термической обработки деталей закрытых передач:
Вариант I.Т.о. шестерни – улучшение, твердость 269 ... 302 НВ; т.о. колеса – улучшение, твердость 235 ... 262 НВ. Марки сталей одинаковы для зубчатой пары: 45, 40Х, 40ХН, 35ХМ и др. Данному варианту свойственны хорошая прирабатываемость зубьев, отсутствие хрупкого разрушения, но сравнительно невысокая нагрузочная способность.
Вариант II.Т.о. шестерни – улучшение и закалка токами высокой частоты (ТВЧ), твердость поверхности, в зависимости от выбранной марки стали, 45 ... 58 HRC, 48 ... 55 HRC; т.о. колеса – улучшение, твердость 269 ... 302 НВ. Марки сталей одинаковы для зубчатой пары: 40Х, 40ХН, 35ХМ и др.
Таблица 3
Марка
стали
| Термо-обработка
| Предельные размеры заготовки, мм
| Твердость зубьев
| , МПа
| , МПа
|
|
| сердцевина
| поверхность
| Закрытые передачи
|
| улучшение
улучшение
|
|
| 235...262 НВ
269...302 НВ
| 235...262 НВ
269...302 НВ
|
|
| 40Х
| улучшение
улучшение
улучшение +
закалка ТВЧ
|
|
| 235...262 НВ
269...302 НВ
269...302 НВ
| 235...262 НВ
269...302 НВ
45...58 HRC
|
|
| 40ХН,
35ХМ
| улучшение
улучшение
улучшение +
закалка ТВЧ
|
|
| 235...262 НВ
269...302 НВ
269...302 НВ
| 235...262 НВ
269...302 НВ
48...55 HRC
|
|
| 40ХН2МА,
38Х2МЮА
| улучшение + азотирование
|
|
| 269...302 НВ
| 58...67 HRC
|
|
| 20Х,
20ХН2М,
18ХГТ,
12ХН3А,
25ХГР
| улучшение + цементация и закалка
|
|
| 300...400 НВ
| 56...63 HRC
|
|
| Открытые передачи
|
| улучшение
|
|
| 192...228 НВ
| 192...228 НВ
|
|
|
| нормализация
| любые
| 179...207 НВ
| 179...207 НВ
|
|
| 35Л
| нормализация
| любые
| 163...207 НВ
| 163...207 НВ
|
|
| 45Л
| улучшение
|
|
| 207...235 НВ
| 207...235 НВ
|
|
| 40ГЛ
| улучшение
|
|
| 235...262 НВ
| 235...262 НВ
|
|
|
Вариант III.Т.о. шестерни и колеса одинаковая – улучшение и закалка ТВЧ, твердость поверхности, в зависимости от выбранной марки стали, 45 ... 58 HRC, 48 ... 55 HRC. Марки сталей одинаковы для зубчатой пары: 40Х, 40ХН, 35ХМ и др.
Вариант IV.Т.о. шестерни – улучшение, цементация и закалка, твердость поверхности 56 ... 63 HRC, марки сталей для шестерни – 20Х, 20ХН2М, 18ХГТ, 12ХН3А и др.; т.о. колеса – улучшение и закалка ТВЧ, твердость поверхности, в зависимости от выбранной марки стали, 45 ... 58 HRC, 48 ... 55 HRC, марки сталей – 40Х, 40ХН, 35ХМ и др.
Вариант V.Т.о. шестерни и колеса одинаковая – улучшение, цементация и закалка, твердость поверхности 56 ... 63 HRC. Марки сталей одинаковы для зубчатой пары: 20Х, 20ХН2М, 18ХГТ, 12ХН3А, 25ХГР и др. Вместо цементации может быть применена нитроцементация (для 25ХГР и 30ХГТ, твердость поверхности 56 ... 63 HRC) и азотирование (для 38Х2МЮА, 40ХН2МА, твердость поверхности 58 ... 67 HRC).
Для учебных проектов рекомендуется выбирать более простые и дешевые варианты термообработки, к примеру, вариант I. Определившись с вариантом, выбирают конкретный материал для шестерни и колеса и выписывают данные из табл. 3 в табличную форму:
Колесо
| Марка
стали
| Вид т.о.
| Средняя
твердость
поверхности
| , МПа
| , МПа
| , МПа
|
расчетное, МПа
| , МПа
| 1 (ш)
|
|
|
|
|
|
|
|
| 2 (к)
|
|
|
|
|
|
|
| 3 (ш)
|
|
|
|
|
|
|
|
| 4 (к)
|
|
|
|
|
|
|
|
В качестве средней твердости в условиях неопределенности берут некоторое среднее значение между границами предлагаемого интервала поверхностной твердости зубьев. Три последних столбца формы заполняют по мере вычисления допускаемых напряжений.
Замечание. Предельные размеры заготовок, фигурирующие в табл. 3, обеспечивают получение требуемых механических характеристик шестерен и колес в ходе термической обработки. Соответствующие условия имеют вид (рис. 2):
; .

Рис. 2. Размеры заготовок (слева – шестерен, справа – колеса)
2.1.2 Допускаемые контактные напряжения рассчитывают отдельно для каждой шестерни или колеса по формуле
. (6)
Параметры, входящие в формулу (6), определяют по описанной ниже процедуре.
Предел выносливости для базового числа циклов нагружения зависит от средней твердости поверхностей зубьев колес и вычисляется по эмпирическим формулам, приведенным в последнем столбце табл. 4.
Таблица 4
Вид т.о.
| Средняя твердость поверхности зубьев
| Сталь
| , МПа
| Нормализация, улучшение
| < 350 НВ
| Углеродистая и легированная
| 2´НВ + 70
| Поверхностная и объемная закалка
| 40 ... 56 HRC
| Углеродистая и легированная
| 17´HRC + 200
| Цементация, нитроцементация
| > 56 HRC
| Легированная
| 23´HRC
| Азотирование
| > 52 HRC
| Легированная
|
|
Коэффициент запаса прочности зависит от структуры материала. При однородной структуре, свойственной объемной термообработке, принимают 1,1, а при поверхностном упрочнении (закалка ТВЧ, цементирование, азотирование) принимают 1,2.
Коэффициент долговечности зависит от ресурса передачи и параметров графика нагружения (рис. 3). Для его определения вначале находят временной ресурс – срок работы передачи, выраженный в часах:
(срок службы, лет) 365 дней 24 час, (7)
где и – суточный и годовой коэффициенты использования передачи, обычно фиксируемые в техническом задании.
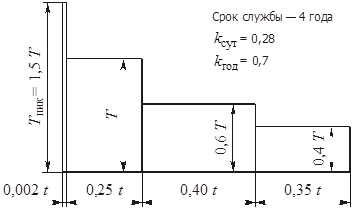
Рис. 3. График нагружения
Далее определяют эквивалентное число циклов изменения контактных напряжений:
, (8)
где – частота вращения конкретного зубчатого колеса; суммирование ведут по участкам графика, соответствующим длительно действующей нагрузке, при этом кратковременное действие пиковых нагрузок (первый узкий участок) не учитывают. К примеру, для графика на рис. 3 формула (8) приводится к виду:
.
Определяют базовое число циклов напряжений, соответствующее пределу выносливости, по формуле
.
При расчете колес, твердость поверхности зубьев которых выражена в единицах Роквелла, производят ее пересчет в единицы Бринелля: 1 HRC » 10 НВ. Неравенство в правой части записанной формулы является ограничением. Если результат вычисления превысит это значение, следует принять .
Находят коэффициент долговечности. Если ,
.
При 
.
Полученный результат должен лежать в пределах
,
где 2,6 для материалов с однородной структурой и 1,8 для поверхностно упрочненных материалов. При выходе из указанного интервала в качестве принимают соответствующее граничное значение.
Коэффициент учитывает влияние шероховатости рабочих поверхностей зубьев:
1 для шлифованных и полированных зубьев при показателе шероховатости 0,63 ... 1,25 мкм;
0,95 при 1,25 ... 2,5 мкм;
0,95 при 10 ... 40 мкм.
Коэффициент , учитывает влияние окружной скорости и выбирается из диапазона . Меньшие значения назначают для более твердых поверхностей зубьев при малых окружных скоростях ( 5 м/с).
При проектном расчете среднескоростных передач 6 – 8 степени точности допускается принимать 1.
Контактные напряжения, в отличие от изгибных, имеют отношение не к отдельному колесу, а к зубчатой паре. Поэтому при расчете на контактную прочность пользуются понятием расчетного допускаемого контактного напряжения . При небольшой разнице в поверхностной твердости шестерни и колеса определяется как меньшее из двух значений и . Если же разница в твердости поверхностей зубьев превышает 70 ... 80 НВ, в качестве принимают меньшее из следующих двух значений:
; .
В случае конической передачи в последнем равенстве вместо множителя 1,23 берут 1,15.
2.1.3 Допускаемые напряжения изгиба рассчитывают для каждой шестерни или колеса по формуле
. (9)
Значения предела выносливости для базового числа циклов нагружения, а также коэффициента запаса прочности приведены в табл. 5.
Коэффициент долговечности учитывает влияние ресурса. Для его определения вначале находят эквивалентное число циклов изменения изгибных напряжений:
, (10)
где показатель 6 для колес с поверхностной твердостью менее 350 НВ и 9 при твердости выше 350 НВ. Далее, коэффициент долговечности определяется формулой:
,
где базовое число циклов, соответствующее пределу выносливости, .
Таблица 5
Вид т.о.
| Средняя твердость
|
| , МПа
| сердц.
| поверхн.
| поковка
| литье
| Нормализация, улучшение
| < 350 НВ
| < 350 НВ
| 1,7
| 2,2
| 1,75´НВ
| Закалка ТВЧ по контуру зубьев
| 25...35 HRC
| 48...58 HRC
| 1,7
| 2,2
| 600 ... 700
| Закалка ТВЧ сквозная, m <3 мм
| 48...55 HRC
| 48...55 HRC
| 1,7
| 2,2
| 500 ... 600
| Цементация
| 30...45 HRC
| 56...63 HRC
| 1,55
| 1,9
| 750 ... 800
| Цементация с автоматич. регулир. процесса
| 30...45 HRC
| 56...63 HRC
| 1,55
| 1,9
| 850 ... 950
| Азотирование
| 24...40 HRC
| 58...67 HRC
| 1,55
| 1,9
| 12´HRCсердц+ +290
|
Найденное значение должно лежать в пределах
,
где 4 для материалов с поверхностной твердостью менее 350 НВ и 2,5 для материалов с поверхностной твердостью выше 350 НВ. При выходе из указанного интервала в качестве принимают соответствующее граничное значение.
Коэффициент учитывает влияние шероховатости переходной поверхности между зубьями, на которой возможно зарождение усталостной трещины:
1 для шлифованных или фрезерованных поверхностей с параметром шероховатости 40 мкм;
1,05 ... 1,2 для полированных поверхностей. Бóльшие значения назначают при улучшении и после закалки ТВЧ.
Коэффициент учитывает влияние реверса. Для нереверсивных передач принимают 1. Для реверсивных передач при одинаковой нагрузке и числе циклов нагружения в прямом и обратном направлении принимают:
0,65 для нормализованных и улучшенных сталей;
0,75 для закаленных и цементированных поверхностей зубьев;
0,9 для азотированных поверхностей.
Не нашли, что искали? Воспользуйтесь поиском по сайту:
©2015 - 2025 stydopedia.ru Все материалы защищены законодательством РФ.
|