|
Условные силы, действующие на шатунные шейки коленчатого вала от двух смежных шатунов
Коленчатый вал двигателя полноопорный с кривошипами, расположенными в вертикальной и горизонтальной плоскостях. Порядок работы двигателя 1-5-4-2-6-3-7-8. Чередование вспышек равномерное через 90˚.
В соответствии с порядком работы двигателя на 1, 2 и 3-ю шатунные шейки одновременно действуют силы от левого и правого шатунов, смещенные одна относительно другой на 90˚, а на 4-ю шейку действуют силы от левого и правого шатунов, смещенные на 450˚.
Суммарные тангенциальные силы, действующие на шатунные шейки от двух смежных шатунов: .
Суммарные силы, действующие на шатунные шейки по радиусу кривошипа от двух смежных шатунов: .
Условные суммарные силы, действующие на шатунные шейки, строят при условии, что во всех левых цилиндрах отсчет углов начинается от 0˚. Силы TΣ и KΣ рассчитываем табличным методом (табл. 6.3).
Таблица 6.3
Левые цилиндры
| 1 (2, 3)-й правый цилиндр
| 1 (2, 3)-я шатунная шейка
| 4-й правый цилиндр
| 4-я шатунная шейка
| φ˚
| Kл, Н
| Tл, Н
| φ˚п1
| Kп1, Н
| Tп1, Н
| KΣ1, Н
| TΣ1, Н
| Rш.шΣ1(2,3), Н
| RкΣ1(2,3), Н
| φ˚п4
| Kп4, Н
| Tп4, Н
| KΣ4, Н
| TΣ4, Н
| Rш.шΣ4, Н
| RкΣ4, Н
|
| -16483
|
|
| -1000
| -3567
| -17483
| -3567
|
|
|
| -1275
| -4547
| -17758
| -4547
|
|
|
| -10481
| -8118
|
| -1371
|
| -11852
| -3482
|
|
|
| -257,3
| 869,8
| -10738
| -7248
|
|
|
| -1416
| -4788
|
| -10357
|
| -11774
|
|
|
|
| 511,98
| -397
| -904,4
| -5185
|
|
|
| -956,8
|
|
| -16483
|
| -17439
|
|
|
|
|
|
|
|
|
|
|
| -2432
|
|
| -15748
| -3545
| -18180
|
|
|
|
|
|
|
|
|
|
|
| -4144
|
|
| -13600
| -6428
| -17744
| -442
|
|
|
|
|
|
|
|
|
|
| -5782
|
|
| -10481
| -8118
| -16263
| -2029
|
|
|
|
|
|
|
|
|
|
| -8794
|
|
| -1416
| -4788
| -10210
| -1192
|
|
|
| 3204,9
|
| -5589
|
|
|
|
| -9401
|
|
| -956,8
|
| -10357
|
|
|
|
| -3011
|
| -12412
|
|
|
|
| -8842
| -3616
|
| -5782
|
| -14625
|
|
|
|
| -8962
|
| -17804
|
|
|
|
| -6002
| -6319
|
| -8794
|
| -14796
| -2723
|
|
|
| -12024
|
| -18025
| -1402
|
|
|
| -1275
| -4547
|
| -9401
|
| -10676
| -4547
|
|
|
| -11052
|
| -12327
| -4547
|
|
|
| -257,3
| 869,8
|
| -8842
| -3616
| -9100
| -2746
|
|
|
| -9132
| -3734
| -9389
| -2864
|
|
|
| 511,98
| -397
|
| -6002
| -6319
| -5490
| -6716
|
|
|
| -5892
| -6204
| -5380
| -6600
|
|
|
|
|
|
| -1275
| -4547
|
| -4547
|
|
|
| -1000
| -3567
|
| -3567
|
|
|
|
|
|
| -257,3
| 869,8
|
|
|
|
|
| -107,2
| -1130
|
|
|
|
|
|
|
|
| -1001
|
|
|
|
|
|
| -163,2
|
|
|
|
|
|
|
|
|
| -1183
|
|
|
|
|
|
| -1371
|
|
|
|
|
|
| 3204,9
|
|
|
| -396,5
|
|
|
|
|
| -10357
|
| -7152
|
|
|
|
| -3011
|
|
|
|
|
|
|
|
|
| -16483
|
| -19494
|
|
|
|
| -5235
|
|
|
|
|
|
|
|
|
| -15748
| -3545
| -20983
|
|
|
|
| -7242
|
|
|
|
|
|
|
|
|
| -13600
| -6428
| -20842
|
|
|
|
| -8962
|
|
|
|
|
|
|
|
|
| -10481
| -8118
| -19443
|
|
|
|
| -12024
|
|
|
|
| -8819
|
|
|
|
| -1416
| -4788
| -13440
| 128,4
|
|
|
| -11052
|
|
| -3011
|
| -14063
|
|
|
|
| -956,8
|
| -12009
|
|
|
|
| -9132
| -3734
|
| -8962
|
| -18093
|
|
|
|
| -5782
|
| -14914
|
|
|
|
| -5892
| -6204
|
| -12024
|
| -17916
| -1287
|
|
|
| -8794
|
| -14686
| -2608
|
|
|
| -1000
| -3567
|
| -11052
|
| -12052
| -3567
|
|
|
| -9401
|
| -10401
| -3567
|
|
|
| -1371
|
|
| -9132
| -3734
| -10503
| 901,6
|
|
|
| -8842
| -3616
| -10214
|
|
|
|
| -10357
|
|
| -5892
| -6204
| -16249
|
|
|
|
| -6002
| -6319
| -16359
|
|
|
|
| -16483
|
|
| -1000
| -3567
| -17483
| -3567
|
|
|
| -1275
| -4547
| -17758
| -4547
|
|
| По полученным данным строим условные полярные диаграммы суммарных сил , действующих на 1 (2, 3)-ю и 4-ю шатунные шейки от каждой пары смежных шатунов. Масштаб диаграмм .
Диаграммы сил SΣ1(2,3) и SΣ4 с центрами в точках Oш1(2,3) и Oш4 являются соответственно полярными диаграммами условных нагрузок на 1, 2 и 3-ю шатунные шейки – Rш.шΣ1(2,3) и на 4-ю шатунную шейку - Rш.шΣ4.
Значения сил Rш.шΣ1(2,3) и Rш.шΣ4 для различных φ заносим в таблицу 6.3 и по ним строим диаграммы Rш.шΣ1(2,3) и Rш.шΣ4 в прямоугольных координатах. Масштабы развернутой диаграммы: и .
По развернутым диаграммам определяем:
; ; ;
; ; ,
где OB – длина диаграммы, мм; F – площадь под кривой Rш.ш, мм2.
По полярной диаграмме строим диаграмму износа 1-ой шатунной шейки. Сумму сил Rш.шi, действующих по каждому лучу диаграммы износа (от 1 до 12), определяем с помощью таблицы 6.4. По данным таблицы 6.4 в масштабе по каждому лучу откладываем величины суммарных сил ΣRш.шi в мм от окружности к центру. По диаграмме износа определяем положение оси масляного отверстия φм=90˚.
Таблица 6.4
Rш.шi
| Значения Rш.шi, Н, для лучей
|
|
|
|
|
|
|
|
|
|
|
|
| Rш.ш0
|
|
|
| -
| -
| -
| -
| -
| -
| -
| -
|
| Rш.ш30
|
|
|
| -
| -
| -
| -
| -
| -
| -
| -
|
| Rш.ш60
|
|
| -
| -
| -
| -
| -
| -
| -
| -
|
|
| Rш.ш90
|
|
| -
| -
| -
| -
| -
| -
| -
| -
|
|
| Rш.ш120
|
|
|
| -
| -
| -
| -
| -
| -
| -
| -
|
| Rш.ш150
|
|
|
| -
| -
| -
| -
| -
| -
| -
| -
|
| Rш.ш180
|
|
| -
| -
| -
| -
| -
| -
| -
| -
|
|
| Rш.ш210
|
|
| -
| -
| -
| -
| -
| -
| -
| -
|
|
| Rш.ш240
|
|
|
| -
| -
| -
| -
| -
| -
| -
| -
|
| Rш.ш270
|
|
|
| -
| -
| -
| -
| -
| -
| -
| -
|
| Rш.ш300
|
|
|
| -
| -
| -
| -
| -
| -
| -
| -
|
| Rш.ш330
|
|
|
| -
| -
| -
| -
| -
| -
| -
| -
|
| Rш.ш360
| -
| -
| -
| -
|
|
|
|
| -
| -
| -
| -
| Rш.ш370
| -
| -
| -
|
| -
|
|
|
|
| -
| -
| -
| Rш.ш380
| -
| -
| -
|
| -
| -
|
|
|
|
| -
| -
| Rш.ш390
| -
| -
| -
| -
| -
| -
| -
|
|
|
|
| -
| Rш.ш420
|
| -
| -
| -
| -
| -
| -
| -
| -
|
|
|
| Rш.ш450
| -
| -
| -
| -
| -
|
|
|
|
| -
| -
| -
| Rш.ш460
| -
| -
| -
| -
| -
|
|
|
|
| -
| -
| -
| Rш.ш470
| -
| -
| -
| -
| -
| -
|
|
|
|
|
| -
| Rш.ш480
| -
| -
| -
| -
| -
| -
| -
|
|
|
|
| -
| Rш.ш510
|
| -
| -
| -
| -
| -
| -
| -
| -
|
|
|
| Rш.ш540
|
|
| -
| -
| -
| -
| -
| -
| -
| -
|
|
| Rш.ш570
|
|
| -
| -
| -
| -
| -
| -
| -
| -
|
|
| Rш.ш600
|
|
|
| -
| -
| -
| -
| -
| -
| -
| -
|
| Rш.ш630
|
|
|
| -
| -
| -
| -
| -
| -
| -
| -
|
| Rш.ш660
|
|
| -
| -
| -
| -
| -
| -
| -
| -
|
|
| Rш.ш690
|
|
| -
| -
| -
| -
| -
| -
| -
| -
|
|
| ΣRш.шi
|
|
|
|
|
|
|
|
|
|
|
|
|
Силы, действующие на колена вала
Суммарные силы, действующие на колена вала по радиусу кривошипа: .
Полярные диаграммы сил Rш.шΣ1(2,3) и Rш.шΣ4 с центрами в точках Oк1(2,3) и Oк4 являются соответственно полярными диаграммами нагрузок на колена вала RкΣ1(2,3) и RкΣ4. Значения RкΣ1(2,3) и RкΣ4 для различных φ заносим в табл. 6.3.
Уравновешивание
Проектируемый однорядный шестицилиндровый двигатель имеет следующий порядок работы цилиндров: 1-5-4-2-6-3-7-8. Промежутки между вспышками равны 90˚. Угол развала цилиндров γ=90˚. Коленчатый вал имеет кривошипы, расположенные в двух взаимно перпендикулярных плоскостях (рис. 7.1).
Силы инерции первого порядка взаимно уравновешиваются . Суммарный момент этих сил действует во вращающейся плоскости, составляющей с плоскостью первого кривошипа угол 18˚26’: ,
где a =253 мм – расстояние между центрами шатунных шеек.
Равнодействующие сил инерции второго порядка для каждой секции двигателя всегда направлены по горизонтали перпендикулярно оси коленчатого вала. Сумма этих равнодействующих сил равна нулю: .
Суммарный момент сил инерции второго порядка также равен нулю: . Центробежные силы инерции для всех секций равны и направлены попарно в разные стороны. Равнодействующая этих сил .
Суммарный момент центробежных сил действует в той же плоскости, что и равнодействующий момент сил инерции первого порядка :

Уравновешивание моментов и осуществляется путем установки двух противовесов на концах коленчатого вала в плоскости действия моментов, т.е. под углом 18˚26’. Это приводит к возникновению дополнительных центробежных сил инерции масс противовесов, передающих свое усилие на 1-ю и 5-ю коренные шейки вала.
Расчет деталей двигателя
Расчет поршня
Поршень воспринимает высокие газовые, инерционные и тепловые нагрузки. Его основными функциями являются уплотнение внутрицилиндрового пространства и передачи газовых сил давления кривошипно-шатунному механизму.
Поверочный расчет элементов поршня осуществляется без учета переменных нагрузок, величина которых учитывается при установлении соответствующих допускаемых напряжений.
На основании данных расчетов (теплового, скоростной характеристики и динамического) получили: диаметр цилиндра D=128 мм, ход поршня S=128 мм, максимальное давление сгорания pZ=8,56 МПа при nN=2200 об/мин, площадь поршня Fп=129 см2, наибольшую нормальную силу при φ=380˚, массу поршневой группы , частоту вращения nх.х.max=2100 об/мин и λ=0,27.
С учетом соотношений, приведенных в табл. 12.1 [1], принимаем: толщину днища поршня δ=19 мм, высоту поршня H=160 мм, высоту юбки поршня hю=83 мм, радиальную толщину кольца t=5,4 мм, радиальный зазор кольца в канавке поршня Δt=0,8 мм, толщину стенки головки поршня s=10 мм, толщину верхней кольцевой перемычки hп=6,4 мм, число и диаметр масляных каналов в поршне nм=8 и dм=1,5 мм (рис. 8.1). Материал поршня – эвтектический алюминиевый сплав с содержанием кремния около 12%, коэффициент линейного расширения αп=22∙10-6 1/К, материал гильзы цилиндра – серый чугун, αц=11∙10-6 1/К.
Напряжения сжатия в сечении x – x:
площадь сечения x – x ,
где , ,
;
максимальная сжимающая сила ,
напряжение сжатия ,
где [σсж]=30-40 МПа – допустимое напряжение на сжатие для алюминиевого поршня.
Напряжения разрыва в сечении x – x:
максимальная угловая скорость холостого хода
;
масса головки поршня с кольцами, расположенными выше сечения x – x
;
максимальная разрывающая сила ;
напряжение разрыва .
Напряжение в верхней кольцевой перемычке:
среза ;
изгиба ;
сложное .
Удельное давление поршня на стенку цилиндра:
;
.
Ускорение приработки юбки поршня, также уменьшение трения и снижения износа пары – юбка поршня – стенка цилиндра – достигается покрытием юбки поршня тонким (0,003 – 0,005 мм) слоем олова, свинца или оловянно-свинцового сплава.
Гарантированная подвижность поршня в цилиндре достигается за счет установления оптимальных диаметральных зазоров между цилиндром и поршнем при их неодинаковом расширении в верхнем сечении головки поршня Δг’ и нижнем сечении юбки Δю’.
Диаметры головки и юбки поршня с учетом монтажных зазоров:
;
,
где ; .
Диаметральные зазоры в горячем состоянии соответственно между стенкой цилиндра и головкой поршня и между стенкой цилиндра и юбкой поршня


где Tц=388 К, Tг=493 К, Tю=428 К – соответственно температура стенок цилиндра, головки и юбки поршня в рабочем состоянии, принятые с учетом жидкостного охлаждения двигателя; T0=293 К – начальная температура цилиндра и поршня.
Т.к. Δг’>0 и Δю’>0 (натяг отсутствует), то поршень пригоден к работе.
Расчет поршневого кольца
Поршневые кольца работают в условиях высоких температур и значительных переменных нагрузок, обеспечивая герметизацию надпоршневого пространства, отвод избыточной доли теплоты от поршня в стенки цилиндра, рациональное распределение масляного слоя по зеркалу цилиндра и ограничения попадания масла в камеру сгорания.
Материал кольца – серый чугун, E=1∙105 МПа.
Среднее давление кольца на стенку цилиндра
,
где – разность между величинами зазоров замка кольца в свободном и рабочем состоянии.
Давление (МПа) кольца на стенку цилиндра в различных точках окружности при каплевидной форме эпюры давления , где μк – переменный коэффициент, определяемый изготовителем в соответствии с принятой формой эпюры давления кольца на зеркало цилиндра.
Результаты расчета p, а также μк для различных углов ψ приведены ниже. По этим данным построена каплевидная эпюра давлений кольца на стенку цилиндра (рис. 8.2).
Угол ψ, определяющий положение текущего давления кольца, град………..
|
|
|
|
|
|
|
| Коэффициент μк…………………………
| 1,05
| 1,05
| 1,14
| 0,9
| 0,45
| 0,67
| 2,85
| Давление p в соответствующей точке…
| 0,172
| 0,172
| 0,187
| 0,148
| 0,074
| 0,110
| 0,467
| Напряжение изгиба кольца, возникающее в сечении кольца, противоположном замку в рабочем состоянии

Напряжения изгиба при надевании кольца на поршень

где m=1,57 – коэффициент, зависящий от способа надевания кольца.
Монтажный зазор в замке поршневого кольца в холодном состоянии
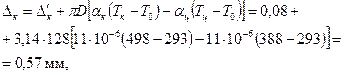
где Δ’к=0,08 мм – минимально допустимый зазор в замке кольца во время работы двигателя, αк=αц=11∙10-6 1/К – коэффициенты линейного расширения материала кольца и гильзы цилиндра, Tц=388 К, Tк=498 К – соответственно температура стенок цилиндра, кольца в рабочем состоянии, принятые с учетом жидкостного охлаждения двигателя; T0=293 К – начальная температура.
Расчет поршневого пальца
Во время работы двигателя поршневой палец подвергается воздействию переменных нагрузок, приводящих к возникновению напряжений изгиба, сдвига, смятия и овализации.
Принимаем наружный диаметр пальца dп=45 мм, внутренний диаметр пальца dв=27 мм, длину пальца lп=112 мм, длину втулки шатуна lш=38 мм, расстояние между торцами бобышек b=51 мм. Материал поршневого пальца – сталь 12ХН3А, E=2,2∙105 МПа. Палец закрепленного типа.
Расчетная сила, действующая на поршневой палец:
газовая ,
инерционная ,
где ,
расчетная ,
где k=0,72 – коэффициент, учитывающий массу поршневого пальца.
Удельное давление пальца на втулку поршневой головки шатуна .
Удельное давление пальца на бобышки .
Напряжение изгиба в среднем сечении пальца при распределении нагрузки по длине пальца согласно эпюре на рис. 8.3:
где .
Касательные напряжения среза в сечениях между бобышками и головкой шатуна
.
Вследствие неравномерного распределения сил, приложенных к пальцу (принимается синусоидальное распределение нагрузки по поверхности пальца – рис. 8.3, а), при работе двигателя происходит деформация сечения пальца (овализация).
Наибольшее увеличение горизонтального диаметра пальца при овализации

Напряжения овализации на внешней поверхности пальца (рис. 8.3, б):
в горизонтальной плоскости (точки 1, ψ=0˚)

в вертикальной плоскости (точки 3, ψ=90˚)

Напряжения овализации на внутренней поверхности пальца (рис. 8.3, б):
в горизонтальной плоскости (точки 2, ψ=0˚)

в вертикальной плоскости (точки 4, ψ=90˚)

Наибольшее напряжение овализации возникает на внутренней поверхности пальца в горизонтальной плоскости, оно не должно превышать 300-350 МПа.
Расчет коленчатого вала
Коленчатый вал – наиболее сложная в конструктивном отношении и наиболее напряженная деталь двигателя, воспринимающая периодические нагрузки от сил давления газов, сил инерции и их моментов. Действие этих сил и моментов приводит к возникновению в материале коленчатого вала значительных напряжений скручивания, изгиба и растяжения – сжатия.
При расчете коленчатого вала принимается, что: кривошип свободно лежит на опорах; опоры и точки приложения сил проходят через средние плоскости шеек; весь пролет между опорами представляет собой абсолютно жесткую балку.
На основании данных динамического расчета имеем: коленчатый вал с симметричными коленами, с противовесами, расположенными только на концах вала; центробежная сила инерции вращающихся масс ; радиус кривошипа R=64 мм. С учетом соотношений, приведенных в табл. 14.1 [1], принимаем следующие основные размеры колена вала (рис. 8.4): коренная шейка – наружный диаметр dк.ш=93 мм, длина lк.ш=74 мм; шатунная шейка – наружный диаметр dш.ш=89 мм, внутренний диаметр δш.ш=33 мм, длина lш.ш=115 мм; расчетное сечение A – A щеки – ширина b=147 мм, толщина h=32 мм; радиус галтелей . Материал вала – сталь 50Г.
По табл. 11.2 и 11.4 [1] для углеродистой стали 50Г определяем:
пределы прочности σв=800 МПа и текучести σт=370 МПа и τт=250 МПа;
пределы усталости (выносливости) при изгибе σ-1=340 МПа, растяжении – сжатии и кручении ;
коэффициенты приведения цикла при изгибе ασ=0,18, кручении ατ=0,08 и растяжении – сжатии ασ=0,14.
По формулам определяем:
при изгибе и ;
при растяжении – сжатии и
;
при кручении и .
Удельное давление на поверхности шатунных шеек
;
,
где ; – соответственно средняя и максимальная нагрузки на шатунную шейку; – рабочая ширина одного шатунного вкладыша.
Расчет коренной шейки. Момент сопротивления коренной шейки кручению
.
Максимальное и минимальное касательные напряжения коренной шейки:
;
.
Среднее напряжение и амплитуды напряжений:
;
;
,
где – эффективный коэффициент концентрации напряжений; q=0,71 – коэффициент чувствительности материала к концентрации напряжений, принятый по данным §11.3 [1]; αкσ=3 – теоретический коэффициент концентрации напряжений, определенный по табл. 11.6 [1] с учетом наличия в шейке масляного отверстия; εмτ=0,61 – масштабный коэффициент, определенный по табл. 11.7 [1] при dк.ш=93 мм, εпτ=1,2 – коэффициент поверхностной чувствительности, определенный по табл. 11.8 [1] с учетом закалки шеек токами высокой частоты.
Так как , то запас прочности коренной шейки от касательных напряжений определяем по пределу текучести:
.
Расчет шатунной шейки.
Момент сопротивления кручению шатунной шейки
.
Максимальное и минимальное касательные напряжения шатунной шейки:
;
.
Среднее напряжение и амплитуды напряжений:
;
;
,
где – эффективный коэффициент концентрации напряжений; q=0,71 – коэффициент чувствительности материала к концентрации напряжений, принятый по данным §11.3 [1]; αкσ=3 – теоретический коэффициент концентрации напряжений, определенный по табл. 11.6 [1] с учетом наличия в шейке масляного отверстия; εмτ=0,62 – масштабный коэффициент, определенный по табл. 11.7 [1] при dш.ш=89 мм, εпτ=0,87 – коэффициент поверхностной чувствительности, определенный по табл. 11.8 [1] для внутренней поверхности шейки (сверления), на которую выходит масляное отверстие.
Так как , то запас прочности шатунной шейки от касательных напряжений определяем по пределу текучести:
.
Моменты, изгибающие шатунную шейку двухпролетного коленчатого вала (рис. 8.4):
в плоскости, перпендикулярной плоскости колена, для сечения I – I по оси масляного отверстия
;
для среднего сечения B – B
,
где ; ;

в плоскости колена для сечения I – I подсчет не производим, т.к. на основании анализа полярной диаграммы и диаграммы износа масляное отверстие на шатунной шейке целесообразно сделать в горизонтальной плоскости (φм=90˚) и, следовательно, ;
для среднего сечения B – B
,
где ;
;
;
расчет моментов и приведен в табл. 8.1, где значения Tл, Tп, Kл и Kп взяты из табл. 6.3.
Максимальные и минимальные нормальные напряжения в шатунной шейке:
в сечении I – I
;
,
где ;
в сечении B – B
;
.
Среднее напряжение и амплитуда напряжений:
для сечения I – I
;
;
,
где – эффективный коэффициент концентрации напряжений; q=0,71 – коэффициент чувствительности материала к концентрации напряжений, принятый по данным §11.3 [1]; αкσ=3 – теоретический коэффициент концентрации напряжений, определенный по табл. 11.6 [1] с учетом наличия в шейке масляного отверстия; εмσ=0,67 – масштабный коэффициент, определенный по табл. 11.7 [1] при dш.ш=89 мм, εпσ=0,87 – коэффициент поверхностной чувствительности, определенный по табл. 11.8 [1] для внутренней поверхности шейки (сверления), на которую выходит масляное отверстие;
Таблица 8.1
φ˚
| Tл, Н
| Tп, Н
| T’Σ, Н
| MT(I – I),=Mφм, Н∙м
| MT(B – B), Н∙м
| Kл, Н
| Kп, Н
| K’Σ, Н
| Mкр(B – B), Н∙м
| MК(B – B), Н∙м
| Mиз, Н∙м
|
|
| -3567
|
|
|
| -16483
| -1000
|
|
|
|
|
| -8118
|
|
|
|
| -10481
| -1371
|
|
|
|
|
| -4788
|
| -156,4
| -15,3
| -19,8
| -1416
| -10357
|
|
|
|
|
|
|
| -2095
| -205
| -265
| -956,8
| -16483
|
|
|
|
|
|
| -8118
| -604,9
| -59,1
| -76,5
| -5782
| -10481
|
|
|
|
|
|
| -4788
| -359,7
| -35,2
| -45,5
| -8794
| -1416
|
|
|
|
|
|
|
| -1317
| -129
| -167
| -9401
| -956,8
|
|
|
|
|
| -3616
|
| -130
| -12,7
| -16,4
| -8842
| -5782
|
|
|
|
|
| -6319
|
|
|
|
| -6002
| -8794
|
|
|
|
|
| -4547
|
|
|
|
| -1275
| -9401
|
|
|
|
|
| 869,8
| -3616
| 861,7
| 84,2
|
| -257,3
| -8842
|
|
|
|
|
| -397
| -6319
|
|
|
|
| -6002
|
|
|
|
|
|
| -4547
|
|
|
|
| -1275
| -36404
| -4605
| -3020
|
|
|
| 869,8
| -12265
| -1199
| -1552
|
| -257,3
| -52891
| -6691
| -5106
|
|
|
|
| -18955
| -1853
| -2398
|
| -1001
| -38182
| -4830
| -3245
|
|
|
|
| -15961
| -1560
| -2019
|
| -1183
| -19449
| -2460
| -875
|
|
|
| -397
| -6500
| -635
| -822
|
|
| -2165
| -274
|
|
|
|
|
| -6594
| -645
| -834
| -3011
|
| -21346
| -2700
| -1115
|
|
|
|
| -14262
| -1394
| -1804
| -5235
|
| -30099
| -3808
| -2223
|
|
|
|
| -17883
| -1748
| -2262
| -7242
|
| -19800
| -2505
| -920
|
|
|
|
| -15486
| -1514
| -1959
| -8962
|
| -7012
| -887
|
|
|
|
|
| -7201
| -704
| -911
| -12024
|
|
|
|
|
|
|
|
| -4145
| -405
| -524
| -11052
| -3011
|
|
|
|
|
| -3734
|
| -1350
| -132
| -171
| -9132
| -8962
|
|
|
|
|
| -6204
|
|
|
|
| -5892
| -12024
|
|
|
|
|
| -3567
|
|
|
|
| -1000
| -11052
|
|
|
|
|
|
| -3734
| -1405
| -137
| -178
| -1371
| -9132
|
|
|
|
|
|
| -6204
| -2531
| -247
| -320
| -10357
| -5892
|
|
|
|
|
|
| -3567
|
|
|
| -16483
| -1000
|
|
|
|
| для сечения B – B
;
;
,
где ; εмσ=0,67 (как для сечения I – I); εпσ=1,2 – коэффициент поверхностной чувствительности, определенный по табл. 11.8 [1] с учетом закалки шеек токами высокой частоты.
Запас прочности шатунной шейки от нормальных напряжений определяется
для сечения I – I – по пределу усталости (при σм<0)
;
Не нашли, что искали? Воспользуйтесь поиском по сайту:
©2015 - 2025 stydopedia.ru Все материалы защищены законодательством РФ.
|