|
Определение площади и размеров агрегатного участка
Расчет площади электромашинного участка производится по удельной площади, приходящейся на явочное количество одновременно работающих в смене Fэ, м2
Fэ = f0 + f1 (Аяр - 1),
где f0 – норма площади на одного производственного рабочего данного участка
или отделения, м2; f0 = 20 м2;
f1 – норма площади на каждого следующего рабочего, м2; f1 = 10 м2;
Аяр – явочное количество одновременно работающих в смене на данном участке
или отделении, чел; Аяр = 9 чел;
Fэ = 20 + 10 (9 – 1) = 100 м2.
С учетом выбранного оборудования (учитывая габариты оборудования, расстояния между оборудованием и стенами, строительные стандарты) окончательно принимается площадь агрегатного участка 148,3 м2.
План агрегатного участка представлен на плакате 2.
Определение числа и грузоподъемности подъемно-транспортных средств
Грузоподъемность транспортных средств определяется исходя из максимальной массы переносимого груза.
На агрегатном участке производится подъем переднего и заднего мостов, весом порядка двух тонн. Для их подъема и перемещения используют кран-балку грузоподъемностью до 3,0 тонн.
Также на агрегатном участке производится перевозка грузов с использованием тележки. На тележке можно перевозить груз до одной тонны.
Расчет потерь мощности и электроэнергии в
Автотрансформаторе
Общую величину потерь активной мощности в автотрансформаторе определяют по формуле
,
где – паспортные потери холостого хода автотрансформатора, кВт;
– нагрузка на стороне ВН, СН и НН, соответственно, кВ·А;
– номинальная мощность автотрансформатора, кВ∙А;
– потери короткого замыкания в лучах трехлучевой схемы замещения автотрансформатора, кВт, определяемые из следующих соотношений:
где – паспортные потери в обмотках для направления потоков мощности от высшего напряжения к среднему, кВт;
– паспортные потери в обмотках для направления потоков мощности от высшего напряжения к низшему, кВт;
– паспортные потери в обмотках для направления потоков мощности от среднего напряжения к низшему, кВт;
α – коэффициент выгодности, определяемый по формуле .
С учетом того, что и в соответствии с получаем:
кВт;
кВт;
кВт.
Подставляя известные значения в формулу получим:
кВт.
Общую величину потерь реактивной мощности в автотрансформаторе определяют по формуле
,
где – паспортный ток холостого хода трансформатора, %;
– напряжения короткого замыкания трехлучевой схемы замещения автотрансформатора, %, определяемые из соотношений:
В соответствии с получаем:
=%;
=%;
=%.
По формуле
+=кВат.
Полные потери мощности в автотрансформаторе определяются по формуле:

кВ∙А.
Потери активной энергии в автотрансформаторе определяются по формуле:
,
где – число часов работы трансформатора в году, час;
– время максимальных потерь обмоток ВН, СН и НН – это условное число часов, в течение которых максимальный ток, протекающий непрерывно, создает потери энергии, равные действительным потерям энергии за год:
где ТМ.В, ТМ.С, ТМ.Н – время использования максимума нагрузки для обмоток ВН, СН и НН – это условное число часов, в течение которых работа с максимальной нагрузкой передает за год столько энергии, сколько при работе по действительному графику, час.
С учетом известных ТМ.В, ТМ.С, ТМ.Н:
час;
час;
час.
По формуле:

+кВт·час.
Потери реактивной энергии в трансформаторе определяются по формуле:
.
|
|
+кВт·час.
Полные потери электроэнергии в автотрансформаторе определяются по формуле:

кВ∙А.
Стоимость потерь С активной электроэнергии в автотрансформаторе определяется по формуле:
,
где C0 – средняя стоимость 1 кВт∙часа электроэнергии, руб/кВт∙час.
руб/год.
Результаты расчета сведены в таблицу 11.
Таблица 11 - Результаты расчета потерь мощности и электроэнергии в автотрансформаторе
Параметр
| Ед. изм
| Значение
| Номинальная мощность автотрансформатора (Sном)
| кВ∙А
|
| Коэффициент выгодности (α)
| -
|
| Активные потери холостого хода автотрансформатора (Pхх)
| кВт
|
| Ток холостого хода автотрансформатора (Iхх)
| %
|
| Потери короткого замыкания автотрансформатора (Pк в-с)
| кВт
|
| Потери короткого замыкания автотрансформатора (Pк в-н)
| кВт
|
| Потери короткого замыкания автотрансформатора (Pк с-н)
| кВт
|
| Напряжение короткого замыкания (Uк в-с)
| %
|
| Напряжение короткого замыкания (Uк в-н)
| %
|
| Напряжение короткого замыкания (Uк с-н)
| %
|
| Расчетная мощность на стороне ВН автотрансформатора (Sв)
| кВ∙А
|
| Расчетная мощность на стороне СН автотрансформатора (Sс)
| кВ∙А
|
| Расчетная мощность на стороне НН автотрансформатора (Sн)
| кВ∙А
|
| Время максимума нагрузки на стороне ВН (Тм вн)
| час.
|
| Время максимума нагрузки на стороне СН (Тм сн)
| час.
|
| Время максимума нагрузки на стороне НН (Тм нн)
| час.
|
| Число часов работы автотрансформатора в году (Tг)
| час.
|
| Средний тариф на активную электроэнергию (Co)
| руб/кВт∙час
|
| Значение потерь активной мощности в автотрансформаторе (Pт)
| кВт
| 2,00
| Значение потерь реактивной мощности в автотрансформаторе (Qт)
| кВар
| 20,00
| Значение полных потерь мощности в автотрансформаторе (Sт)
| кВ∙А
| 20,00
| Значение времени максимальных потерь на стороне ВН (τВН)
| час.
| 157,29
| Значение времени максимальных потерь на стороне СН (τСН)
| час.
| 136,88
| Значение времени максимальных потерь на стороне НН (τНН)
| час.
| 136,88
| Годовое значение потерь активной энергии в автотрансформаторе (Waт)
| кВт∙час
| 175,00
| Годовое значение потерь реактивной энергии в автотрансформаторе (Wрт)
| кВар∙час
| 175,21
| Годовое значение полных потерь энергии в автотрансформаторе (Wт)
| кВ∙А∙час
| 175,09
| Годовая стоимость потерь активной энергии в автотрансформаторе (С)
| руб/год
| 232 575
| В качестве питающего устройства также можно использовать инвертор, так как он позволяет сохранить до 30% энергии руб/год
Однако стоимость инверторных устройств значительно выше чем автотрансформатора, поэтому в качестве питающего устройства выбираем автотрансформатор.
7 Охрана труда и окружающей среды
7.1 Разработка мероприятий по охране труда
В процессе эксплуатации масла соприкасаются с металлами, подвергаются воздействию воздуха, температуры и других факторов, под влиянием которых с течением времени происходит изменение свойств масла: разложение, окисление, полимеризация и конденсация, обугливание, разжижение горючим, обводнение и загрязнение посторонними веществами. Перечисленные факторы действуют в комплексе и взаимно усиливают друг друга, ухудшая качество масла в процессе его эксплуатации. Так, наличие воды способствует окислению масла, а также развитию в нем биозагрязнений, которые развиваются на границе масло - вода. Механические примеси, в состав которых в большинстве случаев наряду с сажей входят металлы в виде продуктов коррозии, являются катализаторами окисления масел, в процессе которого образуются кислоты и различные смолисто-асфальтеновые соединения. Общее содержание образующихся нежелательных примесей может составлять 5-30% в зависимости от срока и условий эксплуатации масел. Масла, содержащие загрязняющие примеси, не способны удовлетворять предъявляемым к ним требованиям и должны быть утилизированы и заменены свежими маслами. Для утилизации отработанных нефтепродуктов (ОНП) используют разные методы, рисунок 14.
Отработанные нефтяные масла являются одним из существенных источников загрязнения окружающей среды - почвы, водных источников и грунтовых вод. Огромный экологический ущерб наносит слив отработанных масел в почву и водоёмы, который по данным зарубежных исследователей, превышает по объему аварийные сбросы и потери нефти при ее добыче. 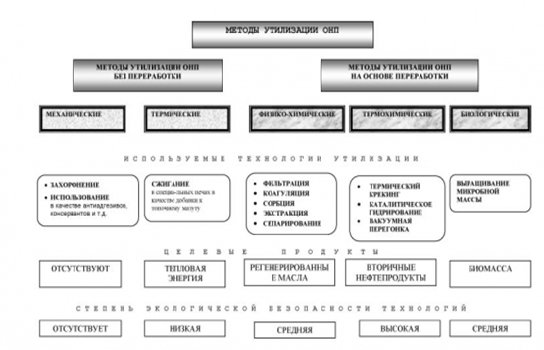
Рисунок 14 - Методы утилизации отработанных нефтепродуктов.
Однако существует организационная проблема, и заключается она в налаживании правильной системы сбора ОНП. Существующая практика показывает, что в настоящих условиях трудно рассчитывать на селективный и технологически своевременный сбор ОНП, а, следовательно, на высокое качество получаемого исходного сырья. Как правило, это будет смесь отработанных масел и других нефтепродуктов, растворителей, промывочных жидкостей и прочих примесей. При этом необходимо учитывать что, с одной стороны, цена такого сырья будет достаточно высокой за счет значительных затрат на организацию их сбора, а с другой, выделение из подобного сырья ценных базовых компонентов для производства товарных масел требует применения сложных, многостадийных и дорогостоящих технологий. В то же время, продукт, полученный в результате переработки, должен быть высоколиквидным на рынке, в том числе зарубежном. Количество же отходов этого процесса должно быть минимальным и легко утилизируемым. Все вышеописанное создает практически безальтернативную основу для применения низкоэнергоемких установок термического крекинга с получением печного топлива для малогабаритных тепловых и силовых агрегатов,
Термический крекинг
В процессе термического крекинга и дистилляции отработанные гидравлические жидкости, моторные и смазочные масла преобразуются в полноценное топливо, подобное дизельному, которое может использоваться для отопления зданий и сооружений. Технология характеризуется высокой эффективностью выхода целевого продукта, который достигает 75-85% от количества перерабатываемого сырья, а также небольшим количеством отходов (кокс и вода). В качестве сырья используются только отработанные масла, и имеется возможность изменения характеристик конечного продукта в зависимости от целей его применения Отработанное масло собирается в приемной емкости отделения приема и усреднения отработанного масла, где оно перемешивается и нагревается. Усредненное и подогретое масло подается в выпарной аппарат отделения обезвоживания, в котором при температуре 110ºС и вакууме происходит отделение масла от воды и легкокипящих углеводородов (в основном, фракций бензина). Пары воды и бензина после конденсации разделяются в отделении очистки водного дистиллята. Бензин и вода после дополнительной доочистки реализуются как товарные продукты. Обезвоженное масло с содержанием воды не более 1% подается в отделение термического крекинга. В котле крекинга при температуре 380-420ºС без доступа воздуха происходит деструкция молекул высококипящих углеводородов с образованием более легких углеводородов, входящих в состав печного топлива и бензина, и их испарение. Одновременно с этим процессом из котла непрерывно удаляются неразложившиеся высококипящие углеводороды, образующие битумную фракцию в количестве 8-12% от массы перерабатываемых масел. Пары углеводородов и газы крекинга, проходя через установленный на котле дефлегматор, охлаждаются до температуры 270ºС и поступают в конденсатор. Здесь происходит конденсация и разделение продуктов крекинга на фракции бензина и печного топлива. Несконденсированные пары углеводородов и газы крекинга подаются на высокотемпературное сжигание. Бензин после отделения от него воды в сепараторе реализуется как товарный продукт. Печное топливо откачивается в отделение стабилизации, где в стабилизаторе в присутствии небольшого количества стабилизирующего вещества отстаивается в течение некоторого времени. Последующая очистка печного топлива от шлама осуществляется в высокоскоростной центрифуге и на адсорбционном фильтре. Очищенное печное топливо является основным товарным продуктом такого производства. Единственным отходом технологического процесса является небольшое (около 0,5%) количество кокса, который периодически удаляется из котла крекинга. При коксовании происходит связывание содержащихся в ММО вредных веществ в нетоксичную форму, пригодную для захоронения. К преимуществам такой технологии относятся: простота технологического процесса и его аппаратурного оформления; возможность переработки широкого спектра отработанных масел с предъявлением ограниченных требований к их качеству; малоотходность и экологическая безопасность производства; получение с высоким выходом основного товарного продукта - печного топлива; ограниченная площадь размещения производства и его полная автоматизация; сравнительно небольшой объем капиталовложений.
7.3 Регенерация
Однако продукты физико-химических превращений масла и примеси, попадающие извне, составляют незначительную часть в общем объеме отработанных технических масел и при помощи определенных методов могут быть удалены. Обычно современные технологические процессы восстановления качества отработанных нефтяных масел с целью их последующего использования по прямому назначению являются многоступенчатыми и в общем виде включают этапы, представленные на рисунке 15.
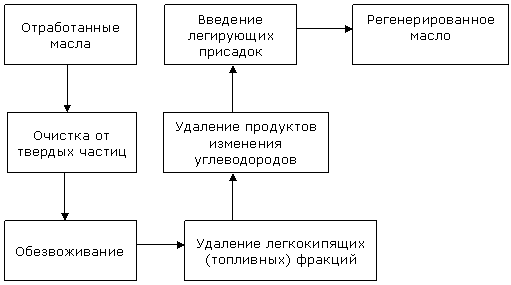
Рисунок 15 - Стадии процесса регенерации отработанных технических масел.
Отдельные этапы процесса регенерации отработанных масел могут исключаться, совмещаться или выполняется в иной последовательности в зависимости от конкретных физико-химических свойств регенерируемого масла и особенностей технологических операций, выбранных для восстановления качества этого масла. В настоящее время для регенерации отработанных масел используют физические, физико-химические и химические методы. Основные из этих методов и применяемое при их реализации технологическое оборудование представлены в таблице 12.
Таблица 12 - Методы и оборудование для регенерации отработанных технических масел.
Методы
| Используемые технологии
| Оборудование
| Физические
| Воздействие силовых полей (гравитационного, центробежного, электрического, магнитного)
| Отстойники
Гидроциклоны
Центрифуги
Электроочистители
Магнитные очистители
| Фильтрование через пористые перегородки
| Фильтры
Фильтры-водоотделители
| Теплофизические технологии (нагревание, выпаривание, водная промывка, атмосферная и вакуумная перегонка и т.п.)
| Выпарные колонки
Вакуумные дистилляторы
Массообменные аппараты
| Комбинированные технологии
| Гидродинамические фильтры
Фильтрующие центрифуги, магнитные фильтры
Трибоэлектрические очистители
| Физико-химические
| Коагуляция
| Смесители-отстойники
| Сорбция
| Адсорберы
| Ионообменная очистка
| Ионообменные аппараты
| Экстракция
| Экстракторы
| Химическая
| Сернокислотная очистка
| Кислотные реакторы
| Щелочная обработка
| Щелочные реакторы
| Гидрогенизация
| Гидрогенизаторы
| Обработка карбамидами металлов
| Реакторы-смесители
| По числу установок и объему перерабатываемого сырья на первом месте в мире находятся процессы с применением серной кислоты. В результате сернокислотной очистки образуется большое количество кислого гудрона – трудно утилизируемого и экологически опасного отхода. Кроме того, сернокислотная очистка не обеспечивает удаление из отработанных масел полициклических ароматических углеводородов и высокотоксичных соединений хлора. Нельзя также регенерировать серной кислотой современные масла, совместимые с окружающей средой (растительные и синтетические сложные эфиры), поскольку серная кислота разлагает их, что, в частности, увеличивает выход кислого гудрона. В нашей стране сернокислотную очистку сейчас практически не применяют. Второе место по объему промышленного применения занимают процессы с использованием в качестве основной стадии сорбционной очистки (контактным или перколяционным способом). Наиболее широко такую технологию применяют на небольших предприятиях в США. В качестве сорбентов широко используют активированные глины. Масла, полученные данным методом, как правило, смешивают со свежими порциями и вводят небольшое число присадок. Недостатки данного процесса заключаются в отсутствии контроля вязкости и фракционного состава получаемого продукта, а также в значительных потерях масла с сорбентом. Возникают трудности и с утилизацией большого количества отработанного сорбента, представляющего опасность для окружающей среды. Синтетические же сорбенты, обладающие высокой термической стабильностью, дающей возможность их регенерации, достаточно дороги. Сорбционную очистку заменяют гидрогенизационными процессами. Однако и в этом случае сорбенты необходимы для защиты катализаторов гидроочистки от преждевременной дезактивации металлами и смолистыми соединениями. Гидрогенизационные процессы все шире применяются при вторичной переработке отработанных масел. Это связано как с широкими возможностями получения высококачественных масел и увеличения их выхода, так и с большей экологической чистотой этого процесса по сравнению с сернокислотной и адсорбционной очисткой. Недостатки процесса гидроочистки – потребность в больших количествах водорода, а порог экономически целесообразной производительности (по зарубежным данным) составляет 30-50 тыс. т/год. Установка с использованием гидроочистки масел, как правило, размещается непосредственно на соответствующем нефтеперерабатывающем заводе, имеющем излишек водорода и возможность его рециркуляции. Для очистки отработанных масел от полициклических соединений (смолы), высокотоксичных соединений хлора, присадок и продуктов окисления применяются процессы с использованием металлического натрия. При этом образуются полимеры и соли натрия с высокими температурами кипения, что позволяет отогнать масло. Выход очищенного масла превышает 80 %. Процесс не требует давления и катализаторов, не связан с выделением хлор- и сероводородов.
Заключение
В данном дипломном проекте на основе условий работы и эксплуатации, возникающих при этом различных неисправностей, для улучшения системы упругого подвешивания, был предложен амортизатор с использованием ферромагнитной жидкости. Был произведен расчет эффективности работы такого амортизатора и как результат уменьшение динамических нагрузок в среднем на 15%. Увеличение курсовой устойчивости на 33.5%. Так же произведен расчет основных размеров амортизатора.
В экономическом разделе рассчитали выгоду от применения устройства, которая составила 490 620 915 руб. вследствие уменьшения количества незапланированных ремонтов на 11.6%.
Разработан агрегатный участок троллейбусного депо объемом выпуска из РР 110 подвижных единиц в год. На агрегатном участке производится ремонт не только заднего моста, но и переднего моста, карданного вала, ступиц колёс, и многого другого оборудования троллейбуса. Трудоемкость ремонта заднего моста составляет 23,21 чел.·ч
В разделе энергосбережения рассчитаны потери в автотрансформаторе, которые сравнили с потерями в инверторе и в качестве питающего устройства оставлен автотрансформатор.
Подбор оборудования для агрегатного участка осуществлен в соответствии с технологическим процессом ремонта заднего моста, а его расстановка произведена соблюдая все необходимые требования. С учётом размещённого оборудования (габариты оборудования, расстояния между оборудованием и стенами, строительные стандарты) окончательно принята площадь агрегатного участка 288 м2.
Все работы в агрегатном участке производятся под строгим контролем мастера за недопущением нарушения технологического процесса, а также за соблюдением правил техники безопасности и условиями труда.
Список используемых источников
1 Бондаревский, Д. И., Кобозев, В. М. Эксплуатация и ремонт подвижного состава городского электрического транспорта. / Д. И. Бондаревский, В. М. Кобозев. – М. : ВШ, 1973. – 285 с.
2 Веклич, В. Ф. Новые технические решения на городском электрическом транспорте. / В. Ф. Веклич. – К. : Будiвельник, 1975. – 255 с.
3 Кобозев, В. М. Эксплуатация и ремонт подвижного состава городского электрического транспорта. / В. М. Кобозев. – М. : ВШ, 1982. – 328 с.
4 Коган, Л. Я. Эксплуатация и ремонт трамваев и троллейбусов. / Л. Я. Коган. – М. : Транспорт, 1979. – 237 с.
5 Малышев, Г. А. Теория авторемонтного производства. / Г. А. Малышев. – М. : Транспорт, 1977. – 298 с.
6Машиностроительное черчение: Учебное пособие для вузов / Под ред. Е. Д. Феоктистова. М. : Машиностроение, 1981. – 304 с.
7Методы получения лакокрасочных покрытий М. : Химия, 1974. – 136 с.
8Правила технической эксплуатации троллейбусов. М. : Транспорт, 1978. – 312 с.
9Ремонт электроподвижного состава промышленного транспорта / Под ред. М. Г. Потапова. М. : Транспорт, 1982. – 288 с.
10Технология окраски изделий в машиностроении: Учебник для проф. – техн. училищ. М.: ВШ, 1979. – 215 с.
11Устройство и эксплуатация троллейбуса: Учеб. пособие для проф.-техн. учеб. заведений. – 2-е изд., перераб. и доп. М.: ВШ, 1978. – 336 с.
12 Чмыхов, Б. А. , Халиманчик, В. А. Организация, планирование и управление производством: Пособие по выполнению практических работ / Б. А. Чмыхов, В. А. Халиманчик. – Гомель, 2003. – 275 с.
13 Чмыхов, Б. А. Применение единой системы технологической документации в дипломном проектировании. / Б. А. Чмыхов. – Гомель, 1991. – 113 с.
14 Чмыхов, Б. А. Организация, планирование и управление тепловозоремонтным производством: Учебное пособие. / Б. А. Чмыхов – Гомель, 2002 – 275 с.
15 Вольберг В. В.Устройства и эксплуатация окрасочно-сушильных агрегатов в машиностроении: Учебное пособие для технических училищ. – М.: Высшая школа, 1982. – 272 с., ил.
16 Шатило С. Н.Пожарная безопасность на железнодорожном транспорте: Учебно-методическое пособие. – Гомель: БелГУТ, 2007. – 344 с.
Не нашли, что искали? Воспользуйтесь поиском по сайту:
©2015 - 2025 stydopedia.ru Все материалы защищены законодательством РФ.
|