Представление виброакустического сигнала полигармонической моделью
Колебательные процессы, сопровождающие функционирование машин и механизмов, непосредственный результат взаимодействия деталей. Свойства или изменение свойств деталей проявляются в их взаимодействии, именно поэтому виброакустический сигнал - побочный результат взаимодействия - является носителем информации о техническом состоянии элементов механизма, образующих кинематические пары: пару колес в зубчатом зацеплении; обоймы, тела качения, сепаратор - в подшипнике качения; цилиндр и поршне в двигателе внутреннего сгорания и т. п. Одновременно с этими явлениями в механизмах имеет место взаимодействие движущихся или вращающихся элементов с внешней средой: вращение лопаток турбины или лопастей винта в потоке газа, вихреобразование в потоке на границе сред, кавитация в жидкости, явление гидравлического удара и др.
Все разнообразие колебательных процессов в механизме можно представить виде вынужденных и собственных колебаний. В качестве носителя информации о техническом состоянии могут служить оба вида колебаний, но характер и объем информации, содержащейся в них, различный. Если амплитуды вынужденных колебаний являются энергетическими характеристиками, содержат информацию о качестве изготовления (сборке, ремонта) и о грубых изменениях параметров технического состояния, граничащих с аварийной ситуацией в процессе эксплуатации и механизма, то окраска (модуляции вынужденных колебаний и колебаний в зоне собственных частот узлов механизма) - это источники информации о наличии дефектов на ранней стадии их развития.
Рассмотрим несколько моделей виброакустических процессов, позволяющих установить взаимнооднозначное соответствие между характеристиками виброакустического сигнала и параметрами технического состояния роторных механизмов. Существует огромное число механизмов циклического действия, в которых характер взаимодействия элементов подчинен периодическому закону, связанному с вращательным движением.
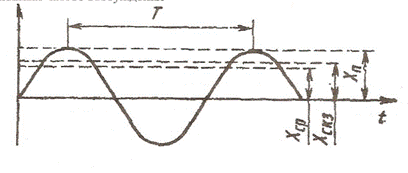
Рис. 2.7 Пример гармонического вибрационного сигнала с указанием пикового, среднего квадратичного и среднего абсолютного значений
В роторных механизмах в низкочастотном диапазоне (до 200-300 Гц) одной из основных частот возбуждения является частота вращения ротора (роторная частота) f=wвр/2π, где WBp - угловая частота вращения ротора.
Колебания механизма в этом диапазоне частот гармонического вида, x(t) =acos(wвpt), и обусловлены, в основном, неуравновешенностью вращающихся масс. Энергия таких колебаний очень велика, затухание в системе мало, поэтому они распространяются на большие расстояния. Именно эти колебания определяют динамическую прочность конструкции механизма. Механизм при этом рассматривается как единая упругая система с сосредоточенными параметрами. Амплитуда колебаний ak < на роторной частоте определяется в основном значением дисбаланса и отношением критической частоты вращения ротора к рабочей. Информативным параметром в такой модели может служить значение амплитуды (или приращение амплитуды) колебаний на роторной частоте.
Периодическая вибрация обычно рассматривается как колебательное движение всего тела относительно положения равновесия (рис. 2.3), и для ее описания достаточно двух параметров: периода осцилляции (или частоты колебаний f=1/T и амплитуды колебаний а).
В практике виброизмерений и вибродиагностики при описании колебаний наиболее употребительны пиковое значение амплитуды Хn=а, характеризующее максимальный размах колебаний относительно положения
равновесия, среднее абсолютное значение (математическое ожидание):
X cp = 1/T ∫ |x|dt = ‹|x|› (2.7)
и среднее квадратическое значение (дисперсия):
X скз = √(1/T) ∫ |x| dt = √‹x2› (2.8)
Таблица 2.2
Диагностическая карта неисправностей
Дефект
| Основные частоты
| Направление измерений
| Примечание
| Неуравнове
шенность ротора
| f вр.
| Радиальное
| Наиболее вероятная причина увеличения виброакустического сигнала
| Зазор в подшипнике скольжения
| Субгармоники f вр., особенно ½ или 1/3 f вр.
| Преимущественно радиальное
| Дефект проявляется на рабочей скорости и рабочей температуре
| Механический люфт
| 2f вр.
| Радиальное и осевое
| А так же суб- и комбинарные гармоники
| Неуравнове
шенности в механизмах и машинах возвратно-поступательного принципа действия
| f вр., и (или) Кf вр., К- число несбалансированных деталей
| Преимущественно радиальное
| Возрастает с ростом частоты вращения
|
В настоящее время методы виброакустической диагностики и прогнозирования остаточного ресурса широко используются в судостроении, авиастроении, энергетике. Данный метод расширил возможности существующих методов неразрушающего контроля, позволил решать практические задачи долгосрочного прогноза состояния агрегатов и механизмов и, как следствие, переходить на их обслуживание и ремонт по фактическому состоянию.
Вибродиагностика станков
Теория колебаний находит широкое применение для диагностирования инструмента и процесса резания. Технологические алгоритмы предусматривают непрерывный мониторинг процессов, который позволяет обнаружить изменение в состоянии объекта диагностирования при его эксплуатации. Для периодической оценки состояния различных машин и агрегатов, имеющих вращающиеся детали, широко применяют вибродиагностику. Этот метод является перспективным для периодического диагностирования состояния станочного оборудования. Вибродатчики с автономной измерительной аппаратурой в нормативные сроки должны подключаться к диагностируемым узлам станка, что позволит выявить для ремонта повреждения, существенно нарушающие качество обработки.
В основе применения методов вибродиагностики лежат следующие положения:
- функционирование любой машины, имеющей вращающиеся массы, сопровождается вибрацией и акустическим шумом;
- изменение технического состояния машин влияет на генерируемые ими виброакустические сигналы;
-параметры виброакустических сигналов могут быть измерены в процессе эксплуатации без разборки станка;
-они являются источниками информации о характере иместе повреждений.
Использование вибродиагностики возможно после выполнения большого объема исследований в соответствии с методическим подходом к разработке систем диагностирования.
Выявляются возможные типичные повреждении или дефекты для данного механизма, их изменение с течением времени эксплуатации и предельные значения для каждого повреждения, определяются диагностические признаки из числа параметров вибросигнала. Временной сигнал колебаний может быть представлен в единицах ускорений колебаний, скорости или амплитуды.
Из спектра колебаний выявляют наиболее информативный диагностический признак. Каждому виду повреждений соответствует характерный вид сигнала. В результате исследований получают своеобразный классификатор виброакустических признаков различных повреждений и дефектов механизма, содержащий сведения о виброакустических признаках и причинах возникновения повреждений и дефектов, динамики их развития, зависимости признаков дефекта от режимов работы механизма, а также рекомендации по устранению повреждений.
Для примера приведем (из А. В. Лукьянова,1999) упрощенные фрагменты классификатора для зубчатых передач. Возбуждение колебаний в зубчатых передачах, отличающихся от колебаний при нормально функционирующих передачах, вызывается дефектами изготовления, сборки и эксплуатации. Последние проявляются в виде абразивного износа зубьев, сколов, трещин и выкрашиваний зубьев.
При эксплуатационных повреждениях свойства вибросигнала, его форма и спектр вибраций - заметно меняются. В частности, в спектре наряду с основными частотами возбуждения – зубцовой частотой, равной f;(f - частота вращения зубчатого колеса; z - число зубьев), появляются новые спектральные составляющие боковые полосы частоты (рис. 2.6.1). Высокие амплитуды боковых полос, окружающих зубцовые частоты, обычно характеризуют значительный износ зубчатых колес, поэтому боковые полосы являются надежным диагностическим признаком износа колес.
Кроме этого, в спектре колебаний передачи с изношенными поверхностями зубьев появляется ряд спектральных составляющих, кратных зубцовой частоте mf3. Они являются отображением увеличения бокового зазора между поверхностями зубьев. Происходит отрыв профилей зубьев в зацеплении и ударный режим возбуждения вибраций.
Диагностировалась прямозубая передача с поверхностями зубьев, изношенными на 75 % от предельного уровня. Поломка или скол зуба шестерни являются опасными повреждениями, которые могут привести к отказу станка при попадании продуктов разрушения в зону зацепления или подшипники. Эти повреждения вызывают снижение жесткости зацепления в момент контакта дефектного зуба. Следующая пара зубьев входит в зацепление с ударом. Амплитуда ударного импульса пропорциональна степени развития повреждения. Импульсы видны на графике временного сигнала виброскорости, показанном на рис. 2.6.1. Частота импульсов соответствует оборотной частоте дефектной шестерни; Т1 - время оборота.
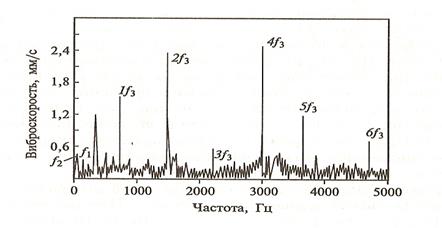
Рис. 2.12Спектр вибраций при равномерном абразивном износе зубчатых колес:
f1и f2 -частоты вращения ведущего и ведомого колеса; f3 -зубцовая частота
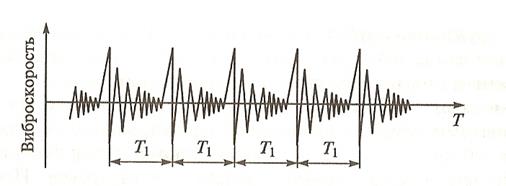
Рис. 2.13Временной сигнал виброскорости при разрушенном зубе
Исследования колебаний в звуковом диапазон е частот и основанные на них методы диагностики повреждений в элементах технологической системы выделяют в обособленный ряд, поскольку в качестве датчика применяют обычный микрофон, а диагностическими признаками повреждений являются физические характеристики звука: звуковое давление, сила звука и т. д. Звуком обычно называют колебательные движения, обладающие частотами от 20 до 20000 Гц. Сигнал от микрофона после усиления и аналого-цифрового преобразования вводился для анализа в ЭВМ.
Шумы в технологическом оборудовании слагаются в различных сочетаниях из звуков, возникающих при соударениях деталей механизмов, например зубчатых колес, муфт, винтовых пар и др.; трении в подшипниках, направляющих, на рабочих поверхностях инструмента и др. Уровень звука изменяется, если в указанных узлах и деталях возникают повреждения. Можно установить, что определенному виду повреждений соответствует специфическая форма звуковой волны. Метод распознавания повреждений в станках состоит в сопоставлении звукового сигнала исправного станка с текущими сигналами, в которых отображаются возможные повреждения. Повреждения в деталях станка вызывают изменение спектрограммы шума. На рис. 2.6.3 показана спектрограмма шума, производимого при работе стальных зубчатых колес. Основная частота шума зависит от числа зубьев и частоты вращения. Для шестерен, спектр шума которых представлен на рисунке, основная частота составляет около 900 Гц. На этой частоте уровень силы звука достигает 90 дБ. При износе зубьев шестерни возрастает энергия соударения при зацеплении зубьев и уровень силы звука. Последний является диагностическим признаком износа.
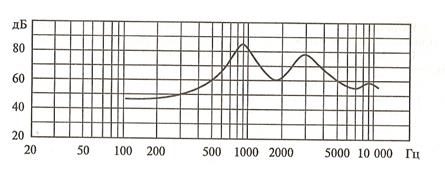
Рис. 2.14Спектрограмма шума, производимого при зацеплении пары стальных шестерен.
Информативная полоса частот, в которой отображается износ инструмента, лежит в диапазоне 4-6 кГц. При работе изношенным инструментом уровень силы звука на 10 дБ выше, чем при заточенном. Очевидно, для диагностирования состояния элементов технологической системы должны быть записаны спектры шумов, возникающих в различных ситуациях, как при рабочих, так и при вспомогательных движениях. Распознавание повреждений выполняется по отклонениям уровней силы звука.
Перспективность диагностики и автоматического управления процессом шлифования на основе поступающей информации об амплитуде звукового давления установлено по результатам экспериментальных исследований, в которых выявлено влияние режима шлифования, характеристики круга, загрязненности СОЖ механическими примесями на амплитуду звукового давления. Кроме того, было установлено, что между параметрами шероховатости Ra шлифуемой поверхности за готовки, износом шлифовального круга, с одной стороны, и амплитудой звукового давления - с другой, имеются корреляционные зависимости. Результаты исследований позволили использовать амплитуду звукового давления в качестве информативного признака состояния процесса шлифования и разработать аппаратную реализацию системы диагностирования, основанную на этом диагностическом признаке.
2.6 Формирование требований к диагностической аппаратуре
На основании изложенного можно сформулировать следующие требования для диагностического комплекса.
Система виброакустического диагностирования станка должна иметь высокоскоростной блок сбора и обработки данных.
Рабочий диапазон частот вибродатчика (акселерометра/пьезодатчика) должен составлять 500-5000 Гц, а акустического датчика 4-6 кГц
Система должна обладать: высокочастотным АЦП, внешним устройством для записи полезной информации. Соединения датчиков и блоков обработки информации должны быть помехозащищенными, влагоустойчивыми, а также устойчивыми к понижению и повышению температуры. Этим требованиям должны удовлетворять все комплектующие к аппаратуре.
Не нашли, что искали? Воспользуйтесь поиском по сайту:
©2015 - 2025 stydopedia.ru Все материалы защищены законодательством РФ.
|