Контроль качества термической обработки стальных изделий
Структурные превращения при термообработке сталей.В стали (т.е. сплаве железа с углеродом с возможной добавкой других легирующих элементов) основными являются следующие три структуры:
аустенит ( A ) - твердый раствор углерода в - железе;
мартенсит ( М ) - твердый раствор углерода в - железе;
перлит ( П ) - эвтектоидная смесь из одновременно образующихся феррита и карбида . Переход от одной структуры к другой характеризует основные превращения в сталях.
Для понимания процессов, происходящих в сталях при закалке и отпуске, необходимо рассмотреть так называемый "стальной" участок диаграммы состояний сплава железо-углерод, представленный на рис. 2.47.
Нижняя критическая точка лежит на линии PSK и соответствует превращению аустенит-перлит. Верхняя критическая точка лежит на линии GSE и соответствует началу выпадения или концу растворения феррита в доэвтектоидных (содержание углерода C < 0,8 %) или цементита в заэвтектоидных (0,8 % < C < 2,14 %) сталях. Чтобы отличить критические точки при нагреве и охлаждении рядом с буквой ставят букву с или r соответственно (например, точка превращения аустенита в перлит при охлаждении обозначается , а точка превращения перлита в аустенит при нагреве обозначается ).
Основные виды термической обработки сталей.
Отжиг - фазовая перекристаллизация, заключающаяся в нагреве выше с последующим медленным охлаждением. Состояние приближается к равновесному. Структура после отжига: перлит + феррит, перлит или перлит + цементит.
Закалка - нагрев выше с последующим быстрым охлаждением. При медленном охлаждении аустенит распадается на феррит + цементит. С увеличением скорости охлаждения превращение происходит при все более низких температурах. Если скорость охлаждения достаточно высока и переохлаждение достаточно велико, то выделения цементита и феррита не происходит и аустенит превращается в мартенсит. При аустенитно-мартенситном превращении происходит только перестройка решетки без
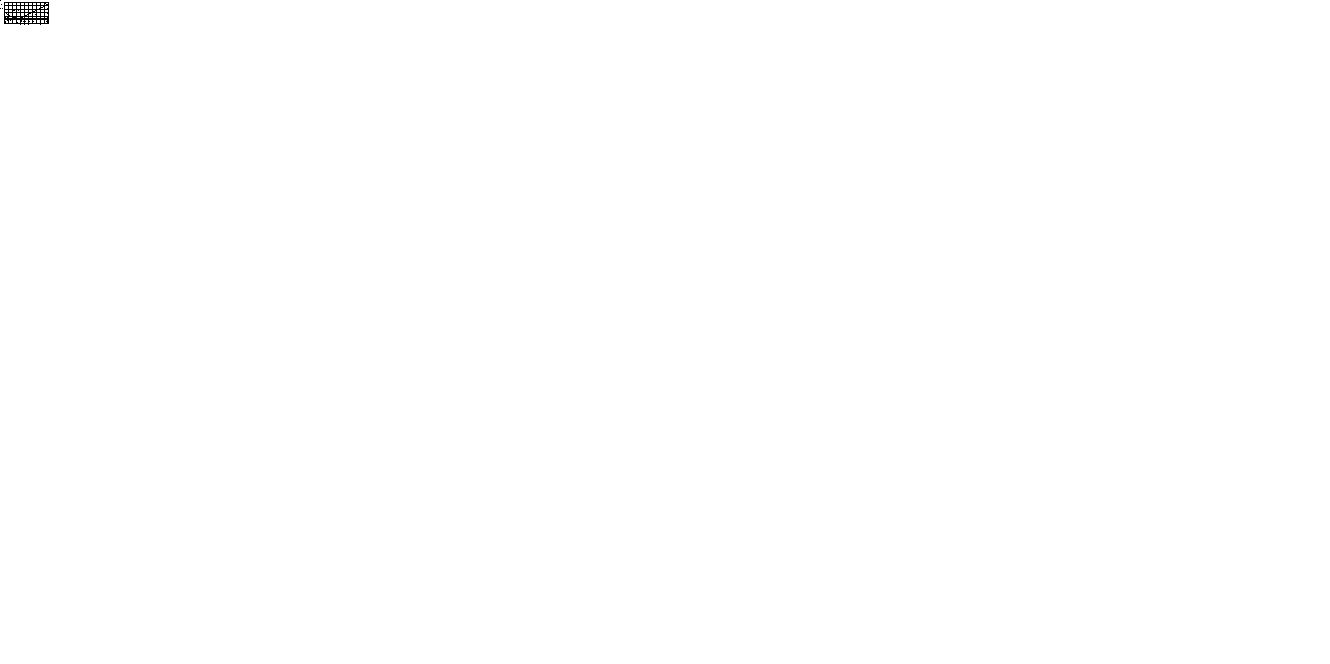
Рис. 2.47. “Стальной” участок диаграммы состояний сплава Fe – C
изменения концентрации реагирующих фаз. Углерод из раствора не выделяется, а атомы железа из решетки гранецентрированного куба перестраиваются в о.ц.к. решетку. Для кристаллической решетки мартенсита характерна тетрагональность (соотношение осей не равно единице вследствие наличия в растворе углерода), что обуславливает высокие внутренние напряжения. Кристаллы мартенсита представляют собой пластины, расположенные параллельно или пересекающиеся под определенными углами, поскольку мартенсит образуется лишь по определенным кристаллографическим направлениям в аустените. Размер кристаллов мартенсита тем больше, чем более однородна и совершенна структура аустенита. Превращение аустенита в мартенсит происходит в определенном температурном интервале, ограниченном точками (начало превращения) и (конец превращения). Положение точек и не зависит от скорости охлаждения и определяется химическим составом аустенита. Если точка лежит ниже нормальной температуры, то не весь аустенит превращается в мартенсит. Количество остаточного аустенита зависит от химического состава и условий закалки стали.
Полученная в результате закалки мартенситная структура придает стали высокую твердость, хрупкость. В сравнении с отожженным состоянием существенно повышаются электросопротивление, коэрцитивная сила, снижаются магнитная проницаемость, намагниченность насыщения и остаточная индукция.
Отпуск - нагрев закаленной стали ниже с последующим медленным или быстрым охлаждением. Исходной является структура закаленной стали, состоящая из мартенсита и аустенита. При повышении температуры отпуска до 200 °С происходит так называемое первое превращение при отпуске. Рентгеновский анализ показывает, что в этом диапазоне температур уменьшается степень тетрагональности решетки мартенсита, то есть соотношение параметров решетки стремится к единице, что связано с выделением углерода из раствора. При этом образуются тонкие (несколько атомных слоев) пластинки карбида, когерентно связанные с твердым раствором. Получившаяся структура носит название отпущенного мартенсита. Второе превращение при отпуске захватывает интервал температур 200-300 °С. В этом интервале остаточный аустенит превращается в отпущенный мартенсит. Повышение температуры более чем на 300 °С, приводит к полному выделению углерода из раствора, и снятию внутренних напряжений. Карбиды обособляются и превращаются в цементит (Fe3C). Сумма этих изменений характеризует третье превращение при отпуске. При 400 °С третье превращение заканчивается, и сталь состоит из феррита и цементита. Дальнейшее повышение температуры приводит к коагуляции частиц феррита и цементита.
Структура, механические и магнитные свойства сталей после закалки и отпуска. Изменение структуры сталей под влиянием термообработки приводит к существенному изменению их свойств.
В отожженном или высокоотпущенном (температура отпуска > 400 °C) состояниях сталь состоит из феррита и включений карбидов (цементита). Феррит обладает низкой прочностью и высокой пластичностью, цементит же при нулевом значении удлинения и сужения имеет высокую твердость. Более высокое значение прочности и меньшая пластичность сплавов с содержанием углерода более 0,01 %, объясняются упрочняющим действием карбидных частиц. При малом количестве цементитных включений пластическая деформация развивается относительно беспрепятственно, и материал характеризуется невысокой твердостью. Если таких частиц будет больше, например если при термообработке измельчаются частицы цементита, то вокруг этих частиц образуются искажения кристаллической решетки, что препятствует движению дислокаций, и сталь упрочняется. Наоборот, в результате укрупнения частиц освободятся некоторые объемы феррита для движения дислокаций, и способность стали к пластической деформации увеличивается. Количество карбидных частиц постоянного размера зависит от содержания углерода в стали, поэтому с увеличением содержания углерода повышаются значения прочности и понижаются значения пластичности как для отожженного, так и высокоотпущенного состояний. При данном же содержании углерода число карбидных частиц, а, следовательно, и площадь поверхности раздела фаз будут возрастать при измельчении карбидов. Более высокая дисперсность карбидной фазы объясняет более высокую прочность закаленной и отпущенной стали по сравнению с отожженной. Повышение , приводящее к укрупнению цементитных частиц, снижает прочность.
Высокая твердость мартенсита объясняется тем, что элементарные кристаллические ячейки его искажены, вследствие чего пластическая деформация затруднена и образование сдвигов в мартенсите почти невозможно. Чем больше углерода в стали, тем больше искаженность тетрагональной решетки мартенсита и больше его твердость. Изложенные представления иллюстрируются представленными на рис. 2.48 экспериментальными зависимостями твердости закаленных сталей с различным содержанием углерода от температуры отпуска.
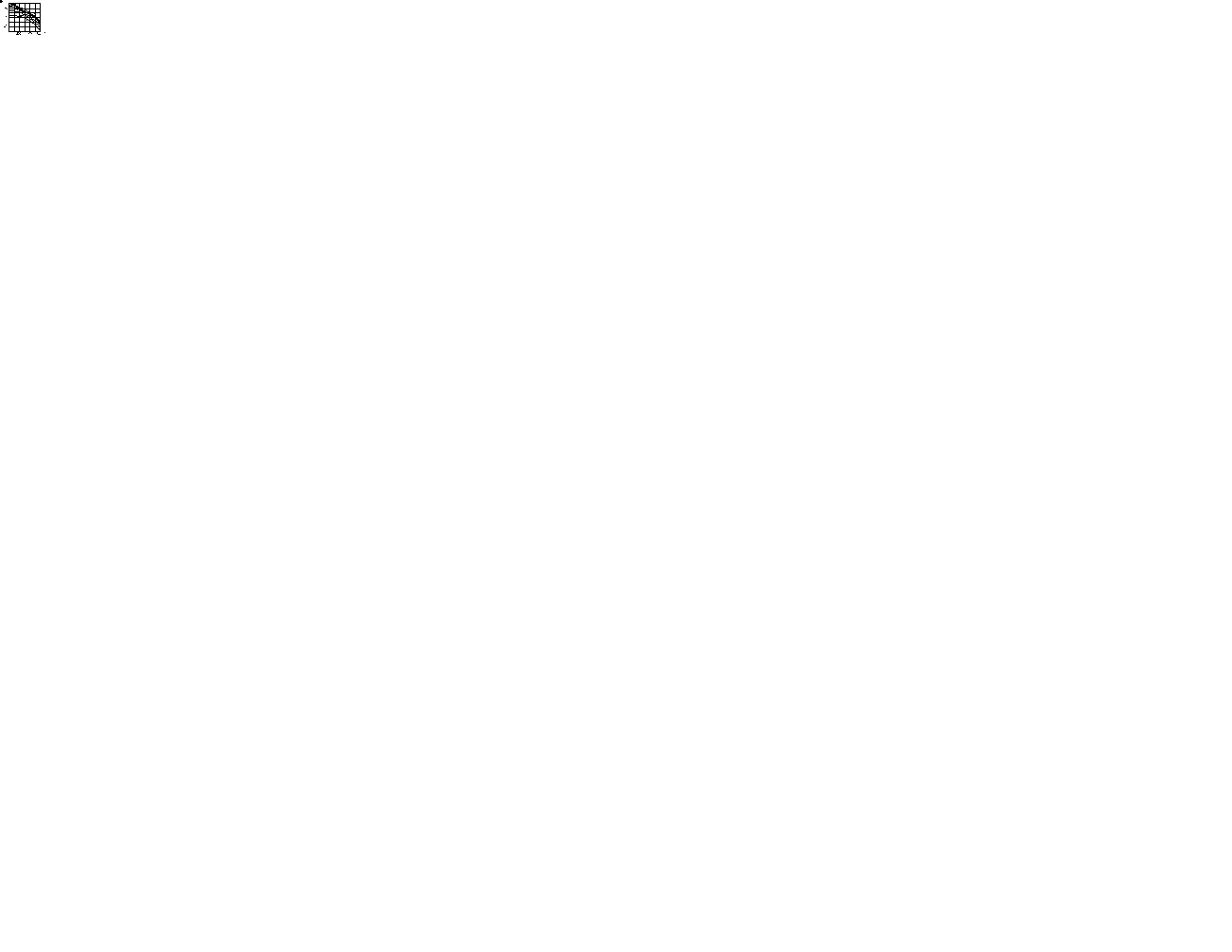
Рис. 2.48. Зависимость твердости закаленных углеродистых сталей с различным содержанием углерода от температуры отпуска
Особенности структуры оказывают большое влияние не только на механические, но и на другие физические, в том числе магнитные, свойства. Рассмотрим это на примере коэрцитивной силы .
Влияние размера частиц. Монокристалл чрезвычайно чистого железа обладает коэрцитивной силой ~ 1 А/м. Тот же самый материал в виде порошка с размером частиц ~ 200 А° может иметь коэрцитивную силу 8 .104 А/м и более. Таким образом, коэрцитивная сила может быть сильно увеличена путем уменьшения размера частиц материала. Структурно нечувствительные свойства от изменения размеров частиц не зависят.
Влияние величины зерна. Измельчение зерна однородного металла приводит к повышению коэрцитивной силы, а также к увеличению твердости и временного сопротивления разрушению. Эмпирически эта зависимость выражается следующей формулой:
, (2.99)
где - диаметр зерна, A и B - константы, причем для чистого железа A = 0,0022 (А), B = 0 (А/см); для электролитического железа: A = 0,004 (А), B = 0,32 (А/см). Очевидно, величина B обусловлена наличием примесей.
Влияние дисперсной фазы внутри зерна. Из опытов известно, что резко возрастает при выделении немагнитной фазы в мелкодисперсной форме. Примером такого влияния является выделение карбидов, нитридов и оксидов в сталях.
Если в ферромагнетике имеются мелкие включения пара- или диамагнитной фазы, то они препятствуют движению междоменных границ и затрудняют намагничивание (см. п. 3.5). При этом уменьшается проницаемость и растет коэрцитивная сила.
Для коэрцитивной силы имеется следующее оценочное выражение:
, (2.100)
где - намагниченность насыщения; - объемная доля включений; - толщина границы между доменами; - диаметр включения.
Из формулы (2.100) следует, что коэрцитивная сила зависит как от общего относительного объема включений, так и от степени их дисперсности. Причем, при коэрцитивная сила увеличивается вместе с растущим диаметром включения. В случае величина падает. Остается ожидать, что вблизи имеет максимум. Действительно, экспериментально найденная зависимость коэрцитивной силы от размера выделяющихся частиц цементита проходит через максимум. Величина , соответствующая максимуму, приблизительно равна толщине доменной границы. Если не меняется, то прирост коэрцитивной силы должен определяться объемом включений, то есть величиной .
Контроль качества закалки.По характеру зависимости магнитных свойств от температуры закалки можно выделить три группы сталей:
- доэвтектоидные низколегированные стали;
- эвтектоидные и заэвтектоидные низколегированные стали;
- высоколегированные стали.
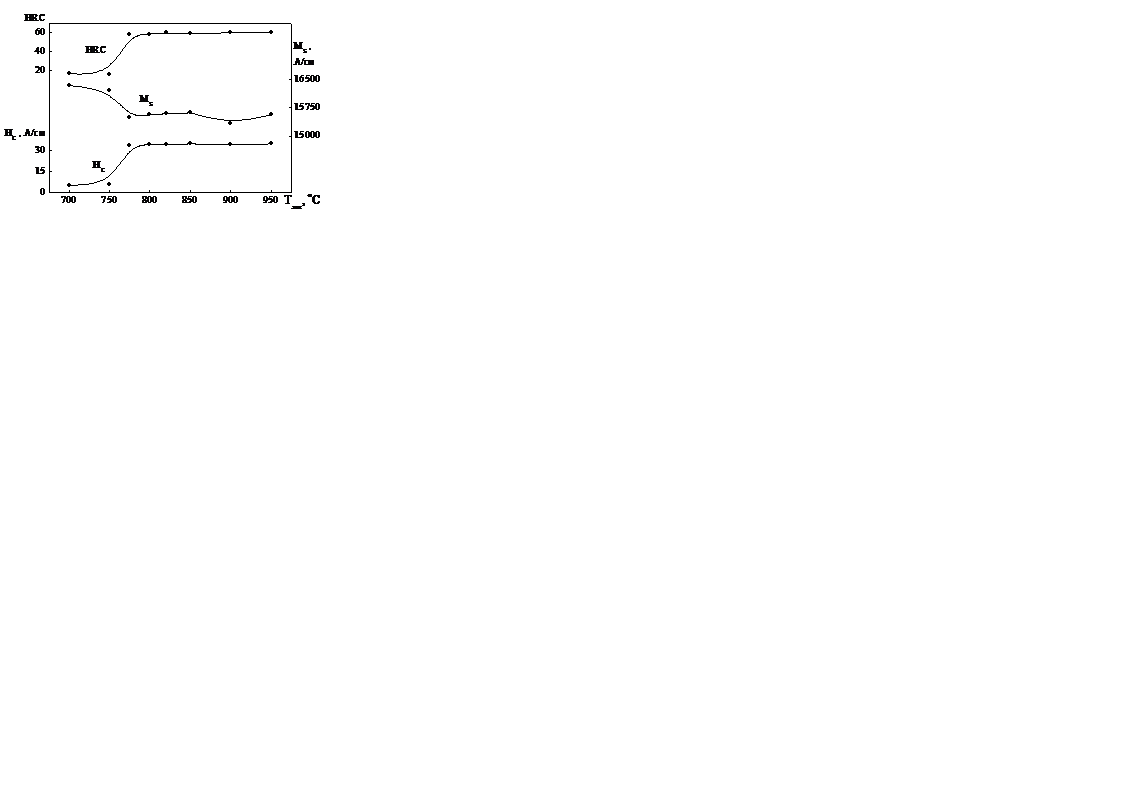
Рис. 2.49. Зависимость твердости и магнитных свойств стали 50Г
От температуры закалки
Доэвтектоидные стали. Примером является сталь 50Г (рис. 2.49). Закалка вызывает увеличение эффективной магнитной анизотропии, что обусловлено тетрагональностью решетки мартенсита и повышением уровня микронапряжений. Появление в стали мартенситной структуры (для стали 50Г - при >770 0С) приводит к расширению петель магнитного гистерезиса (коэрцитивная сила возрастает более чем в 2 раза). Снижение в интервале температур 750 - 800 оС связано с появлением в структуре закаленной стали остаточного аустенита. В результате закалки на мартенсит снижается остаточная магнитная индукция. Потери энергии на перемагничивание в целом растут. Удельное электросопротивление с повышением температуры закалки до 800 - 850 оС растет в связи с увеличением содержания углерода в пересыщенном твердом растворе и появлением некоторого количества остаточного аустенита.
Рост температуры закалки доэвтектоидных углеродистых сталей выше температуры не приводит к изменению прочностных, магнитных и электрических свойств стали. Это связано с тем, что при таких температурах закалки практически весь углерод переходит в твердый раствор, параметры решетки мартенсита стабилизируются, внутренние микронапряжения и плотность дислокаций достигают максимальной величины.
Наиболее характерным видом брака при закалке доэвтектоидных сталей является “недогрев”, при котором закалка производится с температуры ниже и в стали после охлаждения не образуется или образуется не во всем объеме мартенситная структура. Причинами такого брака могут быть недостаточный нагрев изделий в закалочной печи или слишком медленное перемещение изделий из печи в ванну с охлаждающей средой. “Недогрев” обычно выявляют по пониженным значениям коэрцитивной силы.
Эвтектоидные и заэвтектоидные стали имеют общие закономерности изменения магнитных и электрических свойств от температуры закалки с доэвтектоидными сталями. Однако в области температур перегрева при закалке заэвтектоидные стали имеют свои особенности.
Для примера рассмотрим сталь ШХ15, имеющую около одного процента углерода (рис. 2.50).
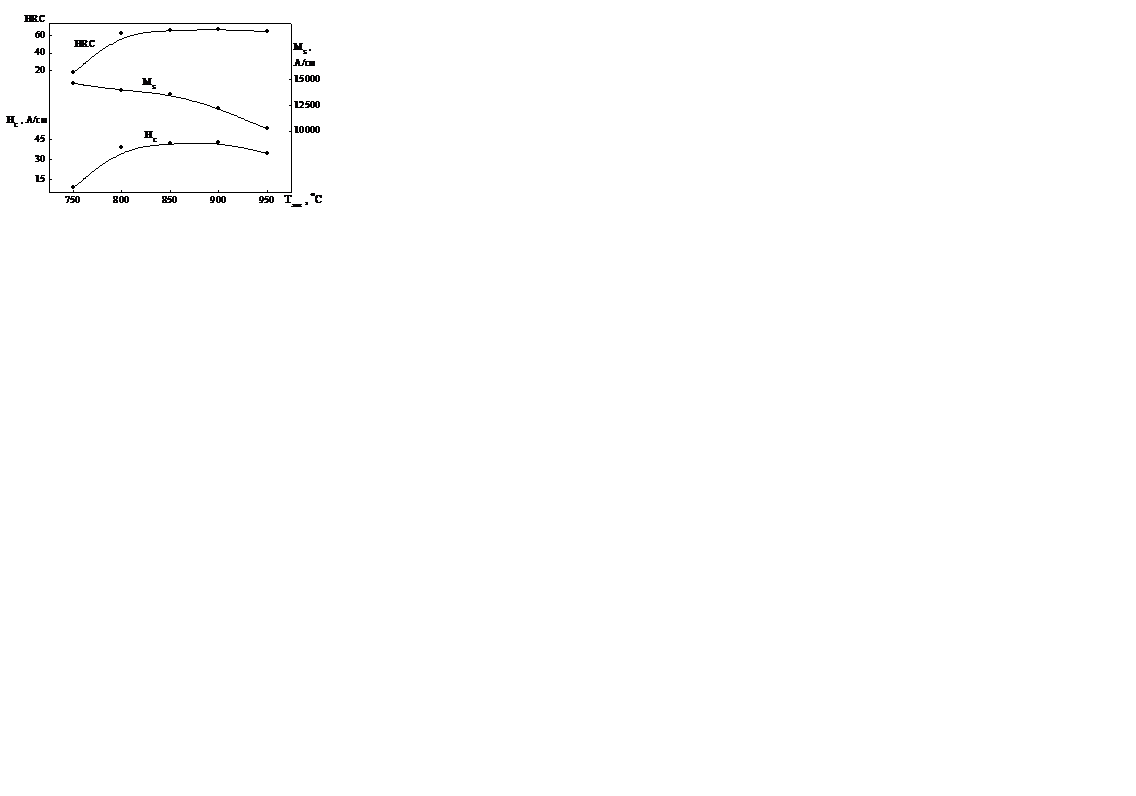
Рис. 2.50. Зависимость твердости и магнитных свойств стали ШХ15
от температуры закалки
Рост твердости и коэрцитивной силы в интервале температур закалки 700 - 800 оС обусловлен теми же причинами, что и у доэвтектоидных сталей. Однако “перегрев”, т.е. существенное превышение при закалке температуры приводит к снижению коэрцитивной силы и дополнительному снижению намагниченности насыщения. Одновременно может наблюдаться некоторое уменьшение твердости. Такое изменение свойств обусловлено появлением в структуре закаленной стали значительного количества остаточного аустенита.
Большое содержание остаточного аустенита в стали является нежелательным, поскольку он может распадаться при комнатных температурах превращаясь в мартенсит. Плотность мартенсита меньше, чем плотность аустенита и в результате указанного превращения в металле возникают дополнительные высокие растягивающие напряжения, которые могут вызвать разрушение (растрескивание) изделий.
Таким образом, для закаленных эвтектоидных и заэвтектоидных сталей необходимо выявлять как “недогрев”, так и “перегрев” при закалке. В этом случае необходимо использовать двухпараметровый контроль: “недогреву” при закалке соответствуют низкие значения коэрцитивной силы и высокие значения намагниченности насыщения, а “перегреву” – низкие значения и низкие значения .
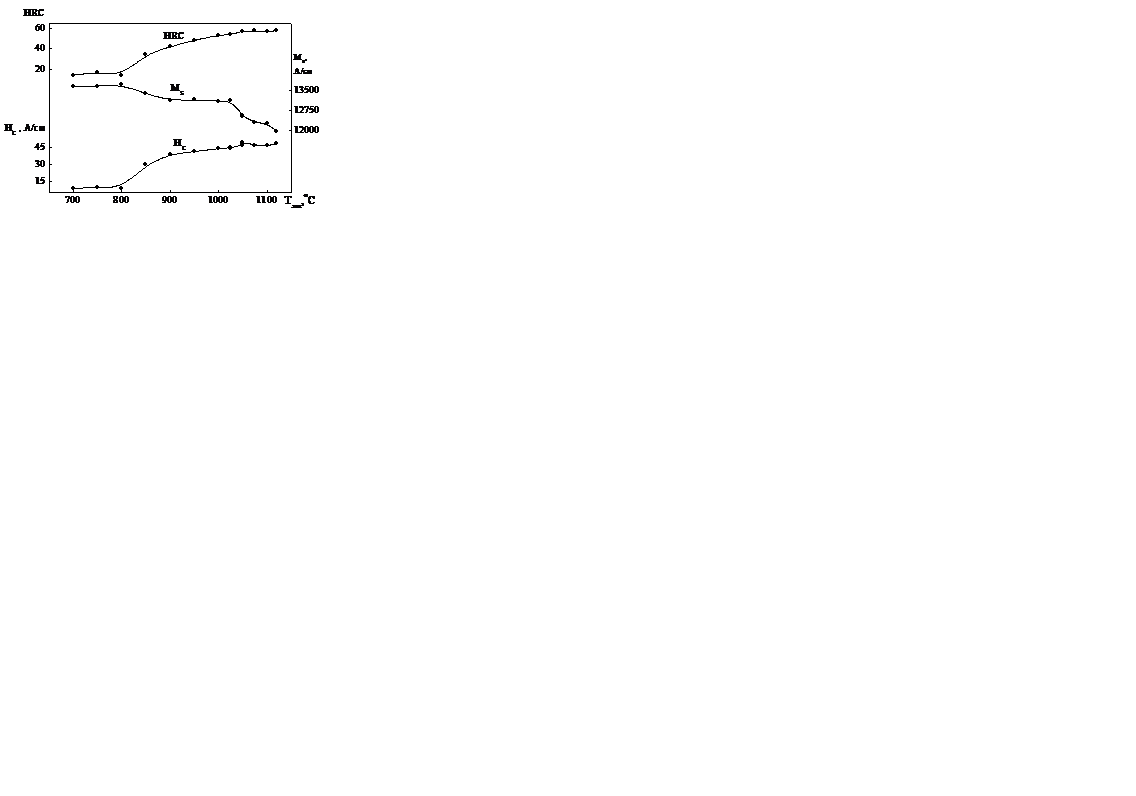
Рис. 2.51. Зависимость твердости и магнитных свойств стали 30Х13
от температуры закалки
Высоколегированные стали, примером которых является сталь 30Х13 (см. рис. 2.51), содержащая 0,3 % углерода и 13 % хрома, имеют свои особенности в поведении прочностных и магнитных свойств при вариации температуры закалки. Повышение температуры закалки выше вызывает продолжающийся рост твердости, связанный с повышением степени дисперсности (т.е. с уменьшением среднего размера частиц) карбидов хрома, что увеличивает число препятствий для смещения дислокаций и упрочняет материал. Коэрцитивная сила меняется аналогично твердости и, как правило, может быть использована для контроля закалки высоколегированных сталей. Повышенное содержание остаточного аустенита в таких сталях может быть обнаружено по снижению намагниченности насыщения.
Контроль качества отпуска. Стали различного химического состава могут иметь очень большое число особенностей в поведении прочностных и магнитных свойств при вариации температур отпуска. В научной литературе приводятся разнообразные классификации сталей по различным наборам признаков. Кроме того, ведутся работы по статистической обработке и выявлению взаимосвязей магнитных параметров контроля и химического состава закаленных и отпущенных сталей. Тем не менее, учитывая наиболее общие закономерности изменения свойств и возможности контроля качества отпуска, стали можно также разбить на три группы:
- низкоуглеродистые низколегированные стали (с содержанием углерода менее 0,3 %);
- средне и высокоуглеродистые низколегированные стали (с содержанием углерода 0,3 и более процентов);
- высоколегированные стали.
На рис. 2.52 приведены зависимости свойств низкоуглеродистой стали 09Г2 от температуры отпуска. Видно, что и твердость и коэрцитивная сила монотонно падают практически во всем диапазоне изменения температур отпуска. Наличие корреляции между этими величинами позволяет с успехом использовать коэрцитиметрические методы контроля качества отпуска низкоуглеродистых низколегированных сталей.
Как видно из рис. 2.53 и 2.54 для сталей с содержанием углерода 0,3 и более процентов характерно существенное монотонное снижение коэрцитивной силы до ~ (250-300) 0С, что делает возможным коэрцитиметрический контроль низкотемпературного отпуска.
При дальнейшем увеличении коэрцитивная сила сталей этой группы меняется слабо (рис. 2.53) или даже неоднозначно (рис. 2.54). Это означает, что контроль прочностных свойств этих сталей после средне и
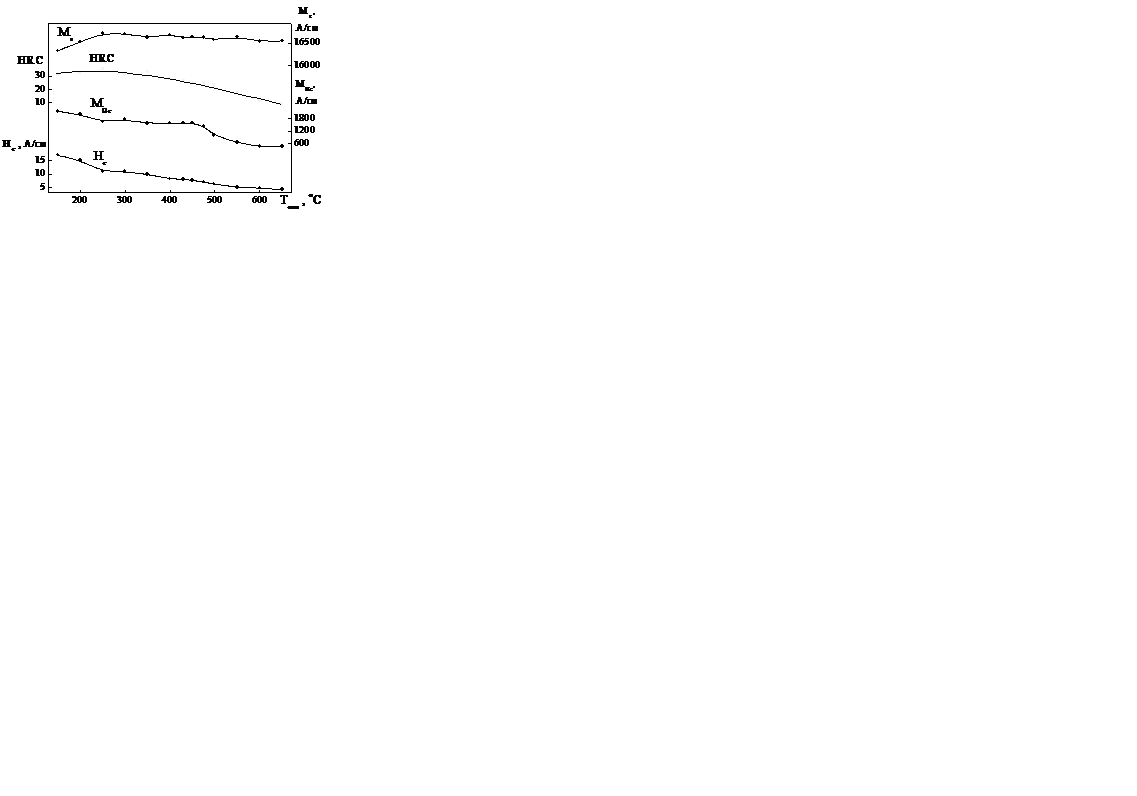
Рис. 2.52. Зависимость твердости и магнитных свойств стали 09Г2
от температуры отпуска
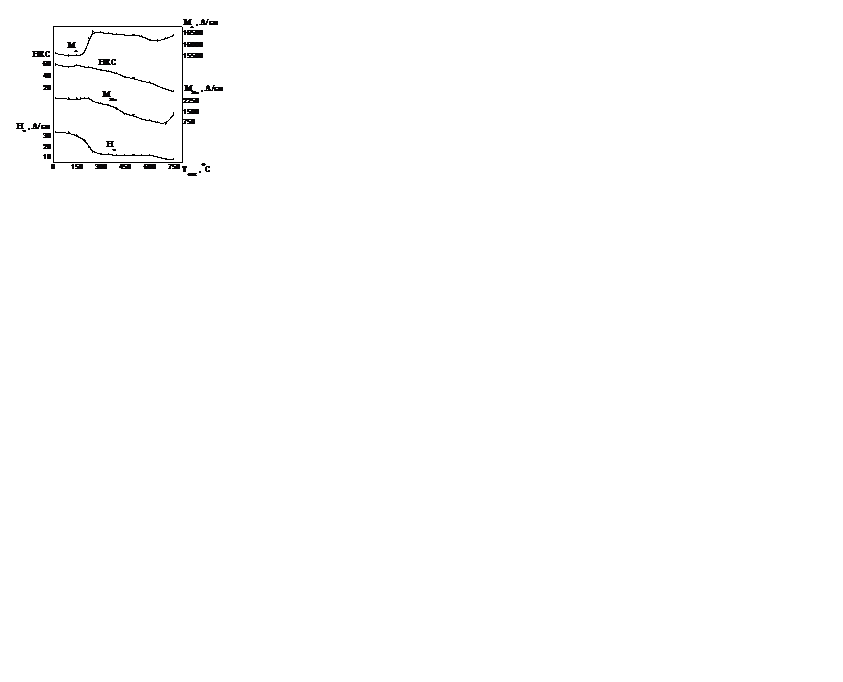
Рис. 2.53. Зависимость твердости и магнитных свойств стали 50Г
от температуры отпуска
высокотемпературного отпуска по коэрцитивной силе невозможен. Использование в качестве параметра контроля величины также невозможно из-за ее слабого изменения и технических трудностей измерения этой величины на реальных изделиях.
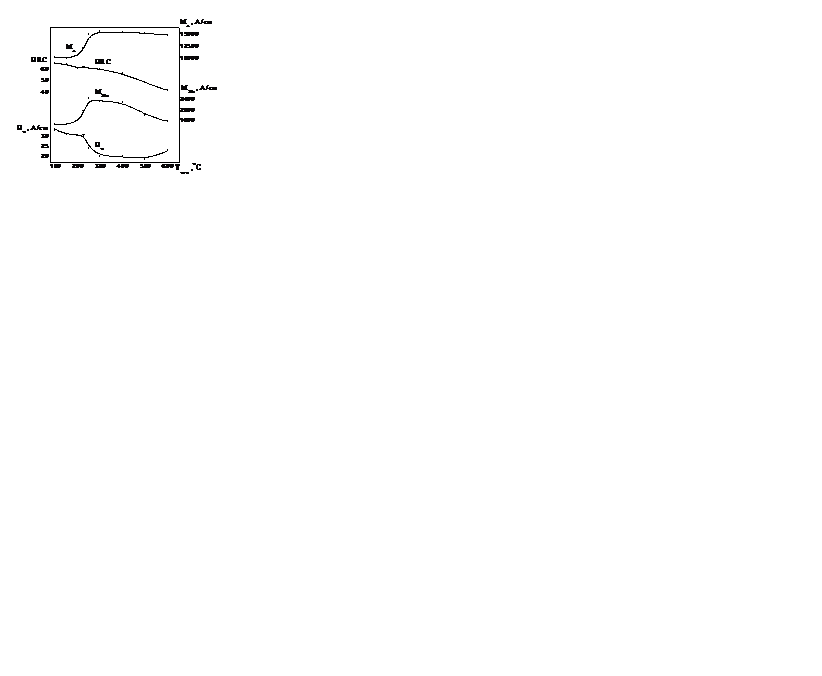
Рис. 2.54. Зависимость твердости и магнитных свойств стали ШХ15
от температуры отпуска
МНr
| Мr
|
Рис. 2.55. Фрагмент нисходящей ветви петли гистерезиса
Исследования последних лет показали, что достаточно универсальными параметрами контроля качества средне- и высокотемпературного отпуска сталей этой группы могут служить две схожих по физической природе магнитных характеристики вещества: намагниченность материала в поле релаксационной коэрцитивной силы (релаксационная намагниченность) и остаточная намагниченность, полученная после отключения поля коэрцитивной силы (намагниченность коэрцитивного возврата). Рис. 2.55 поясняет приведенные определения.
На рисунках 2.53 и 2.54 приведены зависимости более удобной для измерений намагниченности коэрцитивного возврата от температуры отпуска. Видно, что намагниченность коэрцитивного возврата монотонно уменьшается в 1,5 2 раза в диапазоне температур отпуска от (250-300) 0С до (650-700) 0С и может быть использована в качестве параметра для косвенного определения твердости сталей после закалки и последующего средне или высокотемпературного отпуска.
Как видно на примере высоколегированной стали 30Х13 (рис. 2.56) уменьшение твердости при высоких температурах отпуска также может быть определено по величине намагниченности .
Для контроля качества отпуска закаленных сталей во всем диапазоне температур следует использовать многопараметровый контроль. Например, для сталей 50Г и ШХ15 (рис. 2.53 и 2.54) - двухпараметровый с использованием в качестве параметров величин (контроль низкотемпературного отпуска) и (средне и высокотемпературный отпуск).
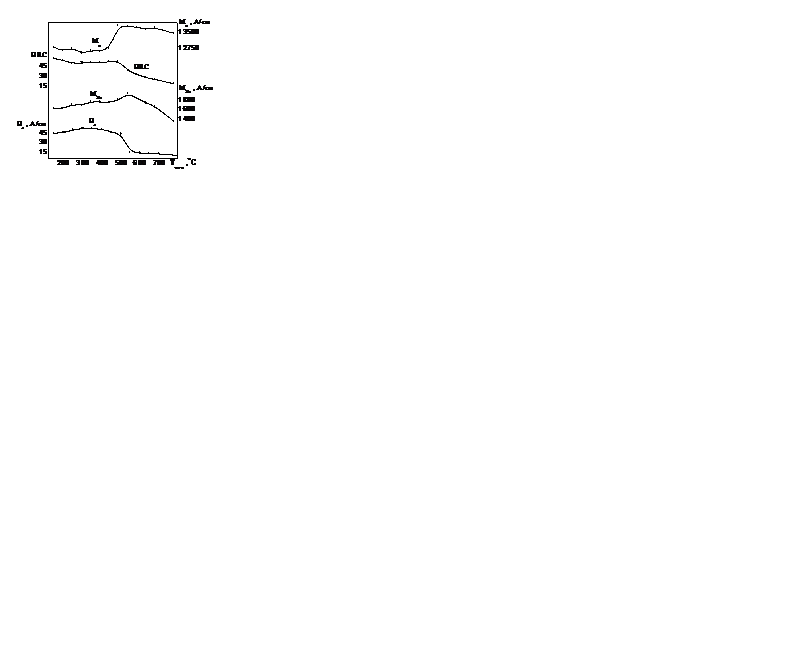
Рис. 2.56. Зависимость твердости и магнитных свойств стали 30Х13
От температуры отпуска
Не нашли, что искали? Воспользуйтесь поиском по сайту:
©2015 - 2025 stydopedia.ru Все материалы защищены законодательством РФ.
|