Расчет зубчатых цилиндрических передач
Федеральное агентство по образованию
ГОУ ВПО “Уральский государственный технический университет – УПИ”
Расчет зубчатых цилиндрических передач
Методические указания по курсам “Детали машин и основы конструирования” и “Прикладная механика” для студентов технических специальностей всех форм обучения
(электронная версия)
Составитель профессор, доктор техн. наук Г.Л.Баранов.
Научный редактор доц., канд. техн. наук Ю.В.Песин
Введение
Цилиндрические зубчатые передачи находят широкое применение в современном машиностроении. Методика прочностного расчета для цилиндрических зубчатых передач внешнего зацепления с эвольвентным профилем зуба регламентирована ГОСТ 21354-87. В соответствии с этим ГОСТом основными видами расчета на прочность таких передач являются: расчет на контактную выносливость для предотвращения усталостного выкрашивания активных поверхностей зубьев и расчет на выносливость при изгибе для предотвращения усталостного излома зуба. Расчет на контактную выносливость позволяет определить межосевое расстояние зубчатой передачи, а расчет на выносливость при изгибе позволяет определить модуль. Основными параметрами цилиндрической зубчатой передачи являются: модуль, передаточное число, межосевое расстояние и коэффициент ширины зубчатого венца. Модуль m выбирается по табл.1.
Таблица 1.
Модули по ГОСТ 9563-60
Ряды
| Значения модулей, мм
|
| 1 1.25 1.5 2 2.5 3 4 5 6 8 10
|
| 1.125 1.375 1.75 2.25 2.75 3.5 4.5 5.5 7 9
|
Межосевое расстояние awвыбирается по табл.2.
Таблица 2
Межосевые расстояния по ГОСТ 2185-66
Ряды
| Значения межосевых расстояний, мм
|
| 40 50 63 80 100 125 160 200 250 315 400 500 630 800 1000
|
| 71 90 112 140 180 225 280 355 450 560 710 900 1120 1400
|
Передаточное число uвыбирается по табл.3
Таблица 3.
Передаточные числа по ГОСТ 2185-66.
Ряды
| Значения передаточных чисел
|
| 1 1.25 1.6 2 2.5 3.15 4 5 6.3 8 10
|
| 1.12 1.4 1.8 2.24 2.8 3.55 4.5 5.6 7.1 9.0 11.2
|
Коэффициент ширины зубчатого венца yba выбирается из стандартного ряда: 0.16 0.25 0.315 0.4 0.5 0.63 0.8 1.0 по ГОСТ 2185-66.
При выборе основных параметров первый ряд следует предпочитать второму.
1. Выбор материалов зубчатых колес и способов термообработки
Наибольшее применение в редукторах находят стальные зубчатые колеса. Механические характеристики сталей, рекомендуемых для изготовления зубчатых колес, приведены в табл.4. В таблице приняты следующие обозначения: способы термообработки Н – нормализация, У – улучшение, З – закалка, Ц - цементация; Dm - наружный диаметр заготовки вал-шестерни, Sm – характерный размер заготовки для насадного зубчатого колеса (рис.1).
Таблица 4
Механические характеристики сталей
Марка стали
| Dm, мм
| Sm, мм
| Термообра
ботка
| Твердость поверхности
| Твердость сердцевины
| Предел прочно-
сти, МПа
| NHO, млн циклов
|
| Любой
| Любая
| Н
| 163-192 НВ
| 163-192 НВ
|
| 7.5
|
|
|
| У
| 192-228 НВ
| 192-228 НВ
|
| 11.2
|
| Любой
| Любая
| Н
| 179-207 НВ
| 179-207 НВ
|
| 9.17
|
|
|
| У
| 235-262 НВ
| 235-262 НВ
|
| 16.8
|
|
|
| У
| 269-302 НВ
| 269-302 НВ
|
| 23.5
| 40Х
|
|
| У
| 235-262 НВ
| 235-262 НВ
|
| 16.8
| 40Х
|
|
| У
| 269-302 НВ
| 269-302 НВ
|
| 23.5
| 40Х
|
|
| У+З (ТВЧ)
| 45-50 HRC
| 269-302 НВ
|
| 73.0
| 40ХН
|
|
| У
| 235-262 НВ
| 235-262 НВ
|
| 16.8
| 40ХН
|
|
| У
| 269-302 НВ
| 269-302 НВ
|
| 23.5
| 40ХН
|
|
| У+З (ТВЧ)
| 48-53 HRC
| 269-302 НВ
|
| 86.9
| 35ХМ
|
|
| У
| 235-262 НВ
| 235-262 НВ
|
| 16.8
| 35ХМ
|
|
| У
| 269-302 НВ
| 269-302 НВ
|
| 23.5
| 35ХМ
|
|
| У+З (ТВЧ)
| 48-53 HRC
| 269-302 НВ
|
| 86.9
| 20Х
|
|
| У+Ц+З
| 56-63 HRC
| 300-400 НВ
|
| 120.0
| 20ХНМ
|
|
| У+Ц+З
| 56-63 HRC
| 300-400 НВ
|
| 120.0
| 18ХГТ
|
|
| У+Ц+З
| 56-63 HRC
| 300-400 НВ
|
| 120.0
| 35Л
| Любой
| Любая
| Н
| 163-207 НВ
| 163-207 НВ
|
| 8.3
| 45Л
|
|
| У
| 207-235 НВ
| 207-235 НВ
|
| 12.7
| . 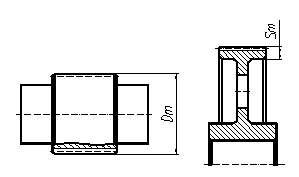
Рис.1. Характерные размеры сечения заготовки
Для ориентировочного определения Dm и Sm используются следующие формулы:
Dm=(20…24) , Sm= 1.2• , ( 1 )
где T1 – крутящий момент на шестерне в Н•м, u – передаточное число зубчатой передачи.
Коэффициент 20 в формуле для Dm используется при расчете косозубых и шевронных передач, для прямозубых передач принимается коэффициент 24. Величина Dm определяется при проектировании вал-шестерни, Sm – при проектировании насадных зубчатых колес.
Для зубчатых передач рекомендуются следующие варианты материалов и термообработок (ТО):
1- Марки сталей одинаковы для колеса и шестерни 40, 45, 40Х, 40ХН и 35ХМ.
Термообработка – улучшение. Твердость зуба шестерни 269…302 НВ, твердость зуба колеса 235…262 НВ.
2- Марки сталей одинаковы для колеса и шестерни 40, 45, 40Х, 40ХН и 35ХМ.
Термообработка зуба шестерни– улучшение с последующей закалкой ТВЧ, твердость поверхности зуба шестерни 45…50 НRC, или 48…53 НRC. Термообработка зуба колеса – улучшение, твердость зуба колеса 235…262 НВ.
3- Марки сталей одинаковы для колеса и шестерни 40, 45, 40Х, 40ХН и 35ХМ.
Термообработки колеса и шестерни одинаковы – улучшение с последующей закалкой ТВЧ, твердость поверхности зуба шестерни и колеса 45…50 НRC, или 48…53 НRC.
4- Марки сталей для колеса 40Х, 40ХН и 35ХМ. Термообработка колеса – улучшение с последующей закалкой ТВЧ, твердость поверхности зуба колеса 45…50 НRC, или 48…53 НRC. Марки сталей для шестерни 20Х, 20ХНМ и 18ХГТ. Термообработка шестерни – улучшение с последующей цементацией и закалкой, твердость поверхности зуба шестерни 56…63 НRC.
Ориентировочно диаметр заготовки зубчатого колеса определяется по формуле
dк = u•Dm.
Если диаметр заготовки колеса dк > 500 мм, то в качестве материала для колеса рекомендуется использовать стальное литье из сталей марок 35Л и 45Л.
2. Расчет допускаемых напряжений
2.1.Расчет допускаемых контактных напряжений
Допускаемые контактные напряжения определяются по формуле
HPj= ,
где j=1 для шестерни, j=2 для колеса, sHlim j - предел контактной выносливости, КHLj - коэффициент долговечности, SHj - коэффициент безопасности.
Предел контактной выносливости и коэффициент безопасности зависят от способа термической или химико-термической обработки и твердости поверхности зуба. Формулы для определения sHlim, значения SH и KHmax приведены в табл.5. Средняя твердость поверхности зуба равна НВ = 0.5 (НВmin + НВmax) или HRC = 0.5 (HRCmin + HRCmax).
Таблица 5
Данные для расчета допускаемых контактных напряжений
Способ термической или химико-термической обработки
| Средняя твердость поверхности зуба
| sHlim , МПа
| SH
| KHLmax
| Улучшение, нормализация
| < 350 НВ
| 2 НВ + 70
| 1.1
| 2.6
| Поверхностная закалка
| 40…56 HRC
| 17 HRC + 200
| 1.2
| 1.8
| Цементация и закалка
| 56…65 HRC
| 23 HRC
| 1.2
| 1.8
|
Коэффициент долговечности определяется по формуле
КHLj = 1, ( 2 )
где NHOj – базовое число циклов при действии контактных напряжений;
NHEj – эквивалентное число циклов напряжений.
Должно выполняться условие КHLj KHLmax, значения KHLmax даны в табл 5.
Значения базового число циклов, рассчитанные по формуле NHO = 30 •HB2.4 120•106, приведены в табл. 4. При определении эквивалентного числа циклов напряжений используется формула
NHE j= h•NΣj, ,
где h – коэффициент эквивалентности, определяемый по табл.6 в зависимости от типового режима нагружения, NΣj – суммарное число циклов нагружения за весь срок службы передачи.
Таблица 6
Характеристики типовых режимов нагружения
Режим нагружения
| h
| F
| Нормализация,
улучшение
q=6
| Закалка,
цементация
q=9
| 0 – постоянный
1 – тяжелый
2 – средний равновероятный
3 – средний нормальный
4 – легкий
5 – особо легкий
| 1.0
0.5
0.25
0.18
0.125
0.063
| 1.0
0.3
0.14
0.06
0.038
0.013
| 1.0
0.2
0.1
0.04
0.016
0.004
|
При постоянной частоте вращения NΣj определяется по формуле
NSj = 60•nj•c•th , ( 3 )
где nj - частота вращения колеса в об/мин, с – число зацеплений за один оборот колеса, th – суммарное время работы передачи в часах; th = L•365•24•KГ•КС•ПВ;
здесь Kг – коэффициент использования передачи в течение года; Kс – коэффициент использования передачи в течение суток; L – срок службы передачи в годах; ПВ – относительная продолжительность включения.
Расчет допускаемых контактных напряжений для зубьев шестерни и колеса sHP1 и sHP2 выполняется по формуле ( 2 ). Допускаемые контактные напряжения передачи равны
sHP=sHPjmin - для прямозубой передачи,
sHP=0.45 (sHP1+sHP2) 1.23•sHPj min - для косозубой и шевронной передач,
здесь sHPj min- меньшее из допускаемых контактных напряжений для шестерни и колеса.
2.2.Расчет допускаемых напряжений изгиба
Допускаемые напряжения изгиба определяются по формуле
,
где sF lim j - предел изгибной выносливости зубьев, SFj - коэффициент безопасности,
KFСj - коэффициент, учитывающий влияние двухстороннего приложения нагрузки,
KFLj - коэффициент долговечности, определяемый по формуле:
КFLj = 1,
здесь qj - показатель степени кривой усталости (табл.6), NFO = 106 – базовое число циклов при изгибе, NFEj – эквивалентное число циклов напряжений при изгибе.
Должно выполняться условие КFLj KFLmax.
Формулы для определения sF lim и значения SF, KFLmax и KFС для реверсивного привода приведены в табл.7. Для нереверсивного привода KFС=1.
Эквивалентное число циклов напряжений при изгибе равно:
NFE j= Fj•NΣj, ,
где NΣj определяется по формуле ( 3 ), Fj - коэффициент эквивалентности при изгибе
(табл. 6).
Таблица 7
Данные для расчета допускаемых напряжений изгиба
Термообработка
| sF lim, МПа
| SF
| KFLmax
| KFC
| Нормализация, улучшение
| 1.75 НВ
| 1.7
| 4.0
| 0.65
| Закалка ТВЧ по всему контуру (m 3 мм)
| 600…700
| 1.7
| 2.5
| 0.75
| Закалка ТВЧ сквозная с охватом впадины(m<3 мм)
| 500…600
| 1.7
| 2.5
| 0.75
| Цементация
|
| 1.65
| 2.5
| 0.75
|
3.Проектный расчет передачи
Межосевое расстояние передачи определяют из расчета на выносливость по контактным напряжениям по формуле
= •(u + 1) , ( 4 )
где = 450 для прямозубых передач, = 410 для косозубых и шевронных передач,
T1 – крутящий момент на шестерне в Н•м, КН – коэффициент контактной нагрузки, - коэффициент ширины зубчатого венца.
Коэффициент ширины зубчатого венца выбирают из ряда по ГОСТ 2185-66: при симметричном расположении шестерни относительно опор =0.315…0.5, при несимметричном =0.25…0.4, для шевронных и раздвоенных косозубых передач =0.5…0.63.
Коэффициент контактной нагрузки вычисляют по формуле
КН = KHα KHβ КНV, ( 5 )
где KHα - коэффициент неравномерности распределения нагрузки между зубьями,
KHβ – коэффициент неравномерности распределения нагрузки по ширине колеса,
КНV – динамический коэффициент.
Для определения этих коэффициентов необходимо знать размеры передачи. Поскольку на данном этапе проектного расчета размеры не известны, то рекомендуется задавать приближенное значение КН=1.2.
Полученное по формуле ( 4 ) значение округляют до ближайшего большего стандартного значения по табл.2. Модуль выбирают из диапазона m= и округляют до стандартного значения по табл.1. Модуль меньше 2 мм для силовых передач применять не рекомендуется. В косозубых передачах стандартизован нормальный модуль mn. Далее определяют суммарное число зубьев. Для прямозубых передач Z = . Рекомендуется сочетание и m выбирать таким, чтобы Z было целым. Для косозубых и шевронных передач суммарное число зубьев предварительно определяют по формуле
Z = ,
где =12 для косозубых передач и =30 для шевронных передач.
Полученное значение Z округляют до ближайшего целого числа Z и уточняют делительный угол наклона зуба по формуле = arccos .
Далее определяют число зубьев шестерни Z1= и округляют его до ближайшего целого числа. Находят число зубьев колеса Z2= Z - Z1 и фактическое передаточное число uф= . Значение uф не должно отличаться от номинального более чем на 2.5% при u 4.5 и более чем на 4% при u> 4.5.
Если Z1 Z1min, то принимают коэффициент смещения шестерни x1=0, если
Z1< Z1min , то коэффициент смещения шестерни определяют по формуле x1= . Для прямозубых передач Z1min=17, для непрямозубых - Z1min=17•cos3 . Коэффициент смещения колеса равен x2= - x1.
Ширину венца колеса определяют по формуле bw2= и округляют до ближайшего числа из ряда нормальных линейных размеров по ГОСТ 6636-69: 20 22 24 25 26 28 30 32 34 (35) 36 38 40 42 45 48 50 53 (55) 56 60 63 (65) 67 (70) 71 75 80 85 90 95 100.
Ширину венца шестерни bw1 принимают на 2…5 мм больше чем bw2.
Определяют диаметры окружностей зубчатых колес, принимая далее для непрямозубых колес m=mn:
делительные окружности прямозубых колес dj=mZj, косозубых колес ,
окружности вершин зубьев daj = dj+2 m (1+xj),
окружности впадин зубьев dfj = dj-2 m (1.25- xj).
Вычисляют окружную скорость в зацеплении:
V= .
По табл.8 назначают степень точности передачи.
Таблица 8
Степень точности передачи.
Степень точности по ГОСТ 1643-81
nст
| Скорость V, м/с
| Прямозубые
| Непрямозубые
|
| до 20
до 12
до 6
до 2
| до 30
до 20
до10 до 4
|
Степень точности nст=9 для закрытых зубчатых передач применять не рекомендуется.
4.Проверочный расчет передачи
Условие контактной прочности передачи имеет вид sHP. Контактные
напряжения определяются по формуле:
= ,
где Z = 9600 для прямозубых и Z = 8400 для косозубых и шевронных передач,
КН - коэффициент контактной нагрузки, определяется по формуле ( 5 ).
Коэффициент неравномерности распределения нагрузки между зубьями равен
KHα =1+A•(nст-5)•К ,
где А=0.06 для прямозубых и А=0.15 для косозубых и шевронных передач,
К - коэффициент, учитывающий приработку зубьев.
Таблица 9
Коэффициент K для одноступенчатых редукторов
| K
| НВ2 350
| НВ2>350
| 0.6
0.8
1.0
1.2
1.4
| 1.03
1.03
1.04
1.06
1.08
| 1.05
1.07
1.11
1.15
1.20
|
Таблица 10
Значения коэффициента KHV
Степень точности
| Твердость поверхности зубьев
| Окружная скорость в зацеплении, м/с
|
|
|
|
|
|
|
| НВ2 < 350
НВ2 350
| 1.03
1.01
1.02
1.01
| 1.09
1.03
1.06
1.03
| 1.16
1.06
1.10
1.04
| 1.25
1.09
1.16
1.06
| 1.32
1.13
1.20
1.08
| 1.48
1.19
1.30
1.12
|
| НВ2 < 350
НВ2 350
| 1.04
1.02
1.02
1.01
| 1.12
1.06
1.06
1.03
| 1.20
1.08
1.12
1.05
| 1.32
1.13
1.19
1.08
| 1.40
1.16
1.25
1.10
| 1.60
1.24
1.37
1.15
|
| НВ2 < 350
НВ2 350
| 1.05
1.02
1.03
1.01
| 1.15
1.06
1.09
1.03
| 1.24
1.10
1.15
1.06
| 1.38
1.15
1.24
1.09
| 1.48
1.19
1.30
1.12
| 1.72
1.29
1.45
1.18
|
| НВ2 < 350
НВ2 350
| 1.06
1.02
1.03
1.01
| 1.17
1.06
1.09
1.03
| 1.28
1.11
1.17
1.07
| 1.45
1.18
1.28
1.01
| 1.56
1.22
1.35
1.14
| 1.84
1.34
1.52
1.21
|
Примечание: в числителе значения для прямозубых передач,
в знаменателе для непрямозубых.
Для плохо прирабатывающихся зубчатых колес с твердостью поверхности зуба НВ2>350 принимают К =1. Если НВ2 350, то К определяют по формуле:
К =0.002•НВ2+ 0.036•(V-9),
где V-окружная скорость в зацеплении.
Динамический коэффициент КНV определяется по табл.10 .
Коэффициент неравномерности распределения нагрузки по ширине колеса равен
KHβ = 1+ (K -1) К ,
где K - коэффициент распределения нагрузки в начальный период работы (табл.9).
В таблице значение K дано в зависимости от коэффициента ширины венца по диаметру , величина которого определяется выражением =0.5 (u + 1).
Допускается перегрузка по контактным напряжениям не более 5%, рекомендуемая недогрузка до 15%. Если указанные условия не выполняются, то следует либо изменить межосевое расстояние передачи, либо изменить , либо выбрать другие материалы зубчатых колес и повторить расчет.
Условия изгибной прочности передачи имеют вид sFj sFPj. Напряжение изгиба в зубьях шестерни определяется по формуле:
,
где YFj - коэффициенты формы зуба, КF - коэффициент нагрузки при изгибе, Yb - коэффициент, учитывающий влияние угла наклона зуба на его прочность, Yb=1 для прямозубых передач, Yb=0.52 для косозубых передач и Yb=0.48 для шевронных передач.
Напряжение изгиба в зубьях колеса равно:
.
Коэффициенты формы зуба даны в ГОСТ 21354-87 в виде графиков, которые аппроксимируются зависимостью:
YFj=3.47+ +0.092• ,
где ZVj - эквивалентное число зубьев, для прямозубых передач ZVj= Zj, для непрямозубых передач ZVj= .
Коэффициент нагрузки при изгибе определяют по формуле: KF = KFα KFβ KFV. Коэффициенты, входящие в эту формулу, имеют такой же физический смысл, что и коэффициенты в формуле для КН. Для их определения используют следующие зависимости: KFα =1 для прямозубых передач, KFα=1+A•(nст-5) для непрямозубых передач, KFβ = 0.18+0.82 K , KFV = 1+1.5•(KHV-1) при НВ2 <350 и KFV = KНV при НВ2 350.
Допускается перегрузка по напряжениям изгиба не более 5%, недогрузка не регламентируется. Если перегрузка более 5% следует увеличить модуль передачи и повторить расчет.
5. Силы в зацеплении
Окружная сила Ft= . Распорная сила: в прямозубых передачах Fr= Fttg , в непрямозубых передачах Fr= Ft• . Осевая сила в косозубых передачах Fа= Ft•tg .
Приложения
Таблица 11
Электродвигатели асинхронные серии 4А, закрытые
обдуваемые (по ГОСТ 19523-81)
Мощ-ность, кВт
| Синхронная частота вращения, об/мин
|
|
|
|
| Типо
размер
| S,
%
| d, мм
| Типо
размер
| S,
%
| d, мм
| Типо
размер
| S,
%
| d, мм
| Типо
размер
| S,
%
| d, мм
| 1.1
1.5 2.2
3.0
4.0 5.5
7.5
18.5
| 71В2
80А2
80В2
90L2
100S2
100L2
112M2
132M2
160S2
160M2
180S2
180M2
200M2
200L2
225M2
250S2
250M2
| 6.3
4.2
4.3
4.3
3.3
3.4
2.5
2.3
2.1
2.1
2.0
1.9
1.9
1.8
1.8
1.4
1.4
|
28 32
| 80A4
80B4
90L4
100S4
100L4
112M4
132S4
132M4
160S4
160M4
180S4
180M4
200M4
200L4
225M4
250S4
250M4
| 5.4
5.8
5.1
4.4
4.7
3.7
3.0
2.8
2.3
2.2
2.0
1.9
1.7
1.6
1.4
1.2
1.3
|
| 80B6
90L6
100L6
112MA6
112MB6
132S6
132M6
160S6
160M6
180M6
200M6
200L6
225M6
250S6
250M6
280S6
280M6
| 8.0
6.4
5.1
4.7
5.1
3.3
3.2
2.7
2.6
2.7
2.8
2.1
1.8
1.4
1.3
2.0
2.0
|
38 38
| 90LB8
100L8
112MA8
112M8
132S8
132M8
160S8
160M8
180M8
200M8
200L8
225M8
250S8
250M8
280S8
280M8
315S8
| 7.0
7.0
6.0
5.8
4.1
4.1
2.5
2.5
2.5
2.3
2.7
1.8
1.5
1.4
2.2
2.2
2.0
|
38 48
|
Таблица 12
Значения КПД механических передач
Передача
| КПД
| Зубчатая цилиндрическая
Зубчатая коническая
Червячная при числе заходов червяка:
Z1=1
Z1=2
Z1=3
Цепная закрытая
Цепная открытая
Плоскоременная
Клиноременная
| 0.98
0.97
0.72
0.82
0.87
0.96
0.92
0.97
0.96
|
Примечание: КПД пары подшипников качения =0.99.
Не нашли, что искали? Воспользуйтесь поиском по сайту:
©2015 - 2025 stydopedia.ru Все материалы защищены законодательством РФ.
|