Дефекты кристаллического строения реальных кристаллов
Пермский военный институт внутренних войск
МВД России
КОНСТРУКЦИОННЫЕ МАТЕРИАЛЫ
И ТЕХНОЛОГИЯ ОБРАБОТКИ
Учебное пособие
Пермь, 2011
УДК 621.791
Рецензенты:
д-р техн. наук, проф. Ю.Д.Щицын
(Пермский государственный технический университет);
д-р техн. наук, проф. В.Я.Беленький
(Пермский государственный технический университет)
Косолапов О.А., Ериков А.П., Логинов В.В., Цимберов Д.М.
Материаловедение и технология конструкционных материалов. Учебное пособие. – Пермь: ПВИ ВВ МВД России, 2011. – 84 с.
Описаны атомно-кристаллическое строение металлов, свойства металлов, строение и свойства сплавов, термическая, химико-термическая, термомеханическая обработка стали, способы повышения надёжности работы машин.
Описаны материалы, применяемые для изготовления деталей машин и конструкций, приведена их классификация и маркировка, указаны области их применения.
Курс лекций предназначен для курсантов, изучающих дисциплину «Материаловедение и технология конструкционных материалов».
УДК 621.791
Раздел 1. КОНСТРУКЦИОННЫЕ МАТЕРИАЛЫ
Атомно-кристаллическое строение металлов
Кристаллические решетки металлов
Все металлы в твердом состоянии имеют кристаллическое строение, их атомы располагаются в пространстве с определенной закономерностью, образуя кристаллическую решетку.
Наименьшая часть объема кристаллической решетки, которая определяет ее систему, называется элементарной кристаллической ячейкой. Любое кристаллическое тело можно представить построенным из элементарных кристаллических ячеек, многократно повторяемых в направлениях осей координат (рис. 1, а).
Кристаллическим веществам свойственна анизотропия свойств, они имеют различные свойства в разных направлениях. Это объясняется тем, что число атомов, приходящееся на то или иное плоское сечение кристаллической решетки, неодинаково.
Металлы имеют кристаллические решетки различных типов. Чаще всего встречаются три типа: кубическая объемно-центрированная (ОЦК), кубическая гранецентрированная (ГЦК) и гексагональная плотноупакованная кристаллические решетки.
В элементарной ячейке кубической объемно-центрированной решетки (рис. 1, б) содержится девять атомов: восемь располагаются по узлам ячейки и один атом - в центре (Mo, W, Na, K, Fea и др.).
В элементарной ячейке кубической гранецентрированной решетки (рис. 1, в) находится четырнадцать атомов, которые расположены в углах ячейки и в центре каждой грани (Ni, Cu, Al, Fe, и др.).
В элементарной ячейке гексагональной плотноупакованной решетки (рис. 1, г) содержится семнадцать атомов, которые расположены в углах ячейки и центрах шестигранных оснований призмы и три атома в средней плоскости призмы (Mg, Zn, Tia и др.).
Полиморфизм
Полиморфизмом или аллотропией называют способность металла в твердом состоянии при изменении температуры перестраивать свою кристаллическую решетку. Полиморфные превращения сопровождаются выделением или поглощением теплоты, а также изменением свойств металла. Различные аллотропические состояния называют модификациями. Каждая модификация устойчива лишь в пределах определенного для данного металла интервала температур. Аллотропические формы обозначаются греческими буквами a, b, g и т.д. На кривых охлаждения и нагрева переход из одного состояния в другое характеризуется остановкой (для чистых металлов) или изменением характера кривой (для сплавов), что связано с выделением или поглощением теплоты. При аллотропических превращениях кроме изменения свойств (теплопроводности, электропроводности, механических, магнитных и др.) наблюдают изменения объема металла и растворимости (например, углерода в железе). Аллотропические превращения свойственны многим металлам (железу, олову, титану и др.).
Железо известно в двух полиморфных модификациях - a и g. На рис. 2 приведена кривая охлаждения железа.
Железо при комнатной температуре обладает ОЦК решеткой; эту модификацию называют a-железом. При нагреве до 768 °С a-железо теряет магнитные свойства, кристаллическая решетка при этом не меняется. При 911 °С ОЦК решетка в железе превращается в ГЦК; железо с такой решеткой называют g-железом. При 1392 °С g-железо превращается в d-железо с ОЦК решеткой, существующее до температуры плавления 1539 °С.
Дефекты кристаллического строения реальных кристаллов
В кристаллах всегда имеются дефекты (несовершенства) строения, вызванные нарушением расположения атомов в кристаллической решетке. Характер и степень нарушения правильности кристаллического строения влияют на свойства металлов. Дефекты кристаллического строения по геометрическим признакам подразделяют на точечные, линейные и поверхностные.
К точечным дефектам (рис. 3), размеры которых по всем трем пространственным координатам соизмеримы с размером атома, относят вакансии, межузельные атомы и примесные атомы.
Отсутствие атома в узле кристаллической решетки называется вакансией (рис. 3, а).
Межузельные дефекты образуются в результате перехода атома из узла решетки в межузлие кристаллической решетки (рис. 3, б) или внедрение в решетку инородного (примесного атома). Точечные дефекты приводят к искажению кристаллической решетки и снижению прочности металлов.
Дислокации - это линии, вдоль и вблизи которых нарушено правильное периодическое расположение атомных плоскостей кристалла. Различают два вида дислокаций - краевые и винтовые.
Краевая дислокация (рис. 4), представляет собой местное искажение кристаллической решетки из-за наличия лишней полуплоскости, называемой экстраплоскостью.
Область несовершенства кристалла вокруг края экстраплоскости и называется краевой дислокацией.
Поверхностные дефекты (рис. 5) представляют собой поверхности раздела между отдельными кристаллитами и их блоками. На границе зерен расположение атомов менее правильное, чем в зерне.
Вакансии, дислокации и другие дефекты атомно-кристаллического строения оказывают существенное влияние на свойства металлов и сплавов. Дислокации облегчают пластическое деформирование металла.
Кристаллизация металлов
Как известно, металлы и сплавы находятся в трех агрегатных состояниях - твердом, жидком и газообразном. Переход металла из жидкого состояния в твердое (кристаллическое) называется кристаллизацией, в газообразное - сублимацией.
На рис. 6 приведена схема кристаллизации металла. До тех пор, пока формирующийся вокруг центра кристаллизации кристалл окружен жидким расплавом металла, он имеет правильную геометрическую форму, но при столкновении и срастании кристаллов их правильная форма нарушается и образуются так называемые кристаллиты - зерна. Величина зерна зависит от числа центров кристаллизации и скорости роста. Чем больше степень охлаждения, тем больше центров кристаллизации и меньше размер зерна. Чем мельче зерно, тем выше механические свойства металла (сплава); особенно это сказывается на пластичности.
Обычно механизм образования кристаллов носит дендритный характер. Это связано с тем, что развитие зародышей протекает, главным образом, в тех направлениях решетки, которые имеют наибольшую плотность упаковки атомов и минимальное расстояние между ними. В этих направлениях образуются ветви - оси первого порядка I (рис. 7).От осей первого порядка начинают расти новые оси второго порядка II, от осей второго порядка - оси третьего порядка III и т.д.
На рис. 8 показана схема строения металлического слитка.
При кристаллизации слитка в результате соприкосновения металла с холодной стенкой изложницы, образуется зона мелких равноосных кристаллов 1. Зона столбчатых кристаллов 2 имеет направленный характер в связи с тем, что они растут от стенки изложницы к центру по направлению отвода тепла. Зона 2 еще более замедляет отдачу тепла наружу, скорость охлаждения еще более уменьшается, поэтому в центре слитка образуется зона крупных неориентированных кристаллов 3.
Свойства металлов
Различают механические, физические, химические, технологические, эксплуатационные свойства металлов.
Механические свойства
Механические свойства характеризуют состояние металлов при воздействии внешней нагрузки. Внешняя нагрузка создает в металле напряжения, равные отношению нагрузки к площади сечения испытуемого образца
.
Напряжения вызывают деформацию металлического образца (изменение формы и размеров под влиянием внешней нагрузки) - упругую, исчезающую после снятия нагрузки, или пластическую, остающуюся после снятия нагрузки. Способность металла сопротивляться деформации и разрушению характеризует его прочность.
Прочностьметаллов определяют на специальных образцах их растяжением, сжатием, изгибом, кручением. Чаще прочность металла характеризуют пределом прочности при растяжении временным сопротивлением sв Па:
,
где Рв - максимальная нагрузка, которую выдержал образец перед
разрушением, Н;
F0 - начальное сечение образца, мм2.
Образец, закрепленный в захватах разрывной машины, деформируется при статической, плавно возрастающей нагрузке со скоростью 2…15 мм/мин. При испытании, как правило, автоматически записывается диаграмма растяжения, выражающая зависимость между нагрузкой и деформацией.
На рис. 9 приведена диаграмма растяжения малоуглеродистой отожженной стали. При нагрузке, соответствующей начальной части диаграммы, материал испытывает только упругую деформацию, которая полностью исчезает после снятия нагрузки. До точки а эта деформация пропорциональна действующему напряжению (нагрузке), что выражается законом Гука: [s = Р/F0 - напряжение в металле, Мн/м2 (кгс/мм2); Р - приложенная нагрузка, МН (кгс); F0 - начальная площадь поперечного сечения образца, мм2; Dl - абсолютное удлинение, мм; l0 - начальная длина образца, мм].
Важнейшей характеристикой упругой прочности является предел упругости. Теоретический предел упругости - максимальное напряжение, до которого образец получает только упругую деформацию, т.е. (рис. 9, а).
Ввиду трудности определения sуп практически пользуются условным пределом упругости, под которым понимают напряжение, вызывающее остаточную деформацию 0,005…0,05 % от начальной длины образца.
Нагрузке в точке а, определяющей конец прямолинейного участка диаграммы растяжения, соответствует предел пропорциональности.
Теоретический предел пропорциональности - максимальное напряжение, до которого сохраняется линейная зависимость между напряжением (нагрузкой) и деформацией (см. рис. 9, а) .
Для большинства материалов теоретические пределы упругости и пропорциональности близки по величине.
Физический предел текучести - напряжение, при котором происходит увеличение деформации при постоянной нагрузке .
На диаграмме растяжения пределу текучести соответствует горизонтальный участок с - d: пластическая деформация (удлинение) - «течение» металла при постоянной нагрузке.
Большая часть технических металлов и сплавов не имеет площадки текучести. Для них наиболее часто определяется условный предел текучести, под которым понимают напряжение, вызывающее остаточную деформацию % l0, т.е. равную 0,2 % от начальной расчетной длины образца (см. рис. 9, б), или .
В точке В, в наиболее слабом месте образца начинается образование «шейки» - сужения поперечного сечения, деформация из равномерной переходит в местную. Напряжение в материале в этот момент испытания называют пределом прочности.
Предел прочности sв - напряжение, соответствующее максимальной нагрузке, которую выдерживает образец до разрушения: .
Пластичность - способность тела (металла) получать остаточное изменение формы и размеров без нарушения сплошности. Пластичность характеризуется относительным удлинением и относительным сужением, определяемыми при испытаниях на растяжение.
Относительное удлинение
,
где l0 и lк - начальная и конечная длина образца;
Dlост - абсолютное удлинение образца, определяемое измерением
образца после разрыва или по диаграмме растяжения (см. рис. 9).
Относительное сужение
,
где F0 - начальная площадь поперечного сечения образца;
Fк - конечная площадь поперечного сужения образца в шейке после
разрыва.
Твердость материала - сопротивление проникновению в его поверхность стандартного тела - наконечника (индентора), например шарика, конуса и т.п., недеформирующегося при вдавливании.
Твердость измеряют методами Бринеля, Роквелла, Виккерса и др.
Твердость по Бринелю определяют статическим вдавливанием в испытуемую поверхность под нагрузкой Р стального закаленного шарика диаметром D (рис. 10, а). Число твердости НВ определяют отношением нагрузки Р к сферической поверхности отпечатка - лунки (шарового сегмента) F диаметром d т.е.
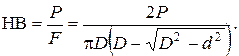
По методу Роквелла (рис. 10, б) в испытуемую поверхность вдавливают индентор - алмазный конус с углом при вершине 120° или стальной шарик малого диаметра. Число твердости HR обратно пропорционально глубине внедрения индентора.
В зависимости от шкалы прибора введены следующие обозначения чисел твердости: HRA, HRB и HRC. Шкалы С и А используют при измерении твердых, очень твердых (твердость > 450 НВ) и тонких материалов. Шкала В предназначена для испытания мягких материалов.
Метод Виккерса (рис. 10, в) позволяет измерять твердость как мягких, так и очень твердых материалов. Этим методом можно измерять твердость очень тонких изделий, а также твердость поверхностных слоев, например, при обезуглероживании, поверхностном наклепе, цементации и т.д.
Твердость по Виккерсу определяют путем статического вдавливания в испытуемую поверхность алмазной четырехгранной пирамиды с углом a = 136° между противоположными гранями (рис. 10, в). Число твердости
,
где d - величина диагонали отпечатка;
Р = 50…1000 Н (5…100 кгс).
Вязкостьявляется одним из основных механических свойств. Она выражает способность материала поглощать работу внешних сил за счет пластической деформации. Для оценки вязкости материалов и установления их склонности к переходу из вязкого в хрупкое состояние наиболее часто проводят ударные испытания на маятниковом копре надрезанных образцов по схеме (рис. 11). Характеристикой вязкости является ударная вязкость.
Ударная вязкость КС представляет собой работу (необходимую для разрушения), отнесенную к рабочей площади поперечного сечения образца.
Дж/м2.
где А - работа, затраченная на разрушение образца;
F0 - площадь поперечного сечения образца в месте надреза.
В зависимости от формы надреза ударную вязкость обозначают коэффициентом КС с соответствующей последующей буквой (KCV, KCU, KCT).
Усталость. Детали машин могут подвергаться воздействию повторно-переменных (циклических) напряжений. В пределах цикла напряжения могут принимать наибольшее и наименьшее значения. Циклы характеризуются коэффициентом асимметрии , если , то цикл симметричный и .
Постепенное накопление повреждений в металле, возникающее при действии циклических нагрузок, приводит к образованию трещин и разрушению. Это явление называется усталостью. Свойство же металлов противостоять усталости называется выносливостью.
По результатам специальных испытаний строят кривые усталости (рис. 12, б). Пределу выносливости (s-1 - при симметричном или sR - несимметричном циклах) соответствует напряжение smax, не вызывающее разрушения образцов при бесконечно большом числе циклов нагружений N. Введены базы испытаний: для стали 1 - не менее 10×106 циклов и цветных сплавов 2 - не менее 100×106 циклов.
Не нашли, что искали? Воспользуйтесь поиском по сайту:
©2015 - 2025 stydopedia.ru Все материалы защищены законодательством РФ.
|