Структурное упрочнение материала износостойкого покрытия
Структурное упрочнение материала износостойкого покрытия является основным направлением совершенствования его свойств, так как изменение физико-механических свойств покрытия отражается на взаимодействии покрытия как с обрабатываемым материалом, так и с инструментальной основой. Прочность материала покрытия оценивается уровнем предела текучести. Однако при анализе механизмов упрочнения необходимо рассмотрение не только зависимости «предел текучести – микроструктура», но и зависимости «вязкость разрушения – микроструктура» [17]. Поэтому для оценки возможности реального, эффективного упрочнения материала покрытия, т. е. повышение предела текучести σт без существенного снижения вязкости разрушения KICП, необходимо сопоставлять механизмы увеличения предела текучести с допустимыми изменениями вязкости разрушения. В современной дислокационной теории пластической деформации и разрушения предел текучести и вязкость разрушения являются функциями следующих параметров:
σт, KICП = f(σп, σд, σр, σф, σз), (1)
где σп – напряжение Пайерлса-Набарро (напряжение трения кристаллической решетки); σд – упрочнение увеличением числа дефектов решетки (вакансий и дислокаций); σр – упрочнение растворенными атомами; σф – упрочнение дисперсными фазами, имеющимися или специально созданными в структуре покрытия; σз – упрочнение микроструктурными барьерами на пути движущихся дислокаций в виде границ зерен, границ двух фаз, узких прослоек второй фазы.
Влияние отдельных механизмов упрочнения суммируется в общее упрочнение. Повышение напряжения трения решетки матрицы σп приводит к некоторому росту предела текучести, но одновременно резко снижается критическое напряжение разрушения. Напряжение Пайерлса-Набарро сильно зависит от типа связи и увеличивается при усилении доли ковалентности в межатомной связи. Торможение дислокаций рельефом Пайерлса – процесс низкотемпературный. Так в железе сила Пайерлса определяет подвижность дислокаций при температуре ниже 0,03Тпл и лишь в ковалентных кристаллах Si, Ge, SiC, Si3N4 вплоть до 0,45Тпл. Поэтому необходимо учитывать влияние напряжение Пайерлса-Набарро на прочность износостойких покрытий.
Покрытия, получаемые физическим осаждением из паровой фазы, как показывают исследования, имеют число дислокаций, близкое к критическому (~1016 м -2), поэтому упрочнение, связанное с увеличением их числа практически неосуществимо. Процесс нанесения износостойкого покрытия на режущий инструмент протекает в среде реакционных газов в камере. В результате плазмохимических реакций между парами материала катода и реакционными газами происходит образование материала покрытия в виде соединения Ме-Х.
Упрочнение растворенными атомами
Упрочнение растворенными атомами при формировании износостойких покрытий является основным механизмом изменения физико-механических свойств, так как покрытия конструируются на базе концентрированных твердых растворов или химических соединений. Изменяя состав твердого раствора, можно оптимизировать его физико-механические характеристики за счет изменения типа химической связи. Модифицирование твердых растворов за счет легирования материала покрытия технологически осуществимо по двум механизмам [5]:
1. Раствор замещения в подрешетке металлоида. Процесс осуществляется за счет направленного изменения состава газовой среды в камере и наличия остаточных газов в камере. В этом случае образовывается соединение по типу МеХ1Х2.
2. Раствор замещения в подрешетке металла. Процесс осуществляется за счет направленного «подпыления» различных элементов. В этом случае образовывается соединение по типу Ме1Ме2Х.
Возможно также протекание обоих механизмов одновременно с образованием сложных соединений. В соединениях по первому типу введение второго металлоида меняет и число электронов на атом, усиливая ковалентную связь, и отклонение от стехиометрии. Внедрение в подрешетку металлоида Х1 другого металлоида Х2 приводит к искажениям кристаллической решетки из-за большей силы связи Х1-Х2. Изменяя объем и жесткость связей, металлоид Х2 участвует в более сильном закреплении дислокаций на примесных атомах [5]. Для такого соединения наблюдаются экстремальные зависимости прочности при изгибе и твердости.
Твердорастворное упрочнение материала покрытия по второму механизму имеет значительно более широкие возможности. Все легирующие элементы в этом случае подразделяются на две большие группы [3]:
· элементы, образующие соединения с неограниченной растворимостью;
· элементы, образующие соединения с ограниченной растворимостью или не взаимодействующие между собой.
При легировании твердого раствора TiN к элементам первой группы относятся Zr, Mo, Cr, V, Ta, Nb, Hf. Они также как нитрид титана образуют нитриды с ГЦК решеткой, обладают высокой твердостью и износостойкостью. В силу их взаимной неограниченной растворимости с нитридом титана состав покрытия можно регулировать в широких пределах и тем самым подбирать его свойства.
Среди нитридообразующих элементов второй группы выделяют Al, Fe, Si, В. Ограниченная взаимная растворимость таких нитридов, а также наличие тройных соединений позволяет предположить, что в покрытиях на основе нитрида титана, легированного элементами второй группы, кроме механизма твердорастворного упрочнения возможно действие механизма дисперсионного упрочнения. Элементы второй группы являются относительно дешевыми и распространенными материалами. Легирующий элемент Ме2 взаимодействует как с металлом так и с металлоидом. При этом действие различных механизмов упрочнения в разной степени влияет на формирование свойств покрытия. Из многих воздействий легирующего элемента на металлоид наиболее явное – изменение термодинамической активности примеси Х. Ближний порядок «замещение-внедрение» дает такой тип препятствий, как пары Ме2-Х. В зависимости от поля смещений пара Ме2-Х как препятствие может оказаться сильнее одиночного атома внедрения. Поэтому упрочнение материала покрытия легированием по второму механизму влияет на величину силы Пайерлса. Это проявляется в увеличении внутреннего трения и, следовательно, предела текучести растворов типа Ме1Ме2Х, причем с повышением температуры это изменение проявляется более отчетливо.
Упрочнение микроструктурными барьерами
Упрочнение микроструктурными барьерами для движения дислокаций (границы зерен, раздел двух фаз, прослойки второй фазы) также может быть эффективным методом повышения прочности. При нанесении покрытий упрочнение микроструктурными барьерами может реализовываться при создании микрослойных материалов. Этому способствуют протекающие при нанесении покрытия процессы испарения (распыления) и конденсации, которые открывают практически неограниченные возможности в конструировании микрослойных покрытий. Варьируя толщину чередующихся микрослоев, можно в широких пределах регулировать механические свойства таких материалов.
Соответствующим выбором материалов чередующихся микрослоев можно изменять другие физико-химические свойства микрослойных материалов, например, теплопроводность, температурный коэффициент линейного расширения, твердость, прочность.
Было показано, что уменьшение толщины пленки приводит к значительному увеличению прочности и твердости. Основной причиной такого характера зависимости является то, что при уменьшении толщины пленки, наблюдается уменьшение размеров кристаллов, приводящее к упрочнению конденсата. Увеличение прочности в этом случае можно выразить зависимостью Петча-Холла [6]:
σ = σ0 + 0.5 0 Kd-0,5, (2)
где σ0 и K – постоянные для данного материала; d – диаметр зерна.
Технологические факторы
Технологические факторы, связанные с процессом нанесения покрытия, играют также важную роль в формировании его свойств. Наиболее сильное влияние на свойства получаемого износостойкого покрытия в процессе его нанесения оказывает температура. С точки зрения увеличения дефектности покрытия влияние температуры возможно по следующим механизмам [3]:
· изменение дефектности покрытия за счет атомов остаточных газов;
· изменение дефектности покрытия за счет упрочнения вакансиями;
· изменение дефектности покрытия за счет измельчения субструктуры конденсата и повышения плотности дислокаций.
Из рисунка 2 видно, что снижение температуры конденсации приводит к увеличению дефектности износостойкого покрытия и, следовательно, изменению его физико-механических свойств (повышению твердости, износостойкости материала покрытия).
Давление рабочего газа в камере оказывает влияние на стабильность разряда, производительность распыления и осаждения, а также формирование покрытия. Влияние давления реакционного газа проявляется в первую очередь в формировании состава (химического и фазового) износостойкого покрытия – содержании металлоида в покрытии и, следовательно, формировании его свойств. Увеличение давления азота при конденсации покрытия приводит к увеличению его микротвердости. Это связано с ростом содержания металлоида в покрытии и, как следствие, с увеличением доли ковалентной связи, приводящей к повышению жесткости межатомных связей. Рост содержания металлоида при увеличении давления приводит к увеличению остаточных сжимающих напряжений σ0, что, видимо, связано с изменением физико-механических свойств материала покрытия. Рост остаточных напряжений и изменение свойств материала покрытия приводят к снижению адгезионной прочности покрытия и подложки.
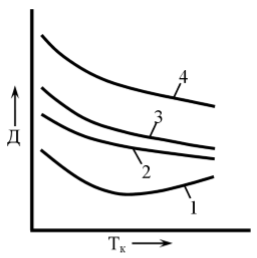
Рисунок. 2. Гипотетические зависимости дефектности покрытия Д от его температуры конденсации Тк [3]: 1 – за счет примесных атомов остаточных газов; 2 – за счет роста числа вакансий; 3 – за счет измельчения микроструктуры и роста плотности дислокаций; 4 – суммарная дефектность
С повышением давления в камере при катодном распылении возрастает стабильность разряда и увеличивается число распыленных атомов (производительность процесса распыления), однако за счет увеличения числа столкновений с атомами газа ограничивается возможность их попадания на основу. При больших давлениях образование химического соединения происходит в газовой среде и осаждение полученного соединения происходит в виде негомогенного и пористого слоя [1].
К технологическим параметрам также относятся и потенциал смещения на подложке, индукция магнитного поля и ток разряда. Эти параметры влияют, в основном, на скорость осаждения покрытия. Увеличение значений этих параметров одновременно приводит к изменению скорости роста за счет увеличения количества металлоида в нитриде и уменьшения скорости роста за счет распыления покрытия. Влияние изменения индукции магнитного поля и тока разряда проявляется слабее.
На физико-механические свойства покрытия оказывает влияние и его микроструктура, формирование которой в свою очередь зависит также от технологических факторов – давления реакционного газа, температуры процесса и скорости осаждения. Увеличение скорости осаждения покрытия приводит к повышению однородности покрытия и уменьшению зерна. В работе [4] в зависимости от температуры процесса предлагается трехзонная модель структуры, показанная на рисунке 3.
При низких температурах подвижность атомов при осаждении на инструментальную подложку ограничена, и структура покрытия является столбчатой, с коническими наростами и слабыми открытыми границами. Такая структура называется также «ботироидальной» и соответствует зоне 1 (рис. 3 а). При увеличении температуры, хотя структура остается столбчатой, происходит более равновесное формирование покрытия, что ведет к его уплотнению и упрочнению межзеренных границ (рис. 3 в). При дальнейшем увеличении температуры процесса структура покрытия приобретает морфологию равноосных зерен (рис. 3 г). Переход между структурами разных зон происходит плавно. Формирование структуры зоны 2 связано с усилением поверхностной диффузии, а зоны 3 – объемной диффузии в покрытии. Такая модель была предложенная Мовчаном и Демчишиным и, впоследствии, была изменена с учетом влияния газовой среды, а затем модифицирована Торнтоном, включившим в нее дополнительную переходную зону (рис.1.7 б), формирующуюся между зонами 1 и 2, и представляющую столбчатую структуру, сходную со структурой зоны 1, но с более мелкими волокнистыми кристаллитами и достаточно плотными границами, обеспечивающими хорошие механические свойства покрытия.

Рисунок 3. Структурные зоны вакуумных конденсатов (по классификации Мовчана – Демчишина) [5]: а – зона 1; б – зона Торнтона; в – зона 2; г – зона 3
Из вышесказанного следует, что в зависимости от функционального назначения покрытия необходимо стремиться к получению оптимальной структуры, обеспечивающей наилучший комплекс механических свойств. На рисунке 4 схематично показано изменение структуры покрытия в зависимости от температуры процесса и давления реакционного газа [4].
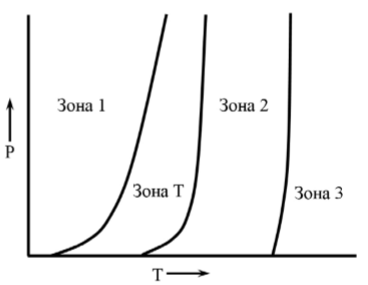
Рисунок 4. Влияние температуры подложки Т и давления реакционного газа Р на структуру конденсата [4]
В процессе конденсации покрытия в нем возникают остаточные напряжения. Возникновение внутренних напряжений в тонких пленках согласно [4], связано с различием коэффициентов термического расширения материалов подложки и покрытия, механизмом кристаллизации (поатомного осаждения, ионной бомбардировке) покрытия, механизмом непрерывного наращивания толщины покрытия, наличием закрепляющего приспособления. При конденсации покрытия методами физического осаждения напряжения в покрытиях имеют не только разные значения, но даже и знаки. Так, согласно [4], в пленках, полученных методами испарения и осаждения, возникают растягивающие напряжения, а в пленках, полученных распылением, они – сжимающие.
Напряжения сжатия являются более выгодными, так как позволяют повысить когезионную прочность и трещиностойкость покрытия. Однако сжимающие напряжения могут приводить к потери устойчивости слоя, в котором они действуют, и кроме того, в зоне краевого эффекта они приводят к возникновению расслаивающих напряжений. На величину внутренних напряжений влияют как химический состав покрытия, его структура, так и технологические параметры. Величина остаточных напряжений зависит и от толщины покрытия [2,4]. В работе [4] среди причин появления напряжений в покрытиях значительная роль отводится появлению оксидных включений. Окисление вызывает увеличение объема, приводит к деформации несоответствия и появлению растягивающих внутренних напряжений.
Не нашли, что искали? Воспользуйтесь поиском по сайту:
©2015 - 2025 stydopedia.ru Все материалы защищены законодательством РФ.
|